Irshad Malik
Quality Assurance Manager at Sapphire Fibres Limited- Claim this Profile
Click to upgrade to our gold package
for the full feature experience.
Topline Score
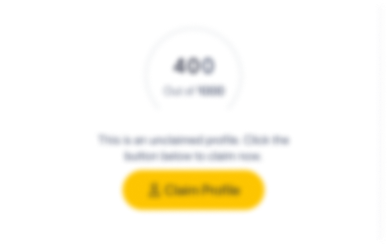
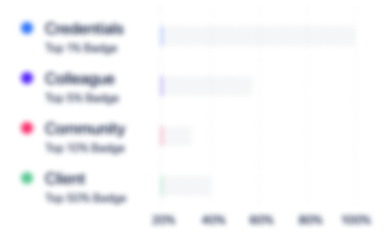
Bio


Experience
-
Sapphire Fibres Limited
-
Pakistan
-
Textile Manufacturing
-
400 - 500 Employee
-
Quality Assurance Manager
-
Feb 2020 - Present
-
-
-
Style Textile
-
Pakistan
-
Textile Manufacturing
-
700 & Above Employee
-
-
Dec 2014 - Present
-
-
-
Dec 2014 - Present
-
-
-
ARP TRADING HOUSE
-
Bangladesh Dhaka
-
MANAGER QUALITY ASSURANCE AND DEVELOPMENT.
-
2007 - 2014
Responsible for overall quality control system, procedures and direction to ensure that customer quality standard are meet. Inspect fabric quality, accessories, parts, components and product for color, measurements, labels and overall quality. Share with the merchandiser and QC and workshop leader, technician and supervisor for PP meeting to decide technical procedure, inspection standards, key processing points and others details before start the production of the order. Provide advice on feasibility of customers, proposed requirements and suitability for mass production . Ensure that quality of pattern construction , pattern size grading and fitting are meeting the customer requirements and provide the technical advice as need. Conduct in line and final production inspection and provide solutions to solve quality issue. Monitor the production process ,ensure all product specifications are accurate , to avoid any quality problems occurs, and meet the customer requirements . Lead , motivate and manage a team of quality controllers ,following up on the QC team. Provide supervisor advice to the factories before and during the manufacturing process. Final production inspection: Garments inspection report, size measurement chart, digital image, laboratory testing and loading supervision. Developing and maintain stringent and transparent quality management procedures. Monitoring quality performance for the factories by gathering relevant , analysis the data and producing reports to top management. To give all type of PSO approval from sampling to production after wash test according to buyers standard after 5 time washing. To give the all type fabric approval for production and inspect during in line like knitting, dyeing , printing and bulk cutting, stitching and also final audit . Keep impeccable record/ ensure style folders are up to date and accurate. Look after ECO test, AZO and all chemical test with SGS and BUREAU VERITAS. Show less
-
-
-
BISMILLAH TEXTILE (PVT) LTD Mills
-
Pakistan Faisalabad
-
Quality Control, Assurance Manager and R&D:
-
2003 - 2007
