Hermann R. Leopold, SSGB
Plant Manager at Elite Comfort Solutions LLC- Claim this Profile
Click to upgrade to our gold package
for the full feature experience.
-
English Full professional proficiency
-
Spanish Native or bilingual proficiency
Topline Score
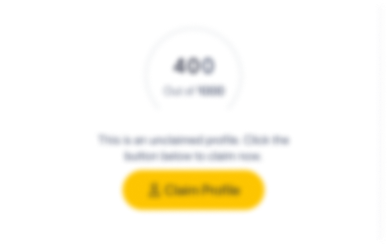
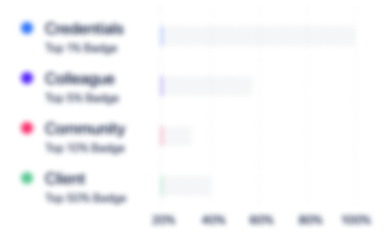
Bio


Experience
-
Elite Comfort Solutions LLC
-
United States
-
200 - 300 Employee
-
Plant Manager
-
Nov 2022 - Present
I am thrilled to announce my smooth transition into the plant manager role for Elite Comfort Solutions pouring plant in Newnan, GA. ECS is a Leggett & Platt Company I am thrilled to announce my smooth transition into the plant manager role for Elite Comfort Solutions pouring plant in Newnan, GA. ECS is a Leggett & Platt Company
-
-
-
FXI
-
United States
-
Consumer Goods
-
700 & Above Employee
-
Sr Plant Manager
-
Oct 2008 - Aug 2022
Reported to the Regional Manufacturing VP governing a $35M budget, while overseeing 8 Managers (Production, Quality Maintenance, Technical, Inventory, Safety/HR, Inventory, and Logistics staff). ▪ Led the production, technical and ops roadmap of a high-tech research & development manufacturing plant in Miami; executed lean production on finished goods, sub-assemblies, services, OEM raw materials, fabricators, and retailers. ▪ Transformed plant production by building a… Show more Reported to the Regional Manufacturing VP governing a $35M budget, while overseeing 8 Managers (Production, Quality Maintenance, Technical, Inventory, Safety/HR, Inventory, and Logistics staff). ▪ Led the production, technical and ops roadmap of a high-tech research & development manufacturing plant in Miami; executed lean production on finished goods, sub-assemblies, services, OEM raw materials, fabricators, and retailers. ▪ Transformed plant production by building a high-performance management team that reduced total plant scrap rate by 20% and facility overtime by 35% from 2016 to 2020; bolstered productivity by 20% achieving Plant of the Year Award YOY. ▪ Implemented a new COVID measure by partnering with procurement, production, and logistics teams to offset supply chain disruption in 2021; regulated budget, mitigated material shortages, and maintained 98.5% OTIF delivery w/ 2-day lead time. ▪ Spearheaded a plant-wide (EH&S) Program in collaboration with team members by identifying root-cause analysis, streamlining workflows, and training; reduced major incidents by 100% across 6+ years within the plant. ▪ Devised a lean-management method (VSM) and PMP preventative maintenance program in partnership with leadership to analyze and iterate material/information process flows; improved material and labor costs by 25%? ▪ Established the first Quality Management System (QMS), hired a QC Manager, and partnered with corporate stakeholders/line managers; created new SOPs and facilitated Six Sigma (SSYB) training which improved quality by 50%. ▪ Optimized the foaming process and increased production quality utilizing Gantt charts, foam technology, and interfacing with sales, tech, and customers; enhanced performance controls, EBITDA, scrap rate, and customer satisfaction scores. ▪ Fostered a culture of safety, lean production, collaboration, and established a continuous improvement framework and mindset for managers and employees using VSM and Kaizen events.
-
-
Technical Manager
-
Dec 1991 - Sep 2008
Under the direction of the Plant Operations Manager (formerly Flexible Foam), oversaw a budget of $12M and led a staff of 7 direct reports (Supervisors, Production, Loading & Operators) and provided valuable technical oversight, product, quality, and process efficiency. ▪ Cultivated a sense of belonging with a safety focus by strengthening team collaboration ensuring pour line efficiency, product specifications, training, and staff fulfillment; balanced growth with fiscal responsibility… Show more Under the direction of the Plant Operations Manager (formerly Flexible Foam), oversaw a budget of $12M and led a staff of 7 direct reports (Supervisors, Production, Loading & Operators) and provided valuable technical oversight, product, quality, and process efficiency. ▪ Cultivated a sense of belonging with a safety focus by strengthening team collaboration ensuring pour line efficiency, product specifications, training, and staff fulfillment; balanced growth with fiscal responsibility and quality production. ▪ Partnered with stakeholders and Sales to expand the business into Central, South America, and the Caribbean markets. ▪ Led the implementation of a new C02 foam pouring technology with minimal foam scrap rate levels reducing foam-line and looper operations rates. ▪ Execute running trials of new formulations and chemicals for adjusting existing formulations as necessary to meet product specifications; identify opportunities for continuous improvement in foam quality of foam and process workflows. ▪ Established and set forth policies, KPIs, SOPs, learning interventions, and research-based strategies; facilitated staff meetings and training to promote synergy and development. ▪ Evaluated the performance of supervisors, pour line engineers, and staff in research, development, product design, and inventory control; served as an SME on all production, technical and quality measures per OSHA guidelines. ▪ Leveraged data-driven insights and previous benchmarks to optimize process workflows, raw material inventory, and waste; fortified team engagement through capability building, positive feedback, and development.
