Gregory Mecomber, CMRP
Maintenance & Reliability Consultant at IDCON INC- Claim this Profile
Click to upgrade to our gold package
for the full feature experience.
Topline Score
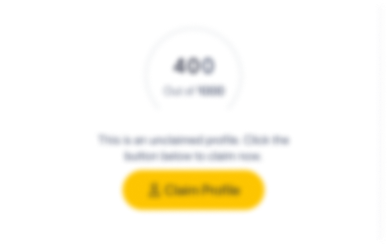
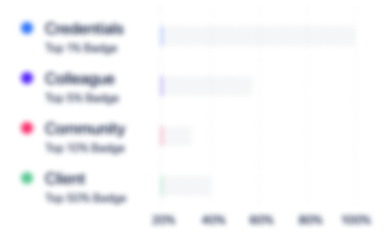
Bio

Luke D. Hamer
Greg combines the operational sense of a seasoned practitioner with the creativity and ingenuity of a novice providing essential agility to navigate the most unique of challenges.

J.R. (Bob) Costello
Gregory Mecomber is a diligent Reliability Engineer who utilizes life cycle management and occupational hazard analysis to increase profitability. Most noted for creating comprehensive life cycle reports, maintaining critical corporate assets and developing effective testing methodologies to predict potential points of failure. He understands the value of life cycle analysis in the overall profitability of a company. Core Qualifications include: Life Cycle Management Point Of Failure Testing Preventive Maintenance Planning In-Depth Data Analysis Equipment Effectiveness Analysis Overall Workplace Efficiency He is responsible for developing the process for tracking and analyzing the life cycle of all critical manufacturing equipment in an oral hygiene setting.

Dallas Hemby
Greg is a great addition to our team. Aside from his excellent maintenance experience, he is also driven, committed, and eager. Greg gives 110% each day! He has represented Aerotek very well and we are lucky to have him on our team.

Luke D. Hamer
Greg combines the operational sense of a seasoned practitioner with the creativity and ingenuity of a novice providing essential agility to navigate the most unique of challenges.

J.R. (Bob) Costello
Gregory Mecomber is a diligent Reliability Engineer who utilizes life cycle management and occupational hazard analysis to increase profitability. Most noted for creating comprehensive life cycle reports, maintaining critical corporate assets and developing effective testing methodologies to predict potential points of failure. He understands the value of life cycle analysis in the overall profitability of a company. Core Qualifications include: Life Cycle Management Point Of Failure Testing Preventive Maintenance Planning In-Depth Data Analysis Equipment Effectiveness Analysis Overall Workplace Efficiency He is responsible for developing the process for tracking and analyzing the life cycle of all critical manufacturing equipment in an oral hygiene setting.

Dallas Hemby
Greg is a great addition to our team. Aside from his excellent maintenance experience, he is also driven, committed, and eager. Greg gives 110% each day! He has represented Aerotek very well and we are lucky to have him on our team.

Luke D. Hamer
Greg combines the operational sense of a seasoned practitioner with the creativity and ingenuity of a novice providing essential agility to navigate the most unique of challenges.

J.R. (Bob) Costello
Gregory Mecomber is a diligent Reliability Engineer who utilizes life cycle management and occupational hazard analysis to increase profitability. Most noted for creating comprehensive life cycle reports, maintaining critical corporate assets and developing effective testing methodologies to predict potential points of failure. He understands the value of life cycle analysis in the overall profitability of a company. Core Qualifications include: Life Cycle Management Point Of Failure Testing Preventive Maintenance Planning In-Depth Data Analysis Equipment Effectiveness Analysis Overall Workplace Efficiency He is responsible for developing the process for tracking and analyzing the life cycle of all critical manufacturing equipment in an oral hygiene setting.

Dallas Hemby
Greg is a great addition to our team. Aside from his excellent maintenance experience, he is also driven, committed, and eager. Greg gives 110% each day! He has represented Aerotek very well and we are lucky to have him on our team.

Luke D. Hamer
Greg combines the operational sense of a seasoned practitioner with the creativity and ingenuity of a novice providing essential agility to navigate the most unique of challenges.

