Gregory Finnegan
Production Planner at Joseph Heler Cheese- Claim this Profile
Click to upgrade to our gold package
for the full feature experience.
Topline Score
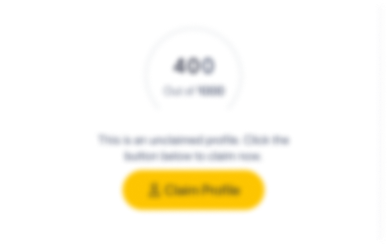
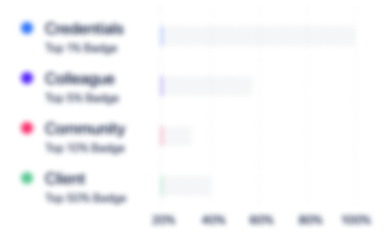
Bio


Credentials
-
Nebs Management Level 3
-
Experience
-
Joseph Heler Cheese
-
United Kingdom
-
Food and Beverage Services
-
1 - 100 Employee
-
Production Planner
-
Apr 2016 - Present
-
-
-
Ornua
-
Ireland
-
Dairy Product Manufacturing
-
700 & Above Employee
-
Planning Scheduler
-
May 2013 - Apr 2016
• Plan production using the company’s planning software to meet demand and customer requirements on a daily basis. • Planning 8-12 Lines daily in an extremely busy factory which produces approximately 1600MT per week on a 3 shift system. • Cover my manager for holidays which requires daily planning of 28 Lines and 500+ SKU’s. • Working closely with demand planner and scheduling team (raw materials) to minimise disruption to the plan. • Produce the best plan possible for production ensuring it is the most cost effective plan and meets the customer and production/business requirements while always focusing on contributing to the 100% service level. As production scheduler I am in constant communication with a wide range of staff within Adams. From Production Director to shop floor teams. I organise and communicate any changes required to the plan with the team managers, team leaders the shop floor and explain why the changes are required. I produce a weekly shift pattern for production covering a 3 shift system.
-
-
-
-
Wastage Co-ordinator
-
Jan 2004 - May 2013
• Recorded Giveaway and trim wastage from Production Lines with monetary gains/losses.• Developed spread sheet to analyse data and to identify problem products.• Drove improvements of poor performing products with support of production teams through equipment on the Lines and root cause investigations and awareness of the costs involved.• Monitored Red and Black bag waste while always actively focusing on reducing these through improvements to the equipment and root cause analysis.• Completed frame analysis of the whole factory and put forward proposal for one area to be utilised, which was approved by Production Director but never put into practice with the change to fixed weight products and guillotine cutters.• Developed presentation to be presented to the IBD for best block utilisation for fixed weight products (block dimensions and weight) with data collated from the lines.Supermarkets moved to fixed weight products which resulted in the need for enormous focus on giveaway and trim, to ensure we remained competitive. I would drive improvements through root cause investigations and the line teams by encouraging them to get involved.
-
-
Manufacturing Team Leader
-
Apr 1999 - Jan 2004
• Production Team Leader – followed company procedures to maintain a safe and productive environment for staff and ensure we produce the best product with quality and pride.• Completed project on changeovers specifically Edam to Gouda – Reducing the time it took and incorporating the changeover into the team and away from the engineers.• Managed 20 – 25 staff over 3-4 production lines.• Completed 2 NEBS management courses – Introductory and Level 3 management. These were run in house with an external facilitator.As Team Leader I managed Holidays, Sickness, Absence, Reviews for around 20-25 team members, also driving 3-4 production lines to be efficient, cost effective and meet all company procedures. Through good communication I kept my Team informed of all company activities. Whilst I was in this role I was also trained to cover the Shift manager for holidays which incorporated putting a staff plan together for 12 production lines and managing the team leaders with any problems that arose.
-
-
Machine operator/Line Leader
-
Apr 1999 - Jan 2004
• Machine Operator/Line leader – setting up the Line for the various orders ensuring all procedures are adhered to.• Clean as you go policy.• Autonomous maintenance at weekends.As a machine operator/line leader I was responsible for ensuring the line ran efficiently and to organise 3/4 staff working on the line also to complete all relevant paperwork for each manufacturing order.
-
-
-
-
Production Operative
-
May 1990 - Apr 1992
• Production Operative – general duties working on a production line. • Production Operative – general duties working on a production line.
-
-
Education
-
Painsley Catholic College
Community
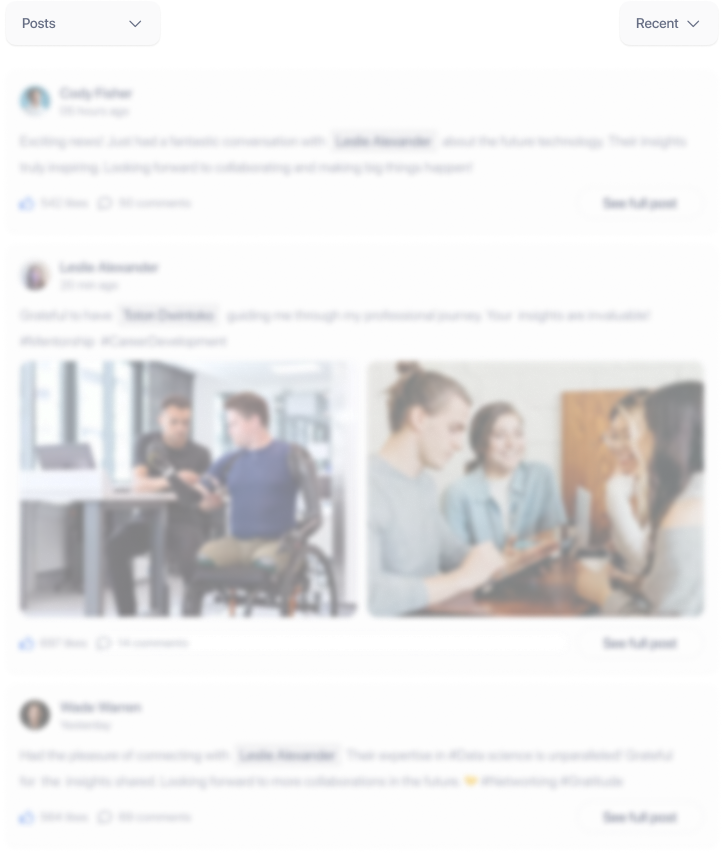