Israel Ortiz, CMM
Materials Supervisor at Neptune-Benson, Evoqua- Claim this Profile
Click to upgrade to our gold package
for the full feature experience.
Topline Score
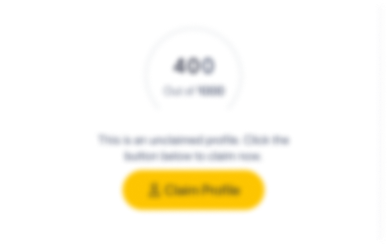
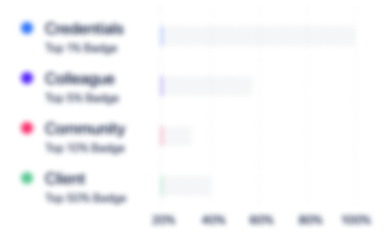
Bio

George Williams
Isreal was a student at two seperate classes in the University of Wisconsin's Engineering Professional Development Maintenance Management Certificate program. While attending a course is not usually reason for recommending someone's skills, there are certain intangibles which make someone valuable to an organization which can be recognized in a group setting. Isreal was a vocal participant in both classes offering his experiences, asking questions, and collaborating with others to complete group activities. The ability to listen, share input, and collaborate are critical skills in today's workplace. Isreal possesses these attributes whick would make him a valuable asset to any team setting.

George Williams
Isreal was a student at two seperate classes in the University of Wisconsin's Engineering Professional Development Maintenance Management Certificate program. While attending a course is not usually reason for recommending someone's skills, there are certain intangibles which make someone valuable to an organization which can be recognized in a group setting. Isreal was a vocal participant in both classes offering his experiences, asking questions, and collaborating with others to complete group activities. The ability to listen, share input, and collaborate are critical skills in today's workplace. Isreal possesses these attributes whick would make him a valuable asset to any team setting.

George Williams
Isreal was a student at two seperate classes in the University of Wisconsin's Engineering Professional Development Maintenance Management Certificate program. While attending a course is not usually reason for recommending someone's skills, there are certain intangibles which make someone valuable to an organization which can be recognized in a group setting. Isreal was a vocal participant in both classes offering his experiences, asking questions, and collaborating with others to complete group activities. The ability to listen, share input, and collaborate are critical skills in today's workplace. Isreal possesses these attributes whick would make him a valuable asset to any team setting.

George Williams
Isreal was a student at two seperate classes in the University of Wisconsin's Engineering Professional Development Maintenance Management Certificate program. While attending a course is not usually reason for recommending someone's skills, there are certain intangibles which make someone valuable to an organization which can be recognized in a group setting. Isreal was a vocal participant in both classes offering his experiences, asking questions, and collaborating with others to complete group activities. The ability to listen, share input, and collaborate are critical skills in today's workplace. Isreal possesses these attributes whick would make him a valuable asset to any team setting.
0
/5.0 / Based on 0 ratingsFilter reviews by:
Credentials
-
Maintenance Management
University of Wisconsin-Madison
Experience
-
Neptune-Benson, Evoqua
-
United States
-
Mechanical Or Industrial Engineering
-
1 - 100 Employee
-
Materials Supervisor
-
Jul 2018 - Present
Started as a contractor in Purchasing and was hired Full-time to lead the Logistics and Supply dept., LEAN and Safety for the factory. Led many Kaizen events including, but not limited to: Reduced Purchasing Backlog from >800 to 0 in first 90 days. Reduced Overdue POs from > 500 items to less than 100. Implemented Meeting best practices to facilitate good communication between divisions. Moved to Materials Supervisor to manage all materials. Implemented 5S & Kanban on the floor and storerooms to reduce item search times from ave. 20 min to less than 1 min. Reduced Stock outs from 2 items /day to less than 2 items per week. Implemented a strong Safety culture with daily toolbox talks, management walks and recording /analyzing near losses & observations with team discussions on improvements. Lead team to Lean Bronze certification. Daily visual management boards, 5S, Standard Work, cost savings, etc... Reduced shipping errors Recorded Standard Work documents for all key operations. Helped the plant transition to Holland, Michigan. Show less
-
-
-
-
Operations and Management Consultant
-
Jul 2017 - Jul 2018
World Class Operations Management consultant specializing in Change Management, Loss Reduction, Organizational & Process Improvement, Management & Leadership development, and overall cost reduction clients included, Aerospace, Auto manufacturing, Food and Beverage, Wine and cheese making, and other manufacturing. World Class Operations Management consultant specializing in Change Management, Loss Reduction, Organizational & Process Improvement, Management & Leadership development, and overall cost reduction clients included, Aerospace, Auto manufacturing, Food and Beverage, Wine and cheese making, and other manufacturing.
