Gary Malone
Senior Implementation Specialist at Clough Wood- Claim this Profile
Click to upgrade to our gold package
for the full feature experience.
-
English -
Topline Score
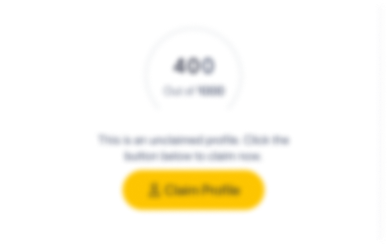
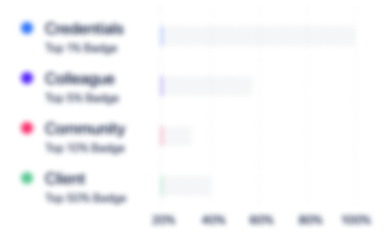
Bio


Experience
-
Clough Wood
-
Australia
-
Oil and Gas
-
100 - 200 Employee
-
Senior Implementation Specialist
-
Apr 2023 - Present
-
-
-
INPEX Corporation
-
Japan
-
Oil and Gas
-
400 - 500 Employee
-
Mechanical Coordinator
-
Aug 2022 - Jun 2023
-
-
-
Looking for work opportunities
-
Western Australia, Australia
-
Mechanical Coordinator
-
Jan 2023 - Feb 2023
Now actively looking for opportunities to return to work Now actively looking for opportunities to return to work
-
-
-
INPEX (via TRACE)
-
Perth, Western Australia, Australia
-
Campaign Mechanical Coordinator
-
Mar 2020 - Aug 2022
-
-
-
INPEX Corporation - engaged via TRACE JV
-
Perth, Western Australia, Australia
-
Mechanical Cooridinator
-
Mar 2020 - Jul 2022
Employed in the campaign offshore maintenance team for coordination of multi-disciplined work scopes. Ensure all work is fully resourced prior to the particular campaign plan, ie spare parts, vendors, isolations & permits, and then to assist with the planning, execution and then finally ensure close out of scopes on campaign completion. Employed in the campaign offshore maintenance team for coordination of multi-disciplined work scopes. Ensure all work is fully resourced prior to the particular campaign plan, ie spare parts, vendors, isolations & permits, and then to assist with the planning, execution and then finally ensure close out of scopes on campaign completion.
-
-
-
INPEX Corporation - engaged by TRACE
-
Perth, Western Australia, Australia
-
Mechanical Coordinator
-
Mar 2019 - Jul 2022
-
-
-
UGL
-
Australia
-
Engineering Services
-
700 & Above Employee
-
Valve SME - Chevron Barrow Island Train2 Turnaround 2020
-
Apr 2019 - Mar 2020
-
-
Mechanical Coordinator - Valve Turnaround Team
-
May 2017 - Mar 2020
Preparation of process valve scope in readiness for 2019 planned shutdown of LNG Train 1
-
-
Mechanical Coordinator - Major Maintenance
-
Sep 2016 - May 2017
-
-
-
Broadspectrum
-
Australia
-
Facilities Services
-
700 & Above Employee
-
Mechanical Coordinator
-
Aug 2014 - Sep 2016
Mechanical maintenance activities for offshore oil and gas assets. Coordination of mechanical maintenance in accordance with the client’s procedures and standards Resourcing work orders with materials, services and labour requirements Developing work packs, as well as coordinating, supervising and managing costs for all assigned activities Liaising with planners and offshore engineers to schedule work into campaigns Mechanical maintenance activities for offshore oil and gas assets. Coordination of mechanical maintenance in accordance with the client’s procedures and standards Resourcing work orders with materials, services and labour requirements Developing work packs, as well as coordinating, supervising and managing costs for all assigned activities Liaising with planners and offshore engineers to schedule work into campaigns
-
-
-
Cameron, a Schlumberger company
-
United States
-
Oil and Gas
-
700 & Above Employee
-
Chevron Project Manager
-
Mar 2014 - Aug 2014
Employed at Cameron International as Chevron Project Manager for Barrow Island and Wheatstone Projects, I was accountable for: Liaising with Chevron and their associated contractors for supply of maintenance services and spares for the Barrow Island and Wheatstone projects Ensuring internal departments at Cameron’s Perth office and workshops were fully compliant with contract requirements Coordinating between various departments to set up QA/QC, HES and Quarantine Management Plan for operations and supply for the Chevron Barrow Island project Ensuring the Chevron team were fully aware of the Cameron contract and the value added services that could be provided Show less
-
-
-
KOSO Kent Introl Ltd
-
United Kingdom
-
Industrial Machinery Manufacturing
-
200 - 300 Employee
-
Choke & Control Valves - Manager
-
Jul 2011 - Feb 2014
Working at Koso Kent Introl, as a control and choke valve manufacturer, as Business Development Manager, I was involved in: Growing companies’ portfolios in the ANZ region by identifying new projects and tracking them through their various stages to optimise Kent Introl’s opportunities Working with both end users and EPC contacts to provide product and technical presentations in order to develop further business opportunities Attending customer project meetings to review contract awards Liaising with the sales team to ensure all documentation QA/QC specific to the project were understood and incorporated in our offer Communicating with the projects team to ensure planning of materials, machining, testing and logistics were under control to ensure deadlines were met Providing technical support for installed base of choke and control valves and associated instrumentation Show less
