Ian A. Smith
Assistant Director of Finance at Louisiana Pain Care- Claim this Profile
Click to upgrade to our gold package
for the full feature experience.
-
English -
Topline Score
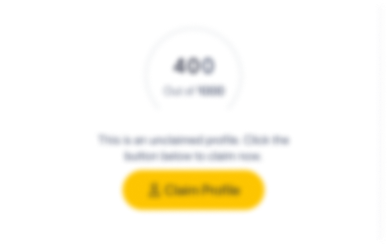
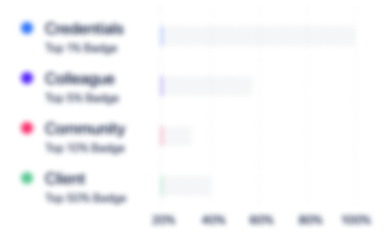
Bio

Aimee Hart FLMI, HIA
Ian is always a pleasure to work with! He's always there for anyone. Ian is highly skilled in Accounting & Management! Very detailed oriented and stays on top of all projects. Ian has been crucial to the success of our company & would be to any company!

John Risher
I am proud to recommend to you Ian Smith as a loyal professional with integrity, dependability, and a desire to excel in all he does. I have known Ian from when he attended West Monroe High School and was a leader is Air Force Junior ROTC. He has proven himself to have determination and drive necessary to meet all challenges as he graduated from College and entered the work force. He would be considered an asset in any situation. He makes things happen to improve the bottom line. John Risher, Former AFJROTC Instructor WMHS CMSgt, USAF Retired

Aimee Hart FLMI, HIA
Ian is always a pleasure to work with! He's always there for anyone. Ian is highly skilled in Accounting & Management! Very detailed oriented and stays on top of all projects. Ian has been crucial to the success of our company & would be to any company!

John Risher
I am proud to recommend to you Ian Smith as a loyal professional with integrity, dependability, and a desire to excel in all he does. I have known Ian from when he attended West Monroe High School and was a leader is Air Force Junior ROTC. He has proven himself to have determination and drive necessary to meet all challenges as he graduated from College and entered the work force. He would be considered an asset in any situation. He makes things happen to improve the bottom line. John Risher, Former AFJROTC Instructor WMHS CMSgt, USAF Retired

Aimee Hart FLMI, HIA
Ian is always a pleasure to work with! He's always there for anyone. Ian is highly skilled in Accounting & Management! Very detailed oriented and stays on top of all projects. Ian has been crucial to the success of our company & would be to any company!

John Risher
I am proud to recommend to you Ian Smith as a loyal professional with integrity, dependability, and a desire to excel in all he does. I have known Ian from when he attended West Monroe High School and was a leader is Air Force Junior ROTC. He has proven himself to have determination and drive necessary to meet all challenges as he graduated from College and entered the work force. He would be considered an asset in any situation. He makes things happen to improve the bottom line. John Risher, Former AFJROTC Instructor WMHS CMSgt, USAF Retired

Aimee Hart FLMI, HIA
Ian is always a pleasure to work with! He's always there for anyone. Ian is highly skilled in Accounting & Management! Very detailed oriented and stays on top of all projects. Ian has been crucial to the success of our company & would be to any company!

John Risher
I am proud to recommend to you Ian Smith as a loyal professional with integrity, dependability, and a desire to excel in all he does. I have known Ian from when he attended West Monroe High School and was a leader is Air Force Junior ROTC. He has proven himself to have determination and drive necessary to meet all challenges as he graduated from College and entered the work force. He would be considered an asset in any situation. He makes things happen to improve the bottom line. John Risher, Former AFJROTC Instructor WMHS CMSgt, USAF Retired

