Girish Radhakrishnan
Vehicle Dynamics R&D Engineer at Optimum G- Claim this Profile
Click to upgrade to our gold package
for the full feature experience.
-
English Full professional proficiency
-
Tamil Native or bilingual proficiency
-
Hindi Native or bilingual proficiency
-
Malayalam Native or bilingual proficiency
Topline Score
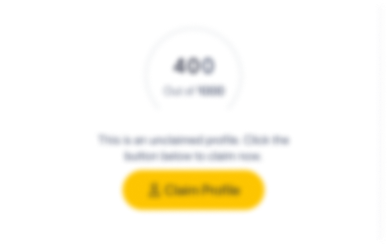
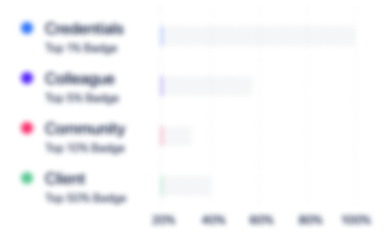
Bio


Credentials
-
Introduction to Vehicle Dynamics and Vehicle Design
Delta Inc
Experience
-
Optimum G
-
United States
-
Motor Vehicle Manufacturing
-
1 - 100 Employee
-
Vehicle Dynamics R&D Engineer
-
Nov 2020 - Present
- Leading the development of dynamic vehicle models capable of operating at the limits of handling- Leading the development of PID controllers, H-infinity controllers, and iterative learning control algorithms for vehicle models- Leading the development of dynamic vehicle models that can efficiently perform steady-state, linearization apart from time-domain simulation- Deploying these models in C++ with CI/CD- Leading the development of OptimumG's ride and handling analysis software- Leading the development of OptimumG's tire modeling and analysis software- Handling various consulting projects on tire testing and analysis
-
-
-
OptimumG
-
United States
-
Motor Vehicle Manufacturing
-
1 - 100 Employee
-
Racecar and Engineering Intern
-
Jul 2019 - Nov 2020
Vehicle Model development for transient vehicle dynamics simulations. - Currently implementing numerical solvers capable of handling discontinuous and numerically stiff systems. - Developed a multi-degree-of-freedom vehicle model capable of simulating vertical, longitudinal and lateral dynamics. This model can deal with fully non-linear springs, dampers, bumpstops, tires as well as 3D aerodynamic maps and variable suspension kinematics, - Developed a multi-objective spring and damper optimization targeted at improving metrics pertaining to vertical dynamics.
-
-
-
University Racing Eindhoven
-
Netherlands
-
Automotive
-
1 - 100 Employee
-
Vehicle Dynamics Engineer
-
Sep 2018 - Apr 2019
-
-
-
OptimumG
-
United States
-
Motor Vehicle Manufacturing
-
1 - 100 Employee
-
Vehicle Dynamics Simulations Sub-Contractor
-
Jun 2017 - Jul 2018
• Created Vehicle Dynamics simulation software focusing on Suspension Setup, Kinematics and Dynamics with fullyfunctional Graphical User Interface.• Created Vehicle Models to solve a wide array of problems such as Diagonal Weight Transfer during Steering,Suspension Wishbone Loads etc.• Created complex Vehicle Models in conjunction with Optimization Algorithms to build a Suspension Setup Tool. Thistool educates the user on ALL the changes required to achieve a setup. Used Genetic Algorithms to implement this.• Created complex Vehicle Models with Optimization Algorithms to build a Suspension Kinematics tool. This tool assiststhe user in deciding the Pick-Up point locations which satisfy the required Bump Steer, required Camber Variation,required Roll & pitch Center position and many more Suspension Parameters.• Implementing Computer Aided Design tools in self-developed simulation software which allows the user to map andgenerate suspension files using imported Vehicle CAD models.• Performing beta testing of OptimumG’s professional software.
-
-
-
Ather Energy
-
India
-
Motor Vehicle Manufacturing
-
700 & Above Employee
-
Vehicle Structure Engineer
-
Sep 2016 - Apr 2017
-Created Product Specification Sheets for the parts that I owned. - Developed a Stress and Strain Calculator for Press-Fit procedures- Worked on the Design and Release of Front and Rear Suspension components-Executed Design Validation Plans to take parts which are in prototyping stage to production stage.-Reworked on the CAD models of Chassis components to make them casting friendly. -Carried out Root Cause Analysis to determine the root causes of the issues in the prototype.
