Haim Moshe
Vice President Of Customer Services at GenCell Energy- Claim this Profile
Click to upgrade to our gold package
for the full feature experience.
Topline Score
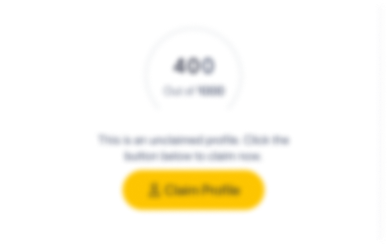
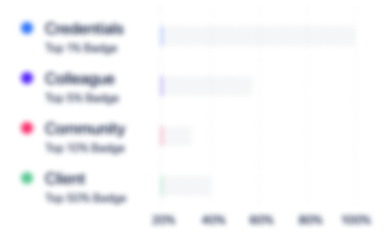
Bio

Arik Goldberg
Haim is a highly experienced and competent Quality Engineer. Whilst at More Energy he was responsible for managing multiple quality projects as a Quality Dep. Manager and Engineer, setting up and managing QC systems for high volume production and supporting the Engineering and Operations Departments of the company. Haim is capable of working either as part of a team, or a sensitive and professional Manager or on his own, and always delivers high quality work on time and budget. Haim would be an asset to any organisation.

Ehud Ben Shlomo
I worked with Haim for several years in two companies, "Mor Energy" & "Sultam system". Haim was the Quality manager for both companies. It was my pleasure to work with Haim, full cooperation, professional and understanding for production and Engineering needs. Always looking for the best performance, thinking how to optimize the process and always come with a new idea for improvement. High level manager, know to focus on the important topics and to find the right solutions. But in parallel, if required, Haim know to get into daily and deeply activities.

Arik Goldberg
Haim is a highly experienced and competent Quality Engineer. Whilst at More Energy he was responsible for managing multiple quality projects as a Quality Dep. Manager and Engineer, setting up and managing QC systems for high volume production and supporting the Engineering and Operations Departments of the company. Haim is capable of working either as part of a team, or a sensitive and professional Manager or on his own, and always delivers high quality work on time and budget. Haim would be an asset to any organisation.

Ehud Ben Shlomo
I worked with Haim for several years in two companies, "Mor Energy" & "Sultam system". Haim was the Quality manager for both companies. It was my pleasure to work with Haim, full cooperation, professional and understanding for production and Engineering needs. Always looking for the best performance, thinking how to optimize the process and always come with a new idea for improvement. High level manager, know to focus on the important topics and to find the right solutions. But in parallel, if required, Haim know to get into daily and deeply activities.

Arik Goldberg
Haim is a highly experienced and competent Quality Engineer. Whilst at More Energy he was responsible for managing multiple quality projects as a Quality Dep. Manager and Engineer, setting up and managing QC systems for high volume production and supporting the Engineering and Operations Departments of the company. Haim is capable of working either as part of a team, or a sensitive and professional Manager or on his own, and always delivers high quality work on time and budget. Haim would be an asset to any organisation.

Ehud Ben Shlomo
I worked with Haim for several years in two companies, "Mor Energy" & "Sultam system". Haim was the Quality manager for both companies. It was my pleasure to work with Haim, full cooperation, professional and understanding for production and Engineering needs. Always looking for the best performance, thinking how to optimize the process and always come with a new idea for improvement. High level manager, know to focus on the important topics and to find the right solutions. But in parallel, if required, Haim know to get into daily and deeply activities.

Arik Goldberg
Haim is a highly experienced and competent Quality Engineer. Whilst at More Energy he was responsible for managing multiple quality projects as a Quality Dep. Manager and Engineer, setting up and managing QC systems for high volume production and supporting the Engineering and Operations Departments of the company. Haim is capable of working either as part of a team, or a sensitive and professional Manager or on his own, and always delivers high quality work on time and budget. Haim would be an asset to any organisation.