Credentials
-
Diploma in Strategic Management
Alison - Free Online LearningMar, 2018- Oct, 2024 -
OSHA 10 Certification
Training Logic, Inc.Jan, 2016- Oct, 2024 -
TWIC
Transportation Security Administration (TSA)Jun, 2020- Oct, 2024
Experience
-
Louisiana Pain Care
-
United States
-
Medical Practices
-
1 - 100 Employee
-
Assistant Director of Finance
-
Jul 2018 - Present
• Responsible for managing contractors maintaining a network of 70+ computers with Windows 10 operating systems. • Managing contractors maintaining the working status of all network printers and faxes. • Ensure proper function of the phone, security, and WiFi systems throughout the facility. • Calculate cost and place orders for equipment as necessary to replace damaged and aging systems, as well as, additional purchasing as deemed necessary through budgetary policy. • Oversee Design and implementation of Acceptable Usage Policy, and other cyber security precautionary measures. • Ensure internal cyber security measures for HIPAA compliance from a managerial standpoint. • Coordinate with third-party network host, managers, and providers to address issues and assist with special projects. • Possess a working knowledge of internal EHR system and respond to lower level issues that may arise when contractors are unavailable. • Coordinate with maintenance contractor, serve as a point of contact for inspections and projects conducted by contractors to ensure completion on time and within budget. • Responsible for all incoming vendor invoices for accounts payable. • Reconciliation of accounts for four separate entities. • Month-end close, profit & loss data, and monthly forecasting. • Executive assistant to CEO and Owners Show less
-
-
-
Smith Consulting
-
United States
-
Business Consulting and Services
-
Freelance Contractor
-
Sep 2017 - Jul 2018
Providing reasonably priced industrial consulting for a variety of needs such as lean-purchasing, supply chain management, 5S, interdepartmental communication, lead-time reduction, continuous improvement, quality control, production analysis, FMEA/RCCA actions, downtime tracking and reduction, waste reduction, and organizational excellence and development. Additionally provided solutions for tutoring college students in various subjects (English, Writing, History), and provided assistance building resumes for students who were going into the workforce post-graduation as well as others who needed updated resumes (including Nurse Practitioners, RNs, LPNs, other medical professionals and business professionals). Show less
-
-
-
-
Production Supervisor - Finishing
-
Jan 2016 - Sep 2017
• Responsible for leading a production team of 25-30 employees on multiple assets including 3-4 right angle basket gluing machines and 9 straight-line gluing machines.• Maintaining the status quo of employees assigned to various roles, organizing and delegating overtime assignments of employees, as well as ensuring the integrity of the department's throughput.• Ensure that throughput meets or exceeds run standards in order to decrease customers' lead time for their product.• Work closely with operators and quality technicians in order to make sure that our quality standards as well as the customers' are met and surpassed. • Ensure that operators are aware of updated policies and procedures relating to product quality, safety, and communication from management, as well as addressing any inconsistencies and problems with managers and other supervisors.• Provide additional support to our management team. Show less
-
-
Continuous Improvement Technician
-
Sep 2014 - Jan 2016
• Responsible for supervising operators' quality checks as well as performing quality self-checks of throughput to ensure the only the highest quality product leaves the facility. • Maintaining the integrity of product through strength testing, surface testing and bending to ensure product meets not only GPI West Monroe's quality standards, but exceeds the standards of our customers. • Work closely with operators and supervisors in order to make sure that quality standards are met and surpassed. This close relationship as a liason between operators and managers ensures that information is communicated.• Prevent substandard material from leaving the facility through batch blocking, product sorting and material tracking.• Ensure that operators are aware of updated policies and procedures relating to product quality and address any inconsistencies and problems with supervisors.• Provide additional support to our technical service engineers assigned to various customers around the country.• Frequently required to meet first-hand with customers in order to resolve quality issues that have arisen from our process.• Experimenting with new check sheets to ensure stronger checks are made to "hot" materials. Show less
-
-
-
-
Stablehand
-
Jan 2013 - Sep 2014
