
Gerry Larkin
Quality and Compliance Manager at CloseReach Ltd- Claim this Profile
Click to upgrade to our gold package
for the full feature experience.
Topline Score
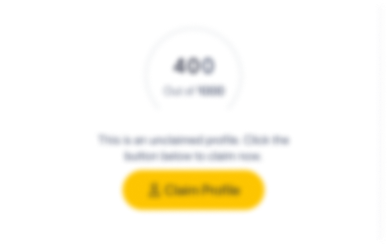
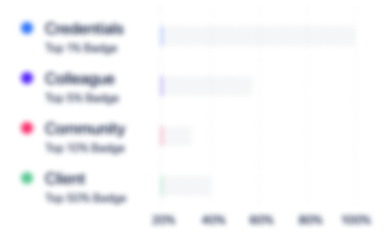
Bio

Ron Joy CPIM
I had the pleasure of working with Gerry at General Dynamics. Gerry is a seasoned professional with in-depth knowledge of Quality Management Systems, auditing, process development and continuous improvement. Gerry’s friendly professional manner allows him to excel in both team environments as well as a sole contributor. I would confidently recommend Gerry. For more information feel free to contact me.

Harry Webster
I'm taking a few minutes to broadcast my thoughts and impressions of Gerry Larkin based on having worked with him for over a decade at GD Canada. Over this period, I have come to know Gerry, first, by his reputation across the business as 'The Expert' in the company's Quality Assurance organization. Gerry would typically lead Quality initiatives end-to-end for GD Canada. My own personal experiences with Gerry have been very positive. The first experiences that come to mind are quality-audits that have been conducted by Gerry on projects of mine. What I remember most was Gerry's non-threatening, supportive leadership style, that helped me better understand his role in improving our company's processes. I also remember Gerry going out of his way to prepare the organization through awareness-sessions in advance of major corporate quality audits. Again, I first recall his gentle and supportive style which had a way of putting the team at ease, given what might otherwise be a stressful event. Most notably, I've had the pleasure of attending Leadership Development training with Gerry which allowed me to learn more about what a well-balanced leader he is. For example, I came to learn that he is a talented musician, known for his informal public performances. Gerry also takes the time everyday to maintain his fitness through daily running. These are the qualities that, for me, standout most. Gerry is a leader that works hard but finds balance - something that other leaders often fail to achieve. As I sit here typing, I smile knowing that wherever Gerry's career takes him, he will be living the 'Good Life'.

Ron Joy CPIM
I had the pleasure of working with Gerry at General Dynamics. Gerry is a seasoned professional with in-depth knowledge of Quality Management Systems, auditing, process development and continuous improvement. Gerry’s friendly professional manner allows him to excel in both team environments as well as a sole contributor. I would confidently recommend Gerry. For more information feel free to contact me.

Harry Webster
I'm taking a few minutes to broadcast my thoughts and impressions of Gerry Larkin based on having worked with him for over a decade at GD Canada. Over this period, I have come to know Gerry, first, by his reputation across the business as 'The Expert' in the company's Quality Assurance organization. Gerry would typically lead Quality initiatives end-to-end for GD Canada. My own personal experiences with Gerry have been very positive. The first experiences that come to mind are quality-audits that have been conducted by Gerry on projects of mine. What I remember most was Gerry's non-threatening, supportive leadership style, that helped me better understand his role in improving our company's processes. I also remember Gerry going out of his way to prepare the organization through awareness-sessions in advance of major corporate quality audits. Again, I first recall his gentle and supportive style which had a way of putting the team at ease, given what might otherwise be a stressful event. Most notably, I've had the pleasure of attending Leadership Development training with Gerry which allowed me to learn more about what a well-balanced leader he is. For example, I came to learn that he is a talented musician, known for his informal public performances. Gerry also takes the time everyday to maintain his fitness through daily running. These are the qualities that, for me, standout most. Gerry is a leader that works hard but finds balance - something that other leaders often fail to achieve. As I sit here typing, I smile knowing that wherever Gerry's career takes him, he will be living the 'Good Life'.

Ron Joy CPIM
I had the pleasure of working with Gerry at General Dynamics. Gerry is a seasoned professional with in-depth knowledge of Quality Management Systems, auditing, process development and continuous improvement. Gerry’s friendly professional manner allows him to excel in both team environments as well as a sole contributor. I would confidently recommend Gerry. For more information feel free to contact me.

