Gianna Credaroli
Business Manager at New York Coffee Festival- Claim this Profile
Click to upgrade to our gold package
for the full feature experience.
-
Spanish Full professional proficiency
-
Italian Elementary proficiency
Topline Score
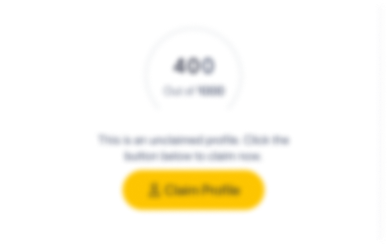
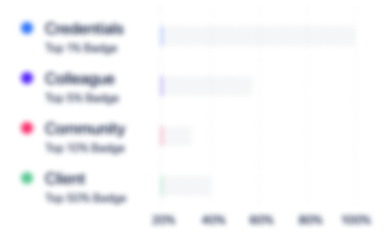
Bio

Luciano Barbugli
Gianna is an excellent wireline engineer. I have no doubt she has the potential to have a successful carrer in the oil & gas industry. Her responsibility and proffesionalism are here strenghts. Her fluent Spanish in outstanding

Luciano Barbugli
Gianna is an excellent wireline engineer. I have no doubt she has the potential to have a successful carrer in the oil & gas industry. Her responsibility and proffesionalism are here strenghts. Her fluent Spanish in outstanding

Luciano Barbugli
Gianna is an excellent wireline engineer. I have no doubt she has the potential to have a successful carrer in the oil & gas industry. Her responsibility and proffesionalism are here strenghts. Her fluent Spanish in outstanding

Luciano Barbugli
Gianna is an excellent wireline engineer. I have no doubt she has the potential to have a successful carrer in the oil & gas industry. Her responsibility and proffesionalism are here strenghts. Her fluent Spanish in outstanding

Experience
-
New York Coffee Festival
-
United States
-
Events Services
-
1 - 100 Employee
-
Business Manager
-
Aug 2022 - Present
I'm working with the CEO to plan the 2023 New York Coffee Festival. I work on strategy and business development for the festival. experience for our guests. Right now, I am strategizing on finding a venue whose square footage can hold enough vendors and guests to generate a profit and create the ultimate experience for our guests. I will work on strategic planning and also manage the guest services team again (including hiring and training personnel). For the 2022 New York Coffee Festival, I managed the front of house at the New York Coffee Festival, this included hiring guest service associates to work in VIP services and ticket check in. Responsibilities: - Manage Guest Services Team: I hired 3 people per day of the festival to greet guests, check tickets, and work in VIP services. - Manage VIP Services: ensure the guest service associates were greeting VIP and Super VIP guests, informing guests on what is included in their ticket, answering guests' questions, and all customer service related inquiries. - Inventory management - Strategic planning - Event planning
-
-
-
BASF
-
Germany
-
Chemical Manufacturing
-
700 & Above Employee
-
Development Engineer
-
Oct 2019 - Present
· Manage field testing of axle and transmission fluids (350 customer trucks across 9 BASF products) in commercialization process · New business development: exceeded annual goal by 132% · Customer engagement: ensure customers’ needs are communicated to technical team to implement end-users’ needs into design consideration · Cross-functional collaboration between sales and marketing to provide reliable solutions that maximize customer experience · Build models in Microsoft Excel to analyze customers’ data, noting actionable patterns, track progress of ongoing tests, and make future predictions · Present models and progress of field trials to upper management · Analyze market trends and industry news, leveraging this information for business unit’s strategy and enhance customer experience · Optimized efficiency of data entry using automation: reducing total time from 2-hours to 30-mins · Write reports summarizing data analysis, results, and actionable pattens (including future predictions and implications of industry developments that may have impact) · Multi-task to ensure all customers are getting the communication and support needed to run successful field tests · Building a field-testing program for our fuel additives business (gasoline and diesel fuel) · Engage with customers and BASF Sales Team at conferences and external events · Scaled up blending process of experimental lubricants to decrease operating cost by 66% and increase output by 300% · Forecast and plan projected field tests to ensure axle and transmission fluids are received by customer prior to truck delivery · Ensure safety stock of experimental axle and transmission lubricants at 3rd party facility to prevent customer delays · Develop diesel additive packages that meet Top Tier requirements to increase business with regional customers