•Performed general maintenance of grounds and facilities such as fence repair, waterproofing, stall cleaning and maintenance, paddock drainage maintenance, yard work, and landscape maintenance. •Providing food, nutritional supplements, and medicines to equines and canines. •Cleaning, conditioning, and repair of tack and saddlery. •Grooming, washing, and rotating of equines from pasture, to paddock, to stall based on weather condition and general health. •Performed general maintenance of grounds and facilities such as fence repair, waterproofing, stall cleaning and maintenance, paddock drainage maintenance, yard work, and landscape maintenance. •Providing food, nutritional supplements, and medicines to equines and canines. •Cleaning, conditioning, and repair of tack and saddlery. •Grooming, washing, and rotating of equines from pasture, to paddock, to stall based on weather condition and general health.
-
-
-
-
Airport Administration Intern -- Marketing & Advertising
-
Mar 2012 - Jul 2012
• Maintained all digital and backlit displays located throughout the airport terminal areas in order to promote local businesses and attractions to traveling patrons who may be interested in visiting different areas during their stay. • Spearheaded a contract with a local construction firm to build special planters as part of an airport beautification project. • Redesigned the airport's emergency manual in accordance 14 CFR Part 139. All medical facility information, emergency contacts, business changes and new airfield maps were updated within the manual to insure that the AEM met federal standards. • Worked closely with airport management on strategy and grant proposals and assisted maintenance with runway inspections and FOD removal in accordance with 14 CFR Part 139. Show less
-
-
-
Plymouth Tube Company
-
United States
-
Mining
-
200 - 300 Employee
-
Plant Production Analyst - Kanban Supply Chain Specialist
-
May 2009 - Jun 2012
• Followed a lean data management system in production databases by tracking 90 days of data at a given time, and eliminating any possibility of duplicate data being entered into the tracking system. This greatly reduced space in the production database, which could lead to slowdowns on the server network. The 90 day information in the database caused the data to be translated into a more manageable amount of information in order to populate spreadsheets which would be distributed to middle and upper management. Older data would be confined to a separate folder for easy access, and would occasionally be requested by corporate managers, production engineers and upper management. • Designed new plant-wide productivity forms that would effectively reduce the analysis time of the data by 50% allowing more work to be done in less time. • Tracked all required and supplemental, and safety training files for employees, both digitally and in a file to be reviewed by management. This database maintained 365 days of data at any given time. All training data records were kept according to the Code of Federal Regulations. • Served as backup MRO purchasing agent for 37 months, but interim agent for a six-week period of time. During this six weeks, the main focuses were on lean purchasing methods and cost cutting, renegotiating pricing with vendors, and requirements planning in order to keep a minimum supply of materials, yet insure an adequate quantity. • Managed a supply crib with over ten thousand miscellaneous parts and MRO goods, coordinate a supply run schedule and maintained stock in 11 standard kanban areas and one programmable Nexiant MRO vending machine. Show less
-
-
-
-
Supply Crib Coordinator & Manufacturing Excellence Assistant
-
Mar 2008 - Dec 2008
• Coordinated supply routes and schedules for 11 facility kanban areas as part of a lean manufacturing initiative. During this time, I successfully overhauled the kanban pull-card system and provided training to insure that the system would be properly used by employees.• Controlled and maintained central UPS shipping area for the facility used by Administration, Maintenance and Quality Assurance• Maintained floor finishes, assisted in safety striping of concrete floors, and designated safety areas plant-wide in accordance with 29 CFR 1910.22.• As part of continuous improvement, I assisted the manufacturing excellence coordinator in 5s and 6s inspections of the facility. During this time PTWM possessed some of the greatest 5s scores companywide.• In order to prevent downtime in another department, I also supplemented production staff in finish departments. Show less
-
-
Kanban Coordinator
-
Feb 2006 - Mar 2008
• Maintained the plant's supply crib by insuring that all items' maximum and minimum levels were clearly defined and strictly adhered to.• Checked inventory levels plant-wide and maintained inventory in 11 kanban areas throughout the shop floor.• Shipped and received freight.
-
-
Education
-
University of Louisiana Monroe
Business Administration and Management, General -
Louisiana Tech University
Bachelor of Science (B.S.), Aviation/Airway Management and Operations -
West Monroe High School
High School Diploma, High School/Secondary Diplomas and Certificates
Community
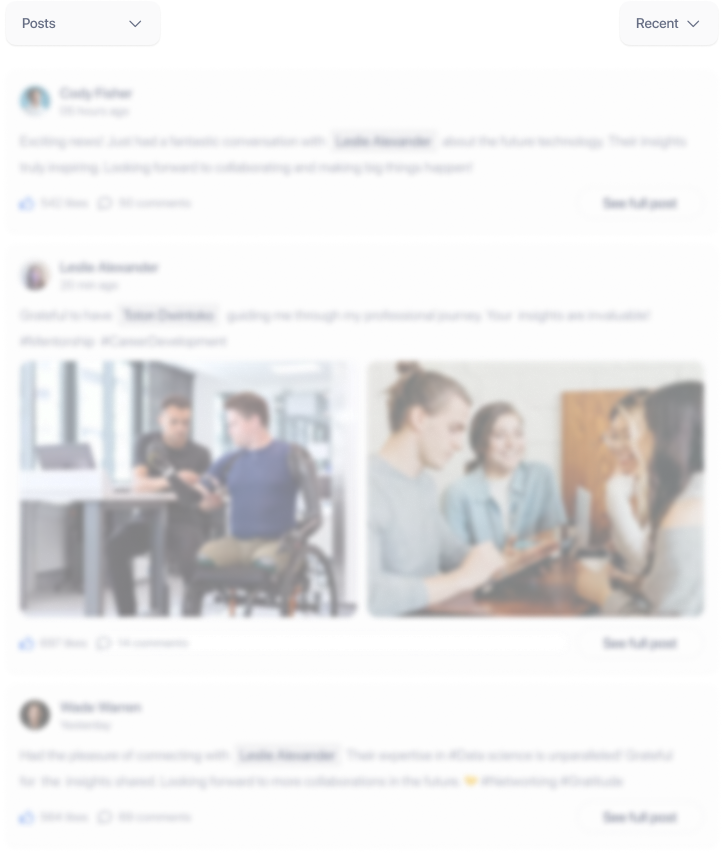