Guillermo Ros
Project Account Manager at MESbook - Gestión de Fábricas en Tiempo Real- Claim this Profile
Click to upgrade to our gold package
for the full feature experience.
-
Español Native or bilingual proficiency
-
Catalán Native or bilingual proficiency
-
Inglés Full professional proficiency
-
Alemán Elementary proficiency
Topline Score
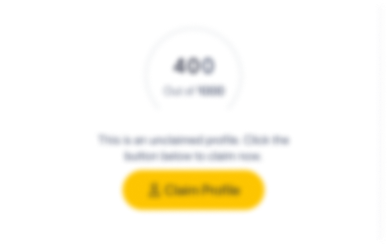
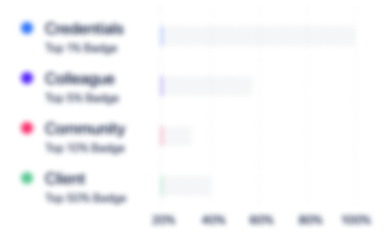
Bio
0
/5.0 / Based on 0 ratingsFilter reviews by:
Credentials
-
Scrum Foundation Professional Certificate SFPC
CertiProfMar, 2021- Sep, 2024 -
Six Sigma Green Belt
AVIA Clúster de Automoción de la Comunitat ValencianaJan, 2015- Sep, 2024 -
Inyección de materiales plásticos y optimización de procesos de inyección
AIMPLAS · Instituto Tecnológico del PlásticoJan, 2014- Sep, 2024 -
Certificate in Advanced English (C1 Advanced)
Cambridge Assessment EnglishJun, 2011- Sep, 2024 -
Certificado Oficial de Grau Mitjà de Valencià (C1)
Junta Qualificadora de Coneixements de Valencià (JQCV) -
Título Superior de Inglés (C1)
Escuela Oficial de Idiomas
Experience
-
MESbook - Gestión de Fábricas en Tiempo Real
-
Spain
-
Software Development
-
1 - 100 Employee
-
Project Account Manager
-
Mar 2021 - Present
• Definition of the scope, specifications, and project requirements, based on client expectations, directly communicating with the client's Project Management and Commercial Area. • Project planning and timeline management, ensuring that it is carried out within the set objectives, including scope, time, and cost requirements. • Participating in consulting processes with clients, analyzing processes and defining the best path and procedure for the processes that will subsequently be implemented within the management system. • Functional definition of the implementation project and coordination of different internal areas for the development of necessary product functionalities to achieve the objectives, ensuring alignment with the project's time and cost goals. • Carrying out the identification of necessary signals and coordinating with the Automation department to develop and establish the infrastructure for data extraction from the machines' PLCs. • Definition of communication and integration functions with the client's ERP/SAP system for system communication. • Managing and adapting customer's Control Plans to integrate the management and reporting of quality controls from the tool through a real-time guided reporting model. • Conducting internal project follow-up meetings and meetings with the client to coordinate all milestones and actions of the implementation project. • Coordinating the start-up, carrying out the verification and validation of all processes and functionalities, training Key Users, and conducting UATs for implementation validation. • Monitoring improvement actions and change management until the objectives set in the project's scope are achieved. • Work within an Agile/Scrum Methodology, participating in daily stand-up meetings, defining backlogs and scopes, sprints planning and retrospective outcomes in order to create action plans for the next sprint. Show less
-
-
-
Dr. Schneider Unternehmensgruppe
-
Germany
-
Plastics Manufacturing
-
400 - 500 Employee
-
Project Quality Planner
-
Oct 2018 - Jun 2020
• Define Quality Standards for the project based on customer requirements and ensure they are achievable and measurable for both, the manufacturing plant but also for sub-suppliers. • Develop and define Control Plans, measurement equipment and any other tools or information which is needed to ensure Quality Standards and Customer Specific Requirements are met on the product and throughout all stages of the process. Creating necessary documentation for this purpose (Quality Book, Q-Instructions, Boundary samples, Control Charts, Cp and Cpk calculation, etc.). • Constantly communicate with customer, attend customer meetings, show results and discuss about current status, ongoing tasks and action plan during project phase. • Effectively align and communicate with team members and project management to ensure correct development of the project and milestones are met according to target and timeline. • Handling and tracking APQP customer's portal and Core tools throughout all the stages and project phases to achieve project PPAP and homologation. • Attendance at customer validation events and presentation of prototypes, initial samples, and OTOP parts for functional, dimensional, and appearance approval until obtaining their homologation. • Validation of measuring equipment through MSA (Measurement System Analysis) and R&R (Repeatability and Reproducibility) studies, as well as conducting dimensional reports. • Support development and Engineering team in order to adequately solve the quality problems of the project, as well as during change management. Collaborating in the creation and updating of design and process FMEAs during the launch of new projects and providing support in the production phase. • Leading the creation and presentation of 8D reports to customers in response to quality claims during the launch phase as well as providing support during series production phase for documenting them. Show less
