Heath Stephenson
Head of Engineering at Nooshee- Claim this Profile
Click to upgrade to our gold package
for the full feature experience.
-
Mandarin Chinese Elementary proficiency
Topline Score
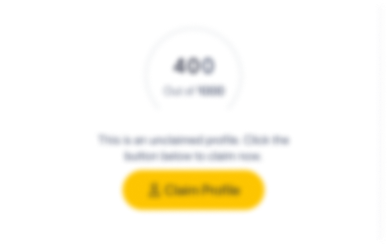
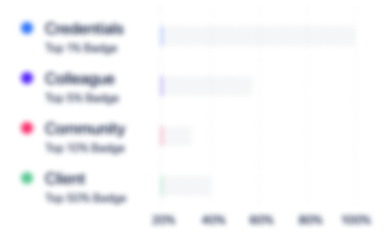
Bio

Jonathan Wilks (CEng MIMechE)
Heath is a very competent automotive engineer and it is a pleasure to work with him. He frequently demonstrates his expertise in CAD and always delivers his work to the highest quality. He would be a great asset to any organisation he is apart of.

Michaela Tod
Heath ran the Quality and Reliability team for China when I was President for the China and then the Greater China Region. When he joined, the quality and reliability function was not very developed. He stepped in and built it up from scratch. He led the quality team in numerous critical reworks that ranged from product reworks to PLGM corrections - all essential to not fall foul of regulations. He is a great problem solver and has always responded extremely quickly to issues at hand. Nothing seemed impossible to him, he simply took each issue, broke it down into constituent parts and then calmly set about resolving it. He used each project to define and improve processes so we became more efficient over time. Importantly, he built strong strong safety processes with early warning systems and fast evaluations by RDD to keep our customers as safe as can be. Lastly Heath has strong values and a great personality - collaborative, solutions focused and very straight.

Jonathan Wilks (CEng MIMechE)
Heath is a very competent automotive engineer and it is a pleasure to work with him. He frequently demonstrates his expertise in CAD and always delivers his work to the highest quality. He would be a great asset to any organisation he is apart of.

Michaela Tod
Heath ran the Quality and Reliability team for China when I was President for the China and then the Greater China Region. When he joined, the quality and reliability function was not very developed. He stepped in and built it up from scratch. He led the quality team in numerous critical reworks that ranged from product reworks to PLGM corrections - all essential to not fall foul of regulations. He is a great problem solver and has always responded extremely quickly to issues at hand. Nothing seemed impossible to him, he simply took each issue, broke it down into constituent parts and then calmly set about resolving it. He used each project to define and improve processes so we became more efficient over time. Importantly, he built strong strong safety processes with early warning systems and fast evaluations by RDD to keep our customers as safe as can be. Lastly Heath has strong values and a great personality - collaborative, solutions focused and very straight.

Jonathan Wilks (CEng MIMechE)
Heath is a very competent automotive engineer and it is a pleasure to work with him. He frequently demonstrates his expertise in CAD and always delivers his work to the highest quality. He would be a great asset to any organisation he is apart of.

Michaela Tod
Heath ran the Quality and Reliability team for China when I was President for the China and then the Greater China Region. When he joined, the quality and reliability function was not very developed. He stepped in and built it up from scratch. He led the quality team in numerous critical reworks that ranged from product reworks to PLGM corrections - all essential to not fall foul of regulations. He is a great problem solver and has always responded extremely quickly to issues at hand. Nothing seemed impossible to him, he simply took each issue, broke it down into constituent parts and then calmly set about resolving it. He used each project to define and improve processes so we became more efficient over time. Importantly, he built strong strong safety processes with early warning systems and fast evaluations by RDD to keep our customers as safe as can be. Lastly Heath has strong values and a great personality - collaborative, solutions focused and very straight.

Jonathan Wilks (CEng MIMechE)
Heath is a very competent automotive engineer and it is a pleasure to work with him. He frequently demonstrates his expertise in CAD and always delivers his work to the highest quality. He would be a great asset to any organisation he is apart of.

Michaela Tod
Heath ran the Quality and Reliability team for China when I was President for the China and then the Greater China Region. When he joined, the quality and reliability function was not very developed. He stepped in and built it up from scratch. He led the quality team in numerous critical reworks that ranged from product reworks to PLGM corrections - all essential to not fall foul of regulations. He is a great problem solver and has always responded extremely quickly to issues at hand. Nothing seemed impossible to him, he simply took each issue, broke it down into constituent parts and then calmly set about resolving it. He used each project to define and improve processes so we became more efficient over time. Importantly, he built strong strong safety processes with early warning systems and fast evaluations by RDD to keep our customers as safe as can be. Lastly Heath has strong values and a great personality - collaborative, solutions focused and very straight.

