Greg Kramer
Business Development Manager at Industrial Controls and Automation- Claim this Profile
Click to upgrade to our gold package
for the full feature experience.
Topline Score
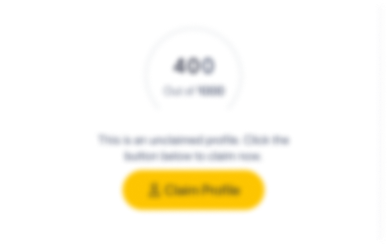
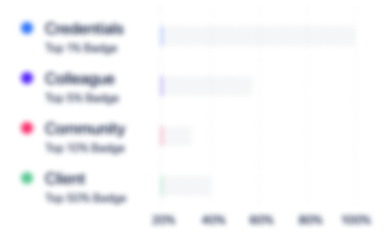
Bio


Experience
-
-
Business Development Manager
-
Sep 2016 - Present
-
-
-
Firestone Industrial Products
-
United States
-
Truck Transportation
-
1 - 100 Employee
-
Senior Customer Quality Engineer
-
Sep 2015 - Sep 2016
-
-
-
Parker Hannifin
-
United States
-
Industrial Machinery Manufacturing
-
700 & Above Employee
-
Quality Manager
-
May 2009 - Jul 2015
Providing Leadership/Quality support and improvement to six Service Center in North America • Achieved initial AS9120 certification with Indianapolis PSC team enabling center to service Aviation, Military, and Defense customers. Winning $60+ Million in business. • Implemented ISO9001 in six facilities, enabling PSC’s to gain new customers and increase market share with existing customer • Led efforts to decrease defect rate from 800+ PPM to 35 PPM, utilizing poka-yoke and yokoten practices. Additionally, reducing Cost Of Poor Quality (COPQ) by 57%. • Achieved Laboratory Control at Source and Designated Quality Representative certification for Indianapolis PSC. Mentored multiple staff members to achieve certification as well. • Led development and implementation of FMEA, Control Plan, and detailed verification procedures, promoting 60%+ sales growth. FMEA used as key tool to manage risk. • Quote/Win Value Add Business in areas such as assembly, kitting, and bagging • Successful transition to new AS9120A requirements Show less
-
-
-
CUMMINS
-
Automotive
-
Senior Quality Engineer
-
Sep 2007 - Apr 2009
Provided Quality Control support and improvement for $500M+ program • Led Advanced Production Quality Planning (APQP) Documentation Preparation and Review • Minimized failures on $15M+ of prototype engines by leading Quality Campaign process • Led Fault Diagnostic, wrote procedures, and provided support on Engine Failures • Led 7 Step Process for Manufacturing Related issues, driving solutions and Error Proofing to APQP Documentation • Utilized Lessons Learned from daily Alpha and Beta Builds, driving additional solutions and Error Proofing to APQP Documentation • Team approach and projected $100’s of millions cost avoidance/savings over life of program Show less
-
-
-
-
Quality Manager and Environment, Health and Safety Engineer
-
Aug 2004 - Jul 2007
