Hector Godina - MBA, CMQ/OE by ASQ
Director of Quality and Operational Excellence at Flogistix, LP- Claim this Profile
Click to upgrade to our gold package
for the full feature experience.
-
English Native or bilingual proficiency
-
Spanish Native or bilingual proficiency
Topline Score
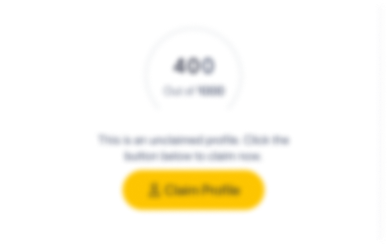
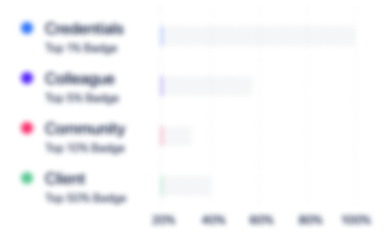
Bio

Michael Theis
Hector Godina and I have been part of Global Quality Management Team at Haldex AB for some years. Hector was taking care of Haldex sites in North and South America in his role as Regional Quality Director. I was holding same postion for EMEA. There have been couple of projects and initiatives we had to take care of in this period of time. Basically it was about introduction of automotive quality tools & methods and to make them standard at Haldex. Hector was always contributing valuable input and was able to share good experience from his previous positions. Relationship was always very good and serious. Hector was specifically pushing installation of a global product audit system and he took the lead to make that a global group standard. Further he delivered best input for set up of a global Cross-functional Quality Review process (CFQR) due to his outstanding knowledge about IATF 16949 and accopanying automotive standards. There have been more projects Hector was involved deeply. Working with Hector was always delivering good value. He has always been professional and did always stand to his commitments. Hector will be an enrichment for any company and quality team.

Ricardo Márquez Rocha
Hell yes! Was the bell ringing in my brain when I was ask to give my recommendation to Hector, I met him 4 years ago, when he was Director of Quality and I was looking for new job and challenges, Hector shares his vision and way to move the organization to improve quality standards and performance, I was convinced and ready to work with him. The way the paradigms were questioned, use of data to make decision, the use of existing know how and the way he coaches our quality engineers creates the perfect environment for continuous improvement. No matter how tense the time, Hector keep the calm and speak from the voice of the data, emotions aside. Any company would be lucky to have Hector as valuable asset

Michael Theis
Hector Godina and I have been part of Global Quality Management Team at Haldex AB for some years. Hector was taking care of Haldex sites in North and South America in his role as Regional Quality Director. I was holding same postion for EMEA. There have been couple of projects and initiatives we had to take care of in this period of time. Basically it was about introduction of automotive quality tools & methods and to make them standard at Haldex. Hector was always contributing valuable input and was able to share good experience from his previous positions. Relationship was always very good and serious. Hector was specifically pushing installation of a global product audit system and he took the lead to make that a global group standard. Further he delivered best input for set up of a global Cross-functional Quality Review process (CFQR) due to his outstanding knowledge about IATF 16949 and accopanying automotive standards. There have been more projects Hector was involved deeply. Working with Hector was always delivering good value. He has always been professional and did always stand to his commitments. Hector will be an enrichment for any company and quality team.

Ricardo Márquez Rocha
Hell yes! Was the bell ringing in my brain when I was ask to give my recommendation to Hector, I met him 4 years ago, when he was Director of Quality and I was looking for new job and challenges, Hector shares his vision and way to move the organization to improve quality standards and performance, I was convinced and ready to work with him. The way the paradigms were questioned, use of data to make decision, the use of existing know how and the way he coaches our quality engineers creates the perfect environment for continuous improvement. No matter how tense the time, Hector keep the calm and speak from the voice of the data, emotions aside. Any company would be lucky to have Hector as valuable asset

Michael Theis
Hector Godina and I have been part of Global Quality Management Team at Haldex AB for some years. Hector was taking care of Haldex sites in North and South America in his role as Regional Quality Director. I was holding same postion for EMEA. There have been couple of projects and initiatives we had to take care of in this period of time. Basically it was about introduction of automotive quality tools & methods and to make them standard at Haldex. Hector was always contributing valuable input and was able to share good experience from his previous positions. Relationship was always very good and serious. Hector was specifically pushing installation of a global product audit system and he took the lead to make that a global group standard. Further he delivered best input for set up of a global Cross-functional Quality Review process (CFQR) due to his outstanding knowledge about IATF 16949 and accopanying automotive standards. There have been more projects Hector was involved deeply. Working with Hector was always delivering good value. He has always been professional and did always stand to his commitments. Hector will be an enrichment for any company and quality team.

