Gustavo Brea
Director Operations – División SML - Soluciones Modernas Logísticas at SMC Soluciones Modernas de Construcción- Claim this Profile
Click to upgrade to our gold package
for the full feature experience.
-
Español -
-
Ingles -
Topline Score
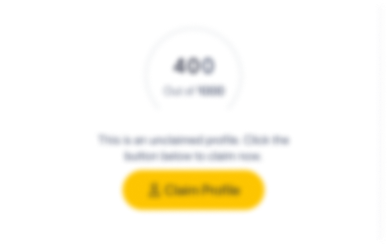
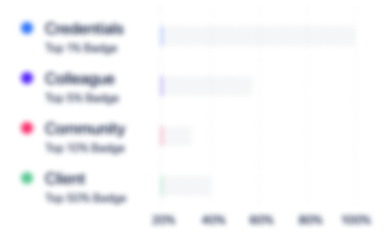
Bio

José Delgado
I met Gustavo when we were taking our BSME studies and afterwards we also finished our Degree in Machine Design and Industrial maintenance. He is a committed professional characterized by his focus on getting things done and his attention to details. He has an outstanding ability to interact with people and propose fresh ideas to solve complex problems. I have no reserve to recommend him for any operational, project or design managerial position.

José Delgado
I met Gustavo when we were taking our BSME studies and afterwards we also finished our Degree in Machine Design and Industrial maintenance. He is a committed professional characterized by his focus on getting things done and his attention to details. He has an outstanding ability to interact with people and propose fresh ideas to solve complex problems. I have no reserve to recommend him for any operational, project or design managerial position.

José Delgado
I met Gustavo when we were taking our BSME studies and afterwards we also finished our Degree in Machine Design and Industrial maintenance. He is a committed professional characterized by his focus on getting things done and his attention to details. He has an outstanding ability to interact with people and propose fresh ideas to solve complex problems. I have no reserve to recommend him for any operational, project or design managerial position.

José Delgado
I met Gustavo when we were taking our BSME studies and afterwards we also finished our Degree in Machine Design and Industrial maintenance. He is a committed professional characterized by his focus on getting things done and his attention to details. He has an outstanding ability to interact with people and propose fresh ideas to solve complex problems. I have no reserve to recommend him for any operational, project or design managerial position.