Provided Quality System leadership and direction for all aspects of business serving customers including Toyota, Honda, Subaru, Nissan, Mazda, and GM. Coordinate EH&S activities including: investigation, correction, training associates, and follow-up • Elimination of Warranty Cost with Toyota, resulting in annual savings in excess of $200K • 80% scrap reduction for key product on new high speed production lines during launch • Led QS/ISO Surveillance Audits from 18 findings to repeated “Zero Finding” Audits • Benchmark supplier representative on Kaizen team with Toyota • 90% reduction in Cost per Recordable Incident from $5000 to less than $500 per incident • 25% reduction in Workman’s Compensation Insurance Premium • Utilized Problem Solving Tools such as 7 Step and 5 Why which contributed to reducing the Recordable Incident Rate from 19.5 to 9.5 in 12 months • Initiated Stretching Program and Safety Audit Improvement efforts which also contributed to reducing the Recordable Incident Rate from 19.5 to 9.5 in 12 months • Led development of new associate testing and training reducing new associate Recordable Incident Rate 65%, which also contributed to reducing overall Recordable Incident Rate • Prepared and Submitted required EPA reports with Zero Issues • Identified and Corrected past EPA Submission Errors with no penalty to company Show less
-
-
-
ARVINMERITOR
-
United States
-
Motor Vehicle Manufacturing
-
Process and Quality Engineer
-
Aug 1999 - Aug 2004
Jeep and Dodge Exhaust Systems Provided Quality System leadership and direction primarily for Jeep product line • Exceeded Part Per Million (PPM) Improvement Goal reducing PPM to Zero and maintaining • Led Label Error Proofing efforts, developing 4 key scenarios and procedures which were recognized and subsequently mandated to be used worldwide by Corporate Quality • Provided Process Sign Off (PSO) and line side support for multiple new customer launch projects including Jeep Liberty and Dodge Durango • Facilitated Employee Involvement (EI) Team to World Class Level • Utilized S3 tools and led changes for quality and cost improvements Advanced Production Planning Team (APPT) Quality Engineer Provided prompt Quality Engineering and Improvement Support for multiple programs and suppliers in multiple locations including Shanghai, Toronto, and various US locations • Coordinated and led QS-9000 Certification for Taylor, MI facility • Facilitated Continuous Improvement (CI) efforts of EI Teams for production lines in Dexter, MO and Canada to achieve Best In Class and World Class line status • Led APQP efforts and line development with launch of GM exhaust in Shanghai, China Show less
-
-
-
Keihin North America, Inc
-
Motor Vehicle Manufacturing
-
1 - 100 Employee
-
Process Engineer
-
1997 - 1999
-
-
Education
-
Ball State University
BS, Manufacturing Engineering -
Villanova University
Certificate, Six Sigma
Community
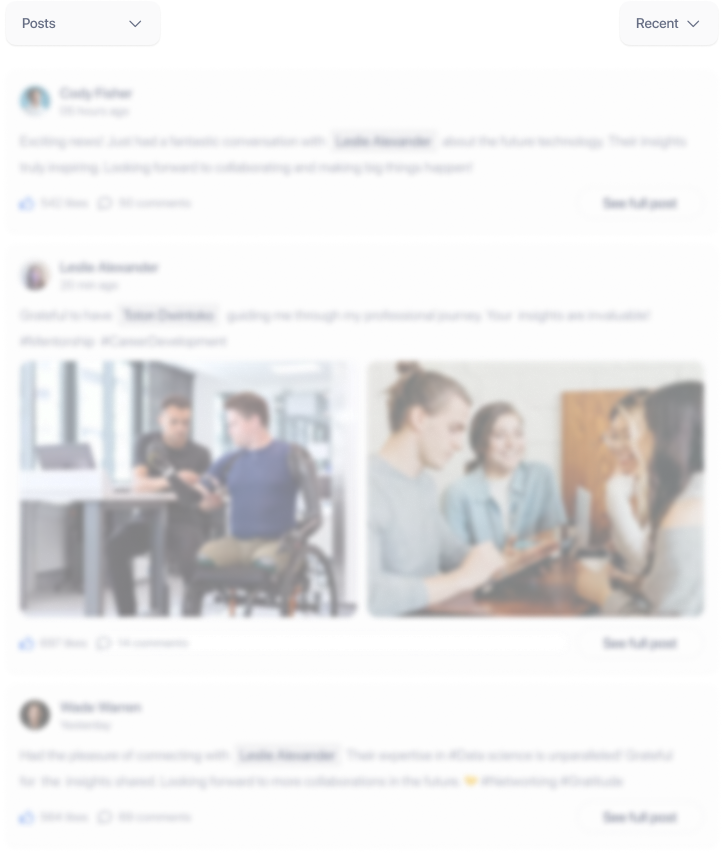