Harald Lang
Director, Global Customer Service Delivery Strategy & Performance Management at Philips Medical Systems DMC GmbH- Claim this Profile
Click to upgrade to our gold package
for the full feature experience.
-
German, English -
Topline Score
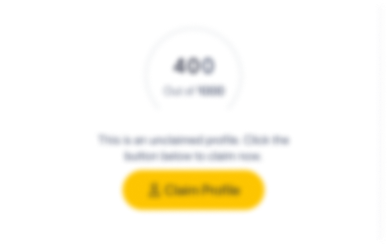
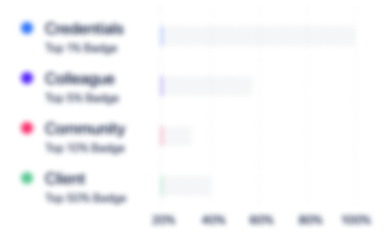
Bio


Credentials
-
EOQ Quality Auditor
- -
EOQ Quality Manager
-
Experience
-
Philips Medical Systems DMC GmbH
-
Germany
-
Medical Equipment Manufacturing
-
100 - 200 Employee
-
Director, Global Customer Service Delivery Strategy & Performance Management
-
Feb 2015 - Present
Leading and managing a global Service Organization to implement effective service delivery strategies within a business - global market structure to ensure consistent high service performance to our worldwide customers. Monitor the implementation in the countries and evaluate delivery performance measures and the customer feedback and continuously improve the business results and the customer experience. Leading and managing a global Service Organization to implement effective service delivery strategies within a business - global market structure to ensure consistent high service performance to our worldwide customers. Monitor the implementation in the countries and evaluate delivery performance measures and the customer feedback and continuously improve the business results and the customer experience.
-
-
-
Philips Healthcare
-
Medical Device
-
100 - 200 Employee
-
Senior Manager Service Supply Chain NA
-
Jul 2008 - Jan 2015
The Customer Service Department serves as the link between Business Units, Global Customer Services and Global Sales and Services. The Life-Cycle Support Center is part of the Service Supply Chain and acts as Service Providcer for Global Customer Service, Global Sales and Service and Operations. The portfolio of Services ranges from Repair, Spare Parts Coordination to Reverse Supply Chain responibilities.
-
-
Program Manager, New Product Introduction
-
Oct 2006 - Jun 2008
Driving new product introduction of OB TraceVue system platform (surveillance, alerting, storage and charting for obstetrical care). Ownership and management of all OB TraceVue related activities in the supply chain. New product introduction (NPI) and current product engineering (CPE) program management. Leader of supply chain cross functional team. Providing cross-functional, cross-program communication, developing and maintaining timelines, plans, issue list, etc. Providing management updates and defines projects and new platforms for continuous improvement of supply chain processes. Liaison between German R&D/ Marketing team and the US supply chain team. Hardware Platform rollover management. Drive improvements in quality, cost, assurance of supply and operational excellence.
-
-
-
DQS Inc.
-
United States
-
Business Consulting and Services
-
1 - 100 Employee
-
DQS Quality Auditor
-
Jan 2001 - Jan 2015
Quality Auditor and notified body for certification of quality management systems per ISO 9000:2000, IS0 13485:2003, German medical product regulation MPG, European Medical Device Directive 93/42/EEC & 90/385/EEC and Canadian Medical Device Requirements CMDCAS. As a Freelancer, 15days per year. Quality Auditor and notified body for certification of quality management systems per ISO 9000:2000, IS0 13485:2003, German medical product regulation MPG, European Medical Device Directive 93/42/EEC & 90/385/EEC and Canadian Medical Device Requirements CMDCAS. As a Freelancer, 15days per year.
-
-
-
-
Program Manager, Supply Chain
-
Jan 2003 - Jun 2005
Transferred to the USA to lead a team to transfer and consolidate patient monitoring manufacturing sites form two locations (USA and Germany) to one centralized location in the USA. Responsible for establish and develop plans including schedule, resource requirements, technical requirements, process development, product data, field factory processes and supplier processes. Lead inventory reduction program to minimize field inventory. Cross-functional team effort between field, logistic, production and engineering departments. Lead development of a business strategy to implement an advanced planning system, define strategy, working with system suppliers, ROI calculation and development of an implementation plan. Lead new product introduction program for an instrument telemetry solution. Coordination and developing consensus among cross-functional engineering teams in Germany and the U.S.