-
-
-
Orion Racing India
-
India
-
Motor Vehicle Manufacturing
-
1 - 100 Employee
-
Testing and Validation Engineer
-
Dec 2015 - Aug 2016
-Tested and validated the various parameters of the car such as lateral and longitudinal accelerations, weight transfer, roll angle, roll gradient through various data acquisition equipment such as accelerometers, linear potentiometer, rotary potentiometer etc-Interpreted the logged data to analyze the performance of the car by creating actual Yaw Moment vs Lateral Acceleration graphs, Yaw Moment vs Yaw Acceleration graphs, Yaw Acceleration vs Time graphs and calculated the percentage error.-Actively analysed driver performance by overlaying the logged data values of the driver with a reference data graph.
-
-
Vehicle Dynamics Engineer
-
Aug 2015 - Aug 2016
-Worked with Optimum T to perform tire modeling to enable objective selection of tire for our car.-Developed excel based simulations for weight transfer during cornering, accelerating or braking, extended the simulation to determine geometric, elastic and non-suspended weight transfers.-Determined Steady state characteristics of the vehicle such as stability index, control etc., through use of self-developed Yaw Moment vs Acceleration graphs which also assisted vehicle design and setup.-Designed, analyzed and optimized the bell crank.-Developed baseline Spring rates and Anti-Roll Bar stiffness required for selected value of Roll Gradient which were further tuned during testing and validation phase.-Developed baseline damping ratios.-Developed matrix to calculate the forces encountered by the suspension control arms during extreme conditions of braking and cornering. -Effectively utilized "CARMAKER's" modeling and simulation software "IPG" to model our Formula Student Prototype. The model included parameters of the car such as tire data, damping curves, bump and rebound stop stiffness, spring stiffness, kinematic parameters & coordinates, power train parameters etc. The output of the software were parameters which define vehicle behavior such as yaw velocity, yaw acceleration, lateral forces generated by the tires, vertical forces on each tire etc., These parameters were further utilized to calculate the yaw moment and yaw inertia which was considered as a vital parameter of vehicle Ride & Handling behavior. -Presented the “Suspension Design Report” to a panel of international judges at “FORMULA STUDENT INDIA” held at BUDH INTERNATIONAL CIRCUIT, Greater Noida
-
-
Manufacturing Engineer
-
Oct 2015 - Dec 2015
-Responsible for manufacturing of parts of wheel assembly such as HUBS, UPRIGHTS, RIM CENTER, CONNECTING LINK etc., and components of drive train systems such as SPROCKET, TRIPOD HOUSING and ECCENTRIC through various industry sponsors-Involved in extensive marketing activities to reel in industrial contacts and sponsors who later helped us in manufacturing, supplying raw material, hardware and financing
-
-
Education
-
Eindhoven University of Technology
Master of Science - M.Sc., Automotive Technology -
KJ Somaiya College of Engineering, Vidyavihar
Bachelor of Science - B.Sc, Mechanical Engineering -
International Indian School Damam
High School, Science
Community
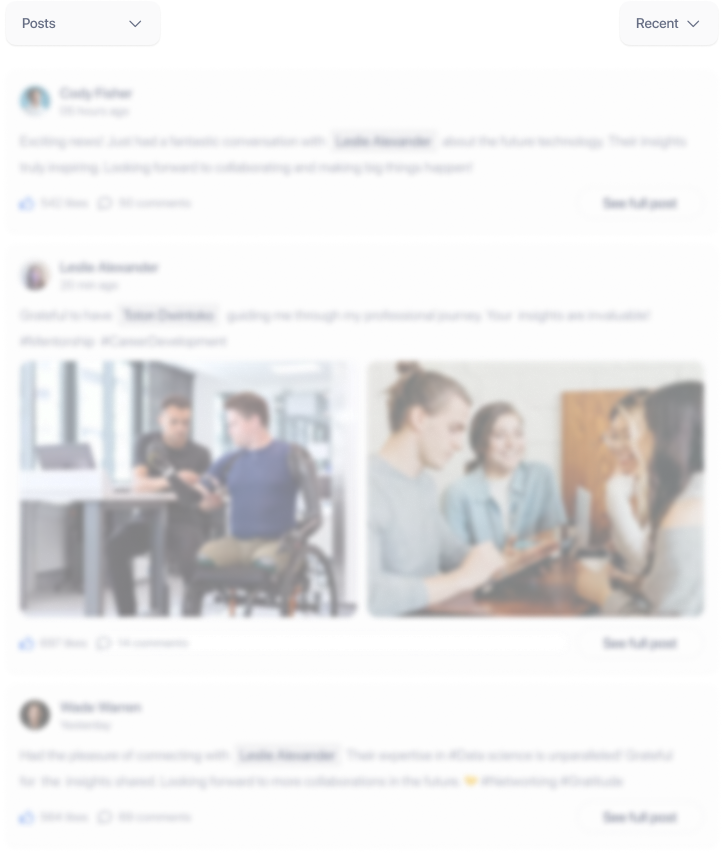