Graciela García Cisneros Flores
Director Of Purchasing at Dürr- Claim this Profile
Click to upgrade to our gold package
for the full feature experience.
-
Inglés Full professional proficiency
Topline Score
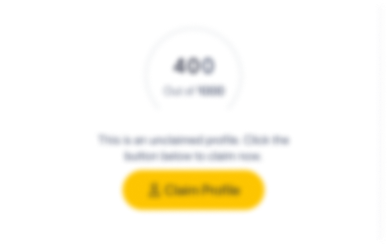
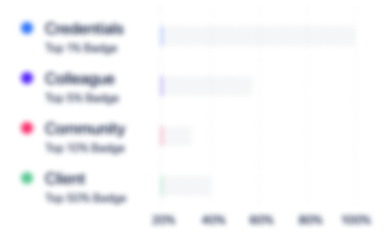
Bio

Cindy Guerrero
Graciela has high negotiation skills and wide knowledge about the industry. English fluent, focused in business success and proposing continual initiatives that take the company to save expenses while obtaining necessary resources. Always oriented to resource optimization. I recommend Graciela as she always shows responsibility and honesty performing her activities.

Cindy Guerrero
Graciela has high negotiation skills and wide knowledge about the industry. English fluent, focused in business success and proposing continual initiatives that take the company to save expenses while obtaining necessary resources. Always oriented to resource optimization. I recommend Graciela as she always shows responsibility and honesty performing her activities.

Cindy Guerrero
Graciela has high negotiation skills and wide knowledge about the industry. English fluent, focused in business success and proposing continual initiatives that take the company to save expenses while obtaining necessary resources. Always oriented to resource optimization. I recommend Graciela as she always shows responsibility and honesty performing her activities.

Cindy Guerrero
Graciela has high negotiation skills and wide knowledge about the industry. English fluent, focused in business success and proposing continual initiatives that take the company to save expenses while obtaining necessary resources. Always oriented to resource optimization. I recommend Graciela as she always shows responsibility and honesty performing her activities.

