Henry Corporon
Offer Data Manager (Offer Creation) at AMEG Group- Claim this Profile
Click to upgrade to our gold package
for the full feature experience.
Topline Score
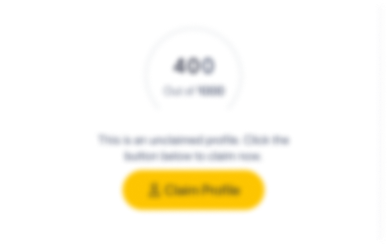
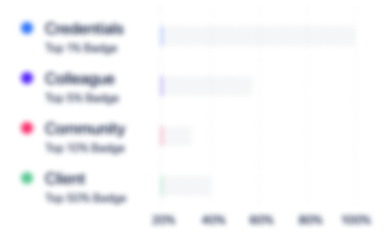
Bio


Experience
-
AMEG GROUP Ingénierie Industrielle
-
France
-
Mechanical Or Industrial Engineering
-
1 - 100 Employee
-
Offer Data Manager (Offer Creation)
-
Jan 2015 - Present
Placing the customer experience at the heart of the project is essential to give meaning and arbitrate the development choices of a product or equipment. Managing the data of an under development product is managing a cross-functional project which requires to: - define the targeted customer experience by type of customer over the entire product life cycle, in all geographical areas covered - define the order flow from the customer to the production plants - formalize the… Show more Placing the customer experience at the heart of the project is essential to give meaning and arbitrate the development choices of a product or equipment. Managing the data of an under development product is managing a cross-functional project which requires to: - define the targeted customer experience by type of customer over the entire product life cycle, in all geographical areas covered - define the order flow from the customer to the production plants - formalize the structure of the offer with Marketing/Product owner by having a customer-oriented approach - share compliance of customer needs with R&D, Industrialization and Logistics - create digital data sets related to the offer (commercial references, technical datasheets, product QR Code, configuration databases, etc.) - test the various digital tools used to configure the products and equipment - ensure the publication of data on websites or in digital tools is made available to customers - enable the quality, accuracy, and relevance of published data The main challenges of this mission entrusted by Schneider Electric are: - work closely with the Marketing/Product Owner function - have an overview of the digital ecosystem made available to customers - consider the complexity of the information systems of a company addressing a global market. It is also an opportunity to practice agile methodologies applied to the development of physical products, within projects punctuated by the same events: Sprint Planning (Post-It™/Kanban), Sprint, Weekly scrum, Review (with stakeholders or with customers), Retrospective. In this context, I was able to be trained in the role of Product Owner. This mission leads me to travel to support the skills development of local teams on digital tools (audit and training).
-
-
Project Manager for Product Technical Publication creation (Offer Creation)
-
Nov 2013 - Jul 2016
The creation of technical or commercial documentation is one of the core businesses of AMEG Group. Several projects have been entrusted to me by Schneider Electric, on offers under development, to make the link with our documentary creation teams. In order to ensure the quality and availability of these documents before the commercial launch of the offers, I coordinated the Marketing, R&D, Industrialization, Quality and Purchasing teams of my client during the creation, proofreading… Show more The creation of technical or commercial documentation is one of the core businesses of AMEG Group. Several projects have been entrusted to me by Schneider Electric, on offers under development, to make the link with our documentary creation teams. In order to ensure the quality and availability of these documents before the commercial launch of the offers, I coordinated the Marketing, R&D, Industrialization, Quality and Purchasing teams of my client during the creation, proofreading and validation cycles. This represents more than a thousand pages of technical literature produced. Some projects have proven to be complex, requiring direct interaction with end users and their subcontractors.
-
-
Project Quality Leader (Offer Creation)
-
Apr 2010 - Apr 2014
This mission was entrusted to me by Schneider Electric, it is also my debuts within a development team of a full product range. Quality was present in all my previous functions and this mission opportunity allowed me to feel to what extent the Quality function represents the " consciousness" of a project. Beyond the guarantee of procedures follow-up and the achievement of quality improvement objectives, it is a question of providing methodological support to each member of the… Show more This mission was entrusted to me by Schneider Electric, it is also my debuts within a development team of a full product range. Quality was present in all my previous functions and this mission opportunity allowed me to feel to what extent the Quality function represents the " consciousness" of a project. Beyond the guarantee of procedures follow-up and the achievement of quality improvement objectives, it is a question of providing methodological support to each member of the project team to progress together towards the realization of customer needs. After validating the production launches in France and Dubai (UAE), I also monitored product quality before transferring the Quality file to the supply management teams.
