Herman Benard, Jr.
Director of Manufacturing at ValvTechnologies, Inc.- Claim this Profile
Click to upgrade to our gold package
for the full feature experience.
-
English -
Topline Score
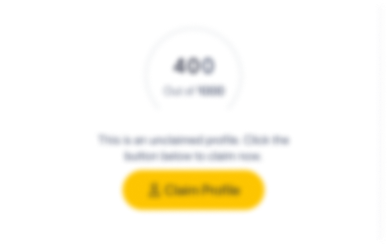
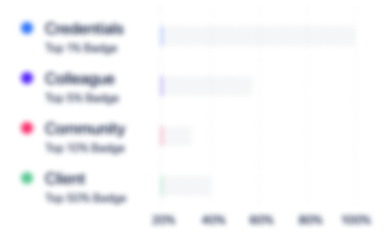
Bio
0
/5.0 / Based on 0 ratingsFilter reviews by:
Credentials
-
Six Sigma Green Belt
Igloo Products Corp.Jun, 2005- Sep, 2024 -
Leadership and Management
University of HoustonMar, 2002- Sep, 2024 -
(SMED) Die Changeover
University of HoustonAug, 2001- Sep, 2024 -
Principles of Lean Manufacturing
University of HoustonJul, 2001- Sep, 2024
Experience
-
ValvTechnologies, Inc.
-
Information Technology & Services
-
Director of Manufacturing
-
Oct 2016 - Present
-
-
-
Thrustmaster of Texas
-
United States
-
Transportation, Logistics, Supply Chain and Storage
-
1 - 100 Employee
-
Manufacturing Manager
-
May 2013 - May 2016
Responsible for strategic business planning and maximizing performance results for in house fabrication, machining, assembly, coating, inspection and testing capabilities. Managed and coordinated all areas of manufacturing at an 300,000 sq. ft. facility with an operations team of 28 salaried (8 Managers/12 Supervisors/8 Manufacturing Engineers) and 175+ hourly employees. Ensured that all 17 flexible assembly cells, 3 fit-up & 7 weld stations, 1 blast & 2 paint booths, and 5 CNC HBM’s/1 CNC Vertical mill/3 CNC VTC’s/3 CNC Horizontal lathes met schedule attainment, sales forecast, ran efficient, safe, and produced a quality product.Responsible for P&L functions of the plant. Managed the department expense budgets and assisted in development of the annual capital and cost savings plan.Improved plant On-Time delivery from 40% to 90% reduced line shutdowns and improved 5S scores.Drove design change in-sourcing $3M products with $750K savings and $1.2M absorption.Manage application of lean manufacturing principles in company operations including manual and CNC machining, welding and fabrication, assembly, and field service. Developed a 2 year plan to rollout the following lean concepts of standard work, 5S deep dives, visual factory, TPM, and kaizen.Documented best practices and implemented standard work (Takt Time & Work Sequence) as a stepping stone to begin Kaizen and continuous improvement activities. Implemented cellular manufacturing reducing process time, process waste, machines and labor requirements yielding $700K in savings.Ensure quality control in accordance with the company ISO-9001:2008 Quality Assurance System. Conducted root cause analysis and problem solving sessions (5 Why & 8D) exercises with cross functional teams.Maintained a safe work environment in accordance with company HSE standards and procedures. Improved safety through various continuous improvement projects (50% decrease in lost time accidents).
-
-
Manufacturing Engineering Manager
-
Mar 2010 - May 2013
Responsible for the manufacturing support department and oversees the application of lean manufacturing principles in company operations including process layouts and flow, fabrication of assembly and test equipment, factory acceptance testing of product, and any coordination with operation or facilities maintenance for physical plant resource issues. Manage an Engineering Team of 10 salaried (7 Manufacturing Engineers, 1 Welding Engineer, and 2 CNC programmers).Develop, evaluate, and improve methods utilizing knowledge of product design, materials and parts, fabrication processes, tooling and production equipment capabilities, assembly methods, and quality control standards.Work concurrently with engineering to develop new products, ensuring that manufacturability and lean thinking is integral to the products’ design. Create and maintain all BOM and routing processes.Analyze and plan work force utilization, space requirements, workflow, and design layout of equipment and workspace for maximum efficiency reducing labor by 20%.Applied advanced knowledge of Geometric Dimensioning and Tolerancing (GD&T) in accordance with ASME Y14.5M:1994 and 2009 to address out of specification parts for third-party vendors.Review and disposition Non Conformance parts daily for both in-house and outsourced parts to determine corrective action.Ensure quality control in accordance with the company ISO-9001:2008 Quality Assurance System. Approve weld procedures to meet DNV or ABS specifications per AWS D1.1, AWS D3.6, ASME Section IX, and API 1104.Evaluated 3 year expansion plan to address production growth and machine capacity limitations.Recommended, managed, and justified capital equipment for CNC horizontal lathes, VTC, HBM and CNC vertical mills, and welding equipment (sub-arc welders, CNC burn table, CNC waterjet, mig/tig weld machines).
-
-
-
Igloo Products Corp.
