Grant Coleman
Field Service Engineer at MDI Medical Ltd- Claim this Profile
Click to upgrade to our gold package
for the full feature experience.
Topline Score
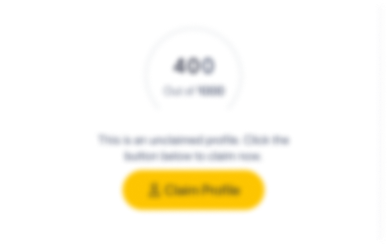
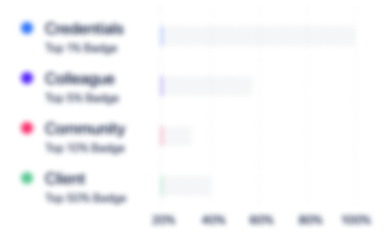
Bio


Experience
-
MDI Medical Ltd
-
Ireland
-
Medical Device
-
1 - 100 Employee
-
Field Service Engineer
-
Nov 2017 - Present
Supporting customers' ultrasound, patient monitoring and information systems. Supporting customers' ultrasound, patient monitoring and information systems.
-
-
-
RSL Medical
-
Ireland
-
Customer Support Engineer
-
Dec 2000 - Apr 2017
RSL Medical supply, install and maintain a range of medical imaging systems and associated equipment, including CT (CAT Scan), MRI, X-ray, ultrasound and Dental systems for the HSE, private hospitals and clinics, and the IPS. Responsible for: • Installation, upgrades, calibration and maintenance of CT, X-ray, Mammography, Ultrasound and Dental systems, included support of time critical sites such as Accident & Emergency Radiology Departments. • Preparation and delivery of operational and technical training courses.
-
-
-
SFK Systems A/S
-
Denmark
-
Machinery Manufacturing
-
1 - 100 Employee
-
Sales/Service Engineer
-
Sep 1999 - Nov 2000
SFK (Haarslev) manufacture, sell and maintain production systems and equipment for the slaughtering and meat processing industries. Responsible for the Production Tracking Management Systems which consist of: an NT server, a fibre optic network, industrial (IP65 rated) PCs on the factory floor, data input and output equipment including weighing scales, barcode scanners, animal grading equipment, PLC controllers, and thermal and office printers. SFK (Haarslev) manufacture, sell and maintain production systems and equipment for the slaughtering and meat processing industries. Responsible for the Production Tracking Management Systems which consist of: an NT server, a fibre optic network, industrial (IP65 rated) PCs on the factory floor, data input and output equipment including weighing scales, barcode scanners, animal grading equipment, PLC controllers, and thermal and office printers.
-
-
-
Videojet Technologies
-
United States
-
Printing Services
-
700 & Above Employee
-
Customer Service Engineer
-
Sep 1998 - Sep 1999
Videojet and Marsh printers are industrial inkjet printers used for product marking and coding in the manufacturing and packaging processes. • Printers included pneumatic, hydraulic, electrical and electronic systems. Responsible for: • Installation (including production line interfacing), upgrades and maintenance of printers. • Preparation and delivery of operational and technical training courses. Videojet and Marsh printers are industrial inkjet printers used for product marking and coding in the manufacturing and packaging processes. • Printers included pneumatic, hydraulic, electrical and electronic systems. Responsible for: • Installation (including production line interfacing), upgrades and maintenance of printers. • Preparation and delivery of operational and technical training courses.
-
-
-
Domino (Australia) Pty Ltd
-
Castle Hill, NSW, Australia
-
Senior Technical Engineer
-
Jan 1997 - Jul 1998
Domino printers are industrial inkjet printers used for product marking and coding in the manufacturing and packaging processes. • Printers included pneumatic, hydraulic, electrical and electronic systems. Responsible for: • Installation, upgrades and maintenance of inkjet printers and systems. • Preparation and delivery of operational and technical training courses. • Specification, testing and installation of new software and upgrades into printers and printer control systems. • Test and verification of data communications between computer systems and printers. • Repairs of PCBs to component level. • Acting National Technical Manager as required. Achievements: • Designed, developed, assembled, installed, tested and documented a synchronising interface for multiple printers for production line use. • Developed and assembled a test rack for testing PCB’s and controlling a print test rig for testing new software. • Assessed and reported on the technical and sales requirements of the Viscanner range of vision systems as a possible product range for distribution in Australia.
