Jack Barker
Sr. Production Manager - Flex Filling at Emergent BioSolutions- Claim this Profile
Click to upgrade to our gold package
for the full feature experience.
Topline Score
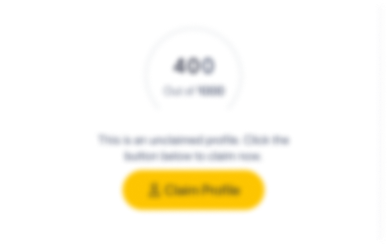
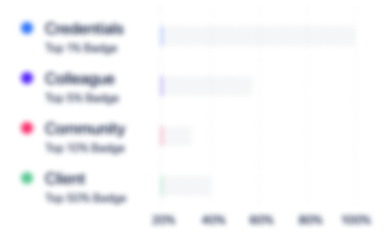
Bio


Experience
-
Emergent BioSolutions
-
United States
-
Biotechnology Research
-
700 & Above Employee
-
Sr. Production Manager - Flex Filling
-
Mar 2022 - Present
-
-
-
Mile High Labs
-
United States
-
Manufacturing
-
1 - 100 Employee
-
Associate Director - Manufacturing
-
Jan 2021 - Mar 2022
-
-
Production Manager - Packaging
-
Dec 2019 - Jan 2021
-
-
-
STAQ Pharma
-
Denver, Colorado
-
Director Of Operations
-
Sep 2018 - Dec 2019
Developed operational processes and launched sterile 503B outsourcing facility from concept design to full production under DEA and FDA federal regulations. - Liaise with C-level executive team to make decisions for operational activities and set strategic goals - Plan and monitor the day-to-day running of business to ensure smooth progress - Supervise staff from different departments and provide constructive feedback - Evaluate regularly the efficiency of business procedures according to organizational objectives and apply improvements - Manage procurement processes and coordinate material and resources allocation - Review financial information and adjust operational budgets to promote profitability - Revise and/or formulate policies and promote their implementation - Manage relationships/agreements with external partners/vendors - Evaluate overall performance by gathering, analyzing and interpreting data and metrics - Ensure that the company runs with legality and conformity to established regulations
-
-
-
Sandoz
-
Switzerland
-
Pharmaceutical Manufacturing
-
700 & Above Employee
-
Production Manager
-
Jun 2015 - Sep 2018
Job Purpose: Directs a multifunctional team responsible for safely producing product in conformance with regulatory requirements (cGMPs, FDA/DEA regulations, etc.), within company policies and goals. Additionally, this position as the SPOC role which is to drive awareness and change management activities necessary for a culture of Data Integrity Excellence. • Manages the overall activities of a functional area within the manufacturing facility. • Responsible for implementing policies/procedures and assuring employees understand/comply with all cGMPs, SOP's, HS&E procedures, FDA, DEA, and OSHA regulations by providing oversight of staff training, task execution, and documentation. • Partners with support organizations to execute critical activities (i.e. CMs/PMs, projects, qualifications/validations, routine monitoring, etc.), resolve issues impacting quality throughput, and to drive improvement in quality/safety/efficiency of facilities/equipment/processes/procedures. • Responsible for assuring maximized utilization of resources (including highlighting opportunities for improvement) and payroll reporting of hourly employees. • Develops functional processes for area managed and executes periodic reviews, CAPAs, change controls, and investigations as assigned. • Drive, monitor and assure delivery of the site DI Plan, within the department • Collaborate with DI lead to drive behavioral change management activities • Continuously improve data integrity knowledge base and understanding within the department: support training related to DI, Deliver DI case studies to the department and share knowledge acquired during the participation of DI walkabouts. • Support preparation for regulatory / health authority inspections and/or response development for DI related topics within the department.
