Gary Williams
Factory Manager at Humdinger Foods- Claim this Profile
Click to upgrade to our gold package
for the full feature experience.
Topline Score
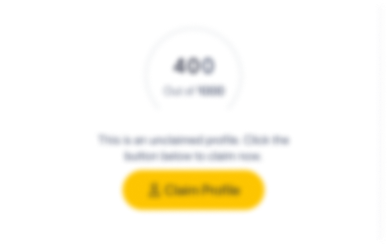
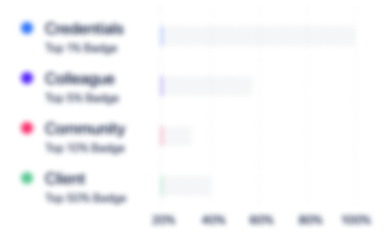
Bio


Experience
-
Humdinger
-
United Kingdom
-
Food and Beverage Manufacturing
-
1 - 100 Employee
-
Factory Manager
-
Feb 2020 - Present
Facilitating the accurate efficient and safe production of all products manufactured at the Hull production and processing sites. Managing all staff within department to achieve optimum labour targets. Ensuring accurate stock control at every stage of manufacture. Driving KPI's to reduce waste and maintain the highest quality within all areas of the operation. Leading and coaching all staff in best in class production practices and Lean Manufacturing principles. Promoting Humdinger values within all areas of the 2 Hull sites.
-
-
-
Cargill
-
United States
-
Food and Beverage Manufacturing
-
700 & Above Employee
-
Manager
-
Mar 2013 - Feb 2020
Managing the day to day operations of the plant, delivering all key performance criteria in line with the business objectives. Accountable for the delivery of production on time to plan and at the right cost and quality levels to meet and exceed customer requirements and to ensure the shift teams operate in line with legal safety standards. Building employee engagement through positive working relationships and encouraging an open and honest environment where employees want to offer their ideas. Delivering safety results through proactive application of hazard spotting and a disciplined approach to risk assessment and accident reporting. Developing and coaching team on lean manufacturing principles and thinking to be able to identify waste within the org. Utilising and managing our multi skilled team to identify, troubleshoot and action workplace issues in a timely manner. Planning and managing plant production shutdowns and liaison between other functional such as maintenance, contractor and operational teams.
-
-
-
Kimberly-Clark
-
United States
-
Manufacturing
-
700 & Above Employee
-
Shift Leader
-
Apr 2010 - Mar 2013
Primarily responsible for the operating performance of the Barton Mill ensuring the Safety, Quality & Productivity targets were achieved, through leading and motivating a shift operations team, ensuring that all team members are aware of the Mill KPI’s, their performance against them and the need for continuous improvement.Leader of site Emergency Response Team, ensuring all emergency situations are dealt with swiftly and in accordance with the ERT procedures.The Shift leader role is focused on people management, driving the right behaviors through leading by example, positive reinforcement, coaching and mentoring on a daily basis, as well as managing individual development through personal appraisals. Responsible for compliance to Health & Safety Policies, including; Vessel entry, hot work and working behind guards permits, writing temporary risk assessments, as well as performing incident / HIPO investigations. Managing staff through HR policies: Absence, Performance Management, Disciplinary and Appraisal. Maintaining an open door policy and being accessible to staff for support & guidance on personal or work related issues.Managing resource allocation, ensuring the correct levels of manning and skill mix are available to meet operations demands..
-
-
Lean Manufacturing Coach
-
Jan 2008 - Apr 2010
Supporting the implimentation of Lean manufacturing by mentoring shift associates in lean principles by providing tools and techniques including mental models, waste walks, visual management, standard work and 4 step problem solving to encourage behaviours that drive actions to achieve business results.
-
-
-
Kimberly Clark
-
Barton Upon Humber
-
Line Leader
-
2002 - Sep 2008
-
-
-
Kimberly-Clark
-
United States
-
Manufacturing
-
700 & Above Employee
-
Manufacturing Technician
-
1993 - 2001
-
-
Education
-
The University of Hull
Level 5 diploma, Management and Leadership -
Wolfreton High Scool
Community
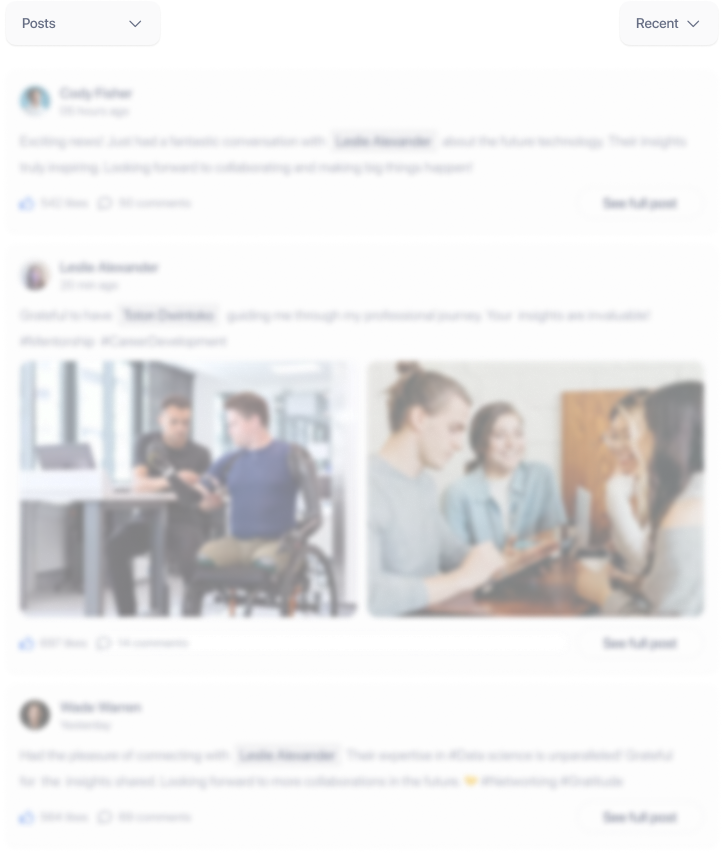