Gary Willcutt
Project Manager at Southern Synergy, Inc.- Claim this Profile
Click to upgrade to our gold package
for the full feature experience.
Topline Score
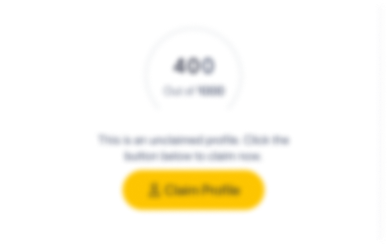
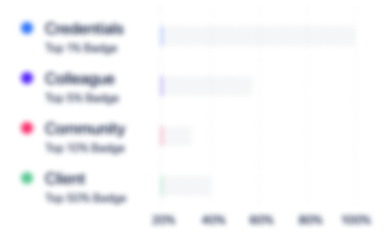
Bio


Experience
-
Southern Synergy, Inc.
-
United States
-
Mechanical Or Industrial Engineering
-
1 - 100 Employee
-
Project Manager
-
Mar 2022 - Present
-
-
-
Nouryon
-
Netherlands
-
Chemical Manufacturing
-
700 & Above Employee
-
Control Systems Engineer
-
Jul 2020 - Present
-
-
-
Akzo Nobel
-
Poland
-
Chemical Manufacturing
-
1 - 100 Employee
-
Control Systems Engineer
-
Nov 2017 - Jul 2020
-
-
-
Shell Global Solutions (US) Inc.
-
Norway
-
Architecture and Planning
-
1 - 100 Employee
-
Senior Automation Engineer
-
2012 - 2015
Provided technical assurance for a variety of projects including small scale, modular LNG manufacture and bio-fuels at various locations involving several DCS manufacturers and Fieldbus technology. Direct involvement with the site and the contract engineering companies. Responsible for achieving project discipline goals, coordinate with other disciplines, plant representatives and contractors, developed, evaluated and implemented cost saving recommendations. Technical Authority for decisions regarding application of specifications. Provided technical expertise for development of front end scopes, estimates and schedules at the early stages of project development.
-
-
-
-
Senior Automation Engineer
-
2010 - 2012
Provide technical assurance during construction, commissioning and start-up of the Sour Crude Unit and the Delayed Coke Unit, two major process units for the Crude Expansion Project that expanded the Port Arthur refinery from 275 MBPD to 600 MBPD. Supported QA during system turn over and responsible for system sign off for instrumentation. Direct interfaces with existing plant personnel, vendors, managing contractor, contractor engineering, and construction to resolve issues based on fit for purpose solutions. Additional responsibilities include developing cost effect work process for handling instrumentation during piping system hydro testing. Also complete technical evaluation of instrumentation spare parts for the total project (+50,000 devices).
-
-
-
-
Senior Control & Automation Engineer
-
2007 - 2010
Provide technical support and assurance during engineering design for Central Processing Facility (CPF) and the Field Logistics Base (FLB) of the Gbaran-Ubie Integrated Oil and Gas Project, located in the Niger Delta of Nigeria. Review design specifications, drawings, procedures and procurement documents. Owner's lead for Factory Acceptance Testing for process control system that utilizes Fieldbus technology, Safety systems, and Fire and Gas systems, including FAT of the 13 modular buildings housing all control systems. Control and safety systems topology include the main control building, four CPF Field Auxiliary Room (FAR) buildings, and eight FARs at remote manifold and well locations.
-
-
-
-
Construction Assurance Manager
-
2004 - 2007
Construction Assurance Manager, Norco Re-instrumentation program, Phase 1 and 2 Upgrade of OL-5. Converting control systems from pneumatic loop control to Fieldbus DCS control without shutdown of operating process units (hot cut over). Responsible for assembling and maintaining the inspection and engineering support team at the job site to assure the constructed automation assets/systems are integrated and installed per the design requirements. Accountable for final CA sign-off of system packages presented by the Main Automation Contractor (MAC). Ensured technology transfer to the plant through documentation and training support. Established and tracked the cost/budget of the CA inspection team. Provide technical expertise for development of front end scopes, estimates and schedules at the early stages of project development for Broadwater LNG Re-gasification Project, a floating storage and re-gasification vessel and Deer Park HT-2 Reactor Upgrade. Lead update of Shell Engineering Guides and General Specifications to incorporate Fieldbus Technology into the field inspection and loop checking procedures.