-
-
-
Schlumberger
-
United States
-
Oil and Gas
-
700 & Above Employee
-
Wireline Field Engineer
-
Oct 2017 - Jun 2019
Highlights: · Perform calculations necessary for oilfield operation and conducted risk assessments to mitigate hazards · Manage Schlumberger personnel to operationally check tools and equipment in preparation of oilfield operation · Supervised oilfield operation at client’s site including data collection, explosives, and safety of all personnel on site · Objective of Wireline operations: better characterization to improve predictive capability of models and increase oil recovery · Led Wireline operations in Vaca Muerta oilfield in Neuquén, Argentina for multiple clients (role was conducted in Spanish), Permian Basin, USA, and Villahermosa, MX · Cross-functional collaboration with sales team to define client’s needs · Manage assets in Wireline operations: tools, rig-up equipment, trucks, explosives, radiation, etc. · Wireline services included casing perforations using explosives, plug setting using explosives, well characterization using sonic tools, well fluid measurements, formation characterization using radiation tools, etc. · Wireline log helped customer diagnose issues (i.e. degradation in casing wall and/or cement), zonal isolation, perforate casing for oil recovery, characterize fluid properties in well (pressure, density, fluid level), and formation characterization · Interpretations of data collected via sonic tools (casing internal radius, external radius, cement integrity, etc.) based on amplitude of attenuation · Highest number of health, safety, and environment reports amongst all engineers in my region (Argentina, Chile, and Brazil) · Attended lectures on economics of Permian Basin (production rate dependent on rate at which oil could exit the Permian Basin via ships, pipelines, etc)
-
-
-
-
Guest Services Associate
-
Nov 2015 - Oct 2017
I worked with the founder of the New York Coffee Festival to help manage the front of house during the 2nd New York Coffee Festival. My responsibilities included: - Custom Service - Managing VIP guests and ticket check in - Inventory Management - Logistics I worked with the founder of the New York Coffee Festival to help manage the front of house during the 2nd New York Coffee Festival. My responsibilities included: - Custom Service - Managing VIP guests and ticket check in - Inventory Management - Logistics
-
-
-
Columbia University in the City of New York
-
Higher Education
-
1 - 100 Employee
-
Graduate Research Assistant
-
Sep 2015 - Dec 2016
Highlights:· Performed computer simulations of polymer grafted nanoparticles to understand corona behavior· Computing languages used: Python, Tcl, Matlab· Taught undergraduate students thermodynamics and mass transport phenomena (Teaching Assistant role)Overview: My graduate research was focused on polymer grafted nanoparticles under Sanat Kumar. For my work, I simulated polymers grafted to the surface of a nanoparticle. I placed this polymer-grafted nanoparticle in a matrix of free chain polymers, which were chemically identical to the grafted polymers. I systematically varied the grafting density (the number of chains grafted to the particle's surface), the length of the chains grafted to the particle's surface and the length of the free polymer chains. I then studied the miscibility of the grafted particle with the free chains. The shape of the corona gave us insight into the interactions between the grafted polymers and free chain polymers.The computing languages that I used to do my research include Python (to generate the initial configuration of the system), Tcl (to gather data collected from the simulation) and Matlab (to analyze the data).
-
-
Teaching Assistant
-
Aug 2015 - May 2016
I was a teaching assistant in the Chemical Engineering department at Columbia University for two semesters. My first semester, as a teaching assistant, was for the course, Introduction to Thermodynamics taught by Dr. Sanat Kumar. My role was to develop rubrics and solutions for course assignments, grade students' quizzes, discuss any concerns students' may have had about the material, manage the grade book for the course and grade exams. My second semester as a teaching assistant was for the course, Transport II, taught by Dr. Christopher Durning. My role was to attend lectures, grade all assignments, and to create and manage the course grade book.