-
-
-
CARDCORP Pty Ltd.
-
Seven Hills, NSW, Australia
-
Service Manager
-
Feb 1995 - Jan 1997
CardCorp manufacture plastic cards and sell and service embossing machines, thermal printers for personalising plastic cards and automated mail insertion systems. • Printers, embossers and mailing systems included electro-mechanical, electrical and electronic systems. Responsible for: • Scheduling & allocation of service calls. • Liaison with equipment manufacturers for implementation of specialised customer applications. • Installation, upgrades and maintenance of Thermal printers and embossers. • Programming of printer and embosser layouts. • Test and verification of data communications between computer systems and printers/embossers. • Preparation and delivery of operational and technical training courses. • Stock control & ordering of consumables and spare parts. Achievements: • Developed and implemented spare parts tracking, inventory and storage systems. • Developed and implemented parts order tracking system. • Improved customer service.
-
-
-
Techcomm Pty Ltd.
-
Chippendale, NSW, Australia
-
Customer Service Engineer
-
Mar 1986 - Jan 1995
Site Engineer: The Reserve Bank, Sydney, NSW, Australia. 1994 – 1995. • Maintenance of REI Currency Verification & Counting Systems. Site Engineer: American Express, North Ryde, NSW, Australia. 1991 – 1994. • Maintenance of REI Trace 1000 Document Reader/Sorters. ◦ High speed (2000 documents per minute) systems that included pneumatic, hydraulic, electro- mechanical, electrical, electronic and computer systems. • Maintenance of IBM PS/2’s and other PC’s, IBM terminals. Achievements: • Improved average OCR read rate, for Trace 1000, from less than 50% to 95%. • Adapted the inkjet system by installing ink filtration to extend inkjet nozzle life from less than 1 month to beyond 15 months. (The manufacturers specified inkjet nozzle lifetime was 3 months.) • Significant reduction in downtime achieved. • Developed and documented PCB repair procedures for common faults. Customer Service Engineer 1986 – 1991. • Installation and maintenance of mainframe, mini and personal computer systems, printers, plotters, scanners. Achievements: • Developed and documented repair procedures for common PSU faults.
-
-
Education
-
Dublin Institute of Technology
Certificate (Level 7), eBioPharmaChem -
Waterford Institute of Technology
Bachelor of Science (BSc), Information Technology
Community
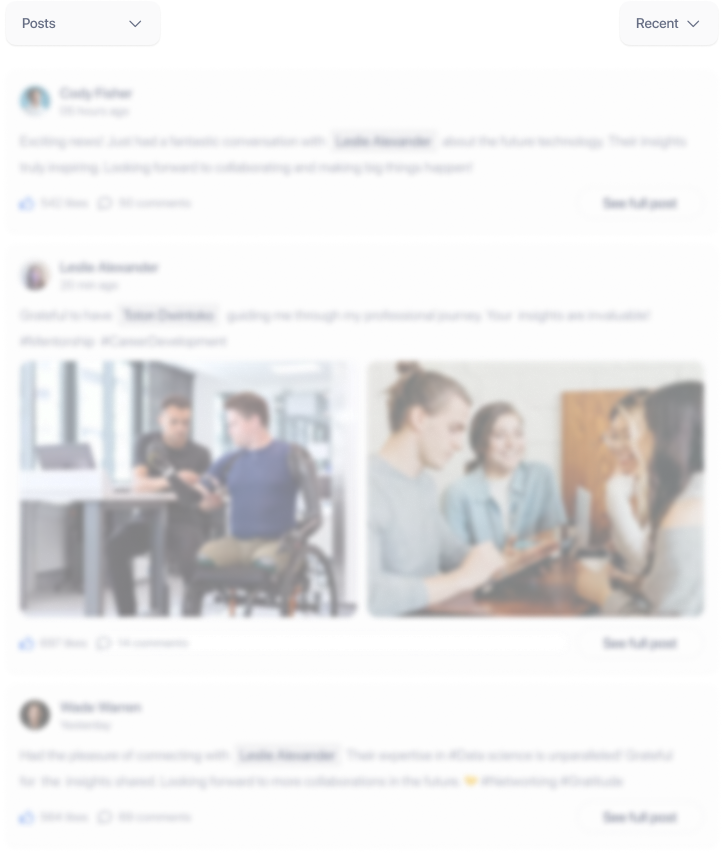