Gary Munro
Operations Manager at Peter Equi & Sons- Claim this Profile
Click to upgrade to our gold package
for the full feature experience.
Topline Score
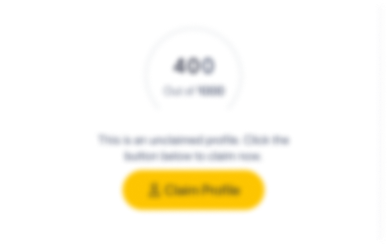
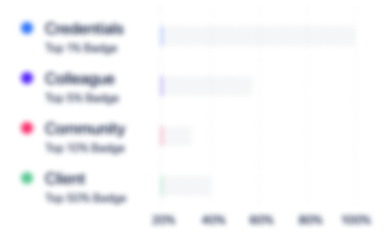
Bio


Experience
-
Equi's Ice Cream
-
United Kingdom
-
Food and Beverage Services
-
1 - 100 Employee
-
Operations Manager
-
Nov 2013 - Present
Hamilton, South Lanarkshire, United Kingdom
-
-
-
Cake Décor Ltd
-
United Kingdom
-
Food and Beverage Manufacturing
-
1 - 100 Employee
-
Operations Manager
-
Sep 2010 - Aug 2013
Cumbernauld • Member of 5 person Senior Management Team which increased turnover from £5-£8mill in 3 years • Manage the Manufacturing, Engineering and Warehouse functions. • Reduced wastage to less than 2.5% equivalent to a 50% reduction. • Reduced headcount by 10% through sourcing equipment in order to mechanise previously manual tasks. • Project managed the move to new factory. Including the design, layout and building of a new production area and warehousing area. • Responsible for Health… Show more • Member of 5 person Senior Management Team which increased turnover from £5-£8mill in 3 years • Manage the Manufacturing, Engineering and Warehouse functions. • Reduced wastage to less than 2.5% equivalent to a 50% reduction. • Reduced headcount by 10% through sourcing equipment in order to mechanise previously manual tasks. • Project managed the move to new factory. Including the design, layout and building of a new production area and warehousing area. • Responsible for Health and Safety throughout the site. No RIDDOR accidents in over 2 years. Implemented Risk Assessments. • Introduced comprehensive package KPI reports which allowed the business to focus on key parameters and help drive strategies for improved performance. • Reduced wastage to less than 2.5% equivalent to a 50% reduction. Show less
-
-
-
Noble Foods Ltd
-
Food Production
-
300 - 400 Employee
-
Operations Manager
-
Apr 2008 - Sep 2010
Loanhead, dinburgh • Solely responsible for setting and controlling site operational overhead budgets, totalling £4.5mill. • Manage the Manufacturing, Engineering, Warehouse, Distribution and Administration Departments • Managedsite Health and Safety. Chair Health and Safety Committee. • Managed the reduction in direct head count from 90 to 68 through improved production process efficiencies (up from 35% efficiency to 70%) and limited capital expenditure. Saving circa £350k in labour costs. • Reduced… Show more • Solely responsible for setting and controlling site operational overhead budgets, totalling £4.5mill. • Manage the Manufacturing, Engineering, Warehouse, Distribution and Administration Departments • Managedsite Health and Safety. Chair Health and Safety Committee. • Managed the reduction in direct head count from 90 to 68 through improved production process efficiencies (up from 35% efficiency to 70%) and limited capital expenditure. Saving circa £350k in labour costs. • Reduced waste packaging disposal costs by 40% through re-cycling and installation of a bailer unit. Saving £24k per year. • Reduced effluent disposal cost by 49% by introducing composite sampling system and improvements to cleaning systems. Saving £170k Show less
-
-
-
-
Manufacturing Manager
-
Mar 1998 - Apr 2008
Cumbernauld • Manage the Manufacturing, Cleaning, Warehouse and Training Departments • Responsible for site Health and Safety. No employee RIDDOR accidents in over 2 years. Chair Health and Safety Committee. • Responsible for setting yearly overhead budgets and labour standards and ensuring they are met. • Managed the reduction in direct head count from 109 to 75. Saving £500K in labour. • Reduced waste from 15% to 5% through better training and improved production processing methods. Saving… Show more • Manage the Manufacturing, Cleaning, Warehouse and Training Departments • Responsible for site Health and Safety. No employee RIDDOR accidents in over 2 years. Chair Health and Safety Committee. • Responsible for setting yearly overhead budgets and labour standards and ensuring they are met. • Managed the reduction in direct head count from 109 to 75. Saving £500K in labour. • Reduced waste from 15% to 5% through better training and improved production processing methods. Saving £150k per year. • Integral member of 4 member team responsible for the design and installation of a fully automated naan bread production line costing £1.5mill • From 1998 to 2002 was Technical Manager in charge of Quality Control and Product Development Departments. Show less
-
-
-
-
Technical Manager
-
Feb 1996 - Mar 1998
Newbridge, Edinburgh • Managed the Technical and Cleaning Departments. • Maintaining and refining existing Quality and HACCP systems. • Responsible for ensuring all food manufacturing legal requirements were met. • Responsible for ensuring product quality parameters were met. • Close liaison with the Marks & Spencer Technologist to ensure a harmonious relationship between the two businesses.