-
-
-
Cameron, a Schlumberger company
-
United States
-
Oil and Gas
-
700 & Above Employee
-
Control Valve Manager
-
Mar 2007 - Jul 2011
My duties included: Ensuring all workshop and site operations were carried out safely and efficiently Managing all aspects of control valve, choke valve and PSV overhaul, testing and replacement when necessary Managing a team of six technicians, which included allocating and scheduling work, undertaking performance reviews and managing disciplinary issues Monitoring direct and indirect expenditure to ensure budgets were met Liaising with other departments, including engineering, QA/QC, machine shop, purchasing and dispatch to ensure all deliverables were met Attending management meetings to discuss and prioritise workloads Liaising with clients to establish and confirm project scope including site visits to both onshore and offshore facilities Monitoring training and certification requirements of personnel in both technical knowledge and health and safety requirements to ensure readiness for planned and unplanned site visits Preparing technical quotations and placing orders via the SAP system Coordinating and planning all aspects of shutdown work, including spare parts, work scope, packs, safety and isolation procedures, logistics and accommodation for teams numbering over 25 Managing both onshore and offshore shutdowns Finalising and authorising engineering reports to be issued to the operators Show less
-
-
-
Yokogawa
-
Japan
-
Automation Machinery Manufacturing
-
700 & Above Employee
-
Service/Sales
-
Jan 2001 - Mar 2007
Service Engineer role included the following: Managing service work on the instrumentation product range, including flow meters, pressure and differential pressure transmitters, temperature transmitters, PH & Conductivity analysers, digital controllers and recorders Ensuring that work packs/scopes contained specific requirements for isolation and PPE health and safety for the individual jobs Commissioning work on new plant start up Liaising with end users and other suppliers to set instruments HART / 4-20mA / BRAIN signals for DCS Liaising with customer with regard to onsite service requirements and quote via SAP system for appropriate service contracts Organising site visits including spares for both planned and callout work, and managing stock level requirements of spares Providing feedback to the sales team on required site upgrades Internal Sales Engineer, I was accountable for: Evaluating customer enquiries, technical and commercial, to provide quotations via the SAP system Using company sizing software to calculate and select the appropriate flow meters for the process conditions Dealing directly with process and project engineers to provide technical input and support for matters such as flow parameters, material compatibility and hazardous area requirements Organising customer visits with external sales team to gain full technical understanding and clarifications for larger projects Show less
-
-
-
Various Positions
-
United Kingdom/Global
-
Marine Engineer/ Service Engineer
-
Jan 1981 - Aug 2000
Previously working at the following companies – Service Engineer – Industrial Purification Systems (Industrial Filtration and compressed air drying) Marine Engineer – Shell Cadet Marine Engineer – P & O Shipping Company (Merchant Navy) I was responsible for – Commissioning and maintaining equipment supplied to a variety of industries Arranging service contracts with customers Performing site demonstrations with mobile unit to assist sales team in selling the technology, and assisting sales teams internally and externally with technical input Managing maintenance and operations of all the ships’ main and auxiliary power plant and machinery, both mechanical and electrical Ensuring planned and routine maintenance programs were adhered to and then evaluated for continuance or improvement During dry dock (shutdown) the management of shore side personnel, and supervising testing and start of machinery start up and commissioning Completing a cadetship (apprenticeship) in Marine Engineering Preparing equipment and spares for major overhauls Managing teams of technicians during schedule and planned maintenance regimes Show less
-
-
Education
-
Glasgow Nautical College
-
Portsmouth Nautical College
-
Campion High School, Liverpool
Community
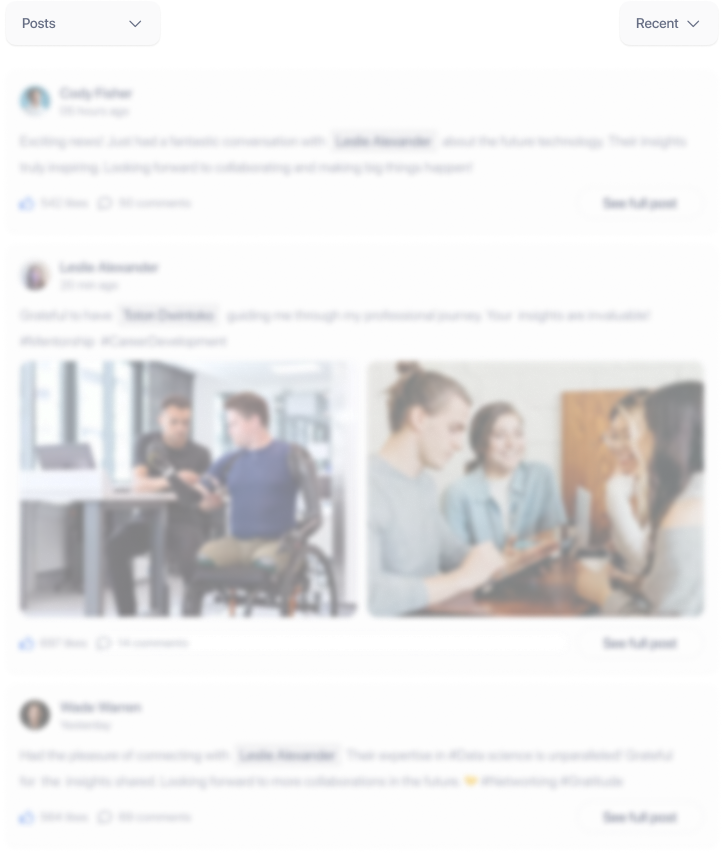