-
-
Project Manager for Industrial Projects
-
Sep 2006 - Apr 2010
The world of microelectronics opened up to me during this mission proposed by e2v (today Teledyne e2v). The challenge for me was to discover the processes and operating modes specific to the testing of electronic components in order to lay out the associated procedures in the ERP. Beyond a simple update, it was necessary to ensure that the instructions were: - correctly initialized for new products - maintainable and maintained - Used A data analysis phase was… Show more The world of microelectronics opened up to me during this mission proposed by e2v (today Teledyne e2v). The challenge for me was to discover the processes and operating modes specific to the testing of electronic components in order to lay out the associated procedures in the ERP. Beyond a simple update, it was necessary to ensure that the instructions were: - correctly initialized for new products - maintainable and maintained - Used A data analysis phase was necessary before evaluating the ERP itself to facilitate the entry, analysis and provision of information to production. Subsequently, projects for the development of testing and conditioning tools were called upon me. This led me to work with local and international subcontractors and to manage innovative projects, from specifications to production validation.
-
-
-
Algeco France
-
France
-
Construction
-
300 - 400 Employee
-
Technical department manager
-
Jun 2004 - Sep 2006
The industrialized modular construction offers endless design possibilities for buildings. In this technical environment mixing large metal structures and traditional building techniques, I took charge of a team of 5 people dealing with the costing of business and the processing of orders, the reception of the business file from invoicing to material orders and the production of manufacturing plans. In addition to the daily management of the team, actions to improve quality and… Show more The industrialized modular construction offers endless design possibilities for buildings. In this technical environment mixing large metal structures and traditional building techniques, I took charge of a team of 5 people dealing with the costing of business and the processing of orders, the reception of the business file from invoicing to material orders and the production of manufacturing plans. In addition to the daily management of the team, actions to improve quality and control deadlines in the processing of files, I was in charge of the management of special cases (hospitals, prisons, etc.) in connection with the office central study, subcontractors and production teams. I also deepened the functioning of our ERP to structure customer invoicing and tariffs Show less The industrialized modular construction offers endless design possibilities for buildings. In this technical environment mixing large metal structures and traditional building techniques, I took charge of a team of 5 people dealing with the costing of business and the processing of orders, the reception of the business file from invoicing to material orders and the production of manufacturing plans. In addition to the daily management of the team, actions to improve quality and… Show more The industrialized modular construction offers endless design possibilities for buildings. In this technical environment mixing large metal structures and traditional building techniques, I took charge of a team of 5 people dealing with the costing of business and the processing of orders, the reception of the business file from invoicing to material orders and the production of manufacturing plans. In addition to the daily management of the team, actions to improve quality and control deadlines in the processing of files, I was in charge of the management of special cases (hospitals, prisons, etc.) in connection with the office central study, subcontractors and production teams. I also deepened the functioning of our ERP to structure customer invoicing and tariffs Show less
-
-
-
KIS
-
France
-
Retail Office Equipment
-
1 - 100 Employee
-
Methods and Industrialization department manager
-
May 1998 - Oct 2003