-
-
-
-
Technical Manager
-
Jan 1992 - Feb 1996
Berwick Upon Tweed • Managed the Laboratory and Quality Assurance departments • Responsible for vendor assurance. • Undertook training courses for HACCP and Basic Food Hygiene. • Installed HACCP system. • Installed BS5750 accredited quality System.
-
-
-
-
Company Support Microbiologist
-
Jan 1988 - Jan 1992
Sharnbrook, Bedford • Gave microbiological support and advice to Unlever’s food manufacturing plants in the United Kingdom, main land Europe and Scandinavia. Covering Meat and Ice Cream manufactures.
-
-
Education
-
University of Manchester - Institute of Science and Technology
Master of Science (M.Sc.), Biochemical Engineering -
University of Strathclyde
Bachelor of Science (BSc), applied microbiology
Community
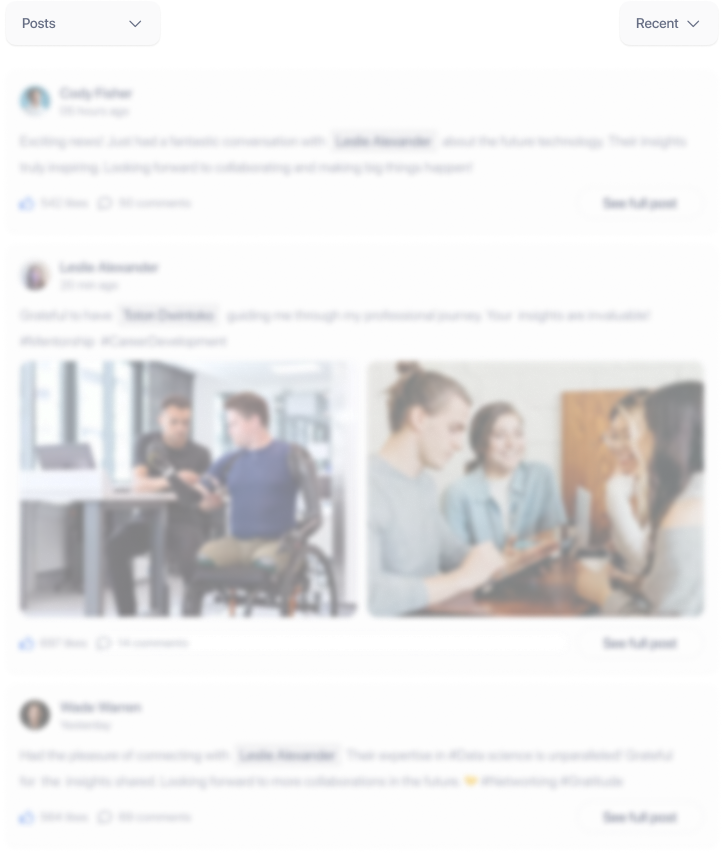