
Hod Zank
Director of Manufacturing at CLEAN ROOMS INTERNATIONAL- Claim this Profile
Click to upgrade to our gold package
for the full feature experience.
Topline Score
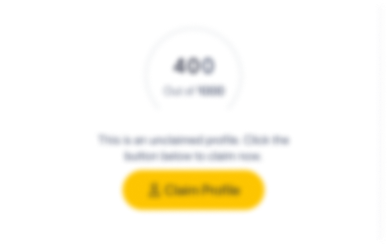
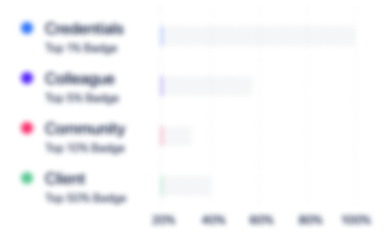
Bio


Credentials
-
Performance Management: Conducting Performance Reviews
LinkedInJul, 2019- Nov, 2024 -
Kata for Daily Improvement
University of MichiganNov, 2016- Nov, 2024 -
Lean Manufacturing
University of MichiganSep, 2005- Nov, 2024
Experience
-
CLEAN ROOMS INTERNATIONAL
-
United States
-
Facilities Services
-
1 - 100 Employee
-
Director of Manufacturing
-
Jun 2021 - Present
Responsible for quality, manufacturing, shipping and receiving, inventory control, and purchasing operations. Responsible for quality, manufacturing, shipping and receiving, inventory control, and purchasing operations.
-
-
-
ODL, Inc
-
United States
-
Wholesale Building Materials
-
300 - 400 Employee
-
Manager of Manufacturing
-
Dec 2018 - Apr 2021
Role expanded to manufacturing manager of Zeeland campus. Caring for 220-plus employees across 3 buildings, 3 shifts, and 350,000 square feet of manufacturing space. $95 million annual plant revenue. Improved safety metric’s by 55% 2020Improved direct and indirect labor costs by 10% 2020Improved Great Place To Work score by 13% in 2019Developed front line leadership teams around personal accountability and empowerment.
-
-
Operations Manager
-
Jan 2015 - Dec 2018
Promoted to operations manager with responsibility for decorative glass assembly and shipping / receiving. Manage 120-plus employees across two buildings and 3 shifts. $35 million annual plant revenueShipping and Receiving efficiency gains of 15% by standardizing processes and solving problems dailyCut quality FPY by 50% developing a first piece process and improving the control planSplit sequential delivery process into two loops that improved indirect labor efficiency by 33% (A3 TPS process)Implemented floor management development systems (TPS)Championed and lead discovery project team that implemented the first (ResolveTM Sealant) robotic foam dispensing cell
-
-
Focus Factory Manager
-
Jan 2009 - Jan 2015
Promoted to manager of injection molding operations with responsibility of manufacturing, scheduling, inventory, engineering, maintenance and new product launch of all injection molding projects. Managed 100,000 sq ft., and 50-plus employees.• Employee safety incidents improved by 75%• OEE improved from 69% to 85%• Scrap rates improved from 3.5% to 2.1%• Improved production up-time and cycle time performance by 40% or $410,000 annually.
-
-
Senior Manufacturing Engineer
-
Jan 2002 - Jan 2009
Promoted to senior manufacturing engineer and lean implementation leader for all manufacturing operations.• Reduced 7,000 miles a year in fork truck transportation waste in the plant annually.• Trained 400 employees the basics of lean manufacturing in a 3-hour class.• Developed and implemented the Standard Work method through coaching, training resulting in solved problems and efficiency improvements of 10%• Liquidated $60,000 of inventory by converting push to pull Kanban systems.• Invented, developed, and implemented the TriSYS product line.
-
-
Senior Porcess and Tooling Engineer
-
Jan 2001 - Jan 2002
Promoted to senior process engineer and NPDP projects engineer managing tooling design, build, and production validation.
-
-
Process Engineer
-
Jun 1998 - Jan 2001
Hired as manufacturing engineer of the injection molding department. Purchased equipment, robotics, and developed procedures and process sheets.
-
-
-
ADAC Automotive
-
Motor Vehicle Manufacturing
-
400 - 500 Employee
-
Engineer Intern
-
Jan 1996 - Jan 1997
Developed a boundary sample process to help team members verify poke yoke systems. Updated and maintained PFMEA documentation for certifications. Developed a boundary sample process to help team members verify poke yoke systems. Updated and maintained PFMEA documentation for certifications.
-
-
Education
-
Ferris State University
BS, Plastics Engineering
Community
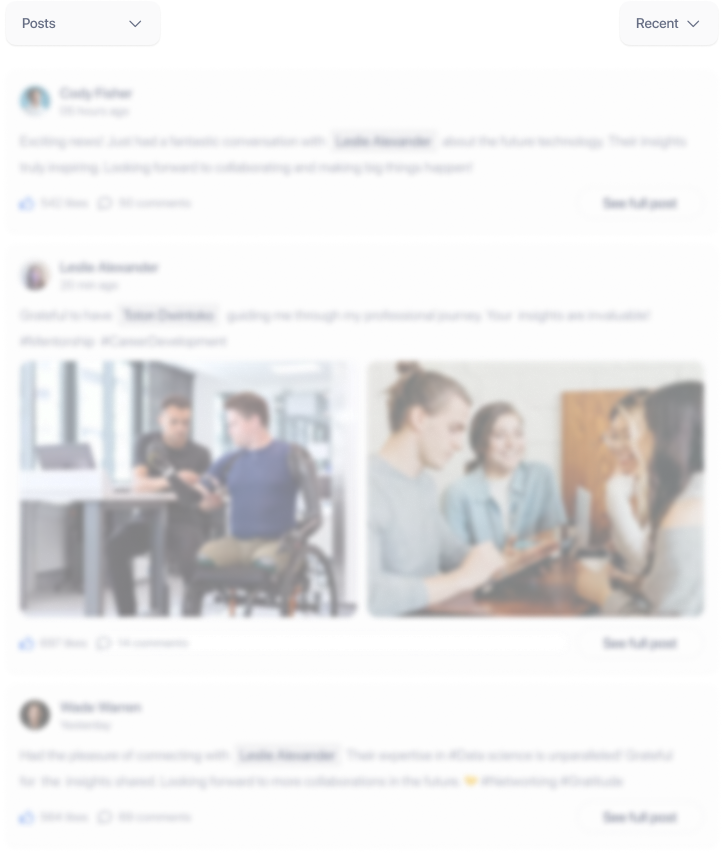