Harry Webster
I'm taking a few minutes to broadcast my thoughts and impressions of Gerry Larkin based on having worked with him for over a decade at GD Canada. Over this period, I have come to know Gerry, first, by his reputation across the business as 'The Expert' in the company's Quality Assurance organization. Gerry would typically lead Quality initiatives end-to-end for GD Canada. My own personal experiences with Gerry have been very positive. The first experiences that come to mind are quality-audits that have been conducted by Gerry on projects of mine. What I remember most was Gerry's non-threatening, supportive leadership style, that helped me better understand his role in improving our company's processes. I also remember Gerry going out of his way to prepare the organization through awareness-sessions in advance of major corporate quality audits. Again, I first recall his gentle and supportive style which had a way of putting the team at ease, given what might otherwise be a stressful event. Most notably, I've had the pleasure of attending Leadership Development training with Gerry which allowed me to learn more about what a well-balanced leader he is. For example, I came to learn that he is a talented musician, known for his informal public performances. Gerry also takes the time everyday to maintain his fitness through daily running. These are the qualities that, for me, standout most. Gerry is a leader that works hard but finds balance - something that other leaders often fail to achieve. As I sit here typing, I smile knowing that wherever Gerry's career takes him, he will be living the 'Good Life'.

Ron Joy CPIM
I had the pleasure of working with Gerry at General Dynamics. Gerry is a seasoned professional with in-depth knowledge of Quality Management Systems, auditing, process development and continuous improvement. Gerry’s friendly professional manner allows him to excel in both team environments as well as a sole contributor. I would confidently recommend Gerry. For more information feel free to contact me.

Harry Webster
I'm taking a few minutes to broadcast my thoughts and impressions of Gerry Larkin based on having worked with him for over a decade at GD Canada. Over this period, I have come to know Gerry, first, by his reputation across the business as 'The Expert' in the company's Quality Assurance organization. Gerry would typically lead Quality initiatives end-to-end for GD Canada. My own personal experiences with Gerry have been very positive. The first experiences that come to mind are quality-audits that have been conducted by Gerry on projects of mine. What I remember most was Gerry's non-threatening, supportive leadership style, that helped me better understand his role in improving our company's processes. I also remember Gerry going out of his way to prepare the organization through awareness-sessions in advance of major corporate quality audits. Again, I first recall his gentle and supportive style which had a way of putting the team at ease, given what might otherwise be a stressful event. Most notably, I've had the pleasure of attending Leadership Development training with Gerry which allowed me to learn more about what a well-balanced leader he is. For example, I came to learn that he is a talented musician, known for his informal public performances. Gerry also takes the time everyday to maintain his fitness through daily running. These are the qualities that, for me, standout most. Gerry is a leader that works hard but finds balance - something that other leaders often fail to achieve. As I sit here typing, I smile knowing that wherever Gerry's career takes him, he will be living the 'Good Life'.

