Guido Parodi
Senior Consultant at Galgano & Associati- Claim this Profile
Click to upgrade to our gold package
for the full feature experience.
Topline Score
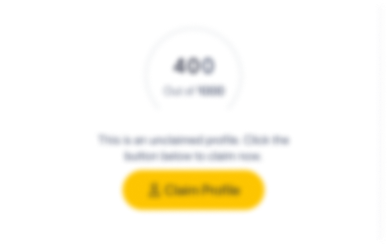
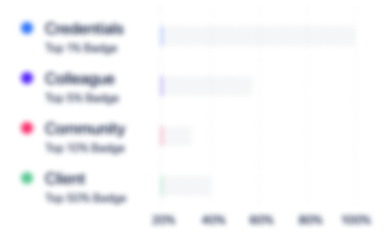
Bio

Khaled Ismail
Guido is my godfather, i learned a lot from him on both personal and profissional level,i have been enjoying working with him for several years, he is one of the best guys i have ever met and i can really say that we are lucky in UTC to have him working with us

LinkedIn User
Guido is a very experienced and professional leader, with great expertise in Quality, Lean and Continuous Improvement. Eventhough Guido was my supervisor, our relationship was (and still is)very friendly and I really enjoyed working for and with him.

Khaled Ismail
Guido is my godfather, i learned a lot from him on both personal and profissional level,i have been enjoying working with him for several years, he is one of the best guys i have ever met and i can really say that we are lucky in UTC to have him working with us

LinkedIn User
Guido is a very experienced and professional leader, with great expertise in Quality, Lean and Continuous Improvement. Eventhough Guido was my supervisor, our relationship was (and still is)very friendly and I really enjoyed working for and with him.

Khaled Ismail
Guido is my godfather, i learned a lot from him on both personal and profissional level,i have been enjoying working with him for several years, he is one of the best guys i have ever met and i can really say that we are lucky in UTC to have him working with us

LinkedIn User
Guido is a very experienced and professional leader, with great expertise in Quality, Lean and Continuous Improvement. Eventhough Guido was my supervisor, our relationship was (and still is)very friendly and I really enjoyed working for and with him.

Khaled Ismail
Guido is my godfather, i learned a lot from him on both personal and profissional level,i have been enjoying working with him for several years, he is one of the best guys i have ever met and i can really say that we are lucky in UTC to have him working with us

LinkedIn User
Guido is a very experienced and professional leader, with great expertise in Quality, Lean and Continuous Improvement. Eventhough Guido was my supervisor, our relationship was (and still is)very friendly and I really enjoyed working for and with him.

