Herman Chiu, P. Eng
Quality at JFE Shoji Power Canada Inc.- Claim this Profile
Click to upgrade to our gold package
for the full feature experience.
Topline Score
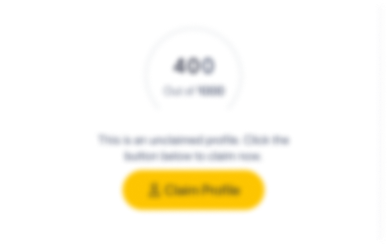
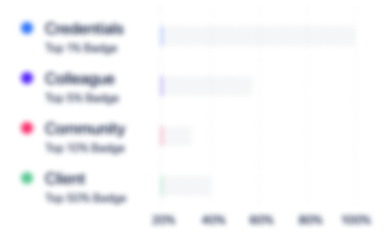
Bio

Hardeep Singh
Herman was a charming, happy and very hard worker. we all enjoy to work together and transfor the knowlege and information. we were working together for contineous improvemets and found root causes and also found the solutions. I highly regards Harman.

Victor Zamorano
Herman is a hard worker, he takes the challenges and gets the results. I've know Herman for 2 years and during the time we've worked together he has shown the skills and the diligence to get the job done.

Hardeep Singh
Herman was a charming, happy and very hard worker. we all enjoy to work together and transfor the knowlege and information. we were working together for contineous improvemets and found root causes and also found the solutions. I highly regards Harman.

Victor Zamorano
Herman is a hard worker, he takes the challenges and gets the results. I've know Herman for 2 years and during the time we've worked together he has shown the skills and the diligence to get the job done.

Hardeep Singh
Herman was a charming, happy and very hard worker. we all enjoy to work together and transfor the knowlege and information. we were working together for contineous improvemets and found root causes and also found the solutions. I highly regards Harman.

Victor Zamorano
Herman is a hard worker, he takes the challenges and gets the results. I've know Herman for 2 years and during the time we've worked together he has shown the skills and the diligence to get the job done.

Hardeep Singh
Herman was a charming, happy and very hard worker. we all enjoy to work together and transfor the knowlege and information. we were working together for contineous improvemets and found root causes and also found the solutions. I highly regards Harman.

Victor Zamorano
Herman is a hard worker, he takes the challenges and gets the results. I've know Herman for 2 years and during the time we've worked together he has shown the skills and the diligence to get the job done.

