
Harold Lambert
Process Developer at Inter IKEA Systems B.V.- Claim this Profile
Click to upgrade to our gold package
for the full feature experience.
Topline Score
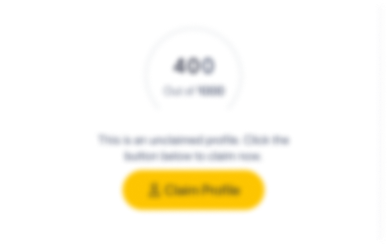
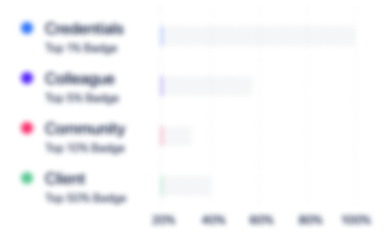
Bio


Experience
-
Inter IKEA Systems B.V.
-
Netherlands
-
Investment Management
-
100 - 200 Employee
-
Process Developer
-
Feb 2021 - Present
-
-
-
IKEA
-
Netherlands
-
Retail
-
700 & Above Employee
-
Distribution Services System Manager
-
Jul 2018 - Jun 2021
Supporting the growing Business with the various system solutions that are integrated to complete the supply chain for Store Distribution and Customer Distribution as well as supporting the introduction of automation into the retail store Supporting the growing Business with the various system solutions that are integrated to complete the supply chain for Store Distribution and Customer Distribution as well as supporting the introduction of automation into the retail store
-
-
-
-
In-Warehouse Logistics Manager
-
Apr 2014 - 2018
. During the time as Logistics Manager I opened 7 CDC's, and worked on the project teams to integrate an automated shuttle system into the customer distribution business as well as participated in the design process of one of IKEA's newest automated building in Joliet, Il. I have supported the North American Organization in performing data analysis to support supply chain matrix changes and moving more of the range closer to the customer resulting in a shorter lead-time and reduced safety stock. I also have analyzed the business inside the 4 walls of a building and determine the best location inside the warehouse for stock to be slotted resulting in the maximum efficiency as well as the best location type to store the goods.
-
-
In-Warehouse Logistics Coordinator
-
Sep 2010 - Apr 2014
-
-
Systems Manager
-
Sep 2007 - Sep 2010
As the system manager for Tacoma I am responsible for managing projects related to the Warehouse Management System. My team and I were responsible to successfully opening the building and ongoing release support. Developing and providing training material for all levels of co-workers. I also oversaw projects related to productivity improvements. Some of these were Fluid Loading, Goods Identification, Conventional Transfer location, and increasing door to door movements (X-DOC). Over the last year these projects helped the facility go from a 4.5 to a 7 cube per hour. I have also participated in the Relations group between IKEA and the WMS provider Consafe Logistics.
-
-
Systems Manager
-
Jan 2006 - Sep 2007
This was the same position that I held for GENCO at the Perryville Maryland site. The contract was canceled by IKEA and I transitioned to their management team during the changeover.
-
-
-
GENCO
-
United Kingdom
-
Food and Beverage Manufacturing
-
Administration Manager
-
Aug 2002 - Jan 2006
I supported users and fixed errors with the ASTRO warehouse Management System, GEMINI order management system, and ICC3 personal computer management system. I was directly responsible to the configuration of ASTRO to reflect the changes in the operational plan for the building. Work closely with North America DC Systems Manager to ensure the systems and hardware support the DC, and comply with IKEA and NA guidelines.
-
-
Process Implementation and Startups
-
Nov 1998 - Aug 2002
I Manage projects for implementation of the software for new customers and Upgrades for existing customers. This entails supervision of three supervisors and assisting the systems department in the design process with the customer. Coordinate with the Project Manager on the physical configuration of buildings to accept the hardware and operation. I am also responsible for all P & L categories, and Care concerning the implementation team.
