
Graham Kennedy
President at AlliedOne Industrial Inc- Claim this Profile
Click to upgrade to our gold package
for the full feature experience.
Topline Score
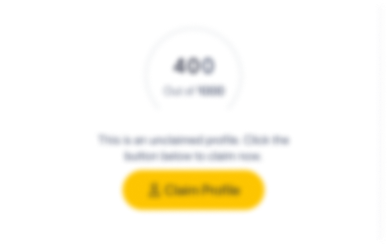
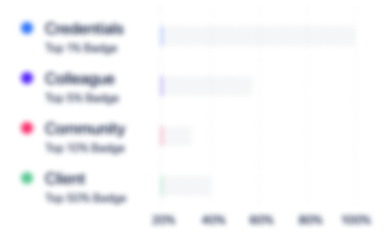
Bio

LinkedIn User
Graham is extremely professional, shows clear thinking and rigor, and master rapidly the essential aspects of driving successful projects.

Mark Doyle
I have had the distinct opportunity to work collaboratively with Graham for a number of years as a co-working in another department. I found Graham to be collaborative, responsive and professional in all of our dealing. Graham’s attention to detail and drive to accomplish combined goals helped the relationship between our two areas of responsibility. He is a good leader, coordinator and communicator. Thus, I am happily providing my personal recommendation for Graham.

LinkedIn User
Graham is extremely professional, shows clear thinking and rigor, and master rapidly the essential aspects of driving successful projects.

Mark Doyle
I have had the distinct opportunity to work collaboratively with Graham for a number of years as a co-working in another department. I found Graham to be collaborative, responsive and professional in all of our dealing. Graham’s attention to detail and drive to accomplish combined goals helped the relationship between our two areas of responsibility. He is a good leader, coordinator and communicator. Thus, I am happily providing my personal recommendation for Graham.

LinkedIn User
Graham is extremely professional, shows clear thinking and rigor, and master rapidly the essential aspects of driving successful projects.

Mark Doyle
I have had the distinct opportunity to work collaboratively with Graham for a number of years as a co-working in another department. I found Graham to be collaborative, responsive and professional in all of our dealing. Graham’s attention to detail and drive to accomplish combined goals helped the relationship between our two areas of responsibility. He is a good leader, coordinator and communicator. Thus, I am happily providing my personal recommendation for Graham.

LinkedIn User
Graham is extremely professional, shows clear thinking and rigor, and master rapidly the essential aspects of driving successful projects.