Credentials
-
Microsoft Teams Essential Training
LinkedInAug, 2020- Oct, 2024 -
Developing Your Leadership Philosophy
LinkedInDec, 2019- Oct, 2024 -
ISO 9001:2015 Internal Auditor Certification
CostCap Inc.Apr, 2018- Oct, 2024 -
Certified in Production and Inventory Management (CPIM)
APICSMar, 2016- Oct, 2024
Experience
-
Dürr
-
Germany
-
Machinery Manufacturing
-
700 & Above Employee
-
Director Of Purchasing
-
May 2022 - Present
*Lead, Manage and control for Procurement of engineered equipment, subcontracts, professional services, commodities, raw material, small tools & supplies. *Lead Purchasing Strategy for Mexico sites. *Responsible for Pre-selection, centralization, evaluation, negotiation with suppliers. *Responsible for projections, financial planning, expediting, delivery schedules and project Purchasing Reporting. *Responsible for supplier development involving Engineering and Quality, building long term relationships bringing cost effective solutions. *Management of assigned personnel: Purchasing Head, Buyers (Interns, Jr. and Sr. level); interfacing with engineering, estimating and site management.
-
-
-
Kiewit
-
United States
-
Construction
-
700 & Above Employee
-
PROCUREMENT MANAGER
-
Jan 2019 - May 2022
*Leadership and Management for Procurement of engineered equipment, subcontracts, professional services, commodities, permanent plant materials, and small tools and supplies. *Management of assigned personnel: Purchasing Agents, Purchasing Managers and other Purchasing employees interfacing with engineering management, estimating management, design management and site management. *Suppliers development (pre-qualification, qualification and capacity studies); negotiation with equipment, material, sub-contractor, service suppliers interacting with corporate attorneys. Achievements: - Pre-qualify Supplier base to get it ready for buy out the project (around $200 MUSD) - Process improvement in Estimating: reduce cycle time from 7 wks to 4.5 wks implementing one AVL with clear scopes, rules of pre-qualification, evaluation and control of Vendors to assure not only best price but best available quality.
-
-
-
Sanmina
-
United States
-
Appliances, Electrical, and Electronics Manufacturing
-
700 & Above Employee
-
PURCHASING AND LOGISTICS MANAGER
-
Jun 2016 - Oct 2018
*Plan, develop, optimize, organize, direct, manage, evaluate, accountable and/or responsible for the Supply Chain processes of the organization.*Track record of delivering cost effective/on time Procurement, Sourcing, Cost reduction, Supplier negotiation which help to optimize the value of the Supply Chain for Apodaca Mfg Plant.Responsible for Development and Control of Suppliers – Supplier’s performanceevaluation, new sources.*Responsible for TCP monitoring and control (costs).*Responsible for Weekly/Monthly/Quarterly statistics record (Metrics) andcorrective action implementation.*Responsible for Traffic/Logistics: Import/Export Operations.Achievements:- Write off RNI MRO PO’s with aging over than 180 days confirmed with suppliers.- Maintain LT for std Raw materials 3-4 weeks for ramp-up production after over than 12months of the lowest demand in Apodaca plant history.- Develop and implement Procedure “Classification, Selection and Suppliers Evaluation”.Currently working with 2 machine shops and a calibration laboratory.- Keep OTD for Direct material in optimal levels (over 95%).- Raw material standardization for over 150 items.- Development for 2 Machine shops to support Manufacturing with over 1MUSD revenueduring 2017; 800 KUSD during 2018.
-
-
SUPPLY CHAIN MANAGER
-
Dec 2013 - Jun 2016
*Recommend new developments in materials and supplies and on improving quality and cost of purchases. *Vendor’s performance evaluation (local and foreign vendors).*Continuous improvement process projects (cost reduction, material substitutions, VSM, etc).Achievements:-Implementation of Quality Management System procedures in Purchasing Active role in ISO certification of Apodaca facility.-Purchasing team building (from 2-16 people): training and mentoring.-Active role in Baker/Sanmina transition being Champion for ERP implementation.-Develop supply program for high runners (frac point product line).-Generate savings for around 5MUSD in the third year of production for frac point PL.-Develop a strong relationship with key suppliers (steel) to assure LT dramatic reduction for frac point product line (8-3 wks).
