
Jonathan Graham
Product Support Engineer at Orthoscan Inc.- Claim this Profile
Click to upgrade to our gold package
for the full feature experience.
Topline Score
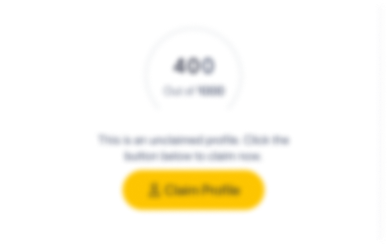
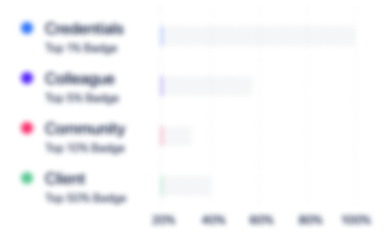
Bio


Experience
-
Orthoscan Inc.
-
United States
-
Medical Equipment Manufacturing
-
1 - 100 Employee
-
Product Support Engineer
-
Aug 2022 - Present
-
-
-
WestRock Company
-
United States
-
Packaging and Containers Manufacturing
-
700 & Above Employee
-
Field Service Engineer
-
Sep 2016 - Aug 2022
Field Service Engineer responsible for company owned automated equipment located at client sites within United States, Canada & Mexico. Scope includes system installation, setup & configuration, calibration, testing, preventive maintenance, inspection, troubleshooting, fault isolation, diagnosis, repair, provide system operational & technical training. 120v/240v/480v, low-voltage, Program Logic Controllers (PLC), PC, networking, pneumatic, CANBUS, etc. Field Service Engineer responsible for company owned automated equipment located at client sites within United States, Canada & Mexico. Scope includes system installation, setup & configuration, calibration, testing, preventive maintenance, inspection, troubleshooting, fault isolation, diagnosis, repair, provide system operational & technical training. 120v/240v/480v, low-voltage, Program Logic Controllers (PLC), PC, networking, pneumatic, CANBUS, etc.
-
-
-
Orthoscan Inc.
-
United States
-
Medical Equipment Manufacturing
-
1 - 100 Employee
-
Field Service Engineer (Contract)
-
Jun 2015 - Jun 2016
Field Service Engineer responsible for equipment located in United States & US territories, with 48 hour response time. Performed onsite technical troubleshooting, repair & calibration of medical mobile mini-c arm x-ray units to manufacturer standards, including mechanical, electrical, software & networking components. Provided assistance, training and instruction as required to clinical staff & biomedical engineers. Completed repair documentation as required by facility, manufacturer & FDA. Field Service Engineer responsible for equipment located in United States & US territories, with 48 hour response time. Performed onsite technical troubleshooting, repair & calibration of medical mobile mini-c arm x-ray units to manufacturer standards, including mechanical, electrical, software & networking components. Provided assistance, training and instruction as required to clinical staff & biomedical engineers. Completed repair documentation as required by facility, manufacturer & FDA.
-
-
-
Orthoscan Inc.
-
United States
-
Medical Equipment Manufacturing
-
1 - 100 Employee
-
Sales Coordinator
-
Jun 2012 - Oct 2014
* Assist 34 international distributors with medical regulatory approval process* Facilitate foreign language translation and implementation for Graphic User Interface as well as operator manuals* Administrate VA & DOD contracts & procurement requests* Administrate Group Purchasing Organization contracts & procurement* Review & submit Requests For Quotes & Requests for Bids* Manage imaging for orthopedic implant labs* Assist Engineering with product releases* Advise on product improvement & assist with implementation* Oversee X-ray unit final quality checks* Manage Expense Reporting for Sales team of approx 25.
-
-
Technical Service Representative / Field Service Engineer
-
Dec 2010 - May 2012
* Provide front line end user support for Medical X-ray (Radiologists, Physicians, Clinicians)* Provide technical support for BioMedical Engineers & service technicians* Remotely troubleshoot as required* Plan field service repair visits: including scheduling personnel, parts ordering & shipment, travel & followup as required. * Manage database of logged service issues. * Administrate service contracts. * Performed Field Service Technician functions (onsite repair)
-
-
-
-
Owner / Operator
-
2007 - 2009
Started Paver Installation Division at UpGrade. Managed all facets of a small construction business, from consulting with customers, quoting, planning, and paver installation for commercial & residential design applications. ICPI certified. Sold business in 2009. Started Paver Installation Division at UpGrade. Managed all facets of a small construction business, from consulting with customers, quoting, planning, and paver installation for commercial & residential design applications. ICPI certified. Sold business in 2009.