Mark Doyle
I have had the distinct opportunity to work collaboratively with Graham for a number of years as a co-working in another department. I found Graham to be collaborative, responsive and professional in all of our dealing. Graham’s attention to detail and drive to accomplish combined goals helped the relationship between our two areas of responsibility. He is a good leader, coordinator and communicator. Thus, I am happily providing my personal recommendation for Graham.
0
/5.0 / Based on 0 ratingsFilter reviews by:
Credentials
-
PFSA INTRODUCTION INTO FOOTBALL SCOUTING
Professional Football Scouts Association (PFSA)Jun, 2020- Sep, 2024 -
PFSA LEVEL 1 TALENT IDENTIFICATION IN FOOTBALL
Professional Football Scouts Association (PFSA)Jun, 2020- Sep, 2024 -
AS9100D - LEAD AUDITOR - PROBITAS AUTHENTICATION CERTIFIED
SAI Global AssuranceFeb, 2017- Sep, 2024 -
Lean Six Sigma Black Belt
Villanova UniversityAug, 2008- Sep, 2024
Experience
-
AlliedOne Industrial Inc
-
Canada
-
Aviation and Aerospace Component Manufacturing
-
1 - 100 Employee
-
President
-
Apr 2018 - Present
o Responsible for all Operational activities, fiscal budgets, P & L, and overall ethos of the company.o Establish objectives for the company and formulate or approve policies and programs· Authorize and organize the establishment of major departments and associated senior staff positions.o Allocate human and financial resources to implement company policies and programs; establish financial and administrative controls; formulate and approve promotional campaigns; and approve overall personnel planning.o Select executive staff including Directors, Managers, and other key stakeholder roles.o Co-ordinate working departments.o Represent the company in negotiations or other official functions.o Manage the manufacturing department and provide direction related to overall requirements and managing costs and timelines.o Directing production and manufacturing staff for optimizing productivity.o Provide direction to the team developing key operational processes and participate in review and approval.o Training, mentoring, and coaching of managers so that they can then provide clear objectives to their teams.o Overseeing all quality control and quality assurance teams for validating conformance and compliance and configuration control.o Responsible for the design and development of business layout, strategic planning, and capital purchases.o Overall manager of the organization for sales and customer relations.
-
-
Director, Quality & Continuous Improvement
-
Apr 2017 - Apr 2018
Coach and Mentor leadership team through Control of Work Transfer. Manage and maintain Multi Site AS9100 audits. Harmonize leadership through Lean Transformation focusing on AS9100D Interaction Of Process activities. Launch Design Of Experiments (DOE), Analysis Of Variance (ANOVA) through machine capability studies. Group Technology, Part Families and Concurrent Engineering Principles in play using Statistical Analysis and 100% Floor Patrol In Process Inspecion. In conjunction to the DOE, Measurement System Analysis (MSA) and Gauge R & R studies contribute to the collection of data required culminating in true Standard Work practices. Layered Process Audits combined with In Process Quality Gate Checklists are added to augment the AS9100 Measurement Of Processes and Product.
-
-
-
2Source Manufacturing Inc.
-
Canada
-
Aviation & Aerospace
-
1 - 100 Employee
-
Quality Assurance Quality Control Manager
-
Oct 2016 - Jan 2017
-
-
-
BOMBARDIER
-
Canada
-
Aviation and Aerospace Component Manufacturing
-
700 & Above Employee
-
Site Leader
-
Jun 2014 - Nov 2014
Operations: Roll out new Xizi site. Mentor supplier VP's, GM's and senior staff. Using AES, drive metrics and corporate continuous improvement culture. Implement line side schooling activities driving behaviour setting objectives to meet strategic goals. Successful transition and launch of the Q400 Strake. Assist in the development of key personnel at the supplier site. Host dignitaries and develop effective communication tools for host site launch. Represent BA partners Honeywell, for Critical path mitigation while in China. Quality: Q400 China Supplier development /M2B/B2B implementation to achieve Q400 Cost and EBIT targets. Support the launching and development of new Chinese Suppliers for the Q400 and C Series through mentoring, coaching, problem solving, corrective action implementation and quality gates to protect Toronto site. Run the business through AES. Focus on driving tangible business results across Operations through the integration of AES as a critical part of day-today business. Rigorously implement fundamental