-
-
-
Baker Hughes
-
United States
-
Oil and Gas
-
700 & Above Employee
-
SUPPLY CHAIN MANAGER
-
Oct 2011 - Dec 2013
*Plan, develop, optimize, organize, direct, manage, evaluate, accountable and/or responsible for the Supply Chain processes of the organization. *Manage and/or execute Supply chain related functions (e.g., develop and implement sourcing strategies, negotiate agreements, etc.), as well as maintain and develop positive business relationships with the supplier’s base. * Recommend new developments in materials and supplies and on improving quality and cost of purchases. *Vendor’s performance evaluation (local and foreign vendors). *Active participation in continuous improvement process projects (cost reduction, material substitutions, VSM, etc). Achievements: - Develop supply program for high runners (frac point product line). - Generate savings for around 5MUSD in the third year of production for frac point PL (material optimization). - Consolidate a strong relationship with key suppliers (steel) to assure LT dramatic reduction for frac point product line (8-3 wks).
-
-
-
GE Oil & Gas
-
Pressure Control Manufacturing Facility - Guadalupe Nuevo Leon, Mexico
-
PROCUREMENT AND LOGISTICS MANAGER
-
May 2007 - Sep 2011
*Responsible for Procurement, Import-Export, Warehouse (Receiving/Shipping) and Logistics areas. *Establish negotiations with local and foreign vendors; supervise raw material import, machinery; shipping control and logistics related to Import-Export. *Negotiate Raw material procurement (forgings, steel in different grades), seek new sources and vendor’s development as well as strong relationships generation. *Vendor’s performance evaluation (local and foreign vendors) *Grant inventory control, preservation and accuracy of inventory through review of entries and shipments processed in the system, cycle counts of inventory and corrective action implementation (follow-up). *Monthly statistics record (Metrics) and corrective action implementation. Achievements: -Implementation of Quality Management System procedures in Purchasing and Warehouse areas. - Active role in API-ISO certification of Monterrey facility. - Development of local vendors (critical components), decreasing lead time in around 50%, as well as adding local content to our product. - Local freight forwarder development (Development of a route Monterrey-Southeast) through bid invitation, drop of freight cost down to 20% in several type/size of trucks. - Negotiation with local vendors of components getting prices equal as prices given in global contracts generating reduction on lead time from 6 to 4 weeks, reduction of freight services and duties by around 7.6% since 2008.
-
-
-
Wood Group Pressure Control
-
Sales and Service Office - Mexico City Area, Mexico
-
PROCUREMENT MANAGER / ADMINISTRATIVE COORDINATOR
-
Jun 2005 - May 2007
*Responsible for running Sales office in Mexico City office as well as Villahermosa and Reynosa Service Centers. *Contracts Administration, Material Control (Planning, Procurement and Logistics); *Warehouse Administration (Villahermosa and Reynosa warehouses: cycle counts). *Resources Administration; Fix asset control *Marketing: Introduce and communicate corporate image; Trade shows organization (Expetro, Expo-ductos), Offices open house; customer service. *Active role in positioning the company in the oil and gas market in Mexico. Achievements: -Start up of Mexico City Sales office, Villahermosa and Reynosa Service Centers (2005, 2006) and Monterrey facility start up (2007, 2008). - Procedures and corporate image implementation in Sales, Procurement and Services Area. - Procedures and corporate image implementation in Monterrey Facility (2007).
-
-
Education
-
UVM, CAMPUS MONTERREY
Bachelor's degree, Business Administration, Management and Operations -
Universidad Nacional Autónoma de México
Bachelor's degree, International Relations
Community
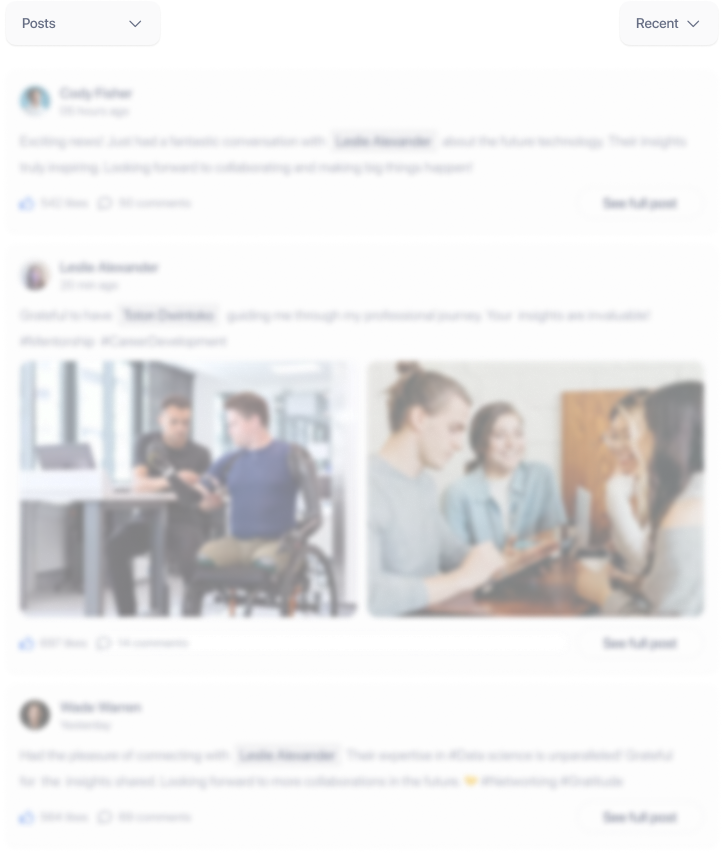