Hannah Thurston-McGowan
Head of Quality at Chemring Countermeasures- Claim this Profile
Click to upgrade to our gold package
for the full feature experience.
Topline Score
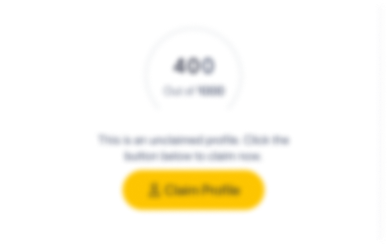
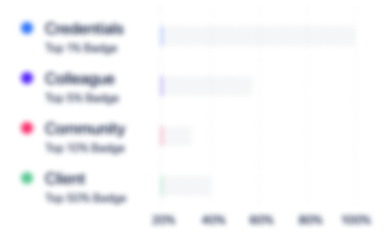
Bio


Experience
-
Chemring Countermeasures
-
United Kingdom
-
Defense & Space
-
100 - 200 Employee
-
Head of Quality
-
Sep 2020 - Present
-
-
-
GSK
-
United Kingdom
-
Pharmaceutical Manufacturing
-
700 & Above Employee
-
Head of Written Standards Transformation
-
Jan 2018 - Aug 2020
Making it easy for employees to find, access, understand and implement the policies and procedures they need.
-
-
Quality Director, Skin Health Category
-
Jul 2015 - Jan 2018
- Champion the GSK Quality message, values and objectives- Reduce negative trends in consumer complaints, recalls and Quality incidents- Lead cultural change to embed Design to Value and Value Engineering within cross-functional teams to ensure robust manufacturing and packaging processes are developed- Represent Quality in strategic-level meetings with R&D and the Commercial business to determine the category pipeline- Represent Quality on the Technical Review Board to challenge the technical diligence of New Product Introduction projects to ensure robust products at launch- Represent Quality in globalization projects for the category. - Ensure product Quality knowledge is available to project teams- Represent Quality at appropriate Network strategy meetings and ensure input to all strategy decisions- Represent Quality in the Due Diligence work of the category, whether selling or buying. Lead and direct trained local support for DD.- Ensure appropriate Quality standards are applied to cosmetic classification products- Lead and direct the Quality activities to deliver compliant, robust and timely New Product Introduction (NPI) launches within the category by; - being the decision-maker for Quality in go/ no go decisions on projects - setting the Quality strategy for each project - coordinating Quality activities between other Quality groups such as auditing teams, R&D Quality and Contract Manufacturing Quality Managers - escalation of issues Show less
-
-
Quality Director, Food/nutrition and Digestive Health Category
-
Mar 2014 - Jul 2015
- Champion the GSK Quality message, values and objectives- Reduce negative trends in consumer complaints, recalls and Quality incidents- Lead cultural change to embed Design to Value and Value Engineering within cross-functional teams to ensure robust manufacturing and packaging processes are developed- Represent Quality in strategic-level meetings with R&D and the Commercial business to determine the category pipeline- Represent Quality on the Technical Review Board to challenge the technical diligence of New Product Introduction projects to ensure robust products at launch- Represent Quality in globalization projects for the category. - Ensure product Quality knowledge is available to project teams- Represent Quality at appropriate Network strategy meetings and ensure input to all strategy decisions- Represent Quality in the Due Diligence work of the category, whether selling or buying. Lead and direct trained local support for DD.- Ensure appropriate Quality standards are applied to cosmetic classification products- Lead and direct the Quality activities to deliver compliant, robust and timely New Product Introduction (NPI) launches within the category by;- being the decision-maker for Quality in go/ no go decisions on projects- setting the Quality strategy for each project- coordinating Quality activities between other Quality groups such as auditing teams, R&D Quality and Contract Manufacturing Quality Managers- escalation of issues Show less
-
-
External Supply Quality Lead, EMEA, Foods
-
Apr 2012 - Mar 2014
- Responsible for the Quality of outsourced contract manufactured products in the EMEA region for brands worth £40M+ annually- The main point-of-contact for the Nutritional and Digestive Health category in issues regarding Quality or QMS application- Proven track record in complaint and deviation reduction.- Planning and leading Quality strategies to deliver improved performance- Ensuring that External Supplier facilities and systems meet and maintain current regulatory and GSK required standards- Quality Leader for all New Product Introduction activities ensuring that products are value engineered with suitable validation protocols in place, that products are introduced smoothly, any issues are identified and addressed, that trials are attended and ongoing production is evaluated to identify any learnings (experience in 100+ NPI projects).- The Quality link between the contractor, Supply Chain, R&D, Regulatory, Brand, legal, Communications and Commercial teams. - Driving Continual Improvement in the contractor network such as the roll-out of Root Cause Analysis and allergen management training.- Appropriate application of risk management by identifying potential short comings in contractors quality systems, considering the risk to quality, safety, legality and GSK reputation. - Communication and cascading of information of significant matters across the organization.- Implementing Quality Systems performance management with appropriate KPIs.- Technical support with production for new or existing products including problem solving and use of RCA tools.- Supporting globalization projects by carrying out Due Diligence visits- Control of the Informed Sport programme and banned substance testing- Coached, developed and lead a group of Quality Managers according to GSK values and objectives- Identification of industry best practices and roll-out to GSK.- Putting in place Service Level Agreements between departments to aid smoother ways of working. Show less