-
-
-
HD Supply
-
United States
-
Wholesale
-
700 & Above Employee
-
Project Specialist
-
Jun 2016 - Jun 2017
Coordinated staged multi-residential renovation project installations managing the entire supply chain from vendor sourcing to product delivery including problem resolution. Heavy SAP, Salesforce and Outlook use Worked with the vendors for special orders for high volume multiple unit renovations. Assisted with product selection, generates quotes. Created quote presentations for the sales representatives. Maintained consistent and accurate project status updates. Show less
-
-
-
-
Production Planner
-
Feb 2013 - Mar 2016
• Provided forecast & demand planning support to various production lines & projects including, but not limited to: planning, progress monitoring & disruption analysis, labor & materials analysis, communicating, and expediting.• Created a communication meeting with operating and support groups (Production, Maintenance, Purchasing, Finance, Warehouse, QA) for preparation and analysis of daily & weekly reports.• Monitored, alerted & advised management to potential supply & delivery issues with suggested solution options.• Extensive use of planning software (SAP, MS Office, MS Project) to review trends, forecast demand, create /track Stock Requirements Lists, Purchase Requisitions, Purchase Orders, and other production transactions.• Interpreted BOM data to create Material Masters in SAP.• Can convert a rough-cut capacity master production schedule into a detailed production plan, after analysis of lot size rules, sales trends, demand forecast, material availability and manufacturing capacity.• Can create/release production orders and partner closely with Manufacturing, Quality and Logistics in the prioritization and expediting of the orders.• Plans and leads Project Accountability Meetings and all Lean Initiatives.• Coaching, training and employee development. Developed Plant Leadership training module. Show less
-
-
Maintenance Planner /Purchaser /Lean Coordinator
-
Feb 2009 - Feb 2013
• Planned and scheduled all maintenance activities in determining all Work Order, PM, Emergency and New Projects to keep industrial goals optimized and maximize line uptime.• Used SAP and MS Office to forecast, plan and schedule all projects and maintenance activities to maximize labor and materials effectiveness.• Overhauled the Maintenance purchasing system to bring budget under control and within budget plans within 3 months of my arrival.• Started Company-wide Safety Work Order Tracking.• Supported Maintenance teams change of culture from Reactive to Reliability focused.• Analyzed, drafted & reported diagnosis of equipment and drew up indicators and management charts.• Helping to implement changes on the production line (productivity, quality safety and security) in connection with New Projects and Production• Supporting Maintenance teams change of culture from Reactive to Reliability focused.