-
-
-
University of Connecticut
-
United States
-
Higher Education
-
700 & Above Employee
-
Teaching Assistant
-
Aug 2013 - May 2015
I was a teaching assistant in the chemical and biomolecular engineering department at the University of Connecticut for three semesters. My first semester as a teaching assistant was for the course, Introduction to Chemical Engineering (CHEG 2103) taught by Dr. William Mustain. My role as a teaching assistant was to grade students' homework, discuss any concerns students' may have had about their grades, manage the grade book for the course and assist Professor Mustain in grading exams. My second semester as a teaching assistant was for the course, Foundations of Engineering (ENGR 1166), taught by Dr. Jeffrey McCutcheon. My role as a teaching assistant was to grade all assignments, calculate students’ grades, and create handouts, exam questions and homework questions for class use. I was also responsible for creating and managing the course grade book. Since this course was targeted to a more designed base approach, I assisted Dr. McCutcheon, the graduate teaching assistants and other undergraduate assistant in developing course projects. The third semester I was a teaching assistant for the course, Fluid Mechanics (CHEG 3123), taught by Dr. Leslie Shor. This semester I was accepted to the Pratt and Whitney Undergraduate Leadership, Teaching and Mentoring Fellows Program at the University of Connecticut (see below).I was required to hold three office hours per week and meet weekly with my faculty advisor. I was required to attend the discussion section of the course and assist in leading the class discussion. I was also responsible for double-checking homework solutions each week before my office hours and discussing any discrepancies with the graduate teaching assistant, Grant Bouchillon. My final responsibility included grading students’ homework and exams and recording all grades.
-
-
R.E.U. Ambassador
-
May 2013 - Aug 2013
My job was to help Dr. McCutcheon (the R.E.U. director) coordinate events, schedule meetings and presentations, and assist students with any concerns they may have had during their stay at the University of Connecticut. I also helped run the Explore Engineering (E2) workshop. This is a program that presents the various engineering practices to high school juniors and seniors through wet-labs and permits these students to engage in a specific engineering field. Students reside at the University of Connecticut during the program to give them a better feel of college living. I also assisted in running the daVinci project. This was a one-week program for middle and high school science, technology and mathematics teachers. These teachers earned continuing education credits for their time spent at this program. They were able to gain more insight into basic engineering concepts. They spent 18 hours learning about rudimentary engineering principles with us. This program was designed to allow these teachers to generate new ideas and implement them in their own classrooms, which proved to be a greatly rewarding experience. During this summer I was also able to continue my research from the previous academic year. I assisted in building a bench top nanofiltration system in order to test nanofiltration, reverse osmosis and brackish water membrane integrity. The new system facilitates more productivity and increases the amount of reverse osmosis testing in the laboratory. I learned about different types of fittings: compression fittings, barbed fittings, hex nipples, and couple fittings. Each day I worked with a vice grip (of which my great-great grandfather invented!), wrenches, and screw drivers. It was an invaluable hands-on experience. Our system did not have a method for temperature regulation; therefore we had to implement a heat exchanger in our system.
-
-
-
-
Research Assistant
-
Sep 2012 - May 2015
I am currently a research assistant in the Sustainable Water and Energy Learning Laboratory under Dr. Jeffrey McCutcheon at the University of Connecticut. My undergraduate research focused on developing a nanofiltration membrane for water softening applications. Our goal was to design a membrane that had a higher water permeability and a higher salt rejection than Dow's NF-90 and NF-270 membranes. I tested Dow's NF-90 and NF-270 membranes in our laboratory under the specifications provided by Dow. I was able to characterize these membranes and meet the performance provided in the specification sheets for these membranes. I then tested a new nanofiltration membrane that was developed in our laboratory. The new thin film membrane consisted of a 3M Nylon-6,6 support layer and a selective layer that was engineered in the laboratory. This was the first nanofiltration membrane designed on a hydrophilic support. I conducted reverse osmosis tests using two different salt solutions, which were tested under commercial specifications. From this study, the pure water and salt permeance of the 2000-ppm magnesium sulfate solution of the Nylon-6,6 membrane was lower than the specifications provided by Dow. However, the salt rejection was similar to that provided by Dow. The salt rejection of the Nylon-6,6 membrane was much higher than the NF-270 membrane when tested experimentally. I presented my work at the 2014 AIChE Annual Undergraduate Student Poster Competition. I won second place in Separations (Division I) for my poster presentation.
