Gavin Klami
Product Development Manager at innovateIT Car Wash Equipment- Claim this Profile
Click to upgrade to our gold package
for the full feature experience.
Topline Score
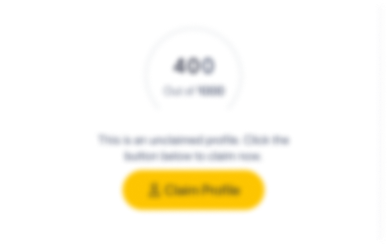
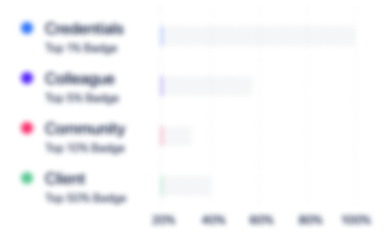
Bio


Experience
-
innovateIT Car Wash Equipment
-
United States
-
Machinery Manufacturing
-
1 - 100 Employee
-
Product Development Manager
-
Oct 2022 - Present
Lead engineering team in development of automated car wash equipment Lead engineering team in development of automated car wash equipment
-
-
-
Philips
-
Netherlands
-
Hospitals and Health Care
-
700 & Above Employee
-
Manufacturing Manager
-
Jan 2020 - Sep 2022
Managing growing high tech line producing, industry first, fully sealed MRI superconducting magnets-Leading 300% growth in 12 month period-Responsible for team of 120 employees-Revenue generation of over $40 million annually
-
-
Industrial Engineer
-
Nov 2017 - Jan 2020
Operations Design Transfer Lead during production launch of first of kind MRI magnet system-Developed and tracked production ramp plan including headcount, equipment and productivity targets-Lead multiple cross functional teams to develop and implement key processes based on complex new product design-Created reporting platform for senior management staff during volume ramp-Participated in structured problem-solving team targeting elimination of projected 2019 $2.1MM productivity shortfall-Lead team through achievement of customer acceptance for production released units in FDA compliant product Show less
-
-
-
M&G DuraVent
-
United States
-
Plant Manager
-
Aug 2015 - Jun 2017
Lead a team (9 direct reports, 50 additional) through all daily plant activities including production, planning, maintenance, material management, engineering, purchasing, safety, human resources, and financing-Budget for all manufacturing operations, including all direct and overhead spends, including quarterly updates and associated reporting-Increased productivity by 5% since 2014-Developed direct labor wage matrix and position requirements to control wage growth while maintaining employee relations with detailed advancement options and schedule-Lead development and execution of capital improvement projects-Guided the creation of a structured safety program that lead to first full year without lost time accident in site history-Acting project manager for ongoing plant consolidation leading direction of project budget, resource management and deliverables Show less
-
-
Manufacturing Manager
-
Jan 2014 - Aug 2015
Managed Manufacturing operation producing a variety of venting used in the HVAC industry. Led cross matrix team with measured metrics. Drove change through open communication and forward thinking mindset.-Maintained industry best lead time for build to order product-Quickly stabilized production and erased excessive past due orders within 2 months of starting position -Worked with hourly workforce to create two-way communication of improvement
-
-
Manufacturing Engineer
-
Feb 2011 - Jan 2014
Played key support role to manufacturing operations-Heavily involved in factory relocation, including layout of all production equipment and coordination of subcontractors-Worked to standardize production processes and documentation-Created tooling for increased throughput and quality control-Original member of Duravent Lean Manufacturing team, involved in first Kaizen event-Key engineering resource in transition to SAP, specialized in MM and PP modules
-
-
-
-
Production Supervisor
-
Jul 2010 - Feb 2011
Led the growth of key production cell to three shift operation and production increase of 350% -Hired, scheduled and trained production staff -Developed maintenance program to stabilize equipment -Created standard work to better predict and control production output Led the growth of key production cell to three shift operation and production increase of 350% -Hired, scheduled and trained production staff -Developed maintenance program to stabilize equipment -Created standard work to better predict and control production output
-
-
-
Serotta Competition Bicycles
-
United States
-
