Iain Reynolds
Principal Engineer at Apollo- Claim this Profile
Click to upgrade to our gold package
for the full feature experience.
-
French -
Topline Score
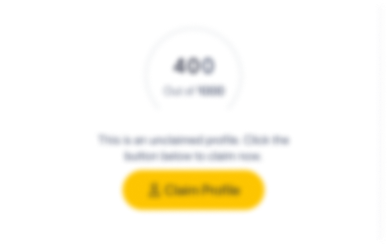
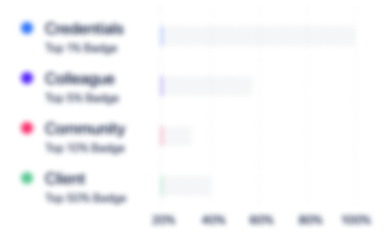
Bio

Monica Mwanje
I had the pleasure of working alongside Iain in the same process engineering team at Jacobs. Iain is a highly skilled and knowledgeable process engineer. Iain's work experience and technical specialism enable him to offer great insights and thus challenge thinking in a project team. It was great working with Iain; he's a real asset to any team he joins.

Monica Mwanje
I had the pleasure of working alongside Iain in the same process engineering team at Jacobs. Iain is a highly skilled and knowledgeable process engineer. Iain's work experience and technical specialism enable him to offer great insights and thus challenge thinking in a project team. It was great working with Iain; he's a real asset to any team he joins.

Monica Mwanje
I had the pleasure of working alongside Iain in the same process engineering team at Jacobs. Iain is a highly skilled and knowledgeable process engineer. Iain's work experience and technical specialism enable him to offer great insights and thus challenge thinking in a project team. It was great working with Iain; he's a real asset to any team he joins.

Monica Mwanje
I had the pleasure of working alongside Iain in the same process engineering team at Jacobs. Iain is a highly skilled and knowledgeable process engineer. Iain's work experience and technical specialism enable him to offer great insights and thus challenge thinking in a project team. It was great working with Iain; he's a real asset to any team he joins.

