Greg Opalka
Controller at ASI Drives- Claim this Profile
Click to upgrade to our gold package
for the full feature experience.
Topline Score
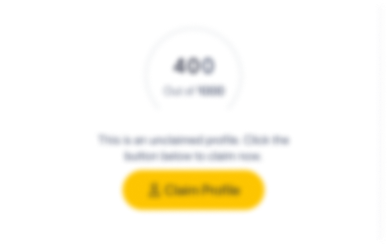
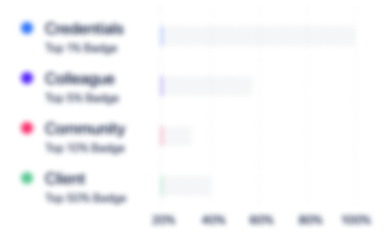
Bio
0
/5.0 / Based on 0 ratingsFilter reviews by:
Experience
-
ASI Drives
-
United States
-
Machinery Manufacturing
-
1 - 100 Employee
-
Controller
-
Jun 2021 - Present
-
-
-
The EF Precision Group
-
United States
-
Medical Equipment Manufacturing
-
1 - 100 Employee
-
Controller
-
Aug 2019 - Jun 2021
-
-
-
NRI, Neptune Research Inc.
-
United States
-
Oil and Gas
-
1 - 100 Employee
-
Controller
-
Apr 2015 - Jan 2018
Manufacturer of composites that restore, protect, and reinforce pipes, pipelines, and civil structures. • Reduced month-end close time from 20 days to 3 by implementing daily reconciliations of Cash, Inventory and other balance sheet accounts. • Successfully led the company through its first financial audit. • Improved the monthly financial package to include analysis of profitability by product line and product. • Analyzed and presented lowest performing items to leadership team… Show more Manufacturer of composites that restore, protect, and reinforce pipes, pipelines, and civil structures. • Reduced month-end close time from 20 days to 3 by implementing daily reconciliations of Cash, Inventory and other balance sheet accounts. • Successfully led the company through its first financial audit. • Improved the monthly financial package to include analysis of profitability by product line and product. • Analyzed and presented lowest performing items to leadership team resulting in $60,000 annual savings by ceasing production of certain products. • Established a Cash Forecast report to anticipate future cash fluctuations and manage line of credit usage. • Fully documented all accounting procedures. Show less Manufacturer of composites that restore, protect, and reinforce pipes, pipelines, and civil structures. • Reduced month-end close time from 20 days to 3 by implementing daily reconciliations of Cash, Inventory and other balance sheet accounts. • Successfully led the company through its first financial audit. • Improved the monthly financial package to include analysis of profitability by product line and product. • Analyzed and presented lowest performing items to leadership team… Show more Manufacturer of composites that restore, protect, and reinforce pipes, pipelines, and civil structures. • Reduced month-end close time from 20 days to 3 by implementing daily reconciliations of Cash, Inventory and other balance sheet accounts. • Successfully led the company through its first financial audit. • Improved the monthly financial package to include analysis of profitability by product line and product. • Analyzed and presented lowest performing items to leadership team resulting in $60,000 annual savings by ceasing production of certain products. • Established a Cash Forecast report to anticipate future cash fluctuations and manage line of credit usage. • Fully documented all accounting procedures. Show less
-
-
-
General Kinematics Corporation
-
Canada
-
Business Consulting and Services
-
Controller
-
May 2011 - Jun 2014
Promoted to Controller from staff accountant position at family-owned custom manufacturing company with annual revenues of $75 million. Transitioned to managing former co-workers by using effective proactive communication skills. Directed team of four. • Reduced month-end close time from over 10 days to five days by changing foreign entities to one month in arrears, implementing more timely cost reporting, and moving appropriate reports from monthly to quarterly basis. • Provided analysis… Show more Promoted to Controller from staff accountant position at family-owned custom manufacturing company with annual revenues of $75 million. Transitioned to managing former co-workers by using effective proactive communication skills. Directed team of four. • Reduced month-end close time from over 10 days to five days by changing foreign entities to one month in arrears, implementing more timely cost reporting, and moving appropriate reports from monthly to quarterly basis. • Provided analysis to leadership team on all aspects of manufacturing, supplying insight and driving better business decisions, resulting in huge cost savings in many departments, such as reducing steel scrap write-off rates from 15% to 4%. • Trained foreign entities on U.S. GAAP, saving time by reducing necessary manipulation of submitted monthly data. • Served on cross-functional team transitioning company to new ERP system, researching and analyzing each department’s process to determine best data communication methods, leading to simpler, centralized system providing consolidated financial data in more user-friendly format for easier analysis. • Introduced notes section on management accounting reports to share comprehensive analysis of key factors causing over or under performance on custom contract jobs, empowering sales department to make better estimates and saving time and money. • Simplified process for analyzing spending on research and development tests, shortening time required to compile data and get information to decision makers.
