Helario Nyandlale
Business Process Engineer at Rand Mutual - RMA- Claim this Profile
Click to upgrade to our gold package
for the full feature experience.
-
English Professional working proficiency
-
IsiZulu + Various South African Official Languages -
-
Portuguese -
Topline Score
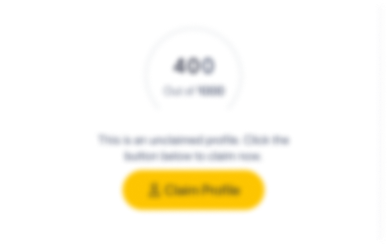
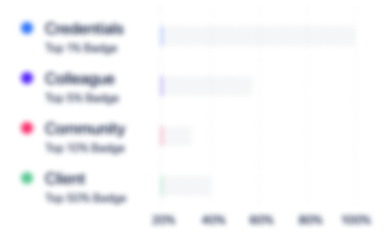
Bio


Credentials
-
Future Leaders Development Program
Wits Business SchoolOct, 2019- Nov, 2024 -
Facilitation Practioner
APMG-InternationalSep, 2014- Nov, 2024 -
Lean Six Sigma Green Belt
The Leadership Centre in conjunction with The Leadership Consulting
Experience
-
Rand Mutual - RMA
-
South Africa
-
Insurance
-
300 - 400 Employee
-
Business Process Engineer
-
Nov 2017 - Present
Lead process improvement initiatives across Business Units, and in conjunction with Business Managers, to deliver efficiencies and benefits to internal and external customers Present findings and recommendations with confidence and communicating these to sponsors and key stakeholders Challenge stakeholders to maximize opportunities from process improvement initiatives Promote and develop a continuous improvement culture across the business Champion the need and benefit by utilizing a structured approach to business process improvement. Identify improvement opportunities and manage improvement requests from the business Coach and support project team members in use of tools and methodologies Document and monitor business processes, business rules, metrics and standard operating procedures as a result of improvement initiatives. Deliver process improvement training to staff Facilitate and provide specialist process improvement advice to business units via targeted workshops to identify and resolve specific issues that are critically impacting business outcomes and require urgent resolution Show less
-
-
-
PPS
-
South Africa
-
Insurance
-
700 & Above Employee
-
Senior Business Process Specialist
-
Jul 2017 - Oct 2017
• Conduct internal process audits according to the defined schedule and implement Preventative Actions based on the outcomes of the TCF feedback framework. • Facilitate workshops with all business areas to challenge, design, document and maintain business processes including process Maps and Work Instructions in the Process Control Manual • On-going liaison with staff and management within the organization to identify potential process improvements and implement the agreed solutions. This includes special projects. • On-going transfer of skill to users for all documented processes through training and accreditation. • Provide first line technical support to users in the business processes. This includes enlivening after hours and weekends. • Provide organizational support by testing new or improved line of business systems and ensuring that a full impact analysis is conducted on business processes with the goal to ensuring that work is conducted in the most effective and efficient manner supporting business objectives. • Conduct business process improvement initiatives aimed at improving efficiencies and effectiveness of operations, by liaising and advising managers. • Identify the scope (core and sub–processes) and life cycle of business processes within area of responsibility. • Ensure that processes and procedures as well as system designs are integrated into a single business solution. • Apply scientific principles and business inputs to refine and re-engineer as-is business process into best scenario to-be processes to enhance customer experience and profitability. • Facilitate and integrate process designs, improvements and maintenance amongst role-players and effectively network with all stakeholders. • Conduct pro-active detection of process bottle-necks and high level operational value chain. • Act as coach to business and other process custodians regarding process re-engineering and improvement methodologies and principles. Show less
-
-
-
Absa Group
-
South Africa
-
Financial Services
-
700 & Above Employee
-
Lean Consultant | Industrial Engineer
-
Aug 2013 - Jul 2017