Ricardo Márquez Rocha
Hell yes! Was the bell ringing in my brain when I was ask to give my recommendation to Hector, I met him 4 years ago, when he was Director of Quality and I was looking for new job and challenges, Hector shares his vision and way to move the organization to improve quality standards and performance, I was convinced and ready to work with him. The way the paradigms were questioned, use of data to make decision, the use of existing know how and the way he coaches our quality engineers creates the perfect environment for continuous improvement. No matter how tense the time, Hector keep the calm and speak from the voice of the data, emotions aside. Any company would be lucky to have Hector as valuable asset

Michael Theis
Hector Godina and I have been part of Global Quality Management Team at Haldex AB for some years. Hector was taking care of Haldex sites in North and South America in his role as Regional Quality Director. I was holding same postion for EMEA. There have been couple of projects and initiatives we had to take care of in this period of time. Basically it was about introduction of automotive quality tools & methods and to make them standard at Haldex. Hector was always contributing valuable input and was able to share good experience from his previous positions. Relationship was always very good and serious. Hector was specifically pushing installation of a global product audit system and he took the lead to make that a global group standard. Further he delivered best input for set up of a global Cross-functional Quality Review process (CFQR) due to his outstanding knowledge about IATF 16949 and accopanying automotive standards. There have been more projects Hector was involved deeply. Working with Hector was always delivering good value. He has always been professional and did always stand to his commitments. Hector will be an enrichment for any company and quality team.

Ricardo Márquez Rocha
Hell yes! Was the bell ringing in my brain when I was ask to give my recommendation to Hector, I met him 4 years ago, when he was Director of Quality and I was looking for new job and challenges, Hector shares his vision and way to move the organization to improve quality standards and performance, I was convinced and ready to work with him. The way the paradigms were questioned, use of data to make decision, the use of existing know how and the way he coaches our quality engineers creates the perfect environment for continuous improvement. No matter how tense the time, Hector keep the calm and speak from the voice of the data, emotions aside. Any company would be lucky to have Hector as valuable asset