Experience
-
Galgano & Associati
-
Italy
-
Business Consulting and Services
-
1 - 100 Employee
-
Senior Consultant
-
Mar 2019 - Present
Consulting in Lean, Quality and Operations area. Specialized in Lean Manufacturing, Process optimization, Root Cause Analysis and Quality improvement Consulting in Lean, Quality and Operations area. Specialized in Lean Manufacturing, Process optimization, Root Cause Analysis and Quality improvement
-
-
-
Ideal Standard International NV
-
Belgium
-
Manufacturing
-
700 & Above Employee
-
Group Quality, Lean, EH&S Director
-
Mar 2016 - Mar 2019
Lead and design lean manufacturing goals and strategies for improving the operations and processes within the organisation. Manage all activities for continuous improvement and performance enhancement and employ lean methodologies and tools in order to accomplish business objectives. Oversee the development of operation transformation strategy for manufacturing, R&D, and distribution. • Establish quality and reliability standards by studying product and consumer requirements with other members of management and with production operators, technicians, and engineers. • Devise testing methods and procedures and reinforce in-process product inspection standards by studying manufacturing methods. • Drive product quality by enforcing Root Cause Analysis methodology and Quality assurance policies and procedures, collaborating with management to develop manufacturing and training methods. • Reduce Warranty costs by 10% YOY Show less
-
-
-
United Technologies
-
United States
-
Aviation and Aerospace Component Manufacturing
-
700 & Above Employee
-
ACE (Achieving Competitive Excellence) Continuous Improvement Manager EMEA
-
2013 - 2015
Managed Quality, Lean manufacturing, and continuous improvement as the leader of EMEA ACE Council, in addition to coordinating all regional councils and relevant UTC ACE network. Provided training and certification of ACE Assessors and development relevant UTC Assessors network. Managed operation transformation projects through implementation of Lean tools, including manufacturing cell design, material presentation, assembly line feeding and routing, sequencing and kitting, integrated production and logistics, line back logistics, and balanced receiving and supplier integration. Spearheaded a strategy for quality and lean manufacturing at the regional level for 200+ sites, including 80+ factories and 120+ business process sites. Implemented effective Train the Trainer strategy fo ACE Certification Program to reach Associate, Practitioner, and Master level. Achieved 100% self-sufficiency status in training and assessments. Show less
-
-
-
Carrier Commercial Refrigeration
-
France
-
Industrial Machinery Manufacturing
-
700 & Above Employee
-
Plant Manager
-
Mar 2010 - 2013
Monitored all operations and processes, prepared operating reports and budgets, and ensured all compliance needs. Developed strategies to increase productivity and production; allocated resources effectively and fully utilized assets to product optimal results. Developed systems and processes that tracked and optimized productivity and standards, metrics, and performance targets to ensure effective return on assets. • Managed 25k unit volume with $180M revenue and full responsibility of P&L and 450 employees, yielding an 86% of employee favourability, 85% EH&S compliance, while reaching the UTC ACE Silver level. • Increased production, assets capacity and flexibility while minimizing unnecessary costs and maintaining current quality standards. • Reduced average labour content by 21% and increased efficiency by 16% with the implementation of a full assembly line and all Lean principles. • Implemented strategies in alignment with strategic initiatives and provided a clear sense of direction and focus. Show less
-
-
-
-
Global Director ACE, Continuous Improvement
-
2008 - 2009
Led the ACE Operating System in Quality, Lean Manufacturing, and continuous improvement in residential and light commercial HVAC business globally. Trained and certified assessors and internal auditors, as well as the development of a network of auditors in cooperation with UTC. Planned and supported R&D for all new products and worked on the qualification protocol for outsourced products. Identified and shared best practices and helped to standardize the skill matrix throughout the business unit. ● Streamlined Quality and Lean manufacturing strategy for 10 manufacturing sites and 19 sales service and distribution sites. ● Deployed Global Business Unit Training strategy through identification, development, and coaching of local talent and delivery methods, resulting in 25,000+ hours of training per year. ● Conducted audits and Lean assessments at supplier sites while leading detailed events for Lean and Quality improvements. Show less
-
-
-
Carrier HVAC
-
Industrial Machinery Manufacturing
-
700 & Above Employee
-
Director Quality & Continuous Improvement EMEA RLCI
-
2006 - 2008
Led the Quality and Continuous Improvement system in Europe, Middle East, and Africa and oversaw production quality and quality system integrity. Coordinated with WHQ of RLCI warranty policy and implemented web-enabled warranty administration system. Managed Lean manufacturing and continuous improvement events with factories and distribution centres. ● Implemented Continuous Improvement strategy throughout the region and initiated cost reduction projects.
-
-
Continuous Improvement Manager EMEA
-
2003 - 2006
Oversaw two divisions for Heating Ventilating Air Conditioning, as well as Commercial Refrigeration, totalling 70 operations, 13k+ employees and $2B in sales. Developed ACE Operating system within the region and developed employee base of ACE Coordinators and Pilots network and ACE Trainer and Assessors. Developed a training plan and submitted reports to WHQ ACE Senior Program Manager and Regional EMEA President.
-
-
Quality Assurance Manager - Villasanta Plant
-
2000 - 2003
Achieved the first site to be recognized on the ACE Silver and Gold level in Carrier EMEA.
-
-
-
Polti Group
-
Italy
-
Consumer Goods
-
100 - 200 Employee
-
Quality Assurance Manager
-
1994 - 2000
Achieved ISO 9000 certification by developing company-wide procedures and quality manual. Achieved ISO 9000 certification by developing company-wide procedures and quality manual.
-
-
-
-
Process Engineer - SPC specialist
-
1990 - 1994
Achieved ISO 9000 certification in Lost Foam Foundry, through the development of manufacturing standard work and quality manual. Achieved ISO 9000 certification in Lost Foam Foundry, through the development of manufacturing standard work and quality manual.
-
-
Education
-
Politecnico di Milano
Master of Engineering - MEng, Mechanical Engineering - Energy -
ITIS P. Carcano
Perito Tessile, Apparel and Textile Manufacture
Community
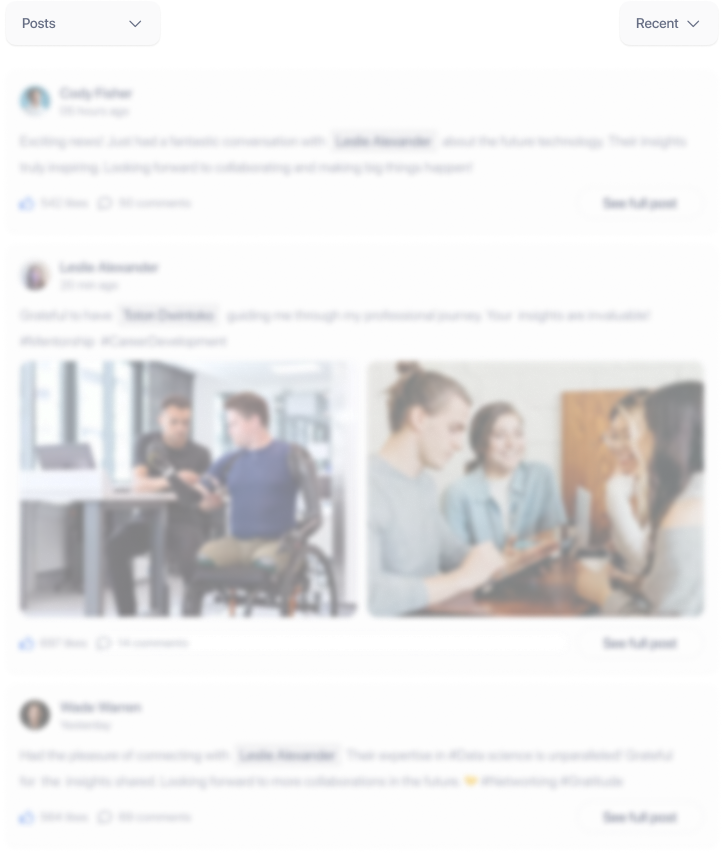