Ehud Ben Shlomo
I worked with Haim for several years in two companies, "Mor Energy" & "Sultam system". Haim was the Quality manager for both companies. It was my pleasure to work with Haim, full cooperation, professional and understanding for production and Engineering needs. Always looking for the best performance, thinking how to optimize the process and always come with a new idea for improvement. High level manager, know to focus on the important topics and to find the right solutions. But in parallel, if required, Haim know to get into daily and deeply activities.
0
/5.0 / Based on 0 ratingsFilter reviews by:
Experience
-
GenCell Energy
-
Israel
-
Renewable Energy Equipment Manufacturing
-
1 - 100 Employee
-
Vice President Of Customer Services
-
Sep 2020 - Present
-
-
Customer Support Director
-
Nov 2018 - Sep 2020
-
-
Quality Manager
-
Mar 2015 - Sep 2020
Setting the company Quality Strategy in alignment with company business objectives. Managing all quality aspects in accordance with internal and external requirements. Acting as leading quality engineering function to support both R&D and Engineering projects. Developing new control methods and processes for supporting company scale-up efforts
-
-
-
HP Indigo
-
Printing Services
-
Senior Quality Engineer
-
Sep 2010 - Mar 2015
Leading and developing cross-organizational failures handling processes Leading cross-organizational processes improvement Defining suppliers quality requirements and support implementations Leading audits as Senior ISO and processes auditor Leading and developing cross-organizational failures handling processes Leading cross-organizational processes improvement Defining suppliers quality requirements and support implementations Leading audits as Senior ISO and processes auditor
-
-
-
-
Quality Assurance Manager
-
Feb 2010 - Sep 2010
Department re-positioning in the company - strengthening the quality support and mentoring across the organization Improved supplier quality management model and implementation process Improving and mentoring all quality control bodies in the organization Integration of quality approaches in projects starting from initiation phases Introduction of quality engineers into the development process lead the company toward "self-inspection" certification from IDF and MOD Department re-positioning in the company - strengthening the quality support and mentoring across the organization Improved supplier quality management model and implementation process Improving and mentoring all quality control bodies in the organization Integration of quality approaches in projects starting from initiation phases Introduction of quality engineers into the development process lead the company toward "self-inspection" certification from IDF and MOD
-
-
-
More Energy
-
Utilities
-
1 - 100 Employee
-
Quality Manager
-
Feb 2007 - Nov 2009
Staffed and managed upwards a “Full-Scope” quality department (quality assurance, engineering, inspection and labs); Maintained ISO certifying; Developed procedures for quality management of procurement; Defined and monitored KPIs; Cost of quality analysis and reporting; Manage integrated improvement teams (multi departmental) both internal and abroad; Main point of contact for the quality activities of the assembly line in Ireland; Established Shelve Life program for the High Volume line
-
-
Quality Engineer
-
2007 - 2007
Lead DFMEA, PFMEA, FAI, PPAP and PQ processes on varied products/processes; Supporting development processes and NPI of electronic and electrochemical products (validation, Experiments); Interfaced with suppliers and project team members for resolution of project quality issues and corrective action requests; Leading quality efforts abroad (China, Ireland, Austria) Including Audits/surveys and supporting/guiding vendors in building the quality into the product; Prepare and host UL surveys; Prepared and implemented SOPs for varied processes; Define and fully implement statistical valid sampling plans; Experiments design, leading and analysis (both internal and external); Leading along with engineering products and processes failures analysis and improvements; Leading MRB meetings on electronics, plastics and electrochemical materials; Defining, building and managing of various data collection systems Show less
-
-
-
Israel Defense Forces
-
Israel
-
Armed Forces
-
700 & Above Employee
-
Quality Assurance Team Leader - Electro-optics and navigation systems
-
2005 - 2007
Managing 6 staff members with the responsibility for quality assurance activities in front of major contractors (i.e Elbit, IAI, El-op, OPGAL, etc.); Act as a permanent member in PR's; review SOW and specifications; define quality procedures; guiding and instructing staff and suppliers employees; defining QA metrics and parameters; leading System, Process and Product Audits.
-
-
QA Coordinator, Fire Control System (FCS)
-
2003 - 2005
Coordinating quality assurance activities in Fire Control Systems projects for the MK Mark 3/4; Holding an office at Elbit and Elop and escorting FAIs, QUAL tests and production audits; Serving as a POC for Engineering, Production and Purchasing departments.
-
-
QA Representative, Fire Control System (FCS)
-
2000 - 2003
Responsibility for testing and approving Fire Control Systems (FCS) at source prior to shipment; Performing engineering tests for prototypes; Production files review; Intensive work with a variety of T.E's,
-
-
Education
-
Sitrin College
P.E, Electronics -
ALD
CQE, Quality Engineering -
ALD
Diploma, Quality Managment
Community
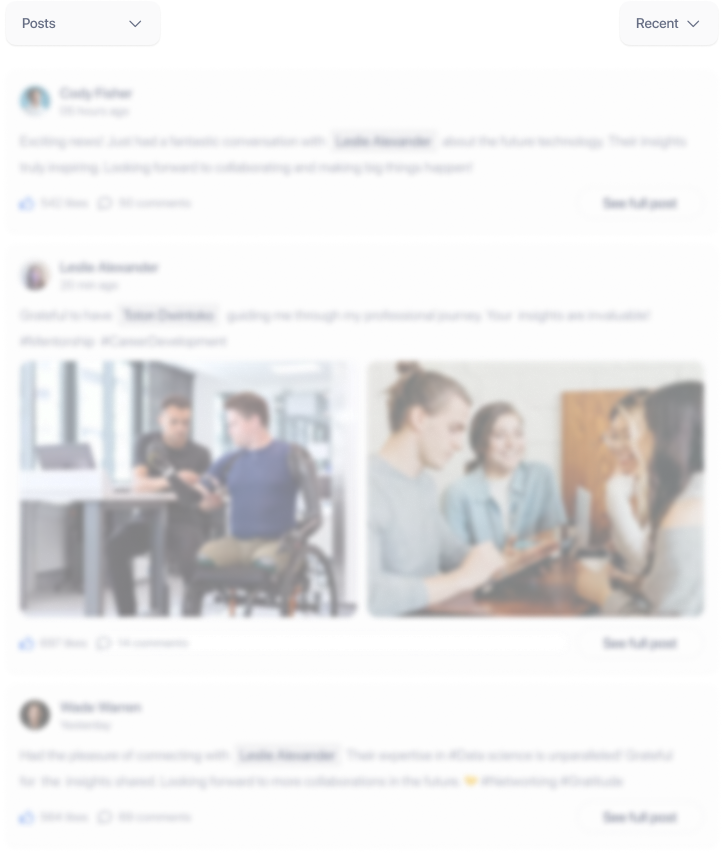