-
-
Cost Accountant
-
May 2004 - May 2011
• Established excellent working relationships between departments, enabling easier information gathering which led to more accurate costing analysis and better company decision making. • Analyzed production department absorption and chargeable hours by extracting data from system, meeting with manufacturing manager, and uncovering inefficient patterns, allowing manufacturing manager to make decisions that raised production hours and schedule meetings at “off” times which resulted in 20%… Show more • Established excellent working relationships between departments, enabling easier information gathering which led to more accurate costing analysis and better company decision making. • Analyzed production department absorption and chargeable hours by extracting data from system, meeting with manufacturing manager, and uncovering inefficient patterns, allowing manufacturing manager to make decisions that raised production hours and schedule meetings at “off” times which resulted in 20% absorption rate increase. GREGORY T. OPALKA Page 2 • Reduced warranty costs by researching and analyzing root cause of warranty expenditures and creating customer questionnaires and preliminary reporting documents for sales and production department to use for better understanding of custom product design and avoidance of excess warranty costs. • Praised for providing excellent customer service to internal departments. • Received multiple days off for speeding along year-end audit by stepping in for controller and completing almost all work needed for auditors; awarded with gift cards and cash bonuses for beneficial cost-saving analysis.
-
-
Education
-
University of Illinois at Chicago
Bachelor's Degree, Accounting
Community
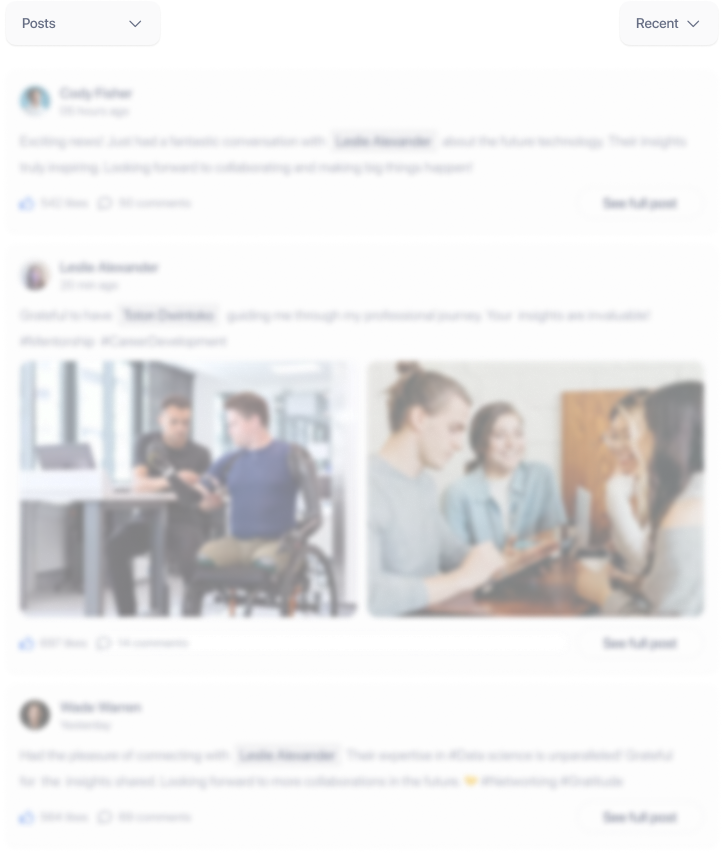