Ian Crawforth
Buyer at FFEI- Claim this Profile
Click to upgrade to our gold package
for the full feature experience.
Topline Score
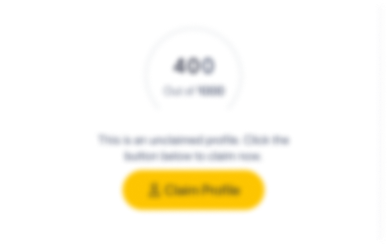
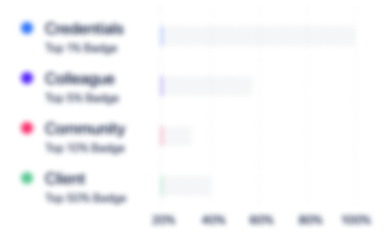
Bio


Experience
-
FFEI
-
United Kingdom
-
Mechanical Or Industrial Engineering
-
1 - 100 Employee
-
Buyer
-
Jan 2009 - Present
• Manage key commodities of sheet metal fabrication, electrical motors and actuators, optical spinners. • Commodity spend approx. £2.35m • Manage change process for key Life Science project • Develop close working relationship with Design & Engineering improving cross-functional team work. • Due to closure of a major sheet metal supplier, managed transfer of business to alternate suppliers, including design review, prototype manufacture, series production during manufacturing operations. • Managed reduction in large assembly stock holding from £76K to £40K through liaising with Production Planners and JIT control of supplier deliveries. • Improved delivery and quality performance of Hong Kong-based metal work supplier, saving on air freight costs - from approx. £4,000 per month to less than £1,000. • Continued development of existing UK sheet metal suppliers to improve cost, quality and delivery performance, resulting in improved material availability and reduced cost. • Developed costing model with key sheet metal supplier to enable optimum quantity/price decisions • Completion of supply agreement with motor supplier, negotiating stock holdings in UK, improving on time delivery performance (now approx. 98% OTD) and eliminating the need and cost for air freight of components from Japan (around £400 per shipment).
-
-
-
Altro Limited
-
United Kingdom
-
Building Materials
-
200 - 300 Employee
-
Group Procurement Officer
-
1990 - 2008
-
-
-
Britannia Airways
-
Luton, Bedfordshire, UK
-
Rotables Controller
-
1986 - 1990
Reported to Supplies Manager, Rotables Section – Responsible for 3 staff • Availability of spares both for planned heavy maintenance and flight line needs. • “Out of hours” cover for line engineering function. • Managed full inventory location analysis. • Analysed usage and agreed increased holding of key items with engineering management Reported to Supplies Manager, Rotables Section – Responsible for 3 staff • Availability of spares both for planned heavy maintenance and flight line needs. • “Out of hours” cover for line engineering function. • Managed full inventory location analysis. • Analysed usage and agreed increased holding of key items with engineering management
-
-
Education
-
Leicester Polytechnic
BEC Higher National Diploma, Business Studies -
Lougborough Grammar School
3 A levels, 8 O levels
Community
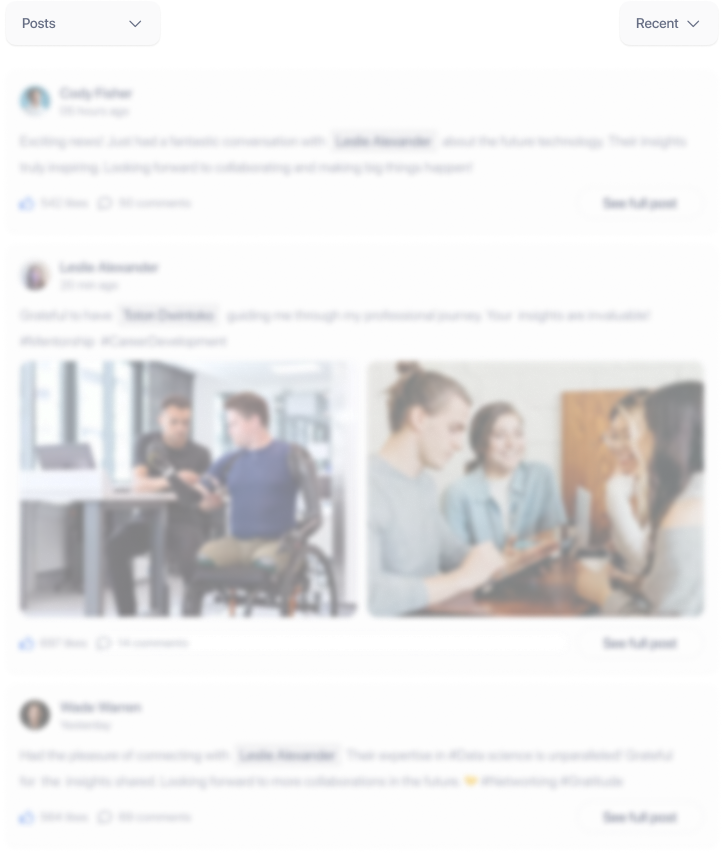