Heather S.
Director of Manufacturing at Terran Orbital Corporation- Claim this Profile
Click to upgrade to our gold package
for the full feature experience.
Topline Score
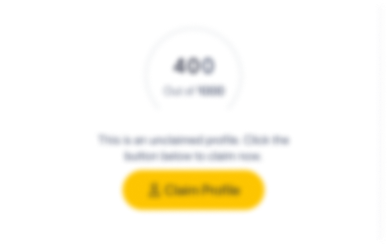
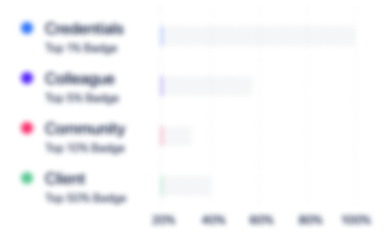
Bio


Experience
-
Terran Orbital Corporation
-
United States
-
Defense and Space Manufacturing
-
300 - 400 Employee
-
Director of Manufacturing
-
Aug 2023 - Present
-
-
-
NBCUniversal
-
United States
-
Entertainment Providers
-
700 & Above Employee
-
Sr Director of Facilities Operations and Engineering
-
Oct 2020 - Aug 2023
-Manage 15 MEP+ Foreman and Managers covering 400 acre lot -Develop CAPEX projects for Studio Lot -Develop and implement continuous improvement processes -Manage Facilities P&L budget -Develop KPI metrics and tracking mechanisms -IFMA Facility Management Professional -Manage 15 MEP+ Foreman and Managers covering 400 acre lot -Develop CAPEX projects for Studio Lot -Develop and implement continuous improvement processes -Manage Facilities P&L budget -Develop KPI metrics and tracking mechanisms -IFMA Facility Management Professional
-
-
-
ADC Aerospace
-
United States
-
Aviation and Aerospace Component Manufacturing
-
1 - 100 Employee
-
Director of Facilities and Environmental Health Safety
-
Jul 2020 - Sep 2020
-
-
Director of Engineering
-
Sep 2018 - Jul 2020
- Manage Engineering Design and Manufacturing, Maintenance, Tooling, and Facilities department- Responsible for the preventative maintenance program and upkeep of 200 pieces of equipment in addition to overall building and grounds maintenance- Manage over 2 million in CAPEX projects, planning, delegating, implementing, and tracking results- Develop processes and implementing structure to improve departments efficiency and flexibility
-
-
-
Milgard Windows and Doors
-
Building Materials
-
700 & Above Employee
-
Continuous Improvement Manager
-
Jun 2017 - Sep 2018
-
-
-
FallTech
-
United States
-
Construction
-
1 - 100 Employee
-
Manufacturing Engineer
-
Oct 2015 - May 2017
-Safety lead - develop and implement new safety procedures; manage safety committee tasks and progress -Develop standardized work -Restructure manufacturing floor to optimize production efficiency resulting in 5% head count reduction -Develop and implement 5S process -Develop and implement Kanban for 50% of production parts -Assist in new ERP development and implementation -Continuously improving material layout and processes within the cell -Coach staff and team members lean techniques in all aspects of the business Show less
-
-
-
General Motors
-
United States
-
Motor Vehicle Manufacturing
-
700 & Above Employee
-
Training Coordinator
-
Jan 2013 - Oct 2015
-Develop, track, and validate Safety, GMS, Launch, Contractual, Leadership and Quality Network training schedules for approximately 1,600 employees -Develop, track, and execute launch training for all new models-Obtained $215,000 in grant money for skilled trades training-Facilitate weekly Key 4 and Quality Council meetings with the plant staff-Manage and execute monthly diversity initiatives including weekly newsletter articles and charitable events-Coordinate and execute all plant joint activities with UAW partners including training, launches, charitable events and employee appreciation activities-Backup for HR Personnel (Labor, Safety, etc.) Show less
-
-
Ergonomist and Industrial Engineer
-
Apr 2011 - Apr 2013
-Ergonomist for both Detroit Hamtramck and the Brownstown Battery Plant-Responded to and analyzed all Quick Response Processes within 48 hours of receipt (received up to 3 a day)-Closed out all Ergo issues within plant control within 3 months-Maintained 0 Red Ergonomic issues within plant control-Successfully implemented several rerates, changeovers, and new product launches for the production Quality department-Consistently worked with management and production to encourage teamwork, incorporate new ideas and develop best practices Show less
-
-
Industrial Engineer
-
Sep 2008 - Apr 2011
-Managed 7 areas consisting of 150 operations-Assisted in line balancing and operation layout for the Chevrolet Volt-Achieved a 36% reduction, increased minutes/hour and percent value added through implementation of lean practices, surpassing the 33% requirement-Analyzed efficiency of manufacturing operations and assisted in developing proper methods and optimum operation layout-Consistently worked with management and production to encourage teamwork, incorporate new ideas, and develop best practices Show less
-
-
Industrial Engineer
-
Jun 2007 - Sep 2008
-Managed 2 areas consisting of 73 operations-Responsible for a 20% productivity head count reduction and achieved a 20% reduction through implementation of lean practices-Successfully implemented 90% of the 2009 model changeover; introduced 5 new engines with additional content without increasing the number of operators-Conducted two continuous improvement workshops with management and production-Increased efficiency of manufacturing operations and layouts
-
-
Education
-
University of Michigan
MSE, Industrial Engineering -
University of Michigan
BSE, Industrial Engineering
Community
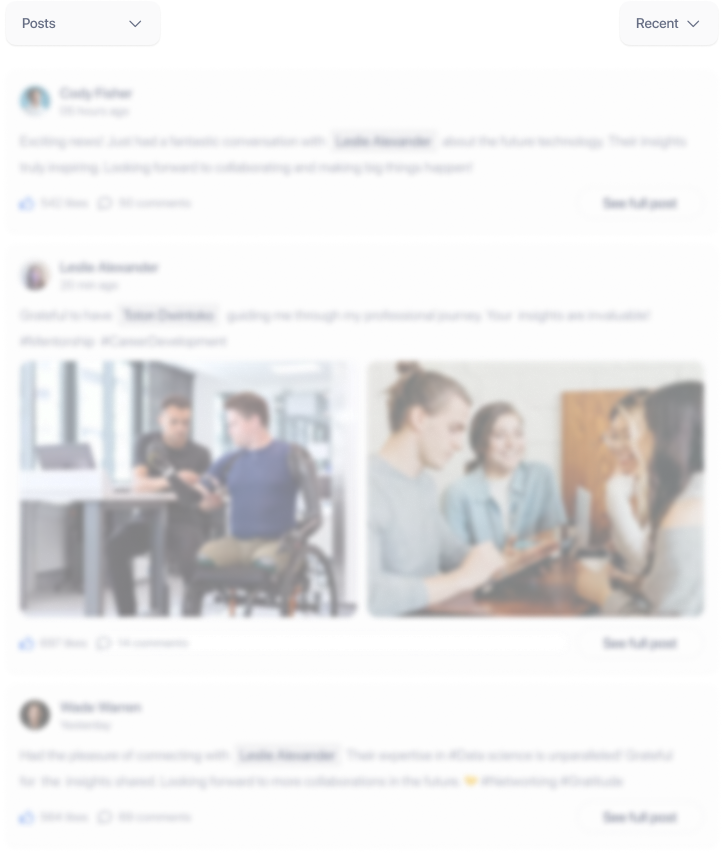