Ivan Sauceda
PC Supply Chain Manager at Reyes Automotive at Reyes Automotive Group- Claim this Profile
Click to upgrade to our gold package
for the full feature experience.
-
Ingles Professional working proficiency
Topline Score
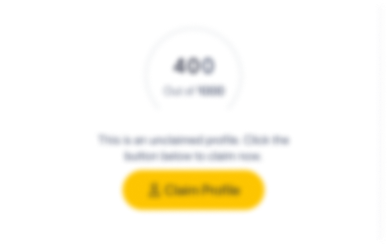
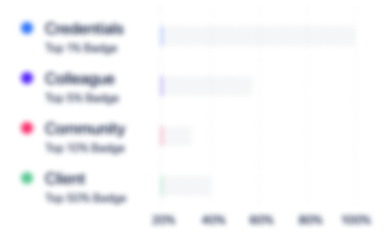
Bio


Experience
-
Reyes Automotive Group
-
United States
-
Automotive
-
1 - 100 Employee
-
PC Supply Chain Manager at Reyes Automotive
-
Aug 2021 - Present
-
-
-
IAC Group
-
United States
-
Motor Vehicle Manufacturing
-
700 & Above Employee
-
Supply Chain Manager level 2
-
Jan 2021 - Sep 2021
-
-
-
Reyes Automotive Group
-
United States
-
Automotive
-
1 - 100 Employee
-
Production Control Assistant Manager
-
Jun 2017 - Jan 2021
* Develop, establish, and provide for the maintenance of reporting systems that related to the Materials function. Compile and maintain inventory, in-process production reports, and status and location of materials.* Monitor inventory levels and inventory control parameters (raw materials, WIP, finished goods) to meet the needs of changing business conditions* Develop Cycle count schedule according ABC analysis.* Do machine and plant capacities, audit of product structure(BOMS), etc.* Serve as materials representative in production launch meetings.* Train other team members in our QAD MRP.* Monitor/promotes environmental, health, safety, and housekeeping within area of responsibility.* Develop material procedures and systems that support the Plant Operations* Have Month End Inventory reports completed and provided to the Production Control Manager no later than 5 working days after month close. Provide a monthly forecast* Identify and analyze any problems in depth, work through logical approaches to determine root cause.* Provide leadership for the Materials Department and participate in attainment of Plant goals.* Responsible for the motivation and development of subordinates to optimize our performance.* Contribute to overall corporate strategies and operations by participation in inter plant and corporate activities.* Help to develop an annual operating budget and manage a system of controls to ensure that service levels and operational performance goals are met within prescribed cost, revenue and profit parameters.* Supervision money back of the alternative cardboard customer package.* Develop plan to do annual physical inventory.* Provide supply chain support to meet business objectives.* New Projects and effective dates coordination, to meet business Goals.* Monitoring Deliveries to Toyota Plan and Service.* Toyota Service supervision, warehouse and deliveries.
-
-
Master Scheduler Production
-
Oct 2015 - Jun 2017
* Develop Pattern Wheel for 23 injection machine* Measurement capacity plan according with the APV* Maintenance of Kanban system, calculation of daily demand.* Monitor and solve of MRP errors working with engineering department* Monitor and investigation of ASN’s late, find route cause of the problem* Daily production included material receiving, picking with scanners, kitting & sequencing, IEK shipping.* Cycle counting ABC, EDI data retrieval, along with Kanban/pull systems system and board process.* Enforced 5S and standardized work utilizing best practices to achieve good score* Administrator of MATTEC system(production injection system)* Develop Plan for annual physical inventory, time lines of activities, preparation of documentation.* Monitoring negative inventory to keep under 1000 dls, and investigation of route cause.* Update Corporative system of capacity plan (CPOD).* Monitoring Gross Requirements and detect any fluctuation* Update corporative system of each machine short term STMP* Coordination of the KANBAN SYSTEM, recount of cards, investigation of missing cards.* Update corporative system of each part (PFEP), review location, warehouse space, supplier lead time, etc.* Ensure proper contact with customers relating to releases and deliveries* Develop, establish, and provide for the maintenance of reporting systems that related to the Materials function.* Compile and maintain inventory, in-process production reports, and status and location of materials.* Monitor inventory levels and inventory control parameters to meet the needs of changing business conditions.* Contribution to overall corporate strategies and operations by participation in interplant and corporate activities
-
-
-
IAC Group
-
United States
-
Motor Vehicle Manufacturing
-
700 & Above Employee
-
Materials Coordinator
-
May 2014 - Sep 2015
* Review and analyze production scheduling requirements to determine products, materials, and actions necessary to ensure the availability of sufficient materials and hardware to meet schedules.* Review all short items in the company and determinate an action plan for recover the good balance.* Identification low raw material inventory after that determine if is necessary to expedite to avoid any plant short material.* Responsible plant Physical inventory preparation.* Review all discrepancies after physical inventory and determinate route cause of any big difference.* Responsible for managing change implementation, raw material bank build or managing product to minimize obsolescence.* Supervision of Incoming and outgoing shipping activities to ensure accuracy, completeness, and conditions of shipments.* Coordination to storage all parts from production or stock in locations according with FIFO system.* Determination proper quantity parts to be shipped according EDI (daily requirements 862).* Generate shipping documents and ship to customer. Ensure the appropriate shipping.* Responsible for verifying supplier, ASN, receipts and performance.* Review and analyze, any demand fluctuation and determinate if we have the ability to support any potential risk in the operation.* Review capacity plant long and short term according with forecast (862 and 830).* Analyze all capacity for storage location using the PFEP (plan for every part).
