Irma Nguyen
Financial Analyst at Torax Medical, Inc.- Claim this Profile
Click to upgrade to our gold package
for the full feature experience.
-
English Native or bilingual proficiency
-
Spanish Native or bilingual proficiency
Topline Score
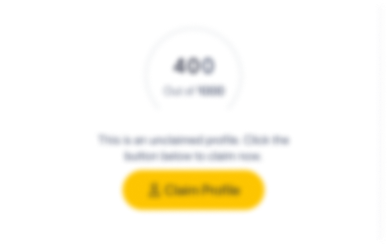
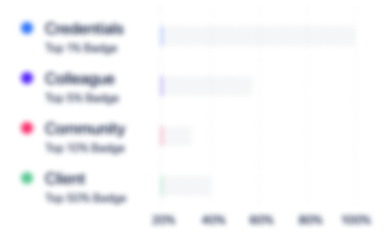
Bio

Don Potter
Irma has solid experience in a variety of Operations and Materials positions with a background in Finance. This provides her the ability to use data to add value to any organization she supports. Irma and I worked together for many years at Pentair including her time in Reynosa, MX prior to moving to Minnesota. She is professional, solid business and people skills and operates with high integrity in driving performance.

Don Potter
Irma has solid experience in a variety of Operations and Materials positions with a background in Finance. This provides her the ability to use data to add value to any organization she supports. Irma and I worked together for many years at Pentair including her time in Reynosa, MX prior to moving to Minnesota. She is professional, solid business and people skills and operates with high integrity in driving performance.

Don Potter
Irma has solid experience in a variety of Operations and Materials positions with a background in Finance. This provides her the ability to use data to add value to any organization she supports. Irma and I worked together for many years at Pentair including her time in Reynosa, MX prior to moving to Minnesota. She is professional, solid business and people skills and operates with high integrity in driving performance.

Don Potter
Irma has solid experience in a variety of Operations and Materials positions with a background in Finance. This provides her the ability to use data to add value to any organization she supports. Irma and I worked together for many years at Pentair including her time in Reynosa, MX prior to moving to Minnesota. She is professional, solid business and people skills and operates with high integrity in driving performance.