One of my best experiences: starting from scratch to set up a Methods department, then taking charge of the upstream Industrialization of products for internal or outsourced manufacturing. A first experience in management, starting with 4 to grow up to 7 people, which was an opportunity to define the industrial operating mode in a high-tech product environment in constant movement: - 1 product introduction every 6 months requiring a complete review of the organization of the 10,000… Show more One of my best experiences: starting from scratch to set up a Methods department, then taking charge of the upstream Industrialization of products for internal or outsourced manufacturing. A first experience in management, starting with 4 to grow up to 7 people, which was an opportunity to define the industrial operating mode in a high-tech product environment in constant movement: - 1 product introduction every 6 months requiring a complete review of the organization of the 10,000 m² of workshop to adapt the load/capacity - the transition from film photography to digital, which prompted us to innovate finding new means of production and testing - the renewal of our ERP, its adaptation to production needs and the implementation of associated procedures… I am also very proud of my team who obtained the congratulations of the ISO9001:2000 auditor during the company's first certification. Show less One of my best experiences: starting from scratch to set up a Methods department, then taking charge of the upstream Industrialization of products for internal or outsourced manufacturing. A first experience in management, starting with 4 to grow up to 7 people, which was an opportunity to define the industrial operating mode in a high-tech product environment in constant movement: - 1 product introduction every 6 months requiring a complete review of the organization of the 10,000… Show more One of my best experiences: starting from scratch to set up a Methods department, then taking charge of the upstream Industrialization of products for internal or outsourced manufacturing. A first experience in management, starting with 4 to grow up to 7 people, which was an opportunity to define the industrial operating mode in a high-tech product environment in constant movement: - 1 product introduction every 6 months requiring a complete review of the organization of the 10,000 m² of workshop to adapt the load/capacity - the transition from film photography to digital, which prompted us to innovate finding new means of production and testing - the renewal of our ERP, its adaptation to production needs and the implementation of associated procedures… I am also very proud of my team who obtained the congratulations of the ISO9001:2000 auditor during the company's first certification. Show less
-
-
-
Schneider Electric
-
France
-
Automation Machinery Manufacturing
-
700 & Above Employee
-
Project Manager - apprenticeship
-
Nov 1994 - Oct 1997
After a Technical University degree (DUT), a year of European university exchange (Erasmus) in England and a specialization, I entered the world of work as apprentice in Schneider Electric while pursuing an engineering course at ECAM Lyon. Quality training, wonderful encounters and strong mentors have enabled me to carry out a variety of projects, including: - an investment in means of production - the implementation of training for production staff - the choice of organization… Show more After a Technical University degree (DUT), a year of European university exchange (Erasmus) in England and a specialization, I entered the world of work as apprentice in Schneider Electric while pursuing an engineering course at ECAM Lyon. Quality training, wonderful encounters and strong mentors have enabled me to carry out a variety of projects, including: - an investment in means of production - the implementation of training for production staff - the choice of organization for the maintenance of industrial resources - the search for a process for decontaminating polluting products Show less After a Technical University degree (DUT), a year of European university exchange (Erasmus) in England and a specialization, I entered the world of work as apprentice in Schneider Electric while pursuing an engineering course at ECAM Lyon. Quality training, wonderful encounters and strong mentors have enabled me to carry out a variety of projects, including: - an investment in means of production - the implementation of training for production staff - the choice of organization… Show more After a Technical University degree (DUT), a year of European university exchange (Erasmus) in England and a specialization, I entered the world of work as apprentice in Schneider Electric while pursuing an engineering course at ECAM Lyon. Quality training, wonderful encounters and strong mentors have enabled me to carry out a variety of projects, including: - an investment in means of production - the implementation of training for production staff - the choice of organization for the maintenance of industrial resources - the search for a process for decontaminating polluting products Show less
-
-
Education
-
ECAM Lyon
Engineer, Mechanical and Manufacturing Process -
Coventry University
Bachelor of Engineering (B.E.), Combined Engineering
Community
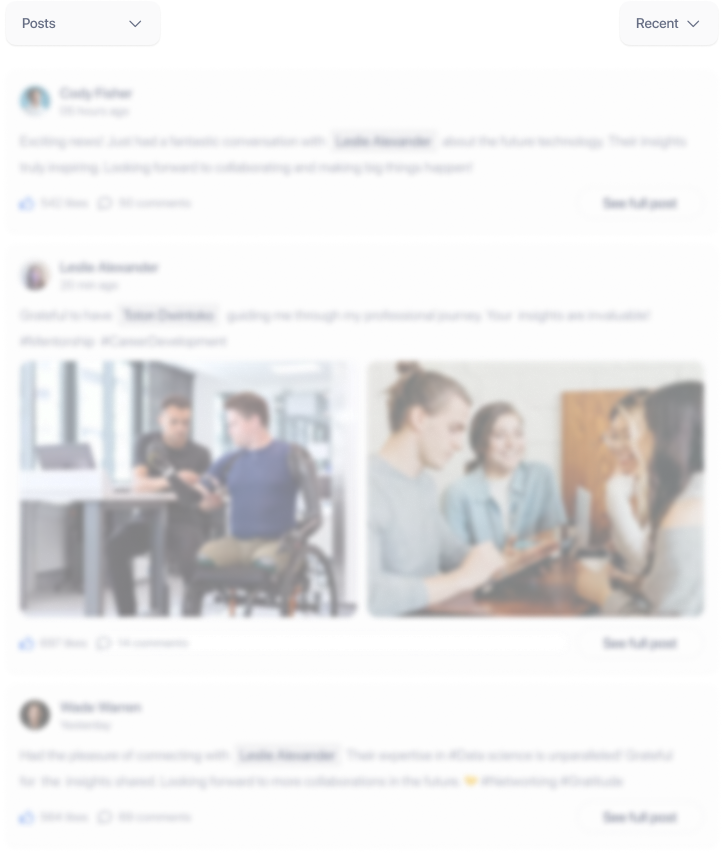