AES tools (eg, DMM, Weekly PSS, Process Confirmation,etc.) across the business. Maturity assessment achievement per glidepath. Develop Chinese Local and regional Quality teams as well a Chinese Supplier Development activity. Implement a strong China supplier Quality team on site in China and a strong SACC, TQM and Xizi Quality management teams. Develop local BA Quality Directors, Managers and staff to support both your Supplier Development and SACC priorities. Develop strong relationships, skills, techniques and measure effectiveness of talent by skills and responsibility matrices. Working with BA and host sites HR, develop skills matrices and competency framework. Performance Improvement and Sustainability: Reduce COQ and Quality Disruption from SACC. Transition SACC and Xizi to full CAB responsibility. Benchmark processes and systems with C Series Quality in China. Develop harmonized strategy with C Series and Supply Chain teams.
-
-
Manager, Quality & Achieving Excellence
-
Jan 2012 - Jun 2014
Responsible for the EJS Equipping, Joining and Stuffing for the Q400 in Shenyang SACC and transition of First Article to Toronto. Manage a target team of Fuselage Specialists to teach Chinese operators the required behaviours for success. As a senior management representative, report out weekly to home site as well as host quarterly PMR or PRM. Utilizing Masterplan and visual management tools, host daily operations reviews with Toronto site and Chinese senior management ops reviews. Daily interactions with VP of Operations, VP of Engineering and VP of Quality for full Policy Deployment at China site. Successful transition for interface and integration of Q400 AVIC SACC First Article. Manage transportation of First Article from Shenyang, Dalian, Los Angeles to Toronto. Verify transportation on location at all ports.
-
-
Manager, Quality - Aerostructures & Intersite China
-
May 2010 - Apr 2014
Manage the Intersite transition of Quality from Belfast to Toronto in China. Work to and implement strong QMS applications. Develop performance objectives. Share objectives with Director of Quality at home site. Achieve corporate goals. Utilize Balanced Scorecard objectives. Change behaviors and mindsets. Quality and Lean transformation: Implement Lean Tools and Techniques via the Bombardier Achieving Excellence System and framework. Implement true root cause and corrective action tools and techniques. Develop clear metrics, visual management tools and deployment through a matrix environment and IPT structure. Roadmaps created and aligned. Top down Bottom up implementation. Enablement and Engagement key here. Employee Feedback, DMM, PMP, PDP, Masterplans, Single Page Lessons, Quality Gates, Problem Solving and Value Stream Mapping are some of the current tools employed here in China. FTT or First Time Through and Group Technology deployment, realization and reporting as well as Concurrent Engineering as part of work scope.Work to and within parameters of BA QMS and TC and EASA regulatory requirements as well as NADCAP for Special Processes.Work within a global environment nurturing new talent. Support business processes and requirements.Overall major cultural shift.
-
-
-
Noranco Inc
-
Canada
-
Airlines and Aviation
-
1 - 100 Employee
-
Director, Continuous Improvement
-
Jan 2009 - May 2010
Coordinate multi site budgets, headcount and cost reduction strategy.Manage B.O.S reporting to President Lean Transformation.5S Deployment: three sites
-
-
Director, Quality & Business Improvement
-
Jul 2007 - Dec 2008
Maintain and improve organizational compliance to the Quality Management System processes and AS9100 B.Deploy and maintain regulatory requirements.Manage and drive Corrective Action Board (CAB) activity to monitor non-conformance levels, overdue corrective actions and improve effectiveness of problem solvingFormulate and maintain quality objectives complementary to corporate policies and goals recognizing the principles of Lean Manufacturing EnterpriseDevelop and initiate standards and methods for inspection, testing and evaluation.Responsible for providing qualified resources for quality activities to achieve continuous improvement in quality, productivity and cost, including all supervision and administration of quality department personnel.Develop and implement ANDON and Pull.Incorporate InProcessInspection. Develop Customer Satisfaction Survey and metric.Develop and implement Receiving Inspection.Implement QA Map using Process Management.
-
-
-
Messier-Bugatti-Dowty
-
France
-
Business Consulting and Services
-
1 - 100 Employee
-
Supplier Quality Technical Lead/Manager
-
Aug 2006 - Jun 2007