Experience
-
Apollo
-
United Kingdom
-
Software Development
-
1 - 100 Employee
-
Principal Engineer
-
Jun 2016 - Present
-
-
-
Reynolds Engineering Consultancy
-
United Kingdom
-
Oil and Gas
-
Director
-
2010 - Present
-
-
-
KCA Deutag
-
Oil and Gas
-
1 - 100 Employee
-
Senior Process Engineer
-
Mar 2013 - Dec 2015
Statoil/DSME –Mariner Drilling Module Detailed Design (North Sea, UK) Drilling module system engineer for the heavy oil producing PDQ Mariner platform. The systems designed included the cutting-edge Intervention & Completion Unit (ICU) and the Drilling & ICU Seawater distribution. The Mariner Platform has a separate ICU beneath the Main Drill Rig to perform work-overs on the existing wells, while Main Rig & Jack-Up drilling operations continue. The unique process design of the ICU was developed with the approval of the Client and Operations, to provide maximum flexibility to perform numerous operations using a number of different fluids. Interfacing with equipment suppliers, Topsides and the main drilling rig, a comprehensive, HAZOP compliant, Issued for Construction (IFC) design was achieved. The seawater system required numerous redesigns due to reduced availability of supply and increased supplier package demands, an innovative network was implemented. All design work was compliant to NORSOK, Statoil and UK sector regulations. Show less
-
-
-
SNC-Lavalin
-
Canada
-
Civil Engineering
-
700 & Above Employee
-
Principal Process Engineer
-
Jun 2011 - Mar 2013
Petróleos de Venezuela (PDVSA) – Rio Caribe/Mejillones FEED (Caribbean, VE) Lead HYSYS simulation engineer for the Mejillones & Rio Caribe Offshore Greenfield Gas/Condensate field development FEED project managing a team of four simulation engineers. The first phase demanded the process design and optimisation of the 250MMSCFD Rio Caribe FPSO, a Wellhead Platform and associated subsea well tiebacks to maximise condensate production while re-injecting produced gas. The recovery from the condensate-rich Rio Caribe field was increased by 23% over the concept design, increasing the revenue for the Early Production Phase by nearly $1billon. For the second ‘Life of Field’ phase of the project, the role required the integration of the Mejillones production fluids which gathered 400MMSCFD of lean gas from three subsea well clusters to a local reception jacket, the replacement of the FPSO for a Central Processing Platform sited in the Rio Caribe field and optimisation of fluid conditioning for single phase gas and condensate export to the onshore processing terminal. The optimisation called for the co-mingled Mejillones and Rio Caribe gas to undergo JT hydrocarbon conditioning with associated heat integration to achieve arrival specification. The position executed a number of in-depth optimisations, studies and reports during the process design including significant interfacing with the Flow Assurance team to create the most cost effective and technically competent design for both subsea and topsides. PFD’s, H&MB’s, P&ID’s, HazOp’s, Process Datasheets, Cause & Effects for the Process and Utilities were completed as well as authoring several technical notes and performing numerous client presentations. Show less
-
-
-
Xodus Group
-
United Kingdom
-
Retail Office Equipment
-
Principal Engineer
-
2010 - Jun 2011
Orion Methanol Assessment - Process study for the Orion subsea tie back to Clyde to determine how methanol, used for hydrate inhibition, passes through the Clyde separation and compression systems. Using dynamic simulation, the methanol was tracked as the Orion field was brought online. The partitioning of methanol to the vapour phase is known to be inaccurate in HYSYS, a deficiency of the Soave-Redlich-Kwong (SRK) Equation of State (EOS) package, therefore Multiflash software using the Cubic-Plus-Association (CPA) EOS package was employed to adjust for the flash vessels. To ensure the Export Gas methanol concentration limits were not breached, the study presented the Export Gas concentrations as a function of time. Laggan Tormore Subsea Gas Compression Study - Process study to develop a high-level design for both a Subsea Gas Compression (SSGC) concept and an alternative platform-based compression concept. The study involved preparing Block Flow Diagrams (BFD's), HYSYS simulations for provide the basis for Heat & Material Balances (H&MB's) and Equipment lists for both concepts. Clyde Platform HYSYS Update and Recovery Factors Review - This project brought the Clyde Platform Master HYSYS model up-to-date using current production data and operating philosophies. This enabled the Orion Recovery Factors report to be updated to assist Clyde operations. Show less
-
-
-
-