-
-
-
Septodont
-
Pharmaceutical Manufacturing
-
100 - 200 Employee
-
Production Manager
-
Sep 2014 - May 2015
• Manage Production of multiple departments including box making, compounding, filling, and packaging • Plan and schedule all production activities • Manage production targets to meet demand • Manage cost control and identify improvement initiatives • Oversee routings and bill of material reviews • Analyze production metrics (Cost, Productivity, Qualtiy); recommend and implement changes as needed • Lead all production teams • Facilitate SOP and Batch record change management • Lead engineering and capital projects with use of internal and external resources • Oversee production equipment and facilities via the maintenance program • Implement and endorse safety policies and compliance within production • Accountable for development and training of production employees in the areas of GMP training, SOP and job duties training, safety training, and leadership development training • Manage performance of direct reports on a timely basis, including performance appraisal system • Ascertain that supervisors appropriately manage performance of their direct reports and complete appraisal process • Responsible for quality systems management within production including deviation investigations, root cause analysis, CAPA, quality improvements for products and processes, and overall GMP compliance • Lead UDI and serialization initiatives to meet FDA standards • Act as project manager for all major production initiatives
-
-
-
Tolmar
-
United States
-
Pharmaceutical Manufacturing
-
700 & Above Employee
-
Production Supervisor
-
Apr 2011 - Sep 2014
• Supervise shift for safety, quality, and make changes as appropriate. Monitor labor expense. • Conduct Incident Investigations: perform root cause determination and analysis, CAPA determinations and implementations, and effectiveness reviews. • Act as a liaison with Quality Assurance to ensure procedures are followed within regulations. • Assist in the coordination of resources to solve technical issues in production. • Act as Technical Expert for process validation initiatives (IQ, OQ, PQ, PV)• Lead development of training program and maintenance of training database • Prepare and administer employee appraisal and performance documentation. • Create, revise and implement Standard Operating Procedures (SOPs) and Production Batch Records. • Review batch records for accuracy and completeness. • Perform Transactions in the Inventory Control Systems (FourthShift) on a timely basis. • Coordinate production resources (labor, equipment, production areas) to efficiently meet Production Schedule requirements and communicate daily recap and priorities to next-shift supervision. • Oversee the production of various types of pharmaceuticals based in dermatology, urology, and oncology from the issuance of raw materials to bulking, filling, and packaging. Fill processes included tubes, bottles, jars, syringes, and vials for powders, creams, ointments, liquids, and polymers.• Improve department efficiency through implementation of process improvement initiatives and effective use of labor• Act as Training Manager for Manufacturing Department, ensuring all employee’s received required training and reviewing of SOP’s as they are updated
-
-
Lead Packaging Technician
-
Sep 2009 - Apr 2011
•Conduct training: Train new and current employees on cGMP’s, company procedures, and operation of packaging processes. •Assist packaging technicians: Set up and operation of all packaging equipment and processes.•Document Control: Distribute updated documents •Assist supervisors in the daily operations of the manufacturing area.•Writing of technical documents for training, company, and manufacturing SOP’s.•Assist engineers in validation of process equipment•Organize multiple manufacturing processes to ensure the processes are completed in a timely manner with high quality•Review batch records•Utilize Fourth Shift Program to order and move product within the system
-
-
Education
-
Colorado State University
Master of Science (M.S.), Organizational Leadership - Strategic Innovation and Change Management -
Colorado State University
Bachelor of Science (B.S.), Psychology
Community
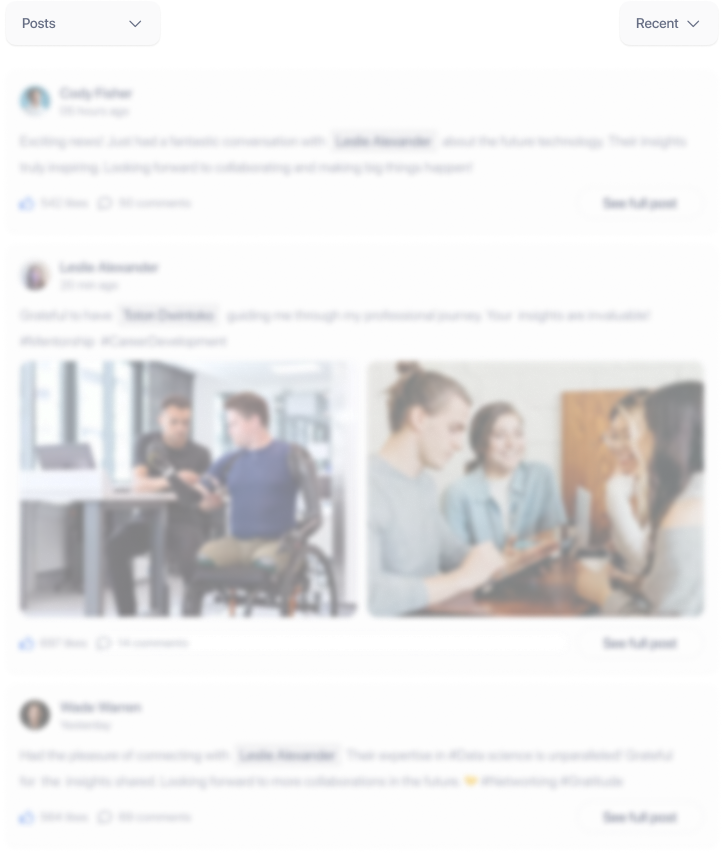