Bharat G.
Student Coordinator (International Relations Cell) at National Institute of Industrial Engineering- Claim this Profile
Click to upgrade to our gold package
for the full feature experience.
Topline Score
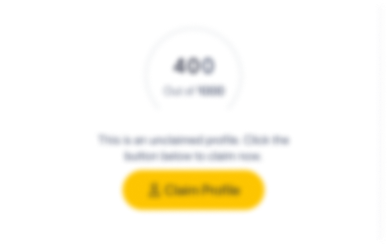
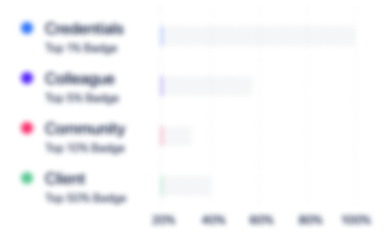
Bio


Experience
-
Indian Institute of Management Mumbai
-
India
-
Higher Education
-
200 - 300 Employee
-
Student Coordinator (International Relations Cell)
-
Oct 2022 - Present
-
-
-
HDFC Bank
-
India
-
Banking
-
700 & Above Employee
-
Summer Intern (Credit Analytics and Innovation-CRAIN)
-
Apr 2023 - May 2023
-
-
-
Outlook Publishing (India) Pvt. Ltd.
-
Media Production
-
700 & Above Employee
-
Winter Intern
-
Jan 2023 - Feb 2023
Business Analytics Business Analytics
-
-
-
LNJ Bhilwara Group
-
India
-
Textile Manufacturing
-
300 - 400 Employee
-
Executive QA/QC at BMD Private Limited
-
Aug 2020 - Jun 2022
Quality assurance, quality control and quality management of water resistant and repellent home furnishing textiles, flame retardant work wear and laminated composite textiles, automotive interior furnishing functional fabric, cut patterns and trims. Conducting trials and sampling on critical quality issues for process and product verification and validation with analysis and testing of aforesaid intermediate fabric and final product. Daily data management and data analysis by implementing formats, check sheets, and report making using bar graph, Pareto chart, scatter diagram for defect analysis and problem solving. Preparation of SOP, WI, OPL, HIRA, EAIA, FMEA and Quality Gate documents. To attend and resolve customer complaints (From Hyundai, KIA, Honda, VW, Skoda, Nissan, Furlenco, Tarasafe, Nex-G, Portwest) and establish fruitful customer relationship (CRM). Preparation of A3, 8D, 5Why, customer specific inspection reports for defect analysis and problem solving including RCA (Root cause analysis) and CAP (Corrective &preventive action) activities. Process audit, product audit and internal auditing of several departments. Decision making,shade evaluation and risk management and deviations on critical supplies. Leading cut pattern and workwear CFT for continual quality improvement. Implementation of 5S, KAIZEN and providing regular trainings to workers related to quality improvement in the department. Minimized lamination droppings by reducing 2 per 100 meters of fabric from 5 per 100 meters. Reduction in PU patch peel-off from 25% to 8.5% monthly. Reduction of fabric wastage (FRC) in inspection department from 4.27% to 3.6% monthly. Implementation of ERP system in work wear and cut patterns inspection process. Achieved “Zero customer complaint” in Q4 2021 from cut patterns, trims customers. 2% cost saving in several products by wastage reduction. Show less
-
-
-
INMAS, Defence Research and Development Organization (DRDO)
-
India
-
Defense and Space Manufacturing
-
100 - 200 Employee
-
Research Intern
-
Dec 2018 - Jun 2020
-
-
-
Shri lakshmi Cotsyn Limited
-
Textile Manufacturing
-
100 - 200 Employee
-
Summer Intern
-
Jun 2017 - Jul 2017
-
-
Community
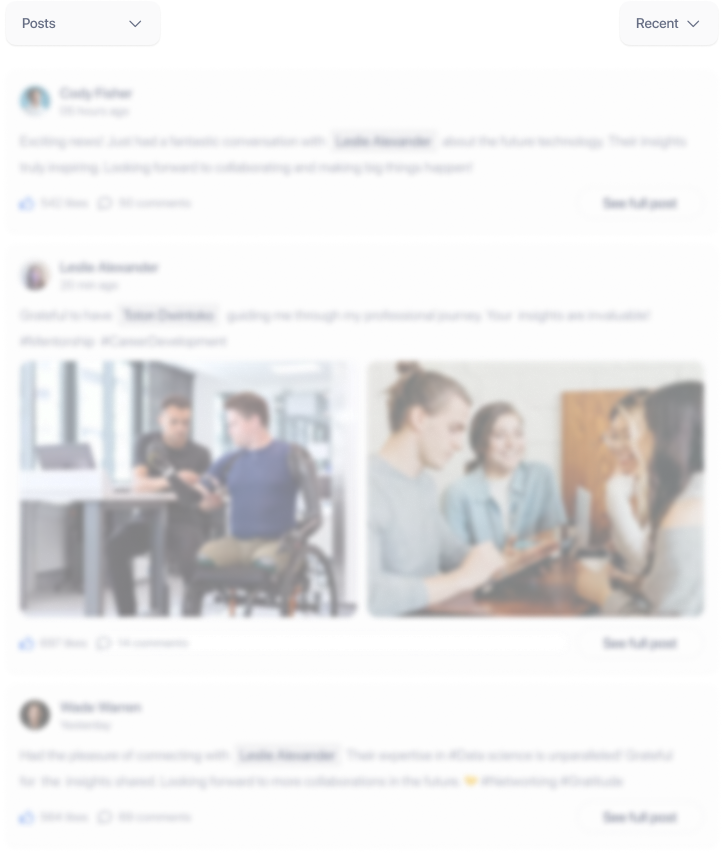