-
-
-
Independence Air
-
Airlines and Aviation
-
1 - 100 Employee
-
Aircraft Maintenance Controller
-
2002 - 2006
* Establish and oversee the completion of assignments by Maintenance personnel working on active aircraft at gate and hangar operations. Redirect work assignments as required. Supervise on-call maintenance personnel contracted to perform maintenance and return to service aircraft.* Provide technical knowledge and logistical support to Maintenance and Flight Crews for active fleet Maintenance Discrepancies, Minimum Equipment List (MEL), Configuration Deviation List, and "Re-Schedules" to determine proper and timely corrective action.* Coordinate with Maintenance, Flight Dispatch, Maintenance Planning, Stores, Engineering, and Inspection, providing current and continuing follow-up to ensure positive corrective action is made as promptly as possible for scheduled and unscheduled maintenance.* Authorize the use of "on-call maintenance" personnel to return aircraft to service, complying with MEL Maintenance Procedures or perform inspections for ferry flights.* Oversee and coordinate aircraft Ferry Flights for the Maintenance Department.* Authorize aircraft ferry flights to recover aircraft grounded at outstations and to relocate parts for aircraft requiring maintenance.* Maintain continuous liaison with Flight Dispatch while providing current and continuous reports of general technical status of the entire fleet. Coordinate maintenance requirements during irregular operations in an effort to minimize costs and disruptions.* Collect and provide information on all daily cancellations and delays resulting from Maintenance or Stores related problems to complete daily Flight Interruption Reports.* Process deferrable items in accordance with the policies and procedures in the General Maintenance Manual. * Ensure MEL Deferred Item status is current and within time limits authorized by MEL.
-
-
-
United Airlines
-
United States
-
Airlines and Aviation
-
700 & Above Employee
-
Aviation Maintenance Technician
-
1995 - 2001
* Airframe & Powerplant Technician* Qualified on all United Airlines fleet aircraft: 727,737,747,757,767,777, A319,A320, DC-10* Qualified on all systems/specialties, including: Electrical, Navigation, Engine, Pneumatic, Environmental, Hydraulic, Structural* Perform routine & non-routine maintenance, base maintenance (C-checks), Line Maintenance (1,2,3-service). * Performed upgrade Lead Technician duties at Washington Dulles (IAD) International Gates. * Maintained logbook entries* Aircraft release qualified. * Responsible for aircraft pushback & de-icing as required.
-
-
Community
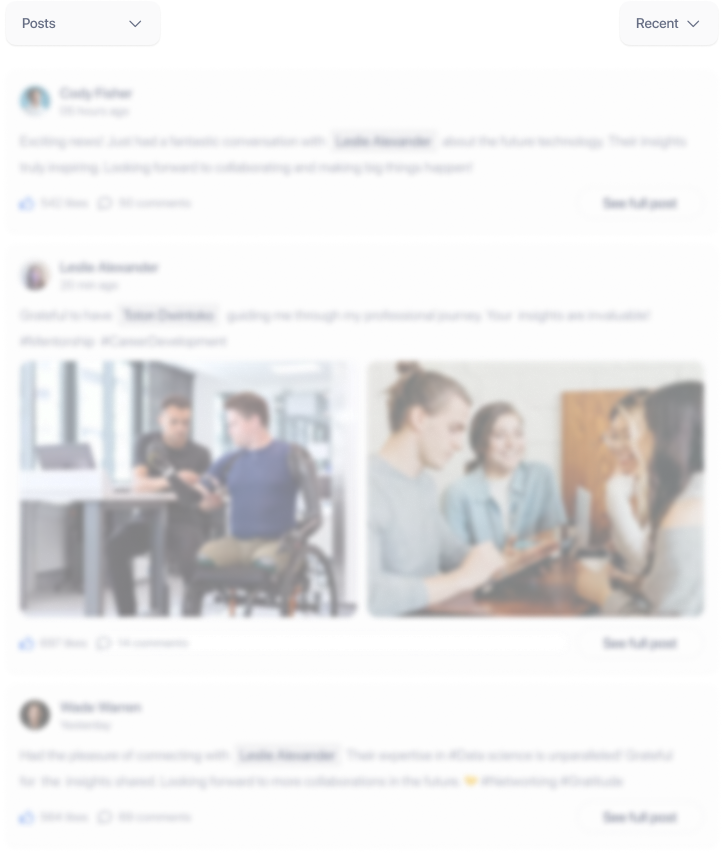