-
-
-
Shell Global Solutions (US) Inc
-
Norway
-
Architecture and Planning
-
1 - 100 Employee
-
Instrument Specialist
-
2002 - 2004
Provided technical assurance for a variety of Shell Chemical projects at various locations involving several DCS manufacturers using Fieldbus technology. Direct involvement with the site and the contract engineering companies. Responsible for achieving project discipline goals, coordinate with other disciplines, plant representatives and contractors, developed, evaluated and implemented cost saving recommendations. Worked as disciple lead for Construction Quality Assurance of instrumentation associated with the Pygas project at Norco. Provided technical expertise for development of front end scopes, estimates and schedules at the early stages of project development. Provided start-up assistance.
-
-
-
BE&K Engineering Company
-
United States
-
Construction
-
1 - 100 Employee
-
Group Leader - Instrumentation
-
1997 - 2002
Instrumentation design lead for major capital projects involving both continuous and batch processes. The plant designs have been in petrochemical, chemical, pulp & paper, oil and gas and bulk pharmaceutical chemical facility requiring validation in accordance with FDA Good Manufacturing Practices. Construction on “green-field” sites is common, requiring all site development, utilities, offices, warehouse and waste treatment in addition to the process structure. Process control provided by various DCS and/or PLC systems interfaced with vendor supplied control systems. Develop vendor and contractor bid documents, produce technical evaluations and recommend vendor or contractor selection. Manage and coordinate vendor and contractor work as part of overall design and construction. Provide technical assistance for construction, commissioning, and start-up. Duties include supervising the work of up to fifteen engineers and designers, maintaining project schedule, making work assignments and monitoring progress of both direct and contract employees. Clients: OCI Chemical Corporation, Decatur Alabama - Continuous production of 40,000 metric tons per year of Coated Sodium Percarbonate. Process control with Foxboro IA series DCS and interfaced with vendor supplied PLC and weigh systems. Provided technical assistance for construction, commissioning, and start-up. E. I. du Pont de Nemours & Co., DeLisle, Mississippi -- Conversion of two production lines to Honeywell DCS. Raisio Group, Summerville, South Carolina --STAEST 4 project, batch production of 15,000-tons per year of Stanol Ester. Process control was provided by Valmet DCS. Provided technical assistance for construction, commissioning, and start-up. Olin Corporation, McIntosh, Alabama -- Capacity increase of the brine treatment plant. International Paper, Erie, Pennsylvania -- No. 18 and 19 low NOx burners controls upgrade. Provided construction and technical assistance during shutdown and start-up.
-
-
-
TMS, Inc.
-
United States
-
Industrial Machinery Manufacturing
-
1 - 100 Employee
-
Engineering/Project Manager
-
1994 - 1997
Engineering/Project manager, responsible for all aspects of engineering, design, planning, scheduling, estimating and supervision of on-going capital projects. Supervised in house design group of eight engineers and designers. Developed and monitored department’s budget, improved administrative systems, made recommendations for changes, and monitor effectiveness. Made improvements to the project cost tracking system; monitor cost and profitability of all engineering jobs. Developed proposals and cost estimates. Developed construction bid documents; technical and commercial bid evaluations; technical support for shutdown/projects. Made work assignments of design personnel, developed technical company promotional literature. Involved in Process Safety Management consulting and developed technical procedures for the Mechanical Integrity element of Process Safety Management.
-
-
-
-
Instrument Group Leader
-
1988 - 1994
Clients: Mobil Exploration and Producing US, Coden, Alabama - Hydrocarbon extraction and treating project. "Fast track" project. Bay Gas Storage Co., Ltd., McIntosh, Alabama -- New 260 MMSCFD salt dome storage compression facility. Emergency Shutdown System, Allen Bradley PLC 5 for process distributed control and communications capabilities for remote process control. Scott Paper Company, Mobile, Alabama -- Installation of a new Celleco saveall and associated equipment for the No. 4 paper machine. Provided construction assistance and start-up coverage of installation. Scott Paper Company, Mobile, Alabama -- Replacement of a cross direction control system and installation of a caliper profiler on the No. 4 paper machine. Provided construction assistance and start-up coverage of installation. Enron Gas Processing, Houston, Texas --Two butane isomerization units. Eka Nobel, Columbus, Mississippi -- Two major "fast track" sodium chlorate projects. Provided technical support for Bailey DCS configuration and system architecture, factory checkout and field start-up, and construction assistance and start-up coverage. Eka Nobel, Columbus, Mississippi -- Provided start-up assistance for a sodium chlorate plant, which included field instruments, analyzers, and Bailey DCS. Integration of existing panel mounted controls into new DCS system, deactivation of existing control room, and combining existing plant controls into new control building. International Paper, Moss Point Mississippi -- Installation of Impact System's first infrared gas dryer system. Mead Paperboard, Stevenson, Alabama -- Installation of a Beloit extended nip press.