Manage all day-to-day aspects of Supplier Quality (Assembly Shop, Test & Receiving Inspection) recognizing Lean Enterprise.Manage various Continuous Improvement/Kaizen projects and Lean Events. Responsible for MDI Assembly Shop Continuous Improvement as part of global Accelerated Lean Platform.Manage Messier Dowty Kaizen NewspaperLiaise with suppliers on key Quality issues to ensure technical issues are identified and validated.Lead Lean Teams through various business functions in order to problem solve and provide resolution/validation. (8 steps to problem solving, 8DProblem Resolution Reporting)Manage projects related to AS9102, AS9103 (i.e. Key Interface Dimension Project), focusing on the reduction of customer escapes.
-
-
Program Quality Engineer
-
Aug 2004 - Jul 2006
Manage all Program Quality activities through Integrated Product Team (IPT)Transfer work package from Singapore. Manage/Coordinate LAI (Last Article Inspection) at Messier-Dowty SingaporeCo-ordinate all customer Engineering activity for purpose of Configuration ManagementManage all aspects of First Article Inspection as the customer delegated authority.Customer delegated MRB.
-
-
-
-
W & MP Team Lead
-
Jul 2003 - Jul 2004
Manage & Schedule all work packages pertaining to Canadair Cockpit for Refurbishment Program.Work Package 3 (Systems) Integration Supervisor/Coordinator for B/A on-site in Wichita. Complete aircraft.Co-ordinate all new Engineering and Methods Planning. (MCG's, DCP's)Liaison between Management and Production floor in order to maintain, plan and crew load scheduled work.Provide knowledge and expertise in the field of Procurement and Quality and the procedures to be followed in regards to responsibilities of Suppliers as per the Bombardier Quality SystemEnsure integrity of Manufacturing System and also Quality procedures are maintainedImplement new procedures for Quality tracking of parts. Six Sigma Ref QDI W1025-4-14.1QC MRB for all outstanding RNC's on Canadair Cockpit and Work Package 3 work share.Six Sigma Management Team member VNCMS project. (Vendor Non-Conformance Management System). Audits carried out Detroit, Wichita, and Mississauga.
-
-
Team Lead (Coordinator)
-
2003 - 2004
Manage RE & RE for first Global Express 5000 (AC 9127) Toronto. Manage Quality MRB, Work & Material Planning and other disciplines for Canadair Cockpit on the BD100 line in Wichita, Kansas. Coordinate refurbishment effort. (Hangar Layout-two aircraft, Break of Inspection activity and Manage, Design Return To Vendor procedure (Six Sigma Group).
-
-
-
Bombardier Aerospace
-
Netherlands
-
Business Consulting and Services
-
Procurement Quality Assurance Lead/Supervisor
-
Jan 1998 - Jan 2002
Program Management for Product Development)Manage Procurement Quality for the Global Express Refurbishment Program A/C9002,3 & 4. Manage Procurement Quality for the Q400 Refurbishment Program A/C 4002,3,4,5. Manage Repatriation of Global Express Heads Up Display Tucson to Toronto. Manage Dash 8 300 Repatriation Interiors Air Norstrum. Manage AMO Quality on Global Express certification for refurbishment.Supervise Procurement Quality Assurance and Planning in four hangars for BFTC (Bombardier Flight Test Center) and PMPD (Program Management for Product Development) at Bombardier Refurbishment Centre. Six Sigma Repatriation & Cost Reduction Project. Savings of approx 3.5 Million, one year.Supervise Quality Inspection in Shipping/Receiving for Bombardier Aircraft.Implemented new procedures for parts planning for Bombardier Aerospace Quality on special programs, new aircraft and prototype parts through JITBombardier supervised AMO (Pearson Airport)-Certified new product for installation on Post C of A Bombardier Aircraft via 24-0078 as a Category 3 & Category 5 inspector. Supervised all aspects of certification through completed aircraft and delivery to customer. Assisted in Sign off of new engineering and/or non-conforming one off parts (RNC) as QC MRBDevelopment of new programs and integration of Access parts planning and inventory systems, integration and harmonization of various Bombardier computer systems for inventory and planning for commonality. Assisted in developing new strategies for incoming and source inspection of parts to be installed on Bombardier Aircraft. Vendor delegate for product installed on new prototype and refurbished flight test aircraft in a Quality role. Supervised Quality in training and performance appraisals. Reviewed Quality and planning needs and assured adequate staffing at Aircraft location.
-
-
Education
-
Villanova University
Lean Six Sigma Black Belt -
Sports Management Worldwide
SOCCER MANAGEMENT AND SCOUTING
Community
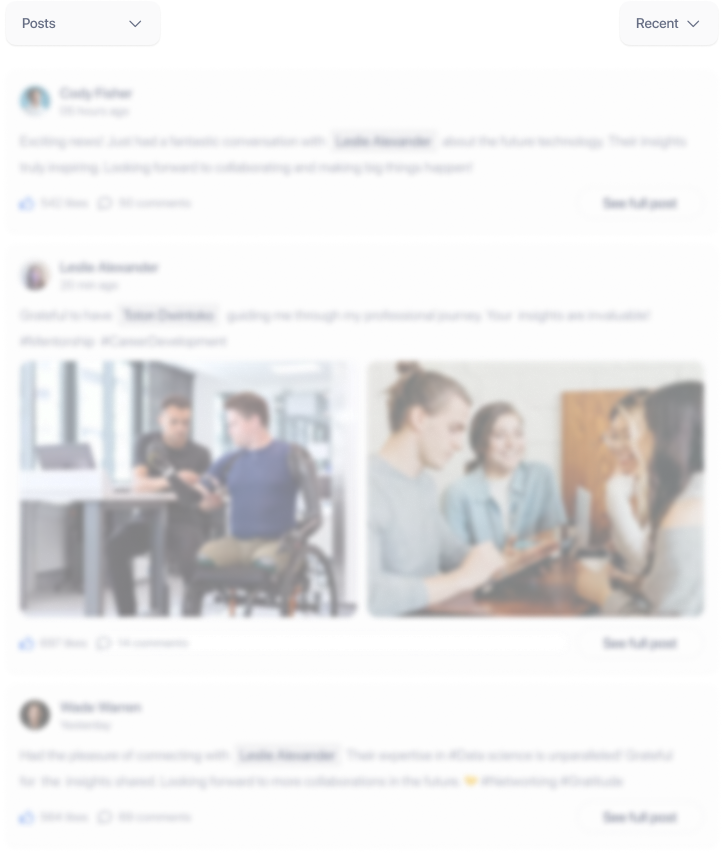