-
-
-
-
Launch Project Manager
-
May 2016 - Oct 2018
• Lead and coordinate launch and industrialization of new projects, transfers and relocation of equipment in the plant. Keep track of the progress and ensure milestones and deliverables are met successfully and according to timeline. • Clearly communicate with customer, attend customer meetings and events, directly respond about project status and discuss project open topics to define the best approach. • Effectively work with cross-functional teams, lead team meetings, manage LOP and define Action Plans to achieve successful launch of the projects and according to targets. Provide necessary information to all departments and clearly communicate with plant management about project status. • Coordinate ramp-up and delivery of the parts during all project phases until SOP, ensuring all launch requirements and the availability of the necessary documentation in the plant. Manage and track other launch requirements such as packaging instructions, product standards, etc. for new customers. Solve issues together with local managers. • Oversee Engineering changes (customer or internally driven) to ensure a smooth transition from the old revision and grant parts are manufactured and delivered according the latest level. • Monitoring and ensuring PPAP homologation according to timing and target and keep permanent contact with team members responsible for each item during each phase and milestone. • Oversee transfer of parts and equipment between plants. Coordinates necessary activities with local managers. • Coordinate customer visits, Run@Rates, Project audits and other events in house. Align with all departments and provide support to achieve the targets. Show less
-
-
-
-
Continuous Improvement Coordinator
-
Nov 2012 - May 2016
• Analysis and implementation of improvements and costs saving activities in the plant (injection moulding, paintline, assembly lines, logistics, etc.).• Management and coordination of the suggestions from employees scheme. Calculation of cost savings, pay off of investments and evaluation of the efficiency of continuous improvement actions.• Lead workshops of continuous improvement, developing Value Stream Mapping of different processes and coordinating workteams in order to find and define opportunities for improvement activities.• Collaborate / lead projects within multidisciplinary teams involving the internal logistics processes, under the basis of a Pull-flow System and implementation of sequenced supply based in logistic trains along the whole flow of the manufacturing process.• Definition and calculation of KPI’s in order to monitoring the production status and productivity rates. Show less
-
-
Optimization and Process Planning Engineer
-
Jun 2012 - Nov 2012
• Training period in Process planning and Optimization Department in Radomierz Plant (Poland).• Analysis of assembly lines and processes, driving projects of optimization and balancing lines to achieve defined savings target.
-
-
Trainee as Production and Process Engineer
-
Oct 2011 - Jun 2012
• Analysis and definition of production processes and elaboration of layouts, process instructions and related documentation.• Implementation and standardization of lean manufacturing tools and techniques in the plant (5’s, TPM, SMED...).• Lead and collaborate with TPM workteams and definition of activities based on scheduled action plan.
-
-
-
Ford Motor Company
-
United States
-
Motor Vehicle Manufacturing
-
700 & Above Employee
-
Trainee Industrial Engineer
-
Oct 2010 - Jun 2011
• Training period and support to the department of Industrial Engineering, Layout and Equipment in Almussafes Plant. • Development of the Final Degree Project “Analysis, design and implementation of a poka-yoke system in the assembly lines”. • Training period and support to the department of Industrial Engineering, Layout and Equipment in Almussafes Plant. • Development of the Final Degree Project “Analysis, design and implementation of a poka-yoke system in the assembly lines”.
-
-
Education
-
Universidad Politécnica de Valencia
Ingeniería Industrial, Especialidad Organización y Gestión Industrial -
The University of Manchester
Industrial Management and Organization Engineer, Industrial Engineering
Community
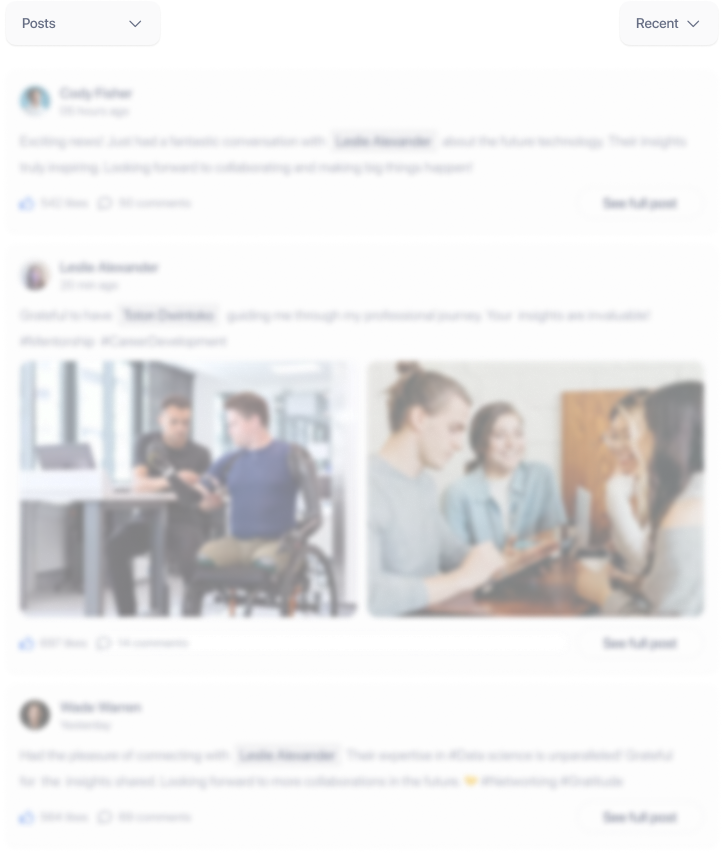