-
-
-
Foamex
-
United States
-
Chemical Manufacturing
-
100 - 200 Employee
-
Technical Manager, Pour Line
-
Jan 1982 - Dec 1991
Reported to the Plant Manager (formerly Crain Industries) and assisted with the plant establishment, operations, and profitability of a new pouring facility in Kent, WA. Managed 9 staff (Supervisors, Production & Techs) to monitor/improve process efficiency, safety, and quality standards. ▪ Partnered with leadership, engineers, and corporate stakeholders in creating manufacturing production SOPs, guidelines, and equipment fulfillment such as pouring machines, storage tanks, conveyors… Show more Reported to the Plant Manager (formerly Crain Industries) and assisted with the plant establishment, operations, and profitability of a new pouring facility in Kent, WA. Managed 9 staff (Supervisors, Production & Techs) to monitor/improve process efficiency, safety, and quality standards. ▪ Partnered with leadership, engineers, and corporate stakeholders in creating manufacturing production SOPs, guidelines, and equipment fulfillment such as pouring machines, storage tanks, conveyors, controllers, and heat exchangers. ▪ Acted as a project lead providing extensive research & development for clients and regional plants on material selection, product designs, and production. ▪ Led the design and development of 50 chemical formulation and foam prototypes to expand the product landscape within the plant; implemented workflow planning and ensured that foam requirements are met in a cost-effective/efficient manner. ▪ Provided analytical expertise for process improvements utilizing lean tools such as SQC and SPC; troubleshoot equipment problems and solve process issues with plant engineering, maintenance, and corporate engineering teams. Show less Reported to the Plant Manager (formerly Crain Industries) and assisted with the plant establishment, operations, and profitability of a new pouring facility in Kent, WA. Managed 9 staff (Supervisors, Production & Techs) to monitor/improve process efficiency, safety, and quality standards. ▪ Partnered with leadership, engineers, and corporate stakeholders in creating manufacturing production SOPs, guidelines, and equipment fulfillment such as pouring machines, storage tanks, conveyors… Show more Reported to the Plant Manager (formerly Crain Industries) and assisted with the plant establishment, operations, and profitability of a new pouring facility in Kent, WA. Managed 9 staff (Supervisors, Production & Techs) to monitor/improve process efficiency, safety, and quality standards. ▪ Partnered with leadership, engineers, and corporate stakeholders in creating manufacturing production SOPs, guidelines, and equipment fulfillment such as pouring machines, storage tanks, conveyors, controllers, and heat exchangers. ▪ Acted as a project lead providing extensive research & development for clients and regional plants on material selection, product designs, and production. ▪ Led the design and development of 50 chemical formulation and foam prototypes to expand the product landscape within the plant; implemented workflow planning and ensured that foam requirements are met in a cost-effective/efficient manner. ▪ Provided analytical expertise for process improvements utilizing lean tools such as SQC and SPC; troubleshoot equipment problems and solve process issues with plant engineering, maintenance, and corporate engineering teams. Show less
-
-
Education
-
DeVry University
Bachelor's Degree, Operations Management and Supervision -
Project Management Institute
Green Belt of Six Sigma Methodology -
IPAE - Lima, Peru
Study of the English Language & American Culture
Community
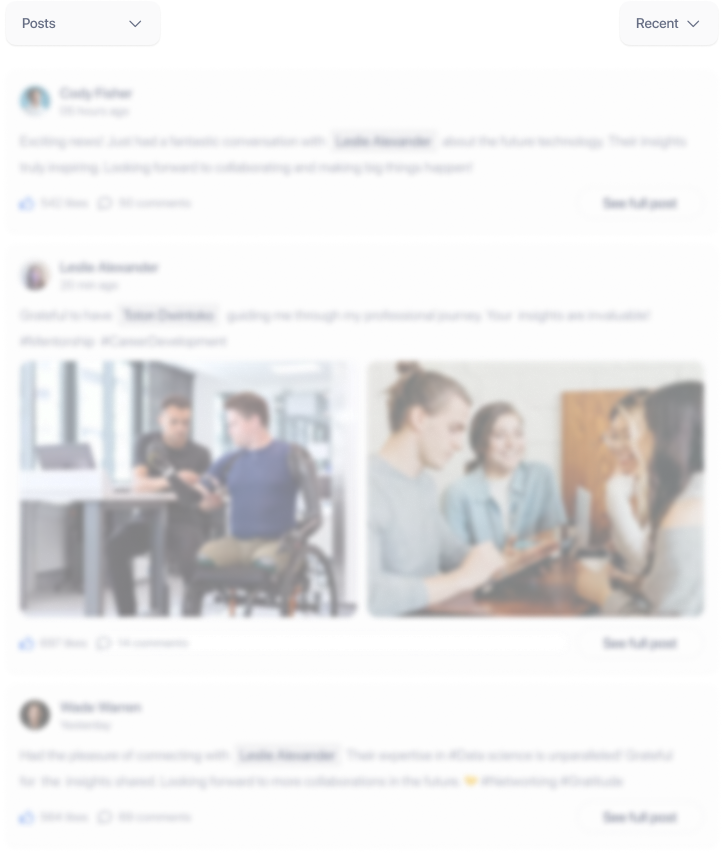