Experience
-
Nooshee
-
United States
-
Retail Health and Personal Care Products
-
1 - 100 Employee
-
Head of Engineering
-
Jan 2023 - Present
-
-
-
-
Director
-
Sep 2022 - Present
-
-
-
Arrival
-
United States
-
Advertising Services
-
Design Engineer
-
Aug 2021 - Sep 2022
-
-
-
Elvie
-
Australia
-
Retail
-
Senior Design Engineer
-
Jan 2021 - Aug 2021
-
-
Design Engineer - Continuous Improvement
-
Feb 2020 - Dec 2020
-
-
-
Dyson
-
Household Appliance Manufacturing
-
1 - 100 Employee
-
Design Engineer - Advanced (Automotive)
-
Feb 2019 - Jan 2020
In February 2019, I moved to Dyson Automotive and took up a role in the HVAC team. Initially, my responsibilities were for the design of the Air Handling Unit selection flaps but these quickly increased to include all interfaces to the airflow ducts. I took a strong position in helping to define the exterior shape of the AHU in order to meet specification requirements and to mitigate part to part packaging clashes with other teams.
-
-
Design Engineer - Advanced (Project Management Secondment)
-
Jul 2018 - Feb 2019
Following my time in China, I worked on a number of projects in Quality before being seconded as a Project Manager to support the creation of the Product Development Processes in Dyson. This required a comprehensive understanding of the end to end product development process and Qualities role within it. Following some success in this role, I was asked to take on an additional project helping to map out the system engineering requirements for the Dyson EV. Here I worked with the various Product Module Sub Teams to help map out the different requirement levels and report on the progress to the department heads. Show less
-
-
Design Engineer - Advanced (Secondment to China)
-
Jul 2017 - Jul 2018
Whilst on secondment, I was tasked with bringing group practices to the China Quality Team. In addition to my normal role, I frequently led time/sales sensitive activities as required by the market or at the request of the management team. These included numerous reworks and kitting activities, all of which were completed with no effect on sales. As part of this and my normal duties, I was required to report to the local exec team on a regular basis regarding in-market quality activities. One notable activity during my time in China was an EOY refurb to support a sales drive. I was responsible for all aspects of the project and despite the tight time scales and legal restrictions; we managed to screen 13k stock, returning 4k saleable products. Show less
-
-
Design Engineer
-
Nov 2014 - Jun 2017
Whilst working in the Quality Department, I was responsible for identifying product issues and trends using a range of data analyses techniques, physical inspections and tear downs. Identified faults were tested to confirm the failure mode and reported back to the Continuous Improvement teams. As a result of my work, I would often be required to rectify issues in market through mitigation activities or full-scale reworks. At all times, I was looking for ways to improve the efficiency of what I was doing through better collaboration and improving the tools and processes involved. Show less
-
-
-
AESSEAL
-
United Kingdom
-
Industrial Machinery Manufacturing
-
400 - 500 Employee
-
Product Development Engineer
-
Aug 2011 - Nov 2014
After being hired out of New Designers into a Fast Track Program, I was responsible for designing, validating and patenting products for the sealing industry. In two cases I oversaw the initial production runs of my products at the factories in India and presented directly to customers and at events. One key project was to rationalize and create the CAD for over 1000 product assemblies. I achieved this by automating all the designs using parametric models and linked spreadsheets. This allowed us to generate all the CAD data, including engineering drawings, automatically. Show less
-
-
-
BMW
-
Motor Vehicle Manufacturing
-
1 - 100 Employee
-
Visualisation Intern
-
Sep 2009 - Aug 2010
During my year long internship with BMW in their design offices in Munich, I was responsible for the creation of digital imagery for internal design guides, review presentations and press pictures. In these areas I worked on the 1 & 6 series as well as the i3 EV. Notably, the imagery I created for the 6 series was used in the 2011 Geneva Motor Show. During my year long internship with BMW in their design offices in Munich, I was responsible for the creation of digital imagery for internal design guides, review presentations and press pictures. In these areas I worked on the 1 & 6 series as well as the i3 EV. Notably, the imagery I created for the 6 series was used in the 2011 Geneva Motor Show.
-
-
Education
-
De Montfort University
BSc, Industrial Design -
Wycliffe College
Community
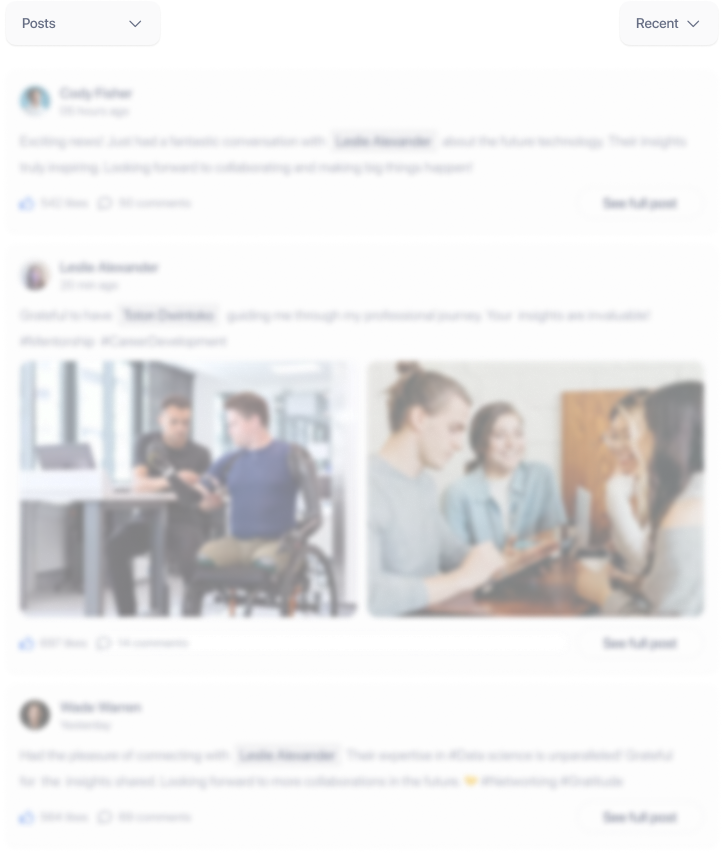