• Analyzing and drafting a diagnosis of equipment and drawing up indicators and management charts• Helping to implement changes on the production line (productivity, quality safety and security) in connection with New Projects and Production• Organizing and planning preventive and improving maintenance in keeping with TPM (total productive maintenance) philosophies• Processing and reducing reactive maintenance by implementing Equipment database and Work History Tracking, Solutions tracking, OEE measuring, Preventive Maintenance tools and procedures, • Equipment manual collection/ organization, Spare Parts Tracking, Inventory Control, • Started Company-wide Safety Work Order Tracking• Contributing and monitoring the Maintenance budget• Creating & Managing the MRO stock (parts) on several units• Managed the maintenance of EH&S records (accidents, waste manifests, etc.) and prepares appropriate reports.• Vendor Management, price analysis and negotiation. Show less
-
-
Lean Coordinator
-
Feb 2003 - Feb 2013
• Oversaw the implementation and training of all plant personnel in the Lean /WCM Continuous Improvement business model including Management as taught by Solving Efeso Consulting at Kolb-Lena Inc. Duties included but not limited to – • Creating checklists and training aides, • Process improvements, • Leading team meetings /trainings, • Leadership development • Leading & implementing TPM Pillars, • Operator training systems development, • Value Stream Mapping, • Waste reduction• Line Efficiency,• Progress reports to executive management • (See Skills for more complete list). • Successfully led 5S effort with culture change focus.• Change resistance management specialist.• Various Line optimization projects resulting in direct labor reductions and increased production output with no capital expense.• Created plant wide Training Matrix and Training plan /policy to support operations.• Started Autonomous Maintenance culture change with focus on Operator Ownership and accountability to reduce Maintenance costs and increase equipment uptime.• Gathered all data and led plant wide equipment OEE calculations and software implementation. • Was principal owner of Plant OEE software and data.• Have been involved with this position continuously until present.Back-up Line Lead included helping staff achieve and exceed operational targets. Training & motivating staff, conflict resolution, KPI implementing and monitoring. Show less
-
-
Production Lead
-
Feb 2001 - Feb 2003
• Scheduled and lead cheese production team in exceeding company targets. • Built effective, cross-trained teams.• Reduced Team conflicts 90%.• Identified best practices and standardized training.• Created on-boarding process to identify optimal temp skills.• Quality testing, operator training, direction of activities, • Developed a more ergonomically process resulting in faster cycle times and less injuries.• Troubleshooting, Root Cause Analysis, safety team member• Lead the 3rd shift packaging team in consistently EXCEEDING company goals and targets, eventually eliminating the need for a 3rd shift.• Implementing Process controls, development of training of operators, and designing /implementing process improvements. • Doubled production output from 200 cs/shift to 450 cs/shift with no capital investment using TPM methods. Show less
-
-
Education
-
University of Wisconsin-Madison - School of Engineering
Certificate, Maintenance Management -
Highland Community College
AA Organizational Management, Business Administration, Management and Operations -
Mission Bay High School
Community
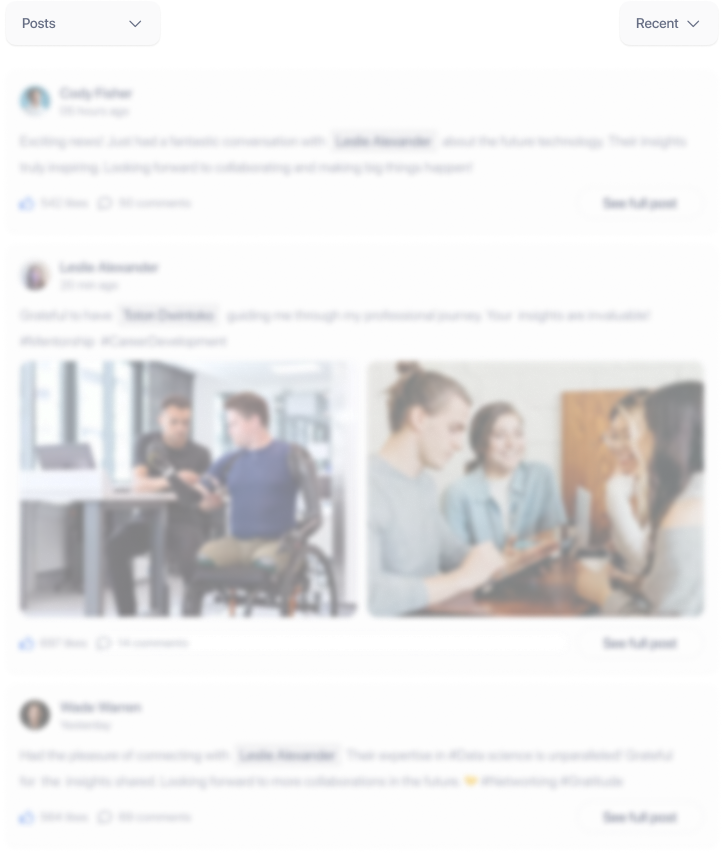