Experience
-
JFE Shoji Power Canada Inc.
-
Canada
-
Appliances, Electrical, and Electronics Manufacturing
-
100 - 200 Employee
-
Quality
-
Sep 2018 - Present
-
-
-
DENSO
-
United States
-
Motor Vehicle Manufacturing
-
700 & Above Employee
-
Quality
-
Oct 2017 - Sep 2018
-
-
-
-
Area Leader, Quality Engineering
-
Mar 2015 - Oct 2017
-
-
Engineering - Quality
-
May 2012 - Mar 2015
-
-
-
DENSO
-
United States
-
Motor Vehicle Manufacturing
-
700 & Above Employee
-
Lead Specialist, Quality Engineering
-
Aug 2010 - May 2012
- Managed team of Supplier Quality and Warranty Engineers - Created and presented yearly Goals and Objectives (G&O) to management to improve supplier processes, relationships and quality. - Investigated and resolved high profile customer warranty issue - Managed monthly budget for Supplier related scrap - Lead and coordinated Go and See (Genba) activities for customer concerns and Kaizen opportunities - Developed and coordinated themed based activities to promote plant quality… Show more - Managed team of Supplier Quality and Warranty Engineers - Created and presented yearly Goals and Objectives (G&O) to management to improve supplier processes, relationships and quality. - Investigated and resolved high profile customer warranty issue - Managed monthly budget for Supplier related scrap - Lead and coordinated Go and See (Genba) activities for customer concerns and Kaizen opportunities - Developed and coordinated themed based activities to promote plant quality awareness at DENSO. - Quality Assurance Visits to Suppliers to audit processes. - Collaborated with Suppliers in the resolution of quality issues
-
-
Advance Specialist, Quality Engineering
-
Jul 2009 - Aug 2010
- Advanced Specialist working in a Tier 1 facility manufacturing Engine Cooling Modules (ECM) and Heating Ventilation and Air Condition (HVAC) - OEM Liason for Toyota, Honda and Ford - Responsible for Toyota and Honda New Product Launches for Radiator and Condenser commodities - Responsible for meeting and exceeding customer quality key performance indicators and quick resolution to quality issues - Root cause analysis of daily production issues and managing the implementation of… Show more - Advanced Specialist working in a Tier 1 facility manufacturing Engine Cooling Modules (ECM) and Heating Ventilation and Air Condition (HVAC) - OEM Liason for Toyota, Honda and Ford - Responsible for Toyota and Honda New Product Launches for Radiator and Condenser commodities - Responsible for meeting and exceeding customer quality key performance indicators and quick resolution to quality issues - Root cause analysis of daily production issues and managing the implementation of corrective actions to prevent re-occurrence - Hosted monthly scrap reduction meetings with cross functional team. Deep analysis of Top 5 defects for month with tracking and verifying of countermeasures. - Internal process audit of assembly lines with high focus on process standards, poke yoke verifications, process work instructions, and countermeasure effectiveness.
-
-
-
SKD Automotive
-
Motor Vehicle Manufacturing
-
1 - 100 Employee
-
QA Supervisor
-
Jan 2007 - Apr 2009
Supervise and mentor Quality Team to ensure that SKD’s Quality Policies and Procedures are adhered to at all levels of production and, conformance to Quality Management Systems (QMS). Identifying business inefficiencies and developing Process Improvement plans.
-
-
QA Engineer
-
Mar 2003 - Jan 2007
Managed production quality aspects from prototype part trial to mass production and, developing Process Improvement plans for Production Quality Assurance.
-
-
QA Technician
-
Jan 2000 - May 2003
Tested and inspected products at various stages of production process. Compiled and evaluated statistical data to determine and maintain the quality and reliability of products.
-
-
Community
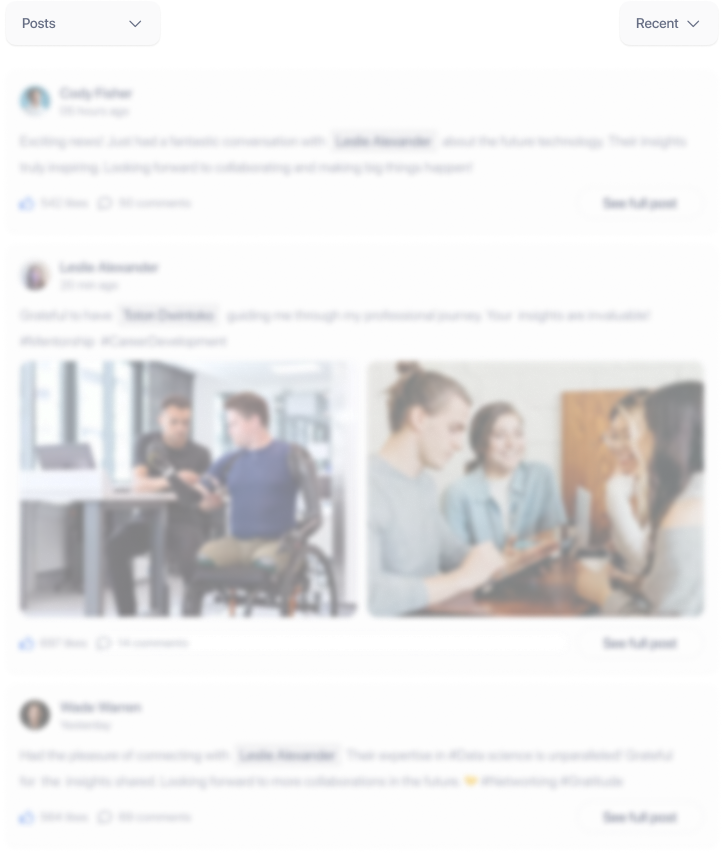