Gilbert Bautista
Quality & Production Capability Manager at Hendon Semiconductors- Claim this Profile
Click to upgrade to our gold package
for the full feature experience.
Topline Score
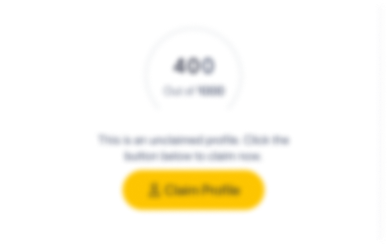
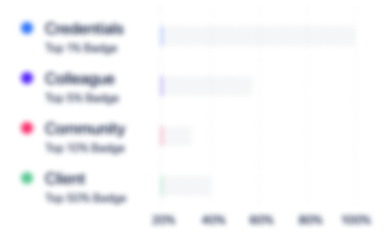
Bio
0
/5.0 / Based on 0 ratingsFilter reviews by:
Experience
-
Hendon Semiconductors
-
Australia
-
Appliances, Electrical, and Electronics Manufacturing
-
1 - 100 Employee
-
Quality & Production Capability Manager
-
Jul 2022 - Present
-
-
Process & Quality Engineer
-
Nov 2021 - Jun 2022
-
-
-
Motherson Australia (SMR & MEPL)
-
Australia
-
Appliances, Electrical, and Electronics Manufacturing
-
1 - 100 Employee
-
Electronics Manufacturing Engineer
-
Jan 2019 - Oct 2021
-
-
-
Ampleon
-
Netherlands
-
Semiconductors
-
400 - 500 Employee
-
Senior Process Development Engineer
-
Dec 2015 - Jan 2019
Develops, designs and plans Assembly Processes and Equipment requirements for new products and packages. Ensures that timing, capability and capacity to support incoming product and packages are well defined before they are processed in Back-end Operations during the release. • Develops and qualifies processes (Thermo-compression Die-bonding, Glue Dispensing and Lid Sealing) and equipment for RF Power products according to the timing of the new product and package release. This is in coordination with the Engineering, Quality and Manufacturing focal persons in Ampleon. Show less
-
-
-
NXP Semiconductors
-
Netherlands
-
Semiconductor Manufacturing
-
700 & Above Employee
-
Process Development Engineer
-
Jun 2010 - Dec 2015
Develops, designs and plans Assembly and Test Processes and Equipment requirements for new products and packages. Ensures that timing, capability and capacity to support incoming product and packages are well defined before they are processed in Back-end Operations during the release. Six Sigma Black-belt Trained for Problem Solving and Project Management. Subject Matter Expert for Product to Package Interaction of RF Power devices. • Co-inventor for Air Cavity Package design to control Glue Flow-out of RF Power devices which protected NXP’s portfolio of design and technology. (pending IP) • Developed and qualified processes (Pre-Assembly, Pick and Place, Glue Die-bonding, Wire-bond, Sealing and Testing) and equipment for RF Power devices and Angular Sensors products according to the timing of the new product and package release. This is in coordination with the Engineering, Quality and Manufacturing focal persons in NXP. • Generated ~300K US$ in 2015 savings for NXP through the characterization and release of new supplier material BOM for RF power devices. Show less
-
-
-
-
Test Process and Equipment Engineer
-
Jun 2004 - Aug 2009
Manages over-all equipment health of the module towards meeting safety, quality, cost and delivery standards. Partners with manufacturing and key factory support groups in aligning resources and ensures that the operational excellence indicators are met or exceeded. • Directed test operations huddle which delivered successful daily and weekly strategic deliverables and demonstrated above goal availability, thus achieving class-leading utilization across the processor factories by the end of Q4'08 comparatively a significant leap of 12% in performance from Q3'08. • Resolved equipment-related issues and saved US$ 800K through kit re-use leading to successful product transfer from the development sites to Intel Philippines which enabled other sites to manufacture new products for mobile computing use. • Authored a Technical Paper about kit inter-changeability for certain processor products without compromising thermal performance and mechanical properties which was presented on a conference in Penang, Malaysia last November 2007 and became a standard tool set-up. • Developed an efficient system that significantly reduced conversion time of the test handler from 8 hours to 2 hours, resulting to 95.5% availability with ~US$ 2.6M savings through maximized output per quarter. • Recovered about US$ 1.2M savings in a span of three months through establishment of standard units safekeeping and usage method during production leading to faster analysis and equipment debug thus lessening downtime to ~3% per day. • Managed and standardized test handler equipment parameters across Intel processor factories in Asia and South America that prevented re-occurring of equipment related failures in the past. Show less
-
-
Education
-
De La Salle University
BS Electronics and Communications Engineering, Electronics and Communications
Community
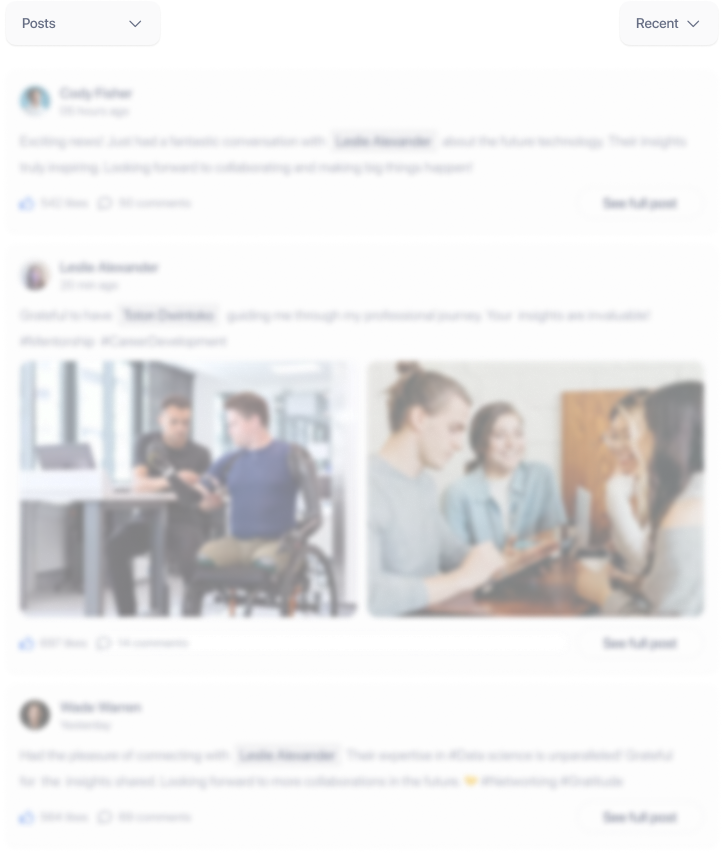