Retail Apparel and Fashion
-
CNC Program Design and Operation
-
Mar 2009 - Jul 2010
Worked with R&D on production development while maintaining existing product runs-Assisted in creating MRP to accurately track material supply and usage-Implemented design changes of existing products to improve run times, final quality and decrease tooling costs-Operated HAAS VF-3 and SL-20 Milling centers including all setups, basic product scheduling and machine maintenance-Provided design input for appropriate production requirements during design and prototyping phases-Worked closely with other production areas to address machining issues, fixturing improvements, and overall process flow-Developed machine costing figures for budget based product development and improvements Show less
-
-
Design Engineer
-
Sep 2008 - Mar 2009
Played role as consultant to design a new version of an adjustable sizing bicycle-Designed basic layout of adjustable sizing bicycle to measure riders for high end custom bicycles-Chose suppliers and worked with subcontractors to ensure viable design-Worked through prototyping stage of product release
-
-
-
Saint-Gobain Abrasives
-
United States
-
Industrial Machinery Manufacturing
-
700 & Above Employee
-
Plant Engineer
-
May 2007 - Sep 2008
Collaborated within group responsible for design of new capital equipment projects and support of existing production equipment. -Mechanical design of production improvement projects to lower production costs and raise quality -Designed machine layouts and implemented process improvements to maximize product output and reduce waste by up to 17% -Administered facility improvement projects of the plant structures -Conducted testing of manufacturing feasibility with new machine design in a controlled R&D environment -Supported maintenance shop and production with training on new equipment and processes Show less
-
-
-
GE
-
Brazil
-
Engineering Services
-
1 - 100 Employee
-
Steam Turbine Accessory Engineer
-
Oct 2006 - May 2007
Aided in the design and implementation of large scale steam turbine lubrication systems -Calculated flow and pressure requirements for turbine rotors in new plant design -Assembled bill of materials for lubrication modules for production ordering -Supported existing installations with trouble shooting of field issues -Met with vendors to assure quality standards before final release to customers Aided in the design and implementation of large scale steam turbine lubrication systems -Calculated flow and pressure requirements for turbine rotors in new plant design -Assembled bill of materials for lubrication modules for production ordering -Supported existing installations with trouble shooting of field issues -Met with vendors to assure quality standards before final release to customers
-
-
-
Rutgers Formula Racing
-
United States
-
Industrial Machinery Manufacturing
-
1 - 100 Employee
-
President
-
May 2004 - May 2006
Managed student Formula SAE organization to ensure that all team goals were obtained-Headed recruitment efforts and new member training-Performed extensive cost analysis and generated reports for updates and competition-Aided members in overall vision and ensured design cohesiveness-Held bi-weekly meetings to keep vehicle production on track-Piloted team to best finish in five year period, and second best in team's 14 year history-Ensured proper and actuate vehicle testing was performed throughout the year-Assisted in advanced machining techniques such as CNC of structural components and development of composite layup techniques Show less
-
-
Engine Team Leader
-
Sep 2003 - May 2004
Supervised power plant design, testing and implementation in vehicle.-Designed intake, exhaust, cooling and fuel systems for optimal combination of reliability, power, fuel economy and cost.-Fabricated intake using wet lay-up carbon composite methods.-Built exhaust, cooling and fuel systems with standard machine shop tooling.-Created and tested engine map using large amounts of dynamometer testing to optimize design goals.
-
-
Education
-
Rutgers University
BS, Mechanical Engineering
Community
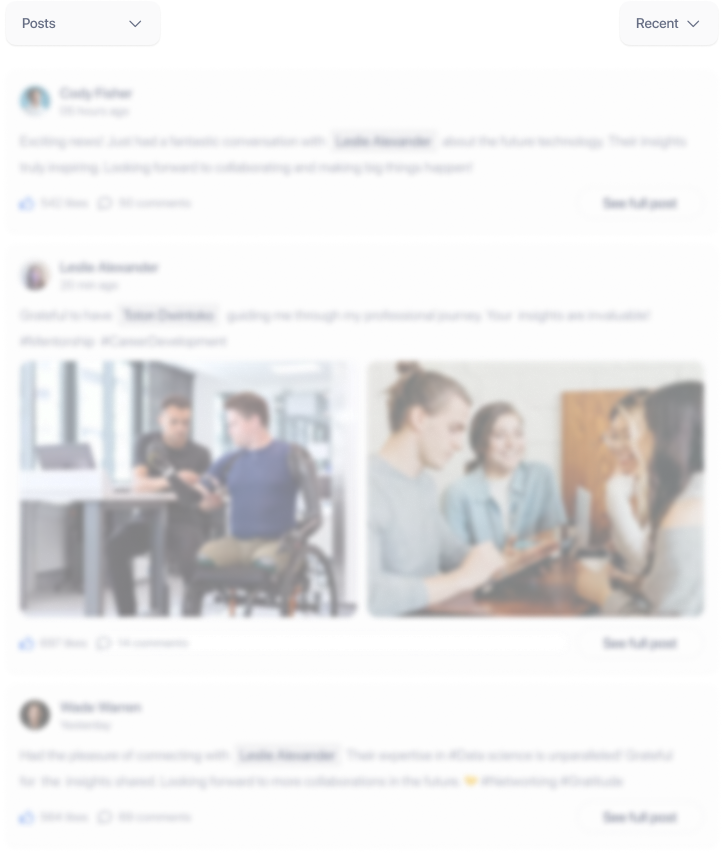