J.R. (Bob) Costello
Gregory Mecomber is a diligent Reliability Engineer who utilizes life cycle management and occupational hazard analysis to increase profitability. Most noted for creating comprehensive life cycle reports, maintaining critical corporate assets and developing effective testing methodologies to predict potential points of failure. He understands the value of life cycle analysis in the overall profitability of a company. Core Qualifications include: Life Cycle Management Point Of Failure Testing Preventive Maintenance Planning In-Depth Data Analysis Equipment Effectiveness Analysis Overall Workplace Efficiency He is responsible for developing the process for tracking and analyzing the life cycle of all critical manufacturing equipment in an oral hygiene setting.

Dallas Hemby
Greg is a great addition to our team. Aside from his excellent maintenance experience, he is also driven, committed, and eager. Greg gives 110% each day! He has represented Aerotek very well and we are lucky to have him on our team.

Credentials
-
Certified Maintenance and Reliability Professionals (CMRP)
SMRPNov, 2019- Nov, 2024 -
ICS-100 Incident Commander System
-May, 2018- Nov, 2024 -
Certified Level 1 Thermographer
Infrared Training CenterAug, 2019- Nov, 2024 -
Certified Electronics Technician, Associate
Electronic Technicians Association InternationalOct, 2014- Nov, 2024 -
Cat 1 Vibration Analysis
Zenco -
Certified Six Sigma Green Belt
Aveta Business Institute -
HP Train To Maintain Jet Fusion 3D 4200 Series
HP -
Level I Machine Lubricant Analyst (MLA)
International Council for Machinery Lubrication (ICML) -
Level I Machine Lubrication Technician (MLT I)
International Council for Machinery Lubrication (ICML)
Experience
-
IDCON INC
-
United States
-
Business Consulting and Services
-
1 - 100 Employee
-
Maintenance & Reliability Consultant
-
Aug 2022 - Present
-
-
-
Diageo
-
United Kingdom
-
Beverage Manufacturing
-
700 & Above Employee
-
Reliabilty Engineer
-
Oct 2021 - Aug 2022
Reliability focused. ISO 9001-2015 Internal Auditor Root Cause and Reliability Centered Maintenance Analysis Process and SOP Improvement Contractor Management Reliability focused. ISO 9001-2015 Internal Auditor Root Cause and Reliability Centered Maintenance Analysis Process and SOP Improvement Contractor Management
-
-
-
DS Smith
-
United Kingdom
-
Manufacturing
-
700 & Above Employee
-
Reliability Engineer
-
Jul 2020 - Apr 2021
-
-
Interim Maintenance Manager
-
Aug 2020 - Jan 2021
-
-
-
SmileDirectClub
-
United States
-
Wellness and Fitness Services
-
700 & Above Employee
-
Laser Safety Officer (Secondary Role)
-
Jan 2020 - Jul 2020
-
-
Maintenance & Reliability Engineer
-
Jan 2019 - Jul 2020
• Institute World Class asset management processes and procedures by applying and driving procedures in identifying, planning, scheduling and executing work.• Perform GAP analysis of existing plant and World Class benchmarks.• Coordinate with maintenance team to implement key metrics to drive asset productivity improvement.• Ensure proper utilization of reliability tools such as PM, PdM and Failure & Risk Analysis to increase production throughput and quality.• Identifies opportunities for reliability performance and cost improvements.• Establishes PM and PdM tasks and frequencies for key process and support equipment.• Conducts RCA on chronic maintenance and repair issues. Initiates corrective actions to equipment design, work practices, etc. based on root cause.• Develop solutions to target improved asset reliability.• Participates in design of new equipment to ensure reliability and maintainability is facilitated into final design.