Herbert Gibson
Quality Engineer at Hamlin Electronics- Claim this Profile
Click to upgrade to our gold package
for the full feature experience.
Topline Score
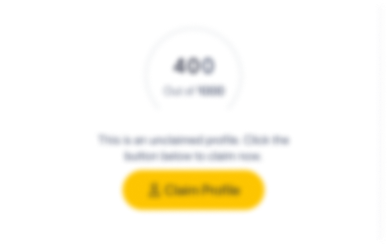
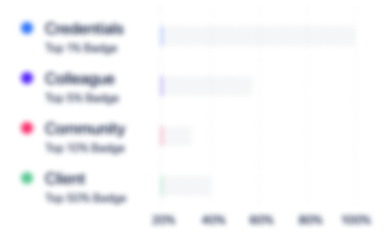
Bio


Experience
-
Hamlin Electronics (Suzhou) Co., Ltd
-
China
-
Appliances, Electrical, and Electronics Manufacturing
-
1 - 100 Employee
-
Quality Engineer
-
Oct 2000 - Present
Responsible for manufacturing, customer and supplier quality issues. • Direct customer quality support to resolve issues and drive customer satisfaction.• Perform teardown and failure analysis of customer returns and production failures.• Direct support to Reed Switch manufacturing floor.• Received internal 6 sigma green belt training.• PPAP submission including Control Plan, Gauge R&R, FMEA’s.• Resolve production, customer and supplier quality issues.• Reduced labor time and increased accuracy of manual counting of modified parts, resulting in $1,000- 2,000 weekly savings.• Tested and debugged production test equipment prior to manufacturing release. • Appointed Interim Quality Manager for 9 months, supervising 7 employees. Performed functions of Quality Manager for 2 years while search for new manager progressed.• Created complete documentation package to support transfer of MDRR-DT switch manufacture from manual labor production site to an automated production facility resulting in reduced production costs.• Internal Auditor – Ensure compliance to TS-16949 and ISO-14000 Standards to maintain certification.• Increased warehouse wire storage space 28% by working with supplier to reduce incoming barrel and shipping crate size.• Improved yield by 10% on assembly machines saving $4,000 per month by analyzing machine production data.
-
-
-
-
Quality Engineer
-
Sep 1996 - Oct 2000
Performed internal systems audits for all plants to QS-9000 standards. Worked with plants to resolve production problems, analyzed customer returned parts ad implement corrective action. Interfaced with sales and engineering to resolve product or internal issues. Assisted international plants in obtaining and maintaining QS-9000 certification. Responsible for maintaining QS-9000 certification for all 8 Wisconsin plants. Performed internal systems audits for all plants to QS-9000 standards. Worked with plants to resolve production problems, analyzed customer returned parts ad implement corrective action. Interfaced with sales and engineering to resolve product or internal issues. Assisted international plants in obtaining and maintaining QS-9000 certification. Responsible for maintaining QS-9000 certification for all 8 Wisconsin plants.
-
-
-
-
Quality / Customer Support Engineer
-
May 1992 - Aug 1996
Responsible for key input commands and software feature additions at customer cellular sites. Analyzed and resolved internal process problems and created/updated procedures to improve product quality for QS-9000. Worked with customers to resolve their software, documentation or operating issues.
-
-
Test Engineer
-
Jun 1989 - Apr 1992
Developed circuit board test fixture hardware and software (HP BASIC) for new cellular and cordless phone product testing. Collaborated with design engineers to increase reliability of board testing and to analyze design and interference problems.
-
-
-
-
Relability Engineer
-
Jun 1984 - May 1989
Performed accelerated life cycle testing on electronic countermeasure equipment to determine failure modes and root cause. Interfaced HP9000 workstation with discrete component test equipment to perform automated component testing. Performed accelerated life cycle testing on electronic countermeasure equipment to determine failure modes and root cause. Interfaced HP9000 workstation with discrete component test equipment to perform automated component testing.
-
-
Education
-
University of Wisconsin-Madison
BSEE, Control Systems
Community
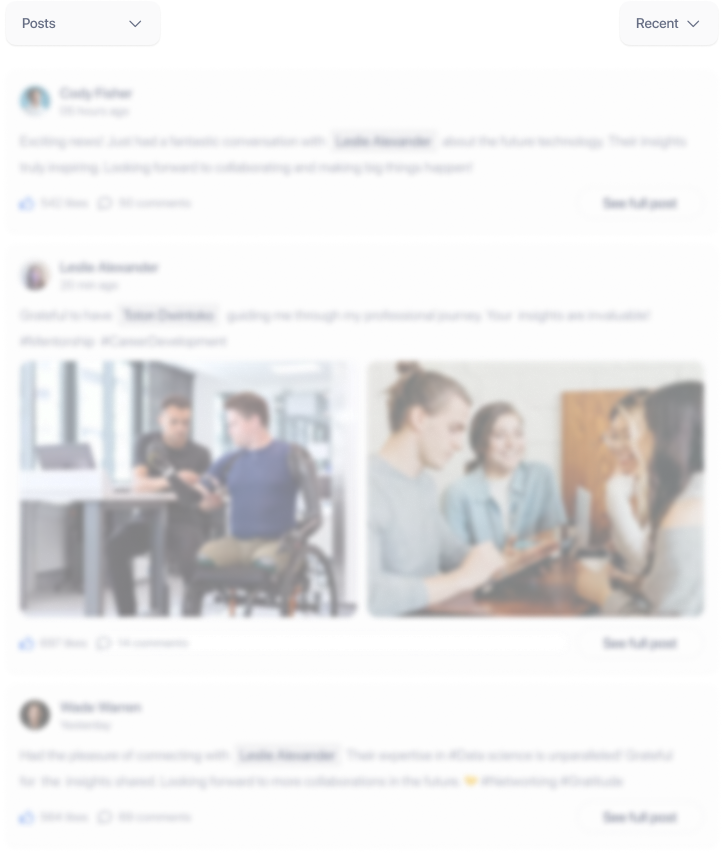