Experience
-
SMC Soluciones Modernas de Construcción
-
Mexico
-
Construction
-
1 - 100 Employee
-
Director Operations – División SML - Soluciones Modernas Logísticas
-
Apr 2017 - Present
Rental of Heavy Machinery and Equipment for cargo handling - Creation of a company in Construserv Group for the rental of heavy machinery and equipment for cargo handling.- Design the annual business plan for its presentation and approval before the council- Control the execution of the different strategies and compliance with the established business plan.- Organize the different departments of the company and supervise its operation- Presentation to the council of investment projects for the company and evaluate financial opportunities that arise.- Selection and development of the work team of all areas of the new company- Motivate and retain the talent of the organization.Achievements:- Achieve first year of the P&L of 113%, reaching a turnover of 20 MM with a profit of 21%.
-
-
Equipment and Productive Systems Manager (6 facilities)
-
Mar 2015 - Present
- Responsible for the Design, Equipment Procurement, Installation and startup of two new Plant facilities located in Puebla and Toluca subjected to Time/Budget Constraints.- Responsible for the implementation of the ERP system in the Factories (Microsoft Dynamics AX)- Accountable for 3 existing Manufacturing Plants and for the Business Unit Engineering Department for design and processing of reinforced steel for Industrial and Urban Civil Works.- Accountable for delivering against Operation goals and for expanding our share in a very competitive Market.- Responsible for expanding our business model across Mexican territory as demanded by our Company growth.Achievements:- I have increase by 200% the Production of the main Plant over the last three years with only 38% of Labor Cost Increase.- I exceeded by 15% against the production goal for the second plant in 2014 and reduced by 35% the manufacturing cost for both plants.- I reduced the transportation cost measured in MXP/Kg by 18%.
-
-
Supply Chain Corporative Manager (7 facilities
-
May 2016 - Apr 2017
Steel, Block, Vibrocompacting and Aggregate Mine Divisions- Design and implement the supply chain system of 7 facilities, that allow monitoring the status of planning, raw material, manufacturing, final product, logistic, purchases of the productive chain.- Leader of the adaptations of the ERP to improve the controls of the different productive processes.- Creation of distribution centers in the Mexican republic, improving delivery times and costs.- Creation of two new corporate department of transportation and heavy equipment, improving historical costs.- Implementation of cyclic inventories and FIFO system, improving the reliability of inventories and reduction of losses and cost.- Design and implement the appropriate levels of inventory available to ensure customer demand, looking for the minimum inventory strategy, in order to reduce the cost.- Strategy implementation with suppliers to increase credit days, improving cash flow- Set new KPIs with direction in order to improve assess of productive and administrative processes.Achievements:- I increased in average 21 days of credit with our suppliers.- I reduced by 7% distribution costs in the 2nd half of 2016
-
-
Equipment and Productive Systems Manager (6 facilities)
-
Mar 2015 - May 2016
Steel, Block and Vibrocompacting Divisions- Design and implement a system of audits that allow monitoring the status of equipment and production systems, generating corrective actions for optimization- Maintain control and ensure investment in machinery and equipment.- Set KPI to assess and monitor maintenance management and proper use of the machines on each Facilities, the effectiveness of the management of each Facilities under lean manufacturing scheme. - Assess and manage the acquisition of new equipment, justifying its profitability and exploitation.- Creating new corporate department for the launch of new machinery and equipment overhauling.- Develop the methodology to stablish the production theoretical capacities for each plant.- Machinery assessments that are out of service in order to determine the profitability of sale or recovery.Achievements:- Changing organizational culture, oriented toward the good practices of Lean Manufacturing.
-
-
Operations Manager (Steel Division – 3 facilities)
-
Sep 2013 - Mar 2015
- Responsible for the Design, Equipment Procurement, Installation and startup of two new Plant facilities located in Puebla and Toluca subjected to Time/Budget Constraints.- Responsible for the implementation of the ERP system in the Factories (Microsoft Dynamics AX)- Accountable for 3 existing Manufacturing Plants and for the Business Unit Engineering Department for design and processing of reinforced steel for Industrial and Urban Civil Works.- Accountable for delivering against Operation goals and for expanding our share in a very competitive Market.- Responsible for expanding our business model across Mexican territory as demanded by our Company growth.Achievements:- I have increase by 200% the Production of the main Plant over the last three years with only 38% of Labor Cost Increase.- I exceeded by 15% against the production goal for the second plant in 2014 and reduced by 35% the manufacturing cost for both plants.- I reduced the transportation cost measured in MXP/Kg by 18%.
-
-
Plant Manager
-
Aug 2011 - Sep 2013
- Responsible in the Reinforced Steel Business Unit for the Manufacturing, Maintenance, Quality and Engineering Departments (6 Engineers, 10 technicians, 90 workers)- Accountable for achieving production goals, material and labor costs, delivery lead time improvements and product quality improvements.- Responsible to improve the efficiency of machines and processAchievements:- I reduced the labor cost by 18% after 2 months and I increase the manufacturing Productivity by 80%. - I developed plans for the recovery of the Plant technical infrastructure and implemented preventive maintenance programs which increased by 23% the overall equipment availability.