• Develop ongoing replacement analysis program for capital equipment based on work order and preventive maintenance histories, reliability performance and cost.• Performs machine condition and performance assessments.• Ensures machine/equipment manuals are accurate and up-to-date.• Facilitates condition monitoring.• Participates in and conducts failure analysis of failed components correlating with CM data (oil analysis, thermography, etc.).• Creates and distributes failure reports to relevant stakeholders.• Evaluates and recommends for use advanced fault identification tools and non-destructive equipment inspection strategies.• Promotes precision maintenance practices.• Identifies opportunities for and participates in execution of manufacturing excellence projects.• Leads the implementation of enhanced performance-oriented programs (PM/PdM/CM) in existing and new production facilities and processes.• Facilitated the adoption, modification and optimization of the Emaint CMMS system. Show less
-
-
-
Sage V Foods
-
United States
-
Food and Beverage Manufacturing
-
1 - 100 Employee
-
Maintenance Consultant - Contract
-
Jun 2019 - Jun 2019
Advised regarding the development of the maintenance program for the manufacturing facility. Assisted with Asset Hierarchy, Asset Criticality, FMEAs, work flow diagrams and procedures, creation of PM & PdM tasks, goals and metrics. Advised regarding the development of the maintenance program for the manufacturing facility. Assisted with Asset Hierarchy, Asset Criticality, FMEAs, work flow diagrams and procedures, creation of PM & PdM tasks, goals and metrics.
-
-
-
Carlex Glass America, LLC
-
United States
-
Motor Vehicle Manufacturing
-
400 - 500 Employee
-
Controls Technician - Maintenance Supervisor
-
Mar 2017 - Jan 2019
Incident Commander. Maintenance supervisory experience. Project lead. Six Sigma. Maintenance planning & scheduling. Identified opportunity and initiated project which resulted in an increase in annual capacity by 55,300 units. Experience with Fanuc robotics (troubleshooting and programming), Cognex software, FactoryTalk suite, Mitsubishi PLC. Maximo. Incident Commander. Maintenance supervisory experience. Project lead. Six Sigma. Maintenance planning & scheduling. Identified opportunity and initiated project which resulted in an increase in annual capacity by 55,300 units. Experience with Fanuc robotics (troubleshooting and programming), Cognex software, FactoryTalk suite, Mitsubishi PLC. Maximo.
-
-
-
Shiloh Industries
-
United States
-
Motor Vehicle Manufacturing
-
700 & Above Employee
-
Multicraft Maintenance Technician & Reliability Lead
-
Aug 2015 - Mar 2017
- Weld engineer. Project leader. Maintenance trainer. - Proficient at troubleshooting and basic programming with RSLogix500, RSLogix5000. - Proficient at operating and basic programming of Nachi, Panasonic and ABB robots. Experience with robotic welding (MIG, resistance, and sonic). - Troubleshooting Allen Bradley PLC's; SLC 500, Micro Logics, and Device Net. - Analysis of equipment, systems, machinery, robotics throughout the plant. - Troubleshoot and repair electrical, pneumatic and hydraulic systems, press and robotic controls, HMIs. - Maintaining and updating wiring and other diagrams as needed. - Calibrating and testing pneumatic, hydraulic, electrical and robotic sensing devices. - Professional and hard working. Very loyal and willing to volunteer. First Responder, Safety Committee. Show less
-
-
-
IAC Group
-
United States
-
Motor Vehicle Manufacturing
-
700 & Above Employee
-
Industrial Maintenance Technician
-
May 2015 - Aug 2015
