Guillermo Espinosa
Gerente concesiones Municipales Nuevo Leon at Promotora Ambiental S.A.B. de C.V.- Claim this Profile
Click to upgrade to our gold package
for the full feature experience.
-
INGLES -
Topline Score
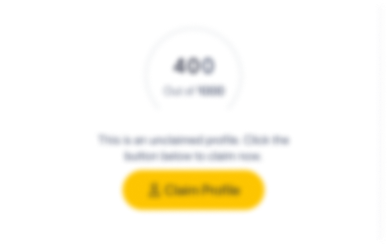
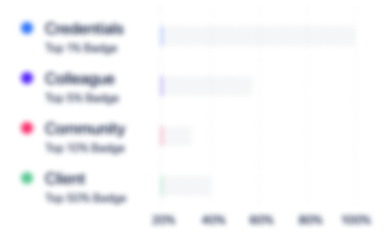
Bio

Guillermo is a great contributor for any company in a senior level, well focused and oriented to get goals and objectives, I recommend him to be on charge of big organizations with good challenges

Guillermo is a manufacturing professional. In his time with Celestica as Production Manager always showed an outstanding communication with all employees. His commitment with the organization was an example for all employees in the manufacturing floor. As General Manager of the Reynosa operation with Promotora Ambiental, Guillermo performed an excellent job with high quality, results under cost and high customer satisfaction.

Guillermo is a great contributor for any company in a senior level, well focused and oriented to get goals and objectives, I recommend him to be on charge of big organizations with good challenges

Guillermo is a manufacturing professional. In his time with Celestica as Production Manager always showed an outstanding communication with all employees. His commitment with the organization was an example for all employees in the manufacturing floor. As General Manager of the Reynosa operation with Promotora Ambiental, Guillermo performed an excellent job with high quality, results under cost and high customer satisfaction.

Guillermo is a great contributor for any company in a senior level, well focused and oriented to get goals and objectives, I recommend him to be on charge of big organizations with good challenges

Guillermo is a manufacturing professional. In his time with Celestica as Production Manager always showed an outstanding communication with all employees. His commitment with the organization was an example for all employees in the manufacturing floor. As General Manager of the Reynosa operation with Promotora Ambiental, Guillermo performed an excellent job with high quality, results under cost and high customer satisfaction.

Guillermo is a great contributor for any company in a senior level, well focused and oriented to get goals and objectives, I recommend him to be on charge of big organizations with good challenges

Guillermo is a manufacturing professional. In his time with Celestica as Production Manager always showed an outstanding communication with all employees. His commitment with the organization was an example for all employees in the manufacturing floor. As General Manager of the Reynosa operation with Promotora Ambiental, Guillermo performed an excellent job with high quality, results under cost and high customer satisfaction.