-
-
Master Scheduler Sr,
-
May 2013 - May 2014
* Develop of production plan of 42 injection plastic machines, 3 assembly lines and one paint Line* Establish min-max for level production* Follow the IAC production system( 7 wastes of manufacturing)* Develop pattern wheel for all production lines* Determinate capacity plant, and establish the NTR (needs to produce) for production* Review customer coverage on the daily meeting with plant manager and operation manager* Establish the good mix of production schedule to minimize the scrap between any set up for a new tool.* Determinate the safety stock and bank build for any contingency or any engineering change.* Schedule the preventive maintenance of each machine or assembly line.
-
-
-
-
Production Manager Jr.
-
Nov 2012 - May 2013
* Management of 23 machines, down time, scrap, and OEE. * Calculate Capacity plan according with customer forecast. * Establish NTR (needs to run) to run efficiency all press. * Determinate Production Budget and management it each month to avoid any extra cost. * Review material consumption and determinate any root cause for any material loss. * Develop multidisciplinary team to fix any customer complain. * Keep under control customer PPM’s. * Management of 23 machines, down time, scrap, and OEE. * Calculate Capacity plan according with customer forecast. * Establish NTR (needs to run) to run efficiency all press. * Determinate Production Budget and management it each month to avoid any extra cost. * Review material consumption and determinate any root cause for any material loss. * Develop multidisciplinary team to fix any customer complain. * Keep under control customer PPM’s.
-
-
-
-
Materials Manager Sr.
-
Sep 2009 - Jan 2012
* Develop and monitoring the MRP for all Raw materials * Establish min-max for the warehouses according with safety stock company policy. * Ensure the good FIFO utilization. * Develop the supplier forecast on weekly time, and review supplier delivery performance. * Monitoring of RAW inventory turns. * Supplier price negotiation, cost reduction and savings costs. * Determinate reorder points of MRO items. * Review all material recovery action plans. * Develop and monitoring the MRP for all Raw materials * Establish min-max for the warehouses according with safety stock company policy. * Ensure the good FIFO utilization. * Develop the supplier forecast on weekly time, and review supplier delivery performance. * Monitoring of RAW inventory turns. * Supplier price negotiation, cost reduction and savings costs. * Determinate reorder points of MRO items. * Review all material recovery action plans.
-
-
-
Aweco de Mexico
-
Plastics Manufacturing
-
1 - 100 Employee
-
Customer Service, Warehouse leader, Materials Planner
-
Aug 2006 - Sep 2009
* Establish the customer demand. * Keep in touch with the customer for any potential change * Develop the production plan, and assembly plan * Determinate any contingency plan. * Determinate min-max racks locations * Develop de shipping customer plan * Maintain the 5’s at warehouse * Determinate goof flow location system * Develop the suppliers forecast. * Follow any potential material short. * Follow the safety stock company policy. * Reduce any potential obsolescence.
-
-
Education
-
Universidad Autónoma de Nuevo León
Ingenieria Control y Automatizacion, Ingeniería en Control
Community
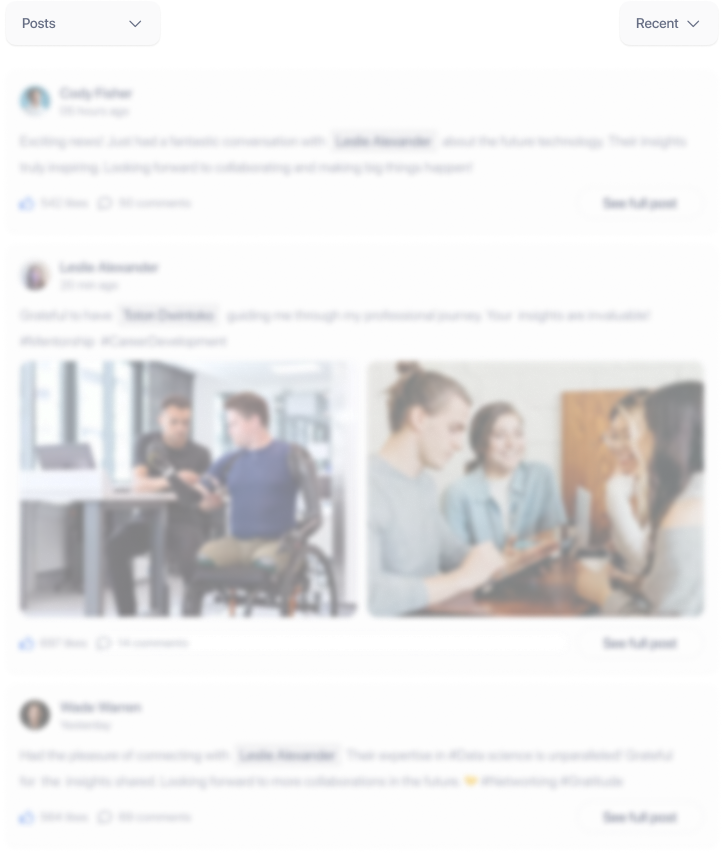