Jack Ader
Packaging Consultant at BoldtSmith Packaging- Claim this Profile
Click to upgrade to our gold package
for the full feature experience.
Topline Score
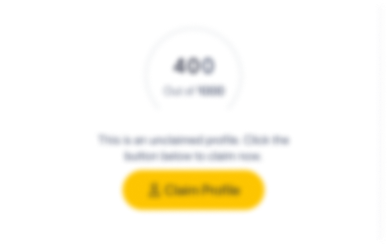
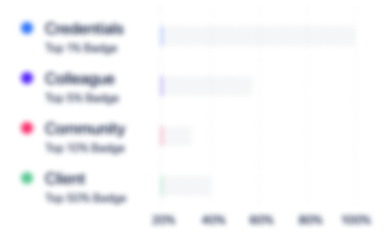
Bio

Jenny Taverna
Jack is a data driven, detail oriented engineer with broad technical knowledge across packaging and manufacturing program management. He has continually demonstrated an eye and passion for continuous improvement and delivered numerous cost savings across numerous projects.

Mike Lang
I would highly recommend Jack Ader for any material handling and packaging engineering opportunities! Based on my experience with Jack he is very detailed and very results driven when it comes to designing and optimizing packaging specifications, improving material flow, assisting with lean manufacturing, improving freight optimization, managing container management and material flow, integrating packaging solutions within manufacturing and warehouse operations, improving product quality during shipments through improved packaging, developing new model program budgets and delivery timing. Jack develops standards and best practices and is able to handle multiple projects, issues, and initiates rapid lower cost solutions. Jack works well in a cross-functional team environment with his department, his customers, and his suppliers. Jack has both the plant operations and corporate material planning & logistics experience and has been successful in all of his organizations. Jack has multiple experiences with automotive OEMs and other companies that he can bring to any organization. Jack's personality, professionalism, and experience is a benefit to anyone's team.

Jenny Taverna
Jack is a data driven, detail oriented engineer with broad technical knowledge across packaging and manufacturing program management. He has continually demonstrated an eye and passion for continuous improvement and delivered numerous cost savings across numerous projects.

Mike Lang
I would highly recommend Jack Ader for any material handling and packaging engineering opportunities! Based on my experience with Jack he is very detailed and very results driven when it comes to designing and optimizing packaging specifications, improving material flow, assisting with lean manufacturing, improving freight optimization, managing container management and material flow, integrating packaging solutions within manufacturing and warehouse operations, improving product quality during shipments through improved packaging, developing new model program budgets and delivery timing. Jack develops standards and best practices and is able to handle multiple projects, issues, and initiates rapid lower cost solutions. Jack works well in a cross-functional team environment with his department, his customers, and his suppliers. Jack has both the plant operations and corporate material planning & logistics experience and has been successful in all of his organizations. Jack has multiple experiences with automotive OEMs and other companies that he can bring to any organization. Jack's personality, professionalism, and experience is a benefit to anyone's team.

Jenny Taverna
Jack is a data driven, detail oriented engineer with broad technical knowledge across packaging and manufacturing program management. He has continually demonstrated an eye and passion for continuous improvement and delivered numerous cost savings across numerous projects.

Mike Lang
I would highly recommend Jack Ader for any material handling and packaging engineering opportunities! Based on my experience with Jack he is very detailed and very results driven when it comes to designing and optimizing packaging specifications, improving material flow, assisting with lean manufacturing, improving freight optimization, managing container management and material flow, integrating packaging solutions within manufacturing and warehouse operations, improving product quality during shipments through improved packaging, developing new model program budgets and delivery timing. Jack develops standards and best practices and is able to handle multiple projects, issues, and initiates rapid lower cost solutions. Jack works well in a cross-functional team environment with his department, his customers, and his suppliers. Jack has both the plant operations and corporate material planning & logistics experience and has been successful in all of his organizations. Jack has multiple experiences with automotive OEMs and other companies that he can bring to any organization. Jack's personality, professionalism, and experience is a benefit to anyone's team.

Jenny Taverna
Jack is a data driven, detail oriented engineer with broad technical knowledge across packaging and manufacturing program management. He has continually demonstrated an eye and passion for continuous improvement and delivered numerous cost savings across numerous projects.