-
-
-
-
Intern
-
May 2014 - Aug 2014
I did a summer internship at Planta Analytica, LLC. Planta Analytica is an analytical laboratory that specializes in chromatography for use in the pharmaceutical industry, food technology and botanical supplements. This company currently has two industry-sponsored projects with Ocean Spray and Pepsi. I was hired to work on a PepsiCo project under PepsiCo’s new division, The Global Nutrition Group. The goal of this division is to drive nutrition innovation. They are currently embarking on a global trek to find new ingredients used to reduce sugar, sodium and calories in both new and existing products. PepsiCo collects plant extracts from all over the world and sends them to Planta Analytica. My job was to assist in developing a process to isolate compounds in these samples using methanol, water and acetone in a chromatographic system. These samples were purified, packaged and sent back to PepsiCo for analysis. Other techniques that I learned this past summer were thin layer chromatography, centrifugal partition chromatography and high performance liquid chromatography.
-
-
-
DynGlobal
-
Renewable Energy Semiconductor Manufacturing
-
1 - 100 Employee
-
Water Purification Specialist
-
Sep 2010 - Jan 2012
DynGlobal manufactures solar panels, solar powered water purification units, solar generators, military equipment, etc. They also design and build water purification units that are designed for military personnel, disaster relief, residential use. For my position, I worked on site control for various DynGlobal projects. I also designed spreadsheets for DynGlobal and for our clients. I calculated the overall cost to build the solar system, the total energy production, and the income stream for a given project. The spreadsheets for DynGlobal included the total cost of materials and labor for a given project, the total amount of energy captured by the solar panels, the income stream generated by selling excess energy back to the grid, and the relevant tax deductions from using renewable energy. I had to contact the IRS, US Treasury and many other governmental departments to determine the maximum tax credits that our solar projects were eligible for and depreciation schedules. I also helped design and build water purification systems. These systems ranged from portable to under-the-sink, to full scale. Our water purification systems utilized reverse osmosis to push dirty water through a membrane. They were powered by solar panels and had applications in military, residential, and commercial.
-
-
Education
-
Columbia University in the City of New York
Master's degree, Chemical Engineering -
Columbia University in the City of New York
Master’s Degree, Chemical Engineering -
University of Connecticut
Bachelor of Science (BS), Chemical Engineering
Community
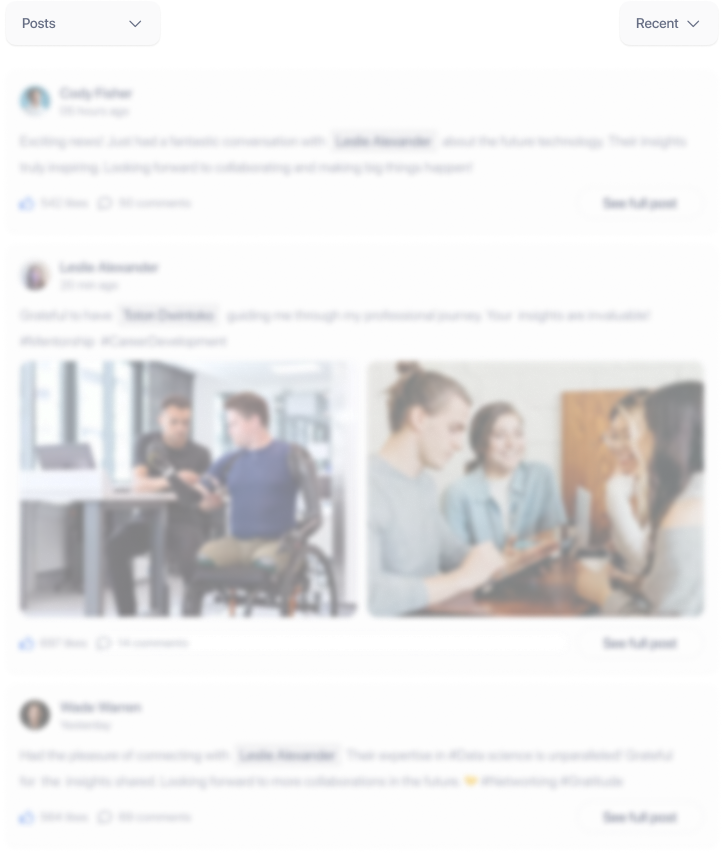