Senior Process Engineer
-
2007 - 2010
Design engineer for a Process Design Package (PDP) for a partial oxidiser and syngas conditioning unit in a Biomass to Liquids project (BTL). The design package included; Aspen Plus process simulation, heat & mass balance, Process Flow Diagrams (PFD’s), Piping & Instrumentation Diagrams (P&ID’s), HTRI heat exchanger design, Process Data Sheets (PDS’s). Process lead for the onshore Natural Gas Dewpointing and Monoethylene Glycol (MEG) storage and regeneration FEED package (seconded to Genesis Oil & Gas Consultants) for an underground gas storage project. The role involved the management and production of documentation including P&ID’s, PFD’s, Process Safeguarding Flow Schemes (PSFS’s), equipment sizing calculations, PDS’s, preliminary control valve & relief valve sizing, API 14C analysis, HAZID/HAZOP. Strict adherence to API standards and delivery of work to very tight deadlines was required to take all FEED deliverables to ‘Approved for Design’ (AFD) level. Process lead for the Utilities & Offsites (U&O) design team on a 270 MWe coal-based IGCC Demonstration Plant with Carbon Capture FEED Package. The U&O design package included water treatment units such as vacuum deaerators, RO membranes, mixed bed and multimedia filters, as well as other systems including the cooling water distribution network; steam systems; bulk chemical storage tanks; effluent treatment facilities and gaseous conditioning and transport systems. The role required the management of a team of up to nine process engineers tasked with producing P&ID’s, UFD’s, Material Selection Diagrams (MSD’s), equipment sizing calculations, PDS’s, utility schedules, control valve, relief valve, line and motor lists. The position also demanded the production of a Power Island auxiliary equipment design package which included compressors, closed circuit heat exchange systems and flash drums as well as authoring the project design basis. Show less
-
-
-
-
Process Engineer
-
2004 - 2007
The Delkor group of companies specialise in the design and sale of solid–liquid separation capital equipment on a worldwide stage. The product portfolio included linear screens, filter presses, hydrocyclones, thickeners and horizontal belt filter for the mining, chemical, water and power industries. The process engineer position fell into two main roles: The Design and Technical Sales role included: laboratory and site testwork; data analysis and report writing; equipment sizing and materials selection; costing and tender submissions to clients; sales meetings with clients; financial planning, scheduling and cash flow analysis of projects; contract handovers including P&ID's and PFD's; project consultation and O&M manual preparation. The Commissioning and Site Work role required: risk assessment and method statement preparation; mechanical installation; preparation and completion of commissioning instructions; cold loop testing, hot commissioning and process acceptance testing; completion of handover and acceptance certificates; client liaison and operator training; troubleshooting and consultancy. The role required numerous overseas travels to countries including China, India, Portugal, Spain, Turkey and the USA for commissioning, testwork and sales meetings. Successfully, single-handedly commissioned the four largest Flue Gas Desulphurisation (FGD) gypsum horizontal belt filters in the world, one of the world’s largest sodium bicarbonate horizontal belt filters and numerous smaller scale horizontal belt filters. Show less
-
-
-
British Sugar
-
United Kingdom
-
Food and Beverage Manufacturing
-
700 & Above Employee
-
Process Engineer
-
2000 - 2004
Spent an industrial placement year with the company which included th design, installation and commissioning of a £100k sulphuric acid project and a £25k filtration project. Various optimisation projects were also undertaken and presented to the appropriate area managers. Upon completion of the year, the position of graduate process engineer was offered and accepted. Trained as a shift team leader, individual parts of the factory were managed, along with the people in those areas, to ensure maximum productivity. Developed an understanding of many chemical engineering unit operations such as diffusion, carbonatation, evaporation, filtration and solids handling. Gained approval and commenced the installation of a £100k fire safety project as well as designing and installing a £25k thickener underflow efficiency project. Achieved the highest mark of the 2002 graduate intake at the end of year assessment. Show less
-
-
Education
-
Loughborough University
BEng (Hons), Chemical Engineering
Community
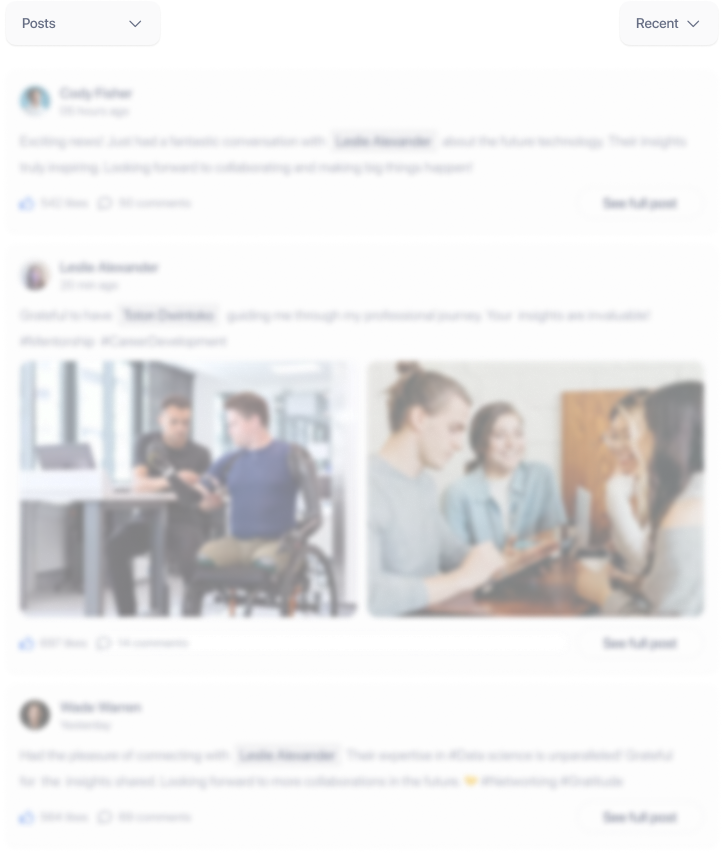