-
-
-
ASTRAL FREAKS
-
Retail Apparel and Fashion
-
Plant Manager
-
May 2005 - Feb 2011
- Development of Strategic Plan and settlement of Key Performance Indicators - Modernization and Automation of the Manufacturing facilities. - Quality Improvement and Cost Reduction Program Implementation - Follow up and Control for a proper application of Policies and Procedures - Supervision and Control of all Production Areas, Quality Department and Warehouse (28 persons). - Fabric Inventory Control for Raw Material, Work in Process and Finished Goods.. - Development of new and Negotiation with existing fabric suppliers to improve quality and cost of the raw material. - Investigation and resolution of customer Quality Complaints with root cause analysis to avoid recurrence. - Process Re-engineering for the Reception, Storage and Distribution of Goods. Achievements: - I reduced the cost of finished product by 9% according to target set in 2009 - I improved our relationship with our suppliers through contracts and agreements. - I restructured the production area an increased by 18% the production capacity. - I reduced the production time from 6 to 4 weeks and thus decreased our inventory levels - I implemented new procedures and management indicators enabling better planning at different stages of production.
-
-
-
-
Project Manager
-
Dec 2003 - Apr 2006
- Design and Manufacture of Injection Molding and Extrusion-Blowing Molds. - Implementation of CNC, CAD, CAM, CAE technologies (3D and Parametric Software) - Design, modeling and analysis in CAD, CAE of packaging and plastic parts. - Study design and manufacturability of new products. - Manufacturing Rapid Prototyping of new design. - Design and manufacture of precision mechanical parts. - Evaluation and acquisition of new CNC equipment. - Modernization and Automation of injection equipment. - Implementation of a new philosophy in Project Development. - Technical Assistance to the marketing management department. - Development of new plastic products. - Implementation of predictive and preventive maintenance practices. - Optimization of Manufacturing Processes. Achievements: - I Implemented a new philosophy of working in development projects, Generating a 65% increase in demand - I Introduced new technologies CNC, CAD, CAM & CAE, achieving the modernization of the mold-making workshop
-
-
-
-
Project Manager
-
Jun 1999 - Dec 2003
Performance as Project Manager: - Design and Manufacture of Injection Molding and Extrusion-Blowing Molds. - Implementation of CNC, CAD, CAM, CAE technologies (3D and Parametric Software) - Design, modeling and analysis in CAD, CAE of packaging and plastic parts. - Study design and manufacturability of new products. - Manufacturing Rapid Prototyping of new design. - Design and manufacture of precision mechanical parts. - Evaluation and acquisition of new CNC equipment. - Modernization and Automation of injection equipment. - Implementation of a new philosophy in Project Development. - Technical Assistance to the marketing management department. - Development of new plastic products. - Implementation of predictive and preventive maintenance practices. - Optimization of Manufacturing Processes. Achievements: - I developed news procedures in the mold maintenance - I Implemented a new philosophy of working in development projects, Generating a 65% increase in demand - I Introduced new technologies CNC, CAD, CAM & CAE, achieving the modernization of the mold-making workshop - I reduced in 8% the machine downtime due to mold failures, with the implementation of new maintenance procedures.
-
-
-
-
Production Engineer
-
Aug 1994 - Apr 1997
- Production Control and Scheduling of the Several plant areas. - Continuous Follow up to Plant Supervisors (24). - Installation and startup of new Equipments. - Development and Implementation of procedures under ISO-9000 and QS-9000 scheme. Achievements: - I successfully implemented a pilot program to control process variability, achieving savings of U.S. $ 258.000 annually. - I led a process of organizational change, achieving saving of U.S.$ 342.000 annually in the production area. - Support in the design and development of new battery models. - Follow up and surveillance for the correct execution of processes. - Technical training of sales staff.
-
-
-
The Goodyear Tire & Rubber Company
-
United States
-
Motor Vehicle Manufacturing
-
700 & Above Employee
-
Production Specialist
-
Jun 1993 - Aug 1994
- Support in the control of production in the vulcanized area. - Design and Manufacture of a truck tire painting machine. - Industrial safety and training coordination in the vulcanized area. - Support in the implementation of a broad training plan for all staff. Achievements: - I assumed the challenge to negotiate with the Labor Union the implementation of a new automatic painting station, - I reduced wasted by 15% deformed tires (0,4% of total). - Support in the control of production in the vulcanized area. - Design and Manufacture of a truck tire painting machine. - Industrial safety and training coordination in the vulcanized area. - Support in the implementation of a broad training plan for all staff. Achievements: - I assumed the challenge to negotiate with the Labor Union the implementation of a new automatic painting station, - I reduced wasted by 15% deformed tires (0,4% of total).
-
-
-
Empresas Polar
-
Venezuela
-
Food and Beverage Services
-
700 & Above Employee
-
pasante
-
1992 - 1993
Análisis de Costos de los insumos energéticos de la Planta Análisis de Costos de los insumos energéticos de la Planta
-
-
Education
-
Universidad Simon Bolivar
Specialist in Machine Design and Industrial Maintenance, Engineering -
Universidad Simon Bolivar
Mechanical Engineer, Engineering
Community
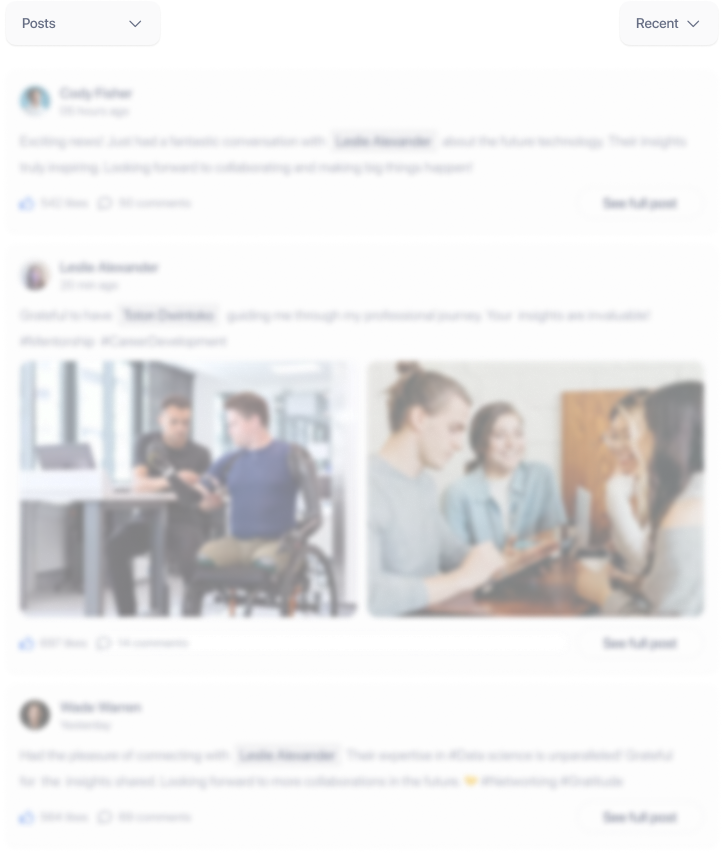