Responsible for monitoring and maintain quality and compliance targets. Monitoring and auditing of products and ensure high standards of quality. Ensuring product comply with legislation and quality assurance codes. Ensuring that all QA test are carried out on time and in full. Delivering presentations to an audience of manager level within the business. Provide weekly and monthly reports to senior managers on performance. Identify training needs and recommendation to improve customer experience. Keeping quality documents up to date. Making sure that all QA record ,data and information are available to managers . Ensuring non confirming products are identified and placed on restriction place. Responsible for the review and update of the programmed quality plans. Awareness of regulatory requirement and customer service expectations. Ensuring activates in the quality plan are carried out. Coordinating the investigation of customer complaints. Preparing and analyzing information for the purpose of management review. Giving specialist quality assurance advice to the company departments as required. Responsible to maintain the quality of: New development and strike offs. Pre production, production and sales promotion Fabric received from folding department Accessories being used in made ups In line process control Final assessments Ratio control Assortments handling (Solid systems) Show less
-
-
-
Kamal Fabric
-
Pakistan Faisalabad
-
Quality control and & Assurance Manager
-
2000 - 2003
Manage the QC department and arrange the QC schedule, tasks and check list from production till shipment. Ensure they full understand the quality control and inspection procedure. Coordinate all business activates required to meet quality standards. Provide quality advice to all quality inspectors before and during the manufacturing process. Work closely with merchandising team in handling and evaluate the sample /test orders, ensure the sample orders can delivered on schedule with good quality. Provide full quality control reporting to merchandising department. Ensure the fabric quality like color matching, design,, GSM, density, tear strength , bowing, skewing, hand feel, pilling, shrinkage and other fabric section as per customer requirements ,also ensure if the fabric has any woven, dyeing, printing or finishing defects, by using 4 point inspection system, make inspection reports. Good command of the international inspection standard. Developing and maintaining stringent and transparent quality management procedures. Show less
-
-
-
Zas Corporation (Buying House)
-
Pakistan Faisalabad
-
Senior Auditor for quality and R&D
-
1994 - 2000
Developments from grey to processing and garments(knitting). Monitoring and handling the quality activities Co-ordination with the marketing department (VENDOR) to execute the shipment Well in time Control over inputs (Fabric, Accessories and relevant information) Control over processes Final Assessments Handling made ups from grey fabric through processing till made ups according to the specifications from the customer. Making in line inspection during all the processes of development of the required products in accordance with the specifications of the customer. Making final audit report after the completion of the order to declare the acceptance or other wise holding of the shipment keeping in view the article as well as customer tolerance level. Regarding new developments and strike offs helping the designing department. To handle the Pre qualification assessments from customer. Show less
-
-
Education
-
govt high school
Community
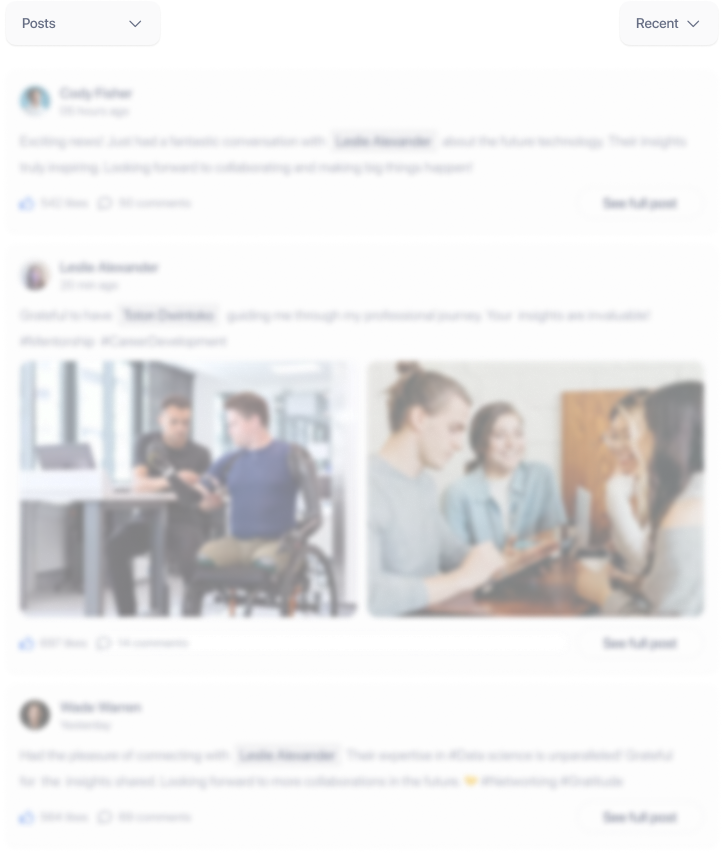