- Repair of production equipment from basic hydraulic equipment to performing both electrical and mechanical work. - Maintenance on Boiler, thermoforming, Isocyanate and Polyol (Polyurethane) foam insulation equipment. - Installed, tested, repaired or replaceed cabling or components on machines and designed component assemblies. - Complete understanding of electrical current. (AC and DC, 120v, 240v, 277v, 460v, etc.) - Control circuitry knowledge. (example: relays, timers, thermo couplings, etc.) - Knowledge of PLC’s. (example: Allen Bradley, Omron, Mitsubishi, etc.) - Knowledge of electrical motor starters/drive units. - Located and repaired failures in electrical motors (AC and DC units), connection devices and electro-mechanical equipment. - Performed basic machining, assembly and welding work (mig and stick), as needed, and used machine tools to recondition or modify various pieces of equipment. - Designed equipment control panels, as needed. - Performed power hand tool maintenance. Show less
-
-
-
Schneider Electric
-
France
-
Automation Machinery Manufacturing
-
700 & Above Employee
-
Electronic Wiring Assembly Technician
-
Jan 2015 - May 2015
- Tested performance of electro-mechanical assemblies, using test instruments such as oscilloscopes, electronic voltmeters, or bridges. - Read blueprints, schematics, diagrams, or technical orders to determine methods and sequences of assembly. - Installed electrical or electronic parts and hardware in housings or assemblies, using wiring equipment and hand tools. - Aligned, fit, or assembled component parts, using hand or power tools, fixtures, templates, or microscopes. - Verified part dimensions or clearances to ensure conformance to specifications, using precision measuring instruments. - Repaired, reworked, or calibrated hydraulic or pneumatic assemblies or systems to meet operational specifications or tolerances. Show less
-
-
-
United States Air Force
-
United States
-
Defense and Space Manufacturing
-
700 & Above Employee
-
Civil Engineering Technician
-
Jul 2002 - Sep 2007
-Field Supervisor and Permit Manager for the Civil Engineering Squadron at Travis Air Force Base, CA (2005). Effectively used this opportunity to assess staffing and equipment requirements and operational procedures for short and long term; improving productivity and cutting operational costs significantly. -As Project Manager and Operations Supervisor of tarmac and aircraft runway repair team, oversaw maintenance of the Travis AFB airfield, saving the U.S. Air Force millions of dollars in aircraft repair costs and flight cancellations. -Safety and Hazardous Material Representative for Civil Engineering Squadron at Travis Air Force Base, CA. -Demonstrated attention to detail while assisting in the organization and preparation of work environment, which resulted in minimal discrepancies through many safety, health, and hazardous material inspections. -Pavements maintenance & construction and heavy equipment operator for United States Air Force; -Blue prints. Topographical, road and drainage mapping and surveying. -Responsible for negotiating and purchasing materials for RED HORSE operations in Iraq, Qatar and Afghanistan. -Developed, Organized, and Implemented an improved training program for new enlistees in the Civil Engineering Squadron at Travis Air Force Base, CA. -Effectively Managed and Maintained personnel, training and financial records. -Performed maintenance on equipment hydraulic systems. -Airfield Maintenance, Grounds Keeping (Parks & Golf Course), Civil Engineering and Maintenance (Roads, Sidewalks, Fencing, Drainage Systems, Building Construction and Facilities Maintenance. Show less
-
-
Education
-
Pearl River Community College
Associate's Degree -
Middle Tennessee State University
-
University of California, Berkeley
-
Community College of the US Air Force
Associate's degree
Community
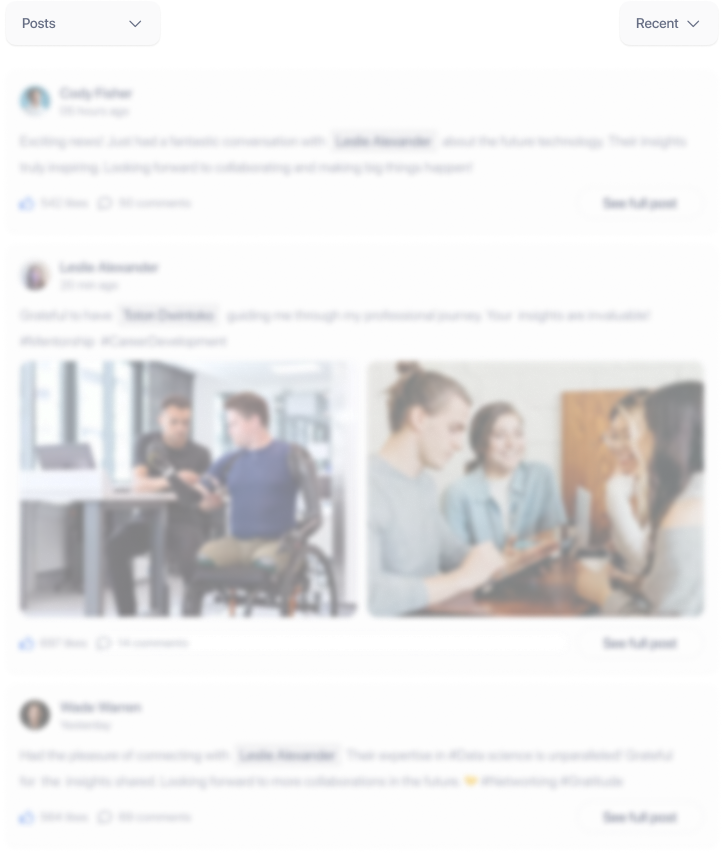