-
-
-
-
Section Engineer
-
1986 - 1988
Instrument engineer for three major "fast tract" specialty chemical projects including coordination with plant and engineering consultant. Responsible for instrumentation design, specification, construction, commissioning, and start-up. Provided technical support for the plant project engineering group, operations, and maintenance. Development of plant policies for Process Hazards Management, Inspection, Testing and Quality Assurance. Instrument engineer for three major "fast tract" specialty chemical projects including coordination with plant and engineering consultant. Responsible for instrumentation design, specification, construction, commissioning, and start-up. Provided technical support for the plant project engineering group, operations, and maintenance. Development of plant policies for Process Hazards Management, Inspection, Testing and Quality Assurance.
-
-
-
Shell Chemical Co
-
United States
-
Legal Services
-
1 - 100 Employee
-
Instrument Engineer
-
1980 - 1986
Plant instrument engineer for two major projects, reviewing contract engineering and following both jobs from engineering consultant’s office to the field through start-up. Provided engineering support for plant project engineering group and for routine plant maintenance. Plant project engineer on minor projects, established instrumentation spare parts and stocking levels for batch type chemical process unit. Plant mechanical/instrument maintenance engineer on shift covering commissioning mechanical equipment and instrumentation and troubleshooting start-up related problems. Worked with maintenance technicians in troubleshooting start-up problems of the process unit. Handled capital projects associated with the process unit. Handled day-to-day maintenance problems as well as long range problems in the unit.
-
-
-
Shell Chemical
-
United States
-
Legal Services
-
1 - 100 Employee
-
Instrument Engineer
-
1977 - 1986
-
-
Education
-
George County High School
-
Mississippi Gulf Coast Community College
-
Mississippi State University
Engineer’s Degree, Mechanical Engineering
Community
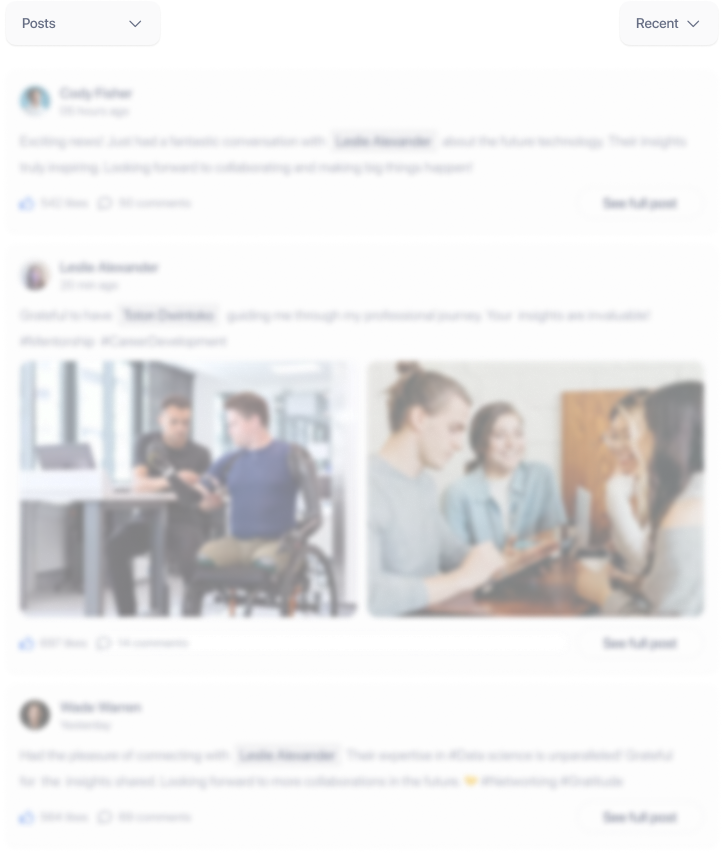