Mike Lang
I would highly recommend Jack Ader for any material handling and packaging engineering opportunities! Based on my experience with Jack he is very detailed and very results driven when it comes to designing and optimizing packaging specifications, improving material flow, assisting with lean manufacturing, improving freight optimization, managing container management and material flow, integrating packaging solutions within manufacturing and warehouse operations, improving product quality during shipments through improved packaging, developing new model program budgets and delivery timing. Jack develops standards and best practices and is able to handle multiple projects, issues, and initiates rapid lower cost solutions. Jack works well in a cross-functional team environment with his department, his customers, and his suppliers. Jack has both the plant operations and corporate material planning & logistics experience and has been successful in all of his organizations. Jack has multiple experiences with automotive OEMs and other companies that he can bring to any organization. Jack's personality, professionalism, and experience is a benefit to anyone's team.

Experience
-
BoldtSmith Packaging
-
United States
-
Packaging and Containers Manufacturing
-
1 - 100 Employee
-
Packaging Consultant
-
Jun 2021 - Present
• Packaging Optimization • Design Engineering • Graphic & Brand Design • E – Commerce Packaging • Custom Transit Testing • Contract Resource • Project Management • Packaging Optimization • Design Engineering • Graphic & Brand Design • E – Commerce Packaging • Custom Transit Testing • Contract Resource • Project Management
-
-
-
-
Packaging Specialist / Consultant
-
2018 - Aug 2021
Performed packaging optimization studies and packaging redesigns for various customers. • Collaborated with DHL Supply Chain and performed packaging optimization study for Honda Motor Company. • Spearheaded Kaizen for Tecumseh Products in redesign indoor and outdoor compressor / condenser unit packaging. • Performed packaging optimization studies of Tesla Model S and X assembly lines. Performed packaging optimization studies and packaging redesigns for various customers. • Collaborated with DHL Supply Chain and performed packaging optimization study for Honda Motor Company. • Spearheaded Kaizen for Tecumseh Products in redesign indoor and outdoor compressor / condenser unit packaging. • Performed packaging optimization studies of Tesla Model S and X assembly lines.
-
-
-
AAM - American Axle & Manufacturing
-
United States
-
Automotive
-
700 & Above Employee
-
Senior Material Handling / Value Stream Engineer
-
2019 - 2021
Developed and implemented packaging and lean material handling for multiple axle, power take-off unit, and rear driveline module programs. Created packaging and material flow plan for every part. Collaborated with industrial engineers in design of flow racks and containers to obtain assembly line part golden zones to improve operator ergonomics and productivity. Customized, sized, and procured container shipping fleets. Collected and approved supplier packaging specifications. Sized and procured flow racks. Quoted and established blanket orders for standard and unique containers, thermoformed trays, plastic pallets, and steel containers. • Identified and implemented $330,000 annual cost savings with conversion from expendable to returnable packaging. • Redesigned service packaging for annual cost savings of $415,000. Show less
-
-
-
Ford Motor Company
-
United States
-
Motor Vehicle Manufacturing
-
700 & Above Employee
-
Material Handling & Packaging Engineer, Project Manager
-
1997 - 2017