-
-
Compliance & Contract Manufacturing Quality Manager for foods
-
Sep 2008 - Apr 2012
- Contractor Management activities for 22 contractors including; dossier creation, audit preparation and CAPA management, KPI reviews, change control management, surveillance visits, technical support, issue management and RCA. - Escalation of incidents- Management of the Quality aspects of Technical Transfer of products from one manufacturing site to another- Management of risk registers and risk assessments of contractors- Quality Leader on NPI projects, reviewing trial data and evaluation of any non-conformities alongside R&D- Alignment of testing methods throughout R&D, manufacturing sites and the range of Third Party Manufacturers- Creation and use of Quality Improvement programmes such as the Risk Assessment model and resource modeling Show less
-
-
Operational Excellence Lead
-
Aug 2006 - Oct 2008
- OE facilitator and mentor for GMS improvement projects (Pharma, Cosmetics, Nutritionals)- Ensuring the application of Lean and Six Sigma principles across the business- Regular user and facilitator for groups using DMAIC, FMEA, House of Quality, Kaizen, PDCA- Growing the OE Community through awareness of online tools- Improving OE processes such as the Green Belt certification process- Member of the approval board for Green Belt certifications- Mentored 8 people to OE Green Belt certification Show less
-
-
Food / Nutritional QMS Leader - 2 year project
-
Aug 2006 - Oct 2008
- Recruiting a multi-functional global team of 50 members to represent the scope of the Nutritionals business- Lobbying sponsors for support and clearing road blocks- Securing and managing a £150,000 budget from SVP of Quality- Regular communication of the project to the project sponsors, QMSC, VP of Nutritionals UK- Arranging fair work split among team members- Gap analysis at manufacturing sites, globally- Conducting a global review of all relevant standards: CFR21/BRC/Codex Alimentarius/Indian/Malaysian/EU/UK/Australian/African.- Arranging and facilitating all aspects of a week-long conference for 23 senior project members in Dubai- Working alongside the QMS Steering Team and Committee to assure nutritional requirements are understood- Author of the Nutritional Policies, Processes and Guidelines- Assisting authorship of associated training packages- Education of auditing groups in new polices and processes (GQA)- Coordinating global distribution of expectations to Third Party Contractors- Attending Audits at Nutritional sites- Overseeing implementation of the policies ad processes within GSK nutritional sites- Managing complex situations with internal & external senior management- Ongoing governance- Launched the Nutritionals Best Practice Forum- ERA 2007 & 2008 GMS Excellence Recognition Awards (ERA) won for this project Show less
-
-
Senior Quality & Compliance Auditor
-
Nov 2000 - Aug 2008
- Conducting audits of new and existing facilities to appropriate European and company standards, including: Pharmaceutical, Steriles, Cosmetic and food / nutrition Third Party Contractors, Licensees, Analytical & Microbiology laboratories, contract packers, promotional packers, warehouses and vaccines distribution chains- Responsible for approval or non-approval of contractors and licensees - Identify and communicate any issues that impact product quality, safety, regulatory compliance or business continuity.- Identify trends of issues within the contractor network- Identifying the need for and conducting training where necessary with third party contractors- Assisted in the development of the Auditor Certification Process- Developed tools that are now common ways of working for the External Supply Audit team, such as the audit risk assessment tool and frequency setting tools- Managing difficult or political situations with diplomacy Show less
-
-
Quality Manager, Pharmaceuticals
-
Oct 1998 - Nov 2000
- Quality checks on all asthma inhaler batches- Responsible for advising the QP on release or rejection of batches within tight time schedules- Writing Standard Operating Procedures and training appropriate personnel- Processing customer complaints.- Setting up a database for recording and trending of exception reports- Monitoring exception reports trends and addressing issues- Reviewing Production Equipment Logs to monitor engineering work- Explaining systems within the department to MCA and FDA inspectors- Assessing validation protocols and change control reports- Ensuring smooth operation of department following change over from BPCS to SAP- Self-inspections of pharmaceutical production areas and ensuring timely CAPA closure Show less
-
-
Education
-
Open University, UK
Bachelor of Science - BS, Open Science -
Open University, UK
BSc Hons, Psychology
Community
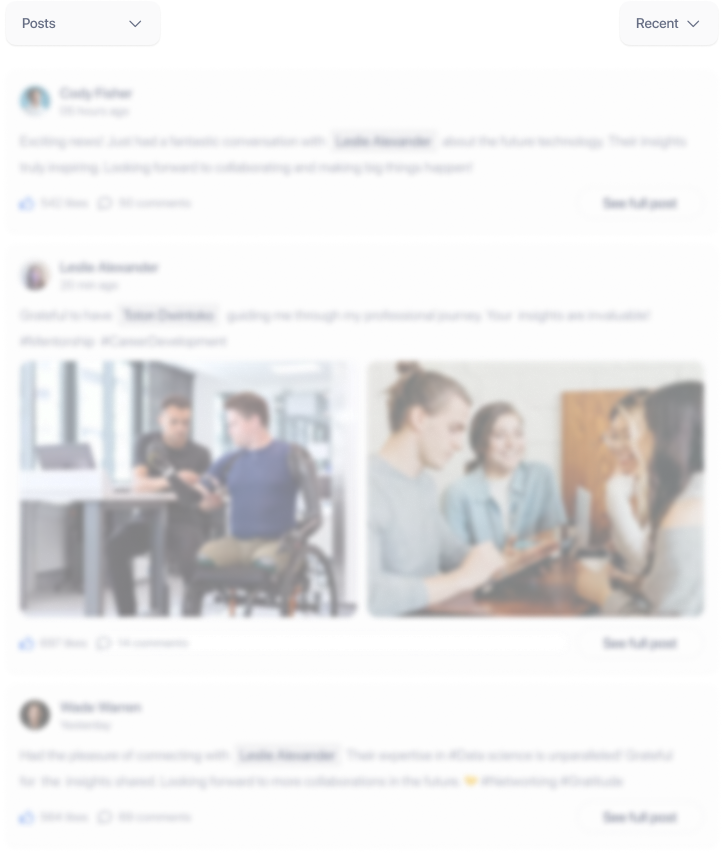