
Greg Paton
Supply Chain Improvement Manager at Foodstuffs North Island Limited- Claim this Profile
Click to upgrade to our gold package
for the full feature experience.
Topline Score
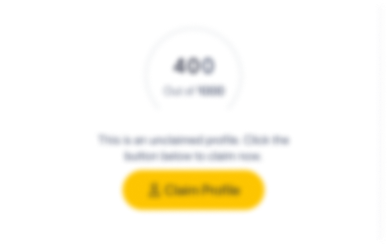
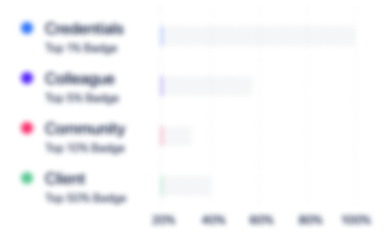
Bio


Credentials
-
PRINCE2® Foundation
AXELOS Global Best PracticeOct, 2022- Oct, 2024 -
PRINCE2® Practitioner
AXELOS Global Best PracticeOct, 2022- Oct, 2024
Experience
-
Foodstuffs North Island Limited
-
New Zealand
-
Retail
-
400 - 500 Employee
-
Supply Chain Improvement Manager
-
Mar 2020 - Present
My role as the Supply Chain Improvement Manager sees the team and me as the Business Process Owner of all the Distribution Centre processes and the configuration of our Warehouse Management System. We are also responsible for the yearly spend and development of the Distribution Centre Roadmap, focusing on continuous improvement and Leading Supply Chain Initiative delivery.By engaging and supporting our Distribution Centre leaders and team, we maintain a customer-driven roadmap to make a real difference to those working within the Supply chain at Foodstuffs North Island.
-
-
Distribution Centre Operation Lead - WMS for the Landing Drive DC
-
May 2019 - Apr 2020
I was the Foodstuffs North Island Lead from a Warehouse Management System Perspective on a Project that saw FSNI build a new purpose-built Ambient Distribution Centre by Auckland Airport. The new DC is the largest Distribution Centre in New Zealand. I was responsible for the Configuration, design and training of the Warehouse Management System processes. I was part of the Wider transition team to ensure a successful transition of Inventory and people from the legacy Distribution centres into their new home. I also led a strong FSNI team who supported the teams as they transitioned to the Landing using the new Warehouse Management System. The opportunity to work on this project is one of my proudest achievements, as there was much pressure to ensure a smooth start for our team members moving to their new home, alongside the complexity of working through the COVID lockdowns. Overall, the outcome of this project was fantastic and saw us successfully mitigate many risks to deliver a WMS Project on time, under budget, with little to no impact on the broader Supply Chain.
-
-
Distribution Centre Operation Lead - WMS
-
Oct 2018 - Feb 2020
As the Distribution Centre Operational Lead, I was the Foodstuffs North Island Lead on a project that saw us replace two legacy systems across 5 of our Distribution Centres, to align all Distribution centres onto one system, one way of working.My role had me overseeing the configuration and design of the new Warehouse Management System and being responsible for the Go-Live activities, and support as each Distribution centre went live with the new Warehouse Management System. I was also responsible for the Project engagement with the broader Stakeholders within the Supply Chain and the wider FSNI business.In this role, I developed Project Management skills and became a Super User of the BlueYonder Warehouse Management Discrete product. I learnt how to effectively deal with people in many different roles and external vendors. I was able to plan the delivery of critical milestones from Project initiation to delivery. Having the opportunity to lead under pressure has helped me become a better decision-maker and boosted my confidence in myself and my own ability.
-
-
DC Operational Planner - WMS
-
Oct 2017 - Oct 2018
My role saw me as part of a project team to replace the legacy Warehouse Management System at our Pilot site with the BlueYonder Warehouse Management Discrete product. I acted as the Inventory subject matter expert and the DC Forklift replenishment and put-away SME.I used my knowledge base to help shape the end to end design of the process and configuration related to my SME area and trained out the use of the new system to our end-users at Foodstuffs North Island.Working as part of a larger team saw me collaborate to develop and implement end to end processes to benefit the entire Supply Chain.
-
-
Operations Manager
-
Aug 2017 - Sep 2017
Operations Manager in an Acting capacity for 6 weeks until a permanent replacement was found.I was responsible for the Operations team consisting of 8 Supervisors, and 50+ employees. My role was ensuring orders were picked in full, presented on time and being of the highest quality.
-
-
Inventory Control Manager
-
Jul 2015 - Aug 2017
Responsible for the control and quality of goods in the DC, ensuring best practise and optimum slotting to improve productivity and accuracy across the DC picking function. I ensure that we have a strong relationship with our Vendors and members so we are working towards the same goals and expectations.
-
-
Inventory Control Supervisor
-
May 2013 - Jun 2015
Leading a team of Inventory controllers across both an Ambient and temperature control Distribution centers.
-
-
Storeman
-
Feb 2008 - May 2013
-
-
Education
-
Universal College of Learning
Sports and Exercise
Community
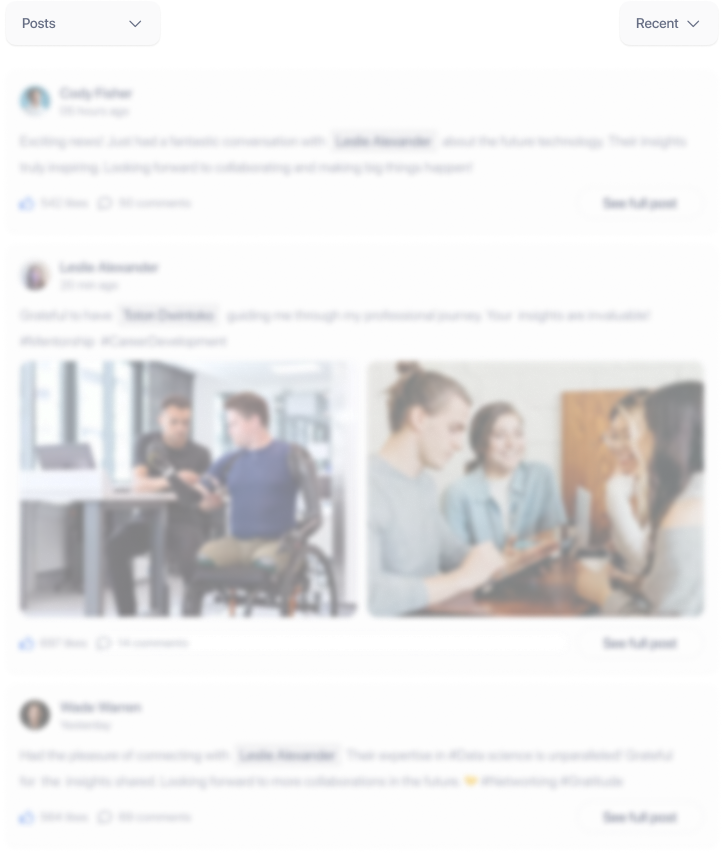