Experience
-
Promotora Ambiental S.A.B. de C.V.
-
Mexico
-
Environmental Services
-
200 - 300 Employee
-
Gerente concesiones Municipales Nuevo Leon
-
May 2016 - Present
-
-
-
Gen Industrial USA Inc
-
United States
-
Environmental Services
-
1 - 100 Employee
-
Gerente Operaciones y Logistica
-
May 2016 - May 2016
Servicios Medio Ambiente
-
-
-
-
Operations
-
Aug 2013 - Apr 2016
-
-
-
-
Plant Manager
-
Oct 2012 - Jun 2013
Responsible for the operation of the production plant at 100%, Production, Process, Manufacturing, Maintenance, Planning, Inventory Control.Goals and AchievementsReducing variable manufacturing costs 4.3% to 3.6%, Optimization of Labor, compliance improved adherence to production plan from 67% to 89% Reduction of change- over downtime by improvements in machining centers and lathes, develop preventative maintenance plan and monitor it 100%, reduced by 15% downtime for corrective maintenance. staff development and training plan development according to business needs200 direct employees, five Heads of Department (Machining, Final Assembly, Maintenance, Process and Planning), 6 supervisors, 3 Process Engineers
-
-
-
-
General Manager
-
May 2010 - Oct 2012
Responsible for the whole facility, operations, financial , human resources, maintance ,new customer arrival, negotiations with municipal authorities , review of contracts, landfill operations.Goals and achievements .sales, operating costs, administrative costs, percentage of income, receivables overdue, percentage of compliance services, compliance maintenance, environmental compliance, organizational climatelabor to 300 direct employees, 4 department managers (operations, maintenance, landfill, administrative) and 4 department coordinators (human resources, purchasing, sales, environment.Reporting direct
-
-
-
-
Operaciones
-
Apr 2010 - May 2010
-
-
-
Elcoteq
-
Luxembourg
-
Appliances, Electrical, and Electronics Manufacturing
-
300 - 400 Employee
-
Manufacturing Manager
-
Oct 2007 - Sep 2009
Production area responsible trought SMT TO BACKENDIncluiding Manual and Automatic insertionResponsible for a product family from Rim customerAchieve production plan and quality target Labor to 850 indirect and 17 supervisorsResponsible for a 12 smt lines in four shift patternHead count analisys and reduction plan Accomplishments.Implement kanban system in order to reduce stock in process Yield increase to 85%to 92% doing a new lay out .Implement a quick feedback to the line
-
-
-
-
Production Manager
-
Jan 2002 - Oct 2007
Production area responsible trought smt to backend Responsible of the Lean system Implementation Achieve production plan and quality target Labor to 700 indirect and 15 supervisorsImplementing cost reduction plan Accomplishments.Implement kanban system in order to reduce stock in process Increase Supermarket level in order to scrap reductionImplement Pull system in order to reduce downtimesReduction Setting time from 4 hours to 20 minutes in smt lines Winner in 5s discipline implementation
-
-
Production Superintendent
-
Jan 2000 - Dec 2001
Production area responsibleGoals' area definitionImproving process cycle time applying balancing lines and Kaizen systemEnsure we have the right people with the right skill ( training skill)Labor to 300 indirect and 5-7 supervisors Achieve QS9001 and ISO14000
-
-
Production Supervisor
-
Oct 1998 - Oct 2000
Backend area responsibleStart-up mass production of 5 production cellsProblems Analysis ImplementationAchieve production plan and quality target Introduce training system in order to improve operator skillsImplement cost reduction plan in areas Achieve QS9001 and ISO14000
-
-
Education
-
Universidad Autónoma de Nuevo León
INGENIERIA, ELECTRONICA Y COMUNICACION -
Universidad Autonoma de Nuevo Leon (FIME)
Electronic and Communications Engineer -
Universidad Autónoma de Nuevo León
Community
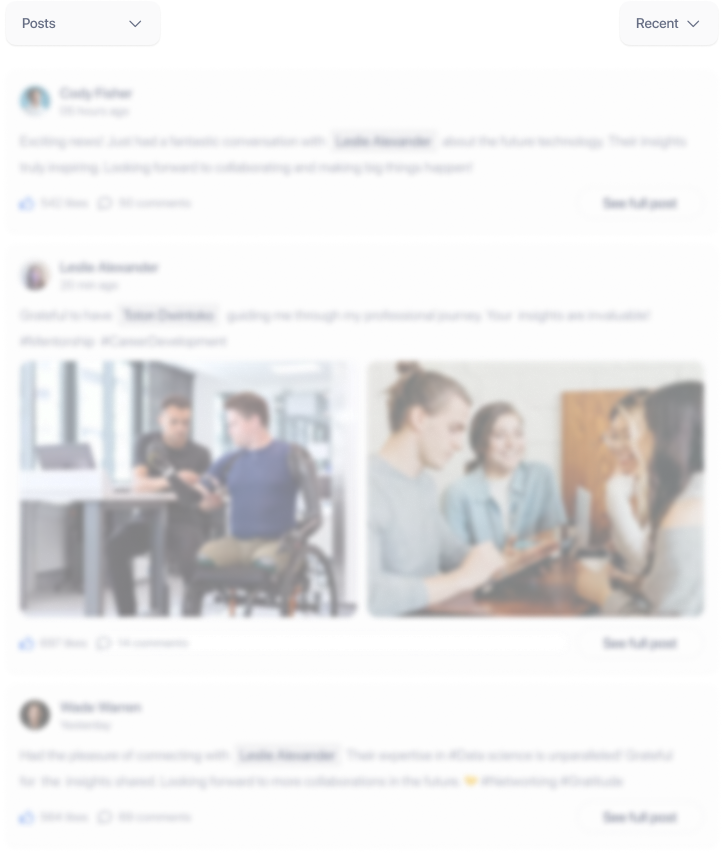