Conduct business process improvement initiatives aimed at improving efficiencies and effectiveness of operations by liaising and advising managers Identify the scope and life cycle of business processes within area of responsibility taking into account the Absa standards Ensure that processes and procedures as well as systems design are integrated into a single business solution Apply scientific and business inputs to refine and re-engineer as-is business process as well as newly to-be refined processes into best scenario to-be processes Facilitate and integrate process designs, improvements and maintenance amongst role-players and effectively network with all stakeholders Apply various applicable Industrial and System Engineering principles in process constraints and opportunity identifications as well as solutioning Define process performance criteria and requirements in terms of time, cost, resources Act as a coach to line managers and other process custodians regarding process re-engineering and improvement methodologies and principles Perform business impact analysis Liaison with line managers on changes that is imposed on current operational environment Apply basic and advances methodologies to identify bottom line and economic profit enhancement opportunities, where it relates to cost efficiencies or income enhancements Deliver project objectives to achieve desired quality and impact within time period planned and within approved budget Manage and co-ordinate implementation of enhancement efforts and change initiatives Interact and attend meetings to ensure major change and small enhancement impacts are pro-actively identified Provide input to and test policy and procedural manuals, job aids and quick references to ensure logic and support to the changes Show less
-
-
-
Franklin Electric
-
United States
-
Appliances, Electrical, and Electronics Manufacturing
-
700 & Above Employee
-
Industrial Engineer
-
Apr 2013 - Aug 2013
Report directly to Industrial Engineering Manager. Apply statistical methods and perform mathematical calculations to determine manufacturing processes, staff requirements, and production standards. Coordinate Quality Control objectives and activities to resolve production problems, maximize product reliability, and minimize costs. Confer with vendors, staff, and management personnel regarding purchases, procedures, product specifications, manufacturing capabilities, and project status. Draft and design layout of equipment, materials, and workspace to illustrate maximum efficiency, using drafting tools and a computer. Review production schedules, engineering specifications, orders, and related information to obtain knowledge of manufacturing methods, procedures, and activities. Communicate with personnel and user personnel to develop production and design standards. Estimate production cost and effect of product design changes for management review, action, and control. Record or oversee the recording of information to ensure currency of engineering drawings and documentation of production problems. Study operations sequence, material flow, functional statements, organization charts, and project information to determine worker functions and responsibilities. Develop manufacturing methods, labour utilization standards, and cost analysis systems to promote efficient staff and facility utilization. Recommend methods for improving utilization of personnel, material, and utilities. Plan and establish sequence of operations to fabricate and assemble parts or products and to promote efficient utilization. Complete production reports, purchase orders, and material, tool, and equipment lists. Regulate and alter workflow schedules according to established manufacturing sequences and lead times to expedite production operations. Reason for leaving: Head hunted at Absa Show less
-
-
-
ACTOM (Pty) Ltd
-
South Africa
-
Appliances, Electrical, and Electronics Manufacturing
-
700 & Above Employee
-
Industrial Engineer
-
Jun 2009 - Mar 2013
Report directly to the Manufacturing Manager. Responsible for performing process capability studies, developing process control plans and performing failure mode & effect analysis (FMEA) functions. Map existing operational layouts, future state value streams and design work cells to optimize equipment and processes to ensure improved efficiency and up-time, in line with operational targets and goals. Perform time and motion studies to determine equipment utilization and capacity requirements, and identify improvement opportunities by using established engineering and problem solving techniques (Lean Manufacturing, Six Sigma, statistical process control (SPC), JIT, KANBAN, KAIZEN, MRP, value stream mapping (VSM) etc.). Develop and implement standard work instructions. Show less
-
-
Education
-
University of Johannesburg
B-tech Industrial Engineering, Manufacturing Engineering, Quality Assurance -
Hulwazi Secondary School
High School, Mathematics and Science
Community
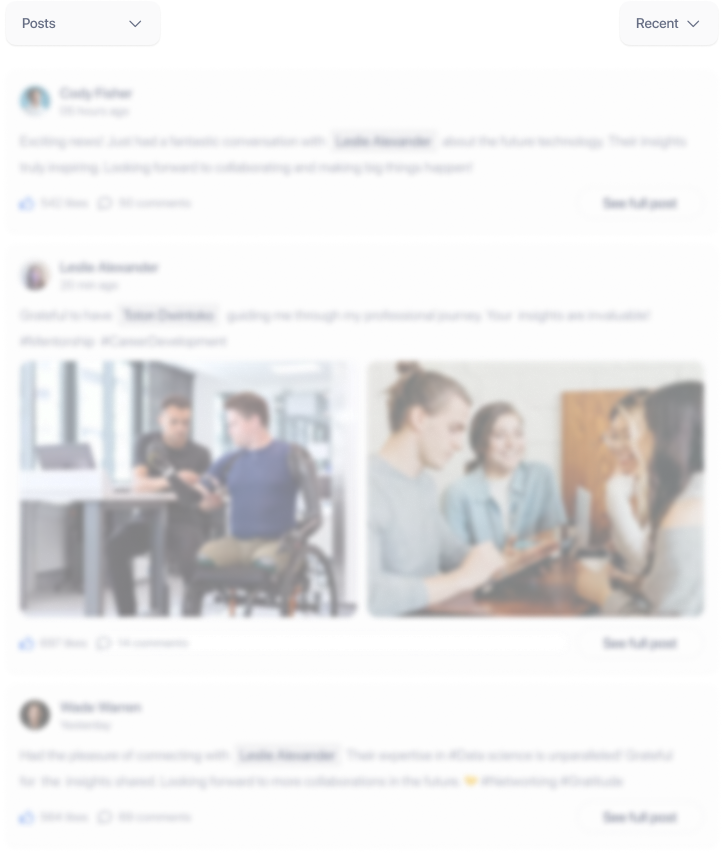