Experience
-
CloseReach
-
Canada
-
IT Services and IT Consulting
-
1 - 100 Employee
-
Quality and Compliance Manager
-
Jul 2021 - Present
-
-
-
Honeywell
-
United States
-
Appliances, Electrical, and Electronics Manufacturing
-
700 & Above Employee
-
Sr. Advanced Quality Assurance Engineer
-
Apr 2015 - Jul 2021
-
-
-
-
Principal Consultant
-
2014 - Apr 2015
Provide consulting services to Government and Private Sector clients including: - Project Management - Quality Systems (AS9100, ISO9001) - Document Management - Process auditing, - Process development, - Continuous improvement and - ESD Control. Provide consulting services to Government and Private Sector clients including: - Project Management - Quality Systems (AS9100, ISO9001) - Document Management - Process auditing, - Process development, - Continuous improvement and - ESD Control.
-
-
-
General Dynamics Mission Systems–Canada
-
Canada
-
Defense and Space Manufacturing
-
700 & Above Employee
-
Manager, Quality Systems and Continuous Improvement
-
2008 - 2014
Responsible for several major company wide projects including: Guided the company, across three major sites in Canada, to successful implementation of the ISO 9001 /AS9100 Quality Management System (QMS) ensuring registration was achieved within a defined budget and with minimum impact to the business.Implemented and managed a program of business audits (100 + per year) which covered all aspects of the business including HR, IT, Legal, Security, Business Development, Procurement, Manufacturing and Engineering, ensuring compliance to business practices, quality, environmental, health & safety and regulatory standards.Developed and successfully implemented a document reduction strategy to identify non-value-added processes. This effort resulted in a 60% reduction in the volume of process documents company wide, reducing the number of documents from 1200 to under 500. The end result was an efficient and cost effective system, which was used by employees in all disciplines across the company. This effort also resulted in approx. $300,000 in savings to the company over 3 years.Implemented and managed a Corrective and Preventive Action (CAPA) system, facilitating users to resolve and bring to closure hundreds of nonconformities annually, ensuring timely and effective corrective action throughout the Quality System Led a cross functional team in the implementation a highly effective Continuous Improvement (CI) Program which produced cost savings of $9.6 million over 4 years using ‘Lean’ principles and other CI methodologies.Worked in collaboration with senior management to design, develop and implement an employee driven continuous improvement initiative, which increased employee involvement to over 40% (over 600 employees) and contributed over 1000 cost savings ideas being implemented annually.
-
-
Manager, Document and Data Control
-
2008 - 2014
Managed the document and data control function for the Corporation, maintaining hundreds of documents under configuration control in accordance with internal policy and ISO Standards. Managed the documentation system for the company (2000 + employees) ensuring all policies and procedures were controlled, current and available to employees as needed. Implemented a process harmonization initiative which merged documents from three sites into one effective system.Developed and successfully implemented a company standard document template utilizing the SIPOC (Supplier-Input-Process-Output-Customer) process model, which resulted in all processes being clearly defined, consistent in format, and providing real value to end users.
-
-
Quality Auditor
-
2000 - 2008
Worked in collaboration with Quality Management to develop and implement an audit program which covered all aspects of the business. Implemented and managed an Electrostatic Discharge (ESD) Control Program which included process implementation, training and auditing for compliance, ensuring minimum risk of ESD damage to customer product.Created, developed and delivered a training program, which ensured all employees were aware of and involved in the Quality System, resulting in a high level of engagement at all levels across the company.Created, developed and implemented an online training program to ensure that all employees were trained in ESD controls and practices. This program has been running successfully for 10 years and is used for the bi-annual certification of all employees in the company.
-
-
-
Mitel
-
Telecommunications
-
700 & Above Employee
-
Quality Engineering
-
1996 - 2000
Responsible for all internal audit activity including Quality System, ESD, product and process audits ensuring that all audits were planned, performed and concluded within a defined schedule.Responsible for the analysis of customer returned product in order to determine root cause of field failures and implement corrective action to prevent recurrence. Implemented an ESD Control Program which included process implementation, training and auditing for compliance, ensuring minimum risk of ESD damage to customer product.
-
-
-
-
Auditor
-
1992 - 1996
As a member of the Internal Audit team, performed Quality Management System process audits on all company processes as part of the ISO 9000 registration requirements
-
-
Computer Technician/ Repair Facility Supervisor
-
1984 - 1992
Responsible to lead a team of 6 computer repair technicians in the repair and refurbishment of customer returned product.Responsible for repair and refurbishment of computers – both mainframes and accessories.
-
-
Computer Assembler/ Computer Technician
-
1975 - 1984
Responsible for repair and refurbishment of computers – both mainframes and accessories.Responsible for the assembly of computer mainframes and accessories.
-
-
Community
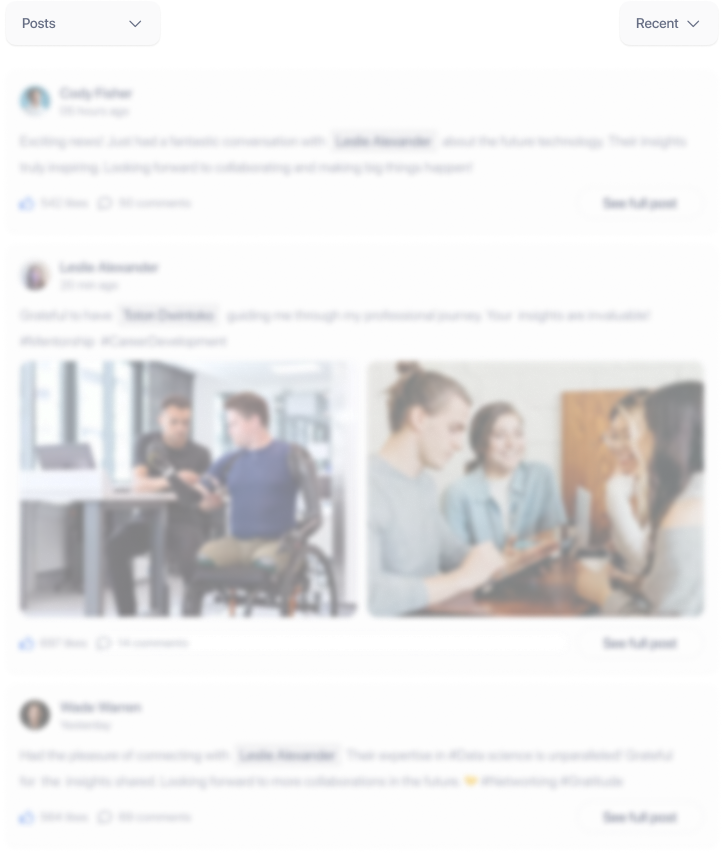