-
United States
-
Manufacturing
-
400 - 500 Employee
-
Industrial Engineering Manager
-
Aug 2007 - Dec 2009
Provided and administered accurate Engineering cost controls; Developed finish goods cost analysis and lead capital program; Controlled and facilitated timely and within budget new and existing product change implementations. Managed an Engineering Team of 11 salaried (5 Process Engineers, 4 Industrial Engineers, 1 Project Manager, and 1 Packaging Engineer).Maintained all BOM, ECN, and routing process.Optimized equipment utilization, operator productivity, waste reduction, bottlenecks, and efficiency by line balancing.Maintained plant layout and control of shop floor changes and provided facilities maintenance project support.Implemented numerous shop floor and supplier savings projects yielding $600K in yearly savings.Participated in and supported Igloo Lean Sigma program and facilitated the Learning Management System. Developed Standard Work, Visual Management tools, and Value Stream Mapping to eliminate waste.Implemented applications of Poka Yoke systems and Design of Experiments (DOE) for root cause and defect analysis.Managed all equipment upgrades and installation involving the facility.Developed and maintained all machine process parameters for the entire facility.
-
-
Plant Manager
-
Jul 2003 - Aug 2007
Responsible for strategic business planning and maximizing performance results through the implementation of Lean Manufacturing concepts. Managed and coordinated all areas of manufacturing at an 805,000 sq. ft. facility with an operations team of 22 salaried (3 Managers/15 Supervisors/4 Process Engineers) and 450+ hourly employees. Ensured that all 10 flexible cellular assembly lines, 23 extrusion blow molding, 32 injection molding, and 5 thermal forming machines met schedule attainment, sales forecast, ran efficient, safe, and produced a quality product.Responsible for P&L functions of the plant. Managed the department expense budgets and assisted in development of the annual capital and cost savings plan.Worked on 5S practices for house keeping and Total Productive Maintenance (TPM) standardization to reduce safety incidents and the overall operating budgets.
-
-
Assembly Manager
-
May 2003 - Jul 2004
Implemented cellular manufacturing reducing machines and labor requirements yielding $1.3M in savings.Introduced cost control and headcount reduction measures to reduce overtime consumption by 50%, saved more than $150K.
-
-
Injection Mold Manager
-
Mar 2002 - May 2003
Performed scrap reduction Kaizen on liquid color and part weight reduction with $500K of annualized savings.Implemented principles of Six Sigma using the DMAIC approach to develop control strategies to reduce process variation.Optimized equipment utilization, operator productivity, and efficiency by implementing Paulson Training (processing software). Changes helped improved department OEE (Overall Equipment Effectiveness) by 15%.Led SMED (Single Minute Exchange Dies) changeover reduction teams on the shop floor to reduce time by 25% standardizing the procedures and yielding annualized savings of $120K.
-
-
Industrial Engineer II
-
Mar 2000 - Mar 2002
Developed standard operating procedures (SOP), assembly jigs, process standards, quality measures (first part inspection), Kanban systems, and Statistical Process Control (SPC) charting.Planned layout of production departments to maximize operating efficiency and to support new expansion projects.Performed Project Management duties for New Product introduction to the market.Maintain CAD layout of 1.2M ft2 facility.
-
-
-
Toshiba International Corporation
-
United States
-
Appliances, Electrical, and Electronics Manufacturing
-
500 - 600 Employee
-
Manufacturing/Industrial Engineer
-
May 1997 - Mar 2000
Redesigned facility layout and workstation layouts to improve efficiencies. Developed work instruction manuals, set-up and maintained routings for manufactured parts, and developed cost estimates and tooling for new products. Implemented cellular manufacturing and visual control systems to improve productivity with a focus on the Toyota Production System. Introduced wire harness boards for quality and process improvements. Designed fixtures, tooling, and gages at problematic operations creating in-process inspection. (Go-No-Go gages) Provided technical support to the sheet metal shop consisting of CNC punch press, sheer, break press, & welding areas.
-
-
Education
-
Lamar University
Bachelor of Science (B.S.), Industrial Engineering
Community
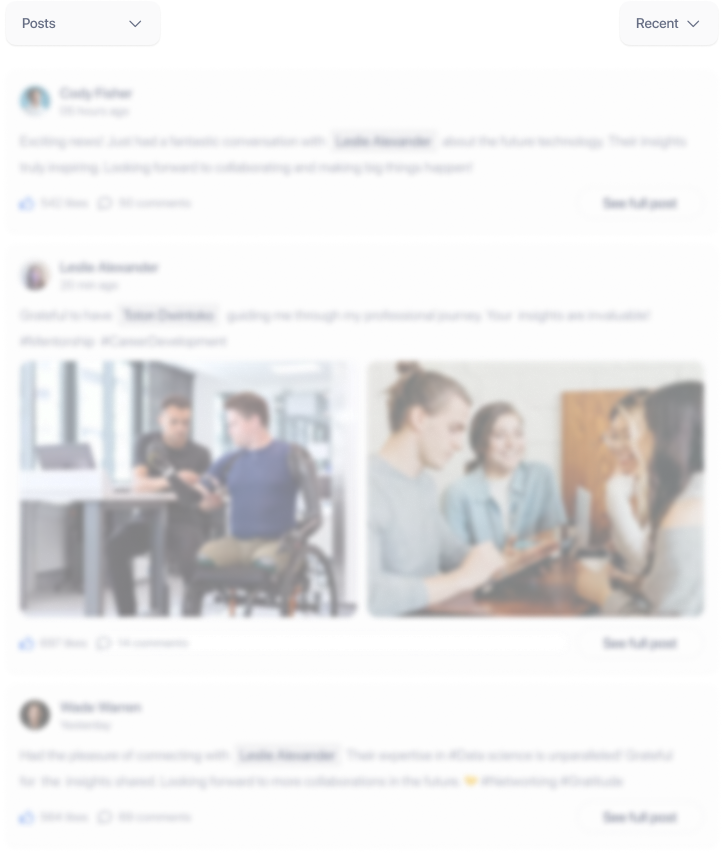