Hubert Parsons
Quality Assurance Manager at Superior Glove- Claim this Profile
Click to upgrade to our gold package
for the full feature experience.
-
English Native or bilingual proficiency
-
Sign Languages Limited working proficiency
Topline Score
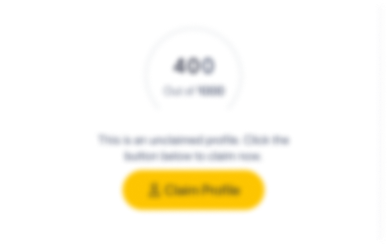
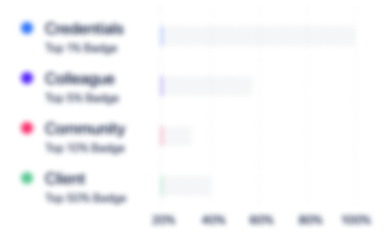
Bio


Credentials
-
Certified Commercial Inspector
International Association of Certified Home Inspectors (InterNACHI)Apr, 2015- Nov, 2024 -
Commercial Inspector
Carson Dunlop Weldon and Associates LtdApr, 2015- Nov, 2024 -
IAC2 Certified
International Association of Certified Home Inspectors (InterNACHI)Mar, 2015- Nov, 2024 -
Certified Home Inspector
Carson DunlopMay, 2014- Nov, 2024
Experience
-
Superior Glove
-
Canada
-
Wholesale
-
100 - 200 Employee
-
Quality Assurance Manager
-
Jan 2016 - Present
-
-
-
I
-
Acton / Georgetown area
-
Owner Operator
-
Aug 2013 - Aug 2015
Home Inspection on new and resale home. Thermal imaging, Maintenance inspection, Pre-purchase inspection Pre-listing inspection Certified Mold Inspector Certified Commercial Inspector 30 days + 1st year of new home warranty inspection. Completed 420 hours of academic hours under the national certification program through Carson Dunlop. Know What You're Buying BEFORE You Own It! Call appointment booking call 519 278 4474 Cell Phone 416 706 5519 Home Inspection on new and resale home. Thermal imaging, Maintenance inspection, Pre-purchase inspection Pre-listing inspection Certified Mold Inspector Certified Commercial Inspector 30 days + 1st year of new home warranty inspection. Completed 420 hours of academic hours under the national certification program through Carson Dunlop. Know What You're Buying BEFORE You Own It! Call appointment booking call 519 278 4474 Cell Phone 416 706 5519
-
-
-
Future steel building
-
Brampton
-
Quality assurance manager
-
Oct 2012 - May 2014
Quality Assurance Manager / Assistant Plant Manager • Designed and implemented a quality control system to track internal and external defects • Designed and implemented KPI system, for scrap tracking, machine efficiency, defects per unit. (DPU) Resulting in cost savings for 2013- $38,000+ and 2014- $45,000+ • Designed and implemented an inventory tracking and scheduling system to show plan v’s actual product on hand. • Improved communication between management and plant employees by implementing weekly and monthly plant wide meetings. • Work with plant employees to show them the importance of good organization at each work station • Implemented Standard work and Key Point at work station. • Collaborate with dispatch and transportation companies on truck scheduling and loading efficiency, which has resulted in drastically reduced wait times. Show less
-
-
-
Toyota Boshoku America
-
United States
-
Motor Vehicle Manufacturing
-
700 & Above Employee
-
QCAM
-
2006 - 2012
Quality Engineering / Quality Control Assistant Manager • Tier 1 supplier to Toyota Motors (Lexus) • Tier 2 supplier to Johnson Controls (Toyota Corolla / Matrix) • Manage a team of 18 staff in the areas of line position, rotation and modified duties. • Direct liaison to Toyota Motors providing and maintaining excellent customer relations. • Work with manufacturing department to implement standard work procedures (Process Engineer). • Provide countermeasure and solutions to customers with regards to defective product. • Working with first in and first out process as it relates to new level parts. • Received JD Power award for the past 5 years for quality and customer service while working in conjunction with JD Power and Associates. • Continually responsible for the preparation of various monthly / weekly / daily reports in MS Excel and Word. • Effectively communicate and assist customer to provide excellent customer service. • Work directly with Toyota on new model launches • Preparing Inspection Standard, Provision Approvals, MQC, PFMEA, for approvals to Toyota. • Visit supplier for process reviews and countermeasure follow. • Prepare A3, Naza Naza (5whys). • Work in the plastic area with injection molds to improve flow line, color, grain, during new model. • Work in the seating area to improve quality. Show less
-
-
-
Trim Masters Inc.