Credentials
-
Project Manager
University of MinnesotaJan, 2013- Nov, 2024
Experience
-
Torax Medical, Inc.
-
United States
-
Medical Equipment Manufacturing
-
1 - 100 Employee
-
Financial Analyst
-
Feb 2020 - Present
-
-
-
TE Connectivity
-
Switzerland
-
Appliances, Electrical, and Electronics Manufacturing
-
700 & Above Employee
-
Material Control Manager
-
Dec 2018 - Jul 2019
-
-
-
Life Fitness
-
United States
-
Wellness and Fitness Services
-
700 & Above Employee
-
Material Control Manager
-
Jun 2017 - Dec 2018
-
-
-
SunOpta
-
United States
-
Food and Beverage Manufacturing
-
700 & Above Employee
-
Supply Planning Manager
-
Dec 2015 - Jun 2017
-
-
-
Apex International Mfg, Inc.
-
United States
-
Manufacturing
-
1 - 100 Employee
-
Supply Planning Manager
-
Jul 2014 - Jul 2015
Responsible for Sales and Operating Plan , Manage scheduling department, Ownership of supply chain department process and procedures continuous improvement. Responsible for Sales and Operating Plan , Manage scheduling department, Ownership of supply chain department process and procedures continuous improvement.
-
-
-
Pentair
-
United Kingdom
-
Industrial Machinery Manufacturing
-
700 & Above Employee
-
Lean Manager
-
Jul 2013 - Mar 2014
Provide expert assistance to the division in leading and implementing strategy deployment to significantly align the organization’s key functions and activities with strategic objectives.
-
-
Operations Project Management
-
Mar 2011 - Jul 2013
Proficiently assisted the site director in applying strategy deployment initiatives; oversaw projects for various site functions/areas working hard to meet and exceed goals. Notable Accomplishments: Took an instrumental role in directing and implementing the following key projects: A project improving the performance, such as service delivery and productivity, of the lowest performing business unit by strengthening the team through team building activities, clear goals, and clear communication Project substantially reducing inventory globally to meet and surpass financial goals, successfully surpassing the initial target of $19M reduction with sustainable decrease of $22M from the global operations Attained cost goals goal for the year as reflected in expertly training all team members in basic cost accounting, as well as creating and streamlining the process which monitored visual tools and cost information with periodic communication. Spearheaded and significantly enhanced the management state of business reports; consequently, optimizing productivity companywide.
-
-
Inventory Control Manager
-
Jul 2009 - Mar 2011
Directed the Material Supermarket for the entire management operations in two manufacturing facilities, including four business units, consolidated into one main facility. Notable Accomplishments: Successfully reinforced and improved the company’s Kanban systems for the delivery of key materials to various manufacturing operations. Executed and supervised visual systems for supermarket inventory controls as well as point-of-use inventory delivery; strategically supported productivity improvements in the manufacturing area.
-
-
Divisional Materials Process & Systems Manager
-
Dec 2008 - Jul 2009
Leveraged outstanding leadership aptitudes in rendering strategic support to the Central Planning Team during management transition. Notable Accomplishment: Efficiently streamlined cycle counting process of inventory for various operations sites; and monitored adherence to the key process and suitability of data quality for all operations.
-
-
Supply Chain Manager
-
Oct 2006 - Dec 2008
Administered a team of results-driven commodity managers in achieving all cost and service goals through development and implementation of annual strategies; and worked collaboratively with strategic suppliers in lean manufacturing and outsourcing initiatives to low-cost regions.
-
-
Materials manager
-
Mar 2002 - Oct 2006
Supervised various teams with supervisors administering areas which included import and export, production planning, purchasing, materials warehousing, shipping, and cross-dock warehouse in Texas. Notable Accomplishments: Built and grew a highly competent Material Management Team through effective hiring, training, team building, and communication which enabled the plant to serve as model for material management throughout the division. Accelerated key growth as reflected in the following implemented initiatives: An improved supermarket for raw materials, which included non-production materials Pull system for planning production lines with visual system in the production floor, enabling better flow of production Proactive participation in sourcing contracts; and implementation of vendor managed inventory (VMI) for numerous high volume of raw materials which improved inventory availability Quickly improved inventory controls through identification of invalid virtual warehouses and execution of the process to control physical inventory. Enhanced transportation time to the U.S. distribution center by identifying better logistics companies, faster and better service brokers, as well as clear certifications from Mexico and USA customs offices.
-
-
-
Emerson
-
United States
-
Industrial Machinery Manufacturing
-
700 & Above Employee
-
Finance Manager/Controller
-
1994 - 2002
-
-
Education
-
Universidad Valle del Bravo
Bachelor's degree, Accountant
Community
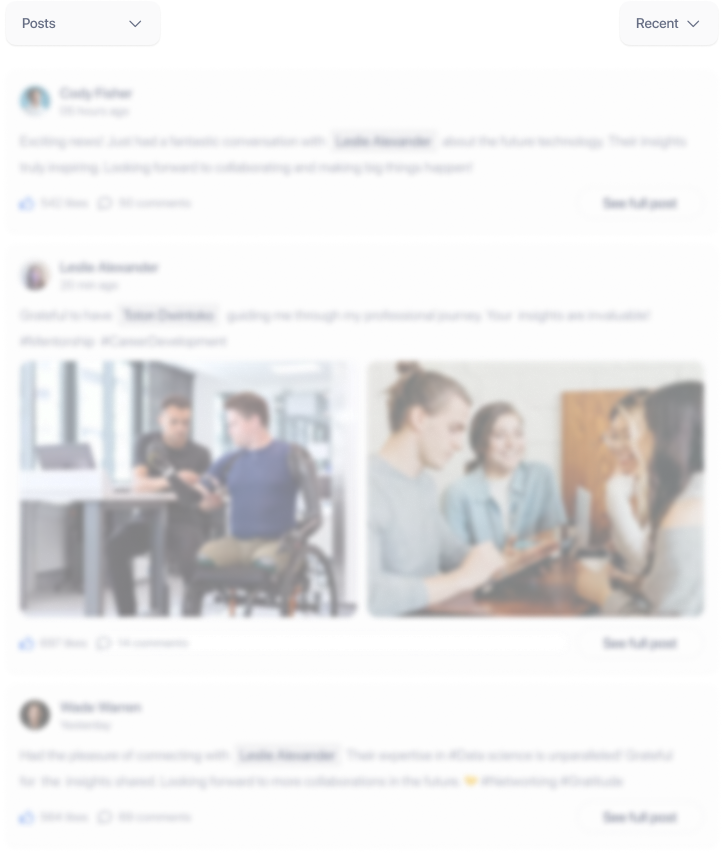