George Mendoza
Quality Manager / mgt rep at W Machine Works, Inc.- Claim this Profile
Click to upgrade to our gold package
for the full feature experience.
Topline Score
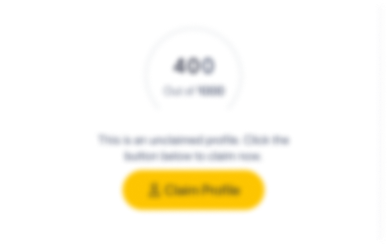
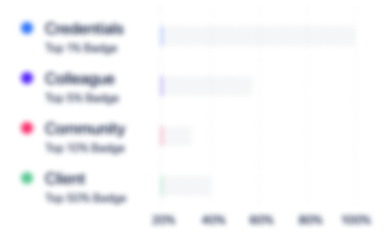
Bio
0
/5.0 / Based on 0 ratingsFilter reviews by:
Experience
-
W Machine Works, Inc.
-
United States
-
Aviation & Aerospace
-
1 - 100 Employee
-
Quality Manager / mgt rep
-
Jul 2013 - Present
Ensures that the QMS complies with customer, regulatory agencies, supplier, and company requirements; ensures that the QMS is followed by employees; ensures employees are trained; addresses customer corrective actions; establishes and maintains company policies; write, revise and maintains all QMS docs; investigates and completes root cause corrective action requests; Ensures that the QMS complies with customer, regulatory agencies, supplier, and company requirements; ensures that the QMS is followed by employees; ensures employees are trained; addresses customer corrective actions; establishes and maintains company policies; write, revise and maintains all QMS docs; investigates and completes root cause corrective action requests;
-
-
-
-
Quality/Product Engineer
-
Dec 2007 - Jun 2013
-
-
-
Integrated Magnetic Systems
-
United Kingdom
-
Biotechnology Research
-
1 - 100 Employee
-
Project Manager
-
2004 - 2006
Main responsibilities support low cost manufacturing region. Created manufacturing drawing, Quality control plans for product realization. Interfaced with customer engineers to identify and solve manufacturing and quality Issues. Created 2D drawings from customer solid model for product manufacturing. Created 3D solid model from customer 2D drawings for CNC programming. Worked with machinist and processing houses to ensure all the customer Requirements were met Key accomplishments: Reduced product cost by 15 percent Applied lean principles in the manufacturing area Show less
-
-
-
W Machine Works
-
United States
-
Aviation & Aerospace
-
1 - 100 Employee
-
Mechanical Engineer
-
2002 - 2004
Performed contract and design review. Reviewed specifications, Blueprints. Engineering change orders, and all related requirements to manufacture product Accordingly and to ensure quality objectives were met. Created manufacturing processes and quality control plans for product realization. Created frozen product realization and quality plans for safety critical parts for Northrop Grumman. Interfaced with customer engineers to identify and solve manufacturing and quality Issues. Created 2D drawings from customer solid model for product manufacturing. Created 3D solid model from customer 2D drawings for CNC programming. Worked with machinist and processing houses to ensure all the customer Requirements are met Programmed PCDMIS Coordinate Measuring Machine (CMM) To validate first piece Inspection against 3D solid model (Cosmo soft wear) Performed internal quality audits per AS9100 requirements Lean manufacturing team member and MRB member. Participated in management reviews and daily production meetings Key accomplishments: 5’s System implementation and lean Principles Improved productivity approximately 10%. Implemented manufacturing work instructions. Recognized for valued added contribution. Show less
-
-
-
General Ceramics
-
Glass, Ceramics and Concrete Manufacturing
-
1 - 100 Employee
-
Quality Manager
-
1997 - 2002
Performed contract review, Specifications review to ensure all the quality requirements Could be met. Participated in design review, for new product launch. Created quality control plans for product realization Managed day to day quality department and quality system per ISO 9001-1994 / 2000. Audited existing quality processes, Identified critical gaps and designed new corrective Procedures Wrote work procedures. Trained staff to achieved quality objectives Implemented Quality improvement program including spot audits, root-cause analysis, And implementation of remedial actions. Handle customer complaints including physically visiting customer plants and Collaborating with production engineers to Identify and solve issues. Approved and disapproved suppliers based on quality delivery and cost Reduced cost for customers on various programs with combine continues Collaboration with customer, colleagues, and vendors. Implemented six sigma visual planning to especial programs. Trained personnel the concept of mechanical inspection and methodology. Maintained root cause and corrective action as well as preventive actions. Prepared various quality performance reports to customers. Oversaw receiving inspection of processed and raw materials and communicated Quality and delivery issues to approved suppliers. Key accomplishments: Reduce scrap approximately 10%. Participated in the transition of ISO 9001-1994 Standards. to ISO 9001-2000, Participated in certifying the company under Boeing quality system D6-82479 Appendix A Show less
-
-
Education
-
Cal State L.A
-
Glendale Community College
-
La. Trade Tech
Community
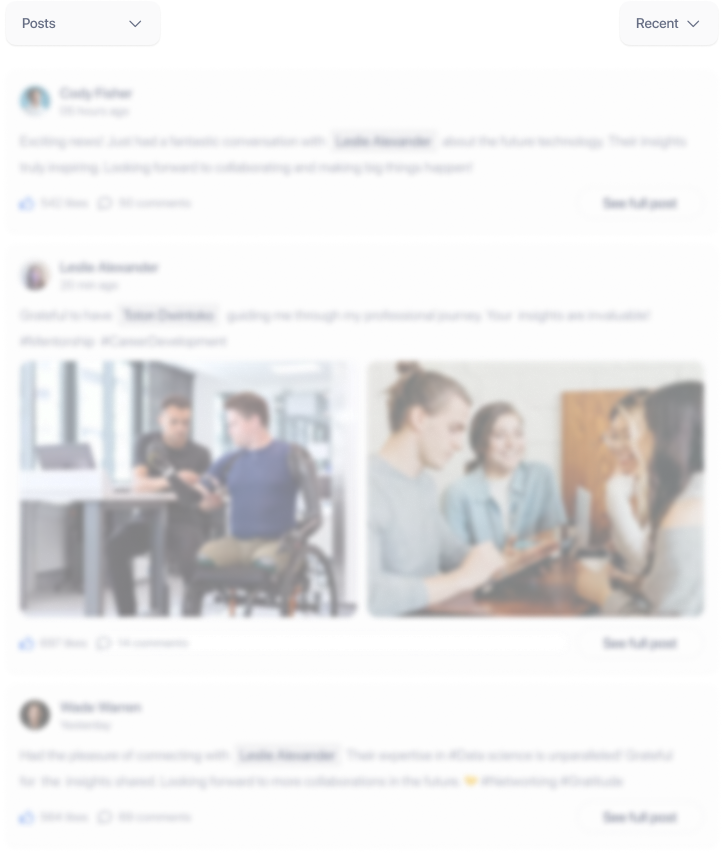