-
-
General Manager Return Center Automotive Customer
-
Jun 1998 - Nov 1998
My responsibilities were to manage and direct the operation of the return center including complete P & L responsibilities, assure attainment of facility production, quality and safety objectives, review and assure accuracy of required production and inventory reports, and provide assistance for the corporate office on special projects as required
-
-
Operations Manager
-
Nov 1995 - Jun 1998
I supervise between 40 to 60 teammates depending on the time of the year. I am responsible for coordinating the work flow between the different sections in the facility and adjusting the workforce to cover the deficient areas. I work closely with the office manger to ensure that orientation and safety training of new teammates occurs within a timely manner. Some of my other responsibilities were coordinating with the corporate systems support department to test modified and new parts of the computer software. Direct the operation of the return center. Assure attainment of facility production, quality and safety objectives. Review and assure accuracy of required production and inventory reports. Provide assistance for the Facility managers on special projects as required. Ability to effectively interact with customers.
-
-
-
Nash Finch Company
-
United States
-
Wholesale
-
400 - 500 Employee
-
Operations Development Specialist
-
Mar 1995 - Nov 1995
I was one person on a team of three. The teams responsibility is to setup, install, and train the employees of a distribution center. The team is to install the Dallas Open System in 12 distribution centers. The Dallas system encompasses directed put-away of receiving, directed replenishment on shipping, a transportation system, and load control. We will also be installing radio frequency in 2 select distribution centers.
-
-
Inventory Control/ System Administrator
-
Mar 1993 - Mar 1995
My responsibilities were to maintain active inventory in the computer system, research problems. As the Dallas System WMS Administrator I was responsible for the training of the employees in regards to the system. Trouble shooting problems and when unable to solve the problem to communicate the problem and all necessary information required from Dallas System Company. It is also my responsibility to follow-up to ensure that the problem was corrected.
-
-
-
B. Green Company
-
United States
-
1 - 100 Employee
-
Stock Controller
-
Sep 1991 - Feb 1993
Inventory control for the following divisions; Frozen, Dairy, Meat, and Ice CreamI performed the same functions for Nash Finch except only for the above mentioned divisions.B.Green’s Military was purchased by Nash Finch in January of 1993. Inventory control for the following divisions; Frozen, Dairy, Meat, and Ice CreamI performed the same functions for Nash Finch except only for the above mentioned divisions.B.Green’s Military was purchased by Nash Finch in January of 1993.
-
-
Education
-
University of Pittsburgh
-
Southern York High School
Community
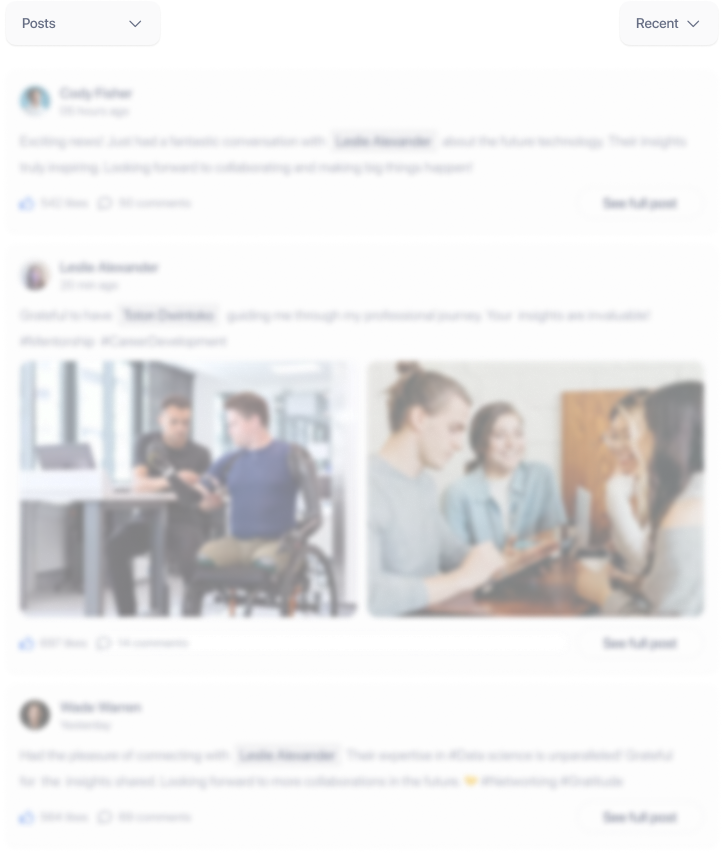