-
-
Project Engineer, Materials
-
Jan 2001 - Dec 2002
SAP Implementation core team member responsible for the materials management module. Process owner for the quality module and side representative in the worldwide project team. Analyze of the manufacturing location in Germany for new strategic products. Global sourcing of potential box build partners, benchmarking and performing a make or buy analyzes. Implementation and realization of a box build strategy and supplier management of these partners. Program management for order related final assembly activities at the customer site. Includes technical feasibility study, cost calculation and set up and management of the assembly sites in different countries (Spain. France, Austria, USA).
-
-
-
Agilent Technologies
-
Biotechnology Research
-
700 & Above Employee
-
Engineer, Production
-
Oct 1999 - Dec 2000
Responsible for product quality and production control of an anesthesia gas monitor. Support the OEM supplier in the USA by any technical changes and issues. Project leader of a production overhead cost reduction program. Project Lead to reduce the customer complaints based on workmanship errors on the production floor. Set up of a cross-functional project team that includes factory, field and service departments in Germany to approve the defoa-process. Responsible for product quality and production control of an anesthesia gas monitor. Support the OEM supplier in the USA by any technical changes and issues. Project leader of a production overhead cost reduction program. Project Lead to reduce the customer complaints based on workmanship errors on the production floor. Set up of a cross-functional project team that includes factory, field and service departments in Germany to approve the defoa-process.
-
-
-
Hewlett Packard
-
United States
-
Information Technology & Services
-
300 - 400 Employee
-
Engineer, Materials Quality
-
Mar 1996 - Sep 1999
Responsible for the materials quality department and supervision of 5 employees. Monitoring the supplier quality of 15000 different purchased parts and 400 different suppliers. Implementation of a computer aided quality management system software to handle the incoming inspection process, nonconforming material handling and return to vendor process total electronically. Outsourcing the operative inspection activities to a logistic provider and responsible for the supplier management of them. Responsible for the materials quality department and supervision of 5 employees. Monitoring the supplier quality of 15000 different purchased parts and 400 different suppliers. Implementation of a computer aided quality management system software to handle the incoming inspection process, nonconforming material handling and return to vendor process total electronically. Outsourcing the operative inspection activities to a logistic provider and responsible for the supplier management of them.
-
-
Education
-
Fachhochschule Ulm - Hochschule für Technik
Dipl. Ing. Medizintechnik, Biotechnology
Community
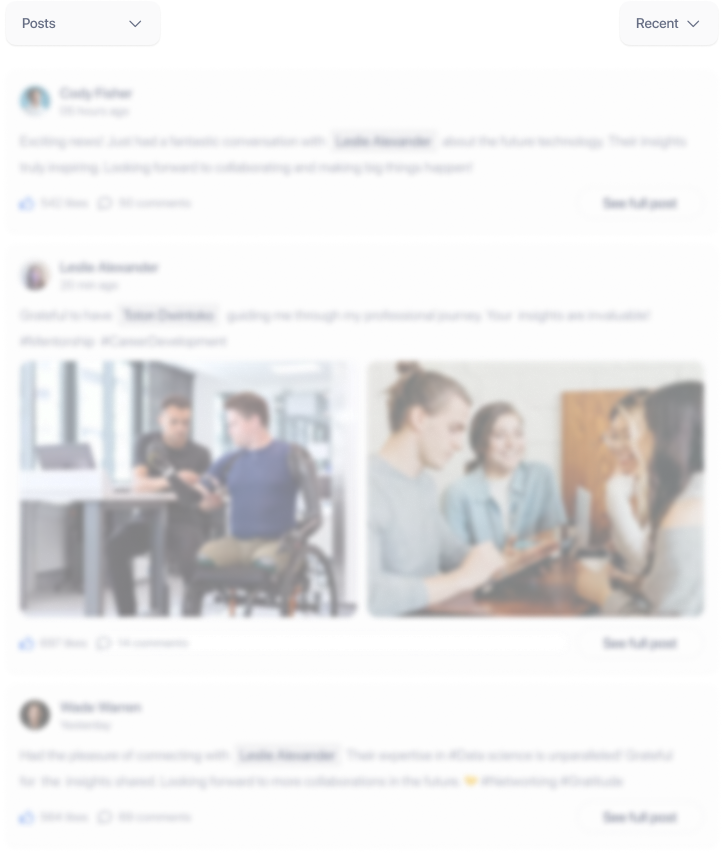