-
Motor Vehicle Manufacturing
-
1 - 100 Employee
-
QCAM
-
2000 - 2006
Quality Control / Problem Resolution • Tier 1 supplier to Toyota Motors • Responsible for customer relations. • Worked with manufacturing department to implement standard work instructions (Process Engineer). • Provided countermeasure and solutions to customers with regards to defective product. • Arranged and conducted onsite inspections with suppliers to review countermeasure effectiveness for short and long term. • Prepared problem resolution reports utilizing MS Word, Excel & PowerPoint and provided the information to customers in timely manner. • Managed issues with regards to product defects and personnel. Show less
-
-
-
Johnson Controls
-
Ireland
-
Industrial Machinery Manufacturing
-
700 & Above Employee
-
line tech
-
1996 - 2000
Line Teck, Master Trainer, Line Teck, Master Trainer,
-
-
Education
-
Bureau veritas
Certification, Quality -
Conestoga College
Certified Quality Assurance, Quality Assurance -
Carson Dunlop
Certificate, Home Inspection -
Toronto School of Business
MCBA, Micro-computer business accounting
Community
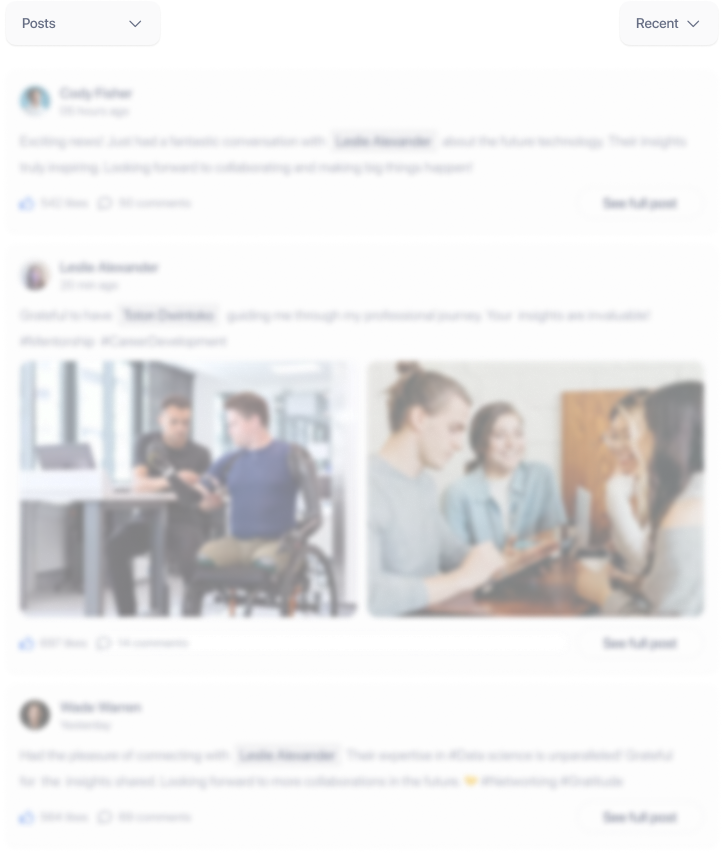