Credentials
-
Data Science Foundations: Fundamentals
LinkedInJun, 2020- Nov, 2024 -
Exemplar Global-Certified ISO 9001:2015 Lead Auditor Training with AIAG IATF 16949:2016 Supplier Auditor Certification
Plexus InternationalMay, 2018- Nov, 2024 -
ASQ - Certified Manager of Quality/Organizational Excellence
ASQMar, 2015- Nov, 2024 -
Certified IATF 16949 Supplier Auditor
AIAG - Automotive Industry Action GroupMay, 2018- Nov, 2024
Experience
-
Flogistix, LP
-
United States
-
Oil and Gas
-
100 - 200 Employee
-
Director of Quality and Operational Excellence
-
Nov 2022 - Present
A leading provider of production optimization and vapor recovery solutions to the domestic onshore oil and gas industry. Flogistix manufactures a large range of gas engine and electric-driven compressors and fluid pump systems and maintains a compressor rental fleet throughout the US. Flogistix’s equipment and services are used to improve production rates, extend the useful life of a well, and increase proven reserves, as well as to reduce emissions and capture valuable vapors that would otherwise be vented or flared. Show less
-
-
-
CFS Brands
-
United States
-
Restaurants
-
100 - 200 Employee
-
Global Director of Quality
-
Nov 2020 - Oct 2022
• Restructured internal resources into a Global Quality organization, delivering agile product development, excellence in manufacturing, and a reliable global supply chain. This organization drove a 40% warranty expense reduction in 2 years, and reduced customer rejects by 55% • Created an Advanced Quality Planning team to partner with the Project Management organization, and manage a 30% increase in product development qualification, improving first-pass approval by 20%. • Integration of Acquisition partners to quality tracking, and collaboration to develop Engineering redesign solutions to address field excursions, with no reoccurrence of 5 targeted projects in the first year. • Created a Supply Quality function to lead supplier qualification for strategic supply chain reshoring projects for significant cost reduction, and resolve order fill backlog. • Ensure compliance to relevant regulation requirements (NSF, UL) for products or equipment food safety, and Plant compliance with Good-Manufacturing-Practices (GMP) and Hazard Analysis and Critical Control Points (HACCP) across the Americas, Europe, and Asia. Show less
-
-
-
Haldex
-
Sweden
-
Motor Vehicle Manufacturing
-
700 & Above Employee
-
Director Of Quality - Americas
-
Oct 2015 - Oct 2020
• Lead Plant Quality teams at 10 operation sites (manufacturing, re-manufacturing and DC's) across US, Mexico and Brazil in matrix organization. • Over 30% reduction in warranty related costs last two fiscal years. • 90% reduction to OEM Customer incoming rejects, main manufacturing sites operating now at <15 PPMs rate. • Flawless launch of key product reintroduction to market with no customer disruptions and/or warranty excursions. • Designed and implemented a proactive product audit process across 7 global manufacturing sites in the Americas, Europe and Asia. Show less
-
-
-
Johnson Controls
-
Ireland
-
Industrial Machinery Manufacturing
-
700 & Above Employee
-
Corporate Regional Quality Manager
-
2007 - 2015
• Led Quality Control teams at 7 Plants in Mexico and US, while executing Corporate Advanced Product Quality Planning (APQP) programs and customer oriented projects. • Qualified new golf cart batteries launch at Mexico Plant using APQP program, obtaining full supply of new customer vehicle line and subsequent Top Supplier Award.• Secured OEM automotive customer approvals on new business/business transfers by hosting audits and fulfilling customer requirements at Mexico and US sites.• Coordinated root cause analysis and problem solving activities reducing product warranty rate in North America, earning a company Merit Award recognition. Show less
-
-
Production Manager
-
2006 - 2007
• Managed supervisors and Plant engineering during “green field” launch, training 300 new employees and processes for 4.9M auto-batteries-year operation at Yuma, AZ.
-
-
Operations Area Manager
-
2004 - 2006
• Managed ramp down of operations at Fullerton, CA Plant for shutdown and operations prior move to Yuma, AZ without customer delivery interruptions, maintaining safety/quality/productivity goals.• Drove efficiency teams execution to gain 15% productivity, and beat conversion cost vs budget in last two fiscal years of operation at Fullerton CA operation.
-
-
Plant Manager for Quality and Continuous Improvement
-
2001 - 2004
• Member of Management team introducing Six Sigma to Johnson Controls operations, coaching Black Belts in project selection and removing barriers for successful project completion and certification.• Restructure of Plant Quality Department, recruiting and training Plant Quality Engineers for effective department function.
-
-
Corporate Quality Engineer
-
1999 - 2001
• JV process auditor, to close gaps in manufacturing processes controls and acceptance criteria with JV partner, qualifying operations for NA market specifications, enabling new $130M USD business.• Acquisition due diligence manufacturing audit at acquisition target with Absorbent Glass Material (AGM) technology, strategic to enter the start-stop automotive-battery market niche.• Led Corporate process compliance audits of lead-acid battery manufacturing processes at Johnson Controls sites, as part of Corporate project to reduce scrap, warranty and improve product electrical compliance. Show less
-
-
Quality Systems Engineer
-
1997 - 1999
• Implementation and training of Statistical Process Control software -GageTalker at shopfloor• Maintenance of Plant QS-9000 certfication• OEM Plant representative for customer claims
-
-
Education
-
California State University-Long Beach
Master of Business Administration -
UNIVERSIDAD IBEROAMERICANA TORREÓN
Bachelor of Science, Industrial Engineering
Community
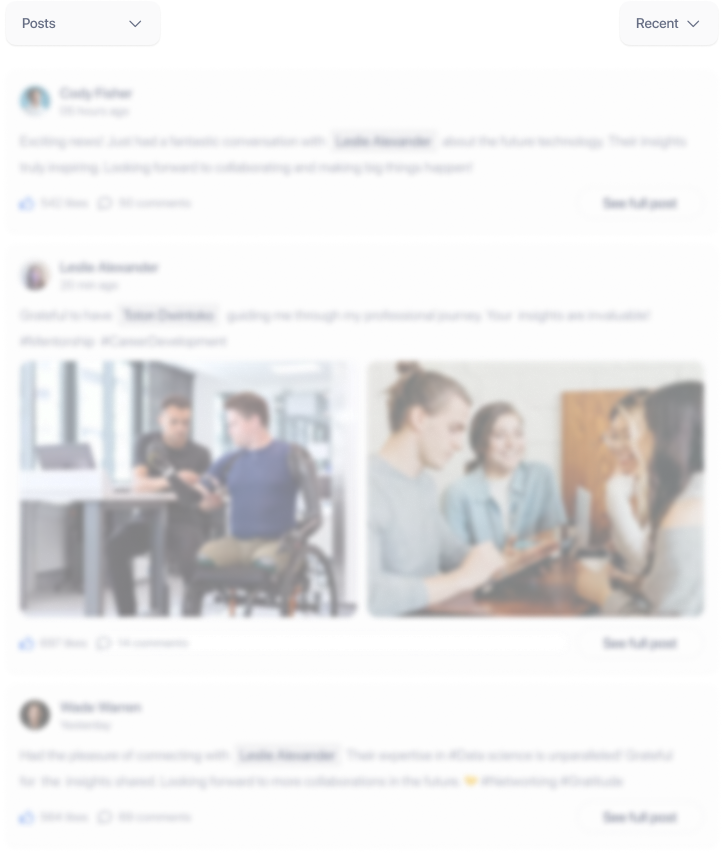