Supported MP&L Packaging and Central Engineering Export Operations, Powertrain Operations, internal and externally purchased transmissions, global engine programs, and cross shipping programs. Oversaw packaging and material handling for all export programs from North America. Developed packaging for programs in South America, Africa, Europe, Australia and Asia. Programs including project and supplier management, procurement and financial control, containerization concept engineering, and returnable and expendable packaging engineering.• Developed global best in practice export packaging system consisting of Expendable Steel Racks (ESR) and ISO Modular Containers (IMC). • Implemented $15 million in material and freight cost savings through design, development, and implementation of unique ESR and IMC packaging. • Obtained $14 million in savings with design, development, and implementation of light-weight returnable shipping equipment strategy for engines. • Rolled out Ford Motor Company’s expendable export packaging strategy and processes: ESRs and IMCs worldwide. • Implemented global common process for export packaging to minimize freight and material cost through creative packaging and conveyance cubing. • Developed, tested, and implemented custom export corrugate packaging for transmissions, rear differential units, fuel tanks, engine components, and lithium-ion batteries. • Wrote and annually updated Ford Motor Company’s Supplier Global Export Market Packaging Terms and Conditions (Packaging Guidelines).• Oversaw and provided on-hand engineering support to multiple North American consolidators with over 24 million cubic feet of automotive parts exported annually. • Held leadership position in global export packaging department in terms of design and development of light-weight returnable shipping racks, ESRs, and IMCs.• Prepared bid packages, allocated business, and managed $20 million corrugate and ESR supply base. Show less
-
-
Material Handling & Packaging Engineer - Windsor Engine Plant
-
1993 - 1997
Launched supplier owned returnable container program for all 4.6L, 5.4L, and 6.8L engine components. First Ford manufacturing facility to implement 100% usage of returnable containers for standard and nonstandard parts. Developed packaging for robotic and manual unload parts. Prepared bid packages and procured $2 million in packaging tooling. Worked with process engineers, part suppliers, and hourly personnel to identify packaging requirements. Collaborated with process engineer, automation supplier, and container supplier on container design to meet auto unload, line side, and shipping requirements. Oversaw material handling and assembly sign off of packaging design. Show less
-
-
Material Handling & Packaging Engineer - Romeo Engine Plant
-
1990 - 1993
Developed and implemented supplier owned returnable container pilot program for 70% of 4.6L engine components. Created packaging for robotic and manual unload parts. Prepared bid packages and procured container tooling. Worked closely with process engineers, part suppliers, and hourly personnel to identify packaging requirements. Collaborated with process engineer, automation supplier, and container supplier on container design to meet auto unload, line side, and shipping requirements. Oversaw material handling and assembly sign off of packaging design. Partnered with logistics group and supplier to establish container fleet size. Show less
-
-
-
Ghafari Associates
-
United States
-
Architecture and Planning
-
400 - 500 Employee
-
Manufacturing Engineer
-
1983 - 1990
Held various contract engineering positions in automotive industry. • Ford Alpha – Performed various cost benefit kitting studies for assembly plants. Simulated press production and quick die change for stamping plants • GM BOC – Supervised the conversion of plant layouts and underground utilities prints to digital media. • GM Hydramatic – Over saw the construction of a plant storm water cleaning facility. Ford Transmission and Chassis Division – Developed plant layouts and machine/material handling installation drawings for AXOD transmission program. Show less
-
-
Education
-
Lawrence Technological University
BS, Architecture -
Central Michigan University
MBA, Business
Community
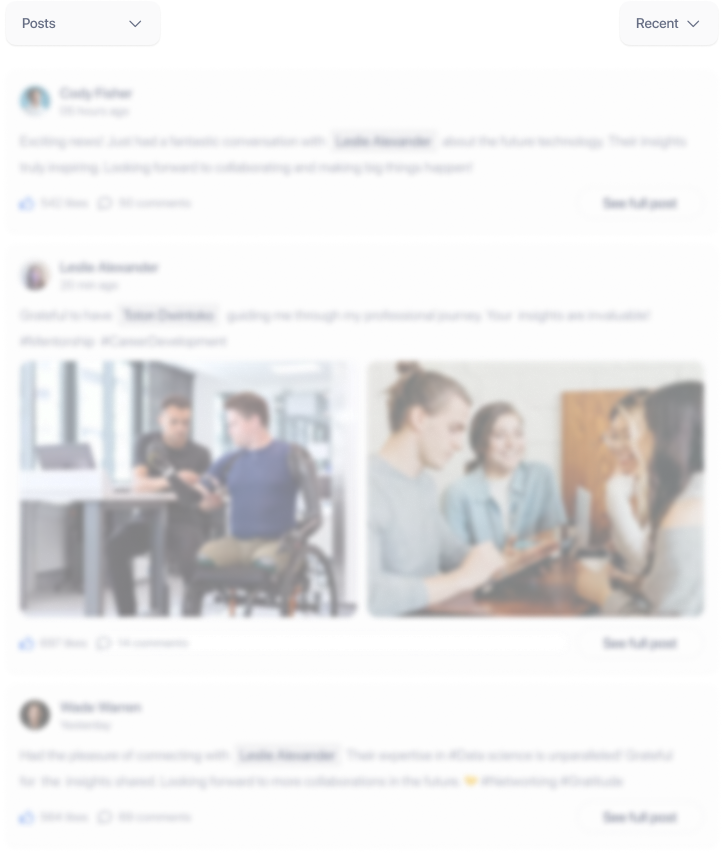