Gary Last
Hazardous area inspector at Lark Technology Group Ltd.- Claim this Profile
Click to upgrade to our gold package
for the full feature experience.
-
English -
Topline Score
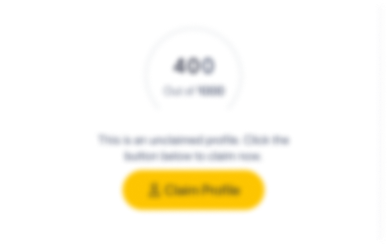
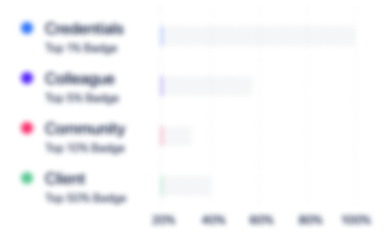
Bio


Credentials
-
Duolingo Italian Fluency: Elementary (Estimated)
DuolingoFeb, 2017- Sep, 2024
Experience
-
Lark Technology Group Ltd.
-
United Kingdom
-
Automation Machinery Manufacturing
-
1 - 100 Employee
-
Hazardous area inspector
-
Mar 2021 - Present
-
-
-
PPG Industries
-
Utilities
-
100 - 200 Employee
-
Electrical Maintenance Engineer
-
Oct 2016 - Present
Responsible for; . the installation and repair of electrical equipment in Hazardous areas. . Ensuring the safe operation of the site steam generators, including boiler checks and ordering of chemicals. . Ensure the safe operation of the cooling tower and conducting legionella checks . Assisting with mechanical inspections during routine plant maintenance shutdowns. . Ordering materials and spares. . Conducting electrical maintenance of switch gear during shutdowns. Responsible for; . the installation and repair of electrical equipment in Hazardous areas. . Ensuring the safe operation of the site steam generators, including boiler checks and ordering of chemicals. . Ensure the safe operation of the cooling tower and conducting legionella checks . Assisting with mechanical inspections during routine plant maintenance shutdowns. . Ordering materials and spares. . Conducting electrical maintenance of switch gear during shutdowns.
-
-
-
-
Maintenance Engineer
-
Oct 2015 - Oct 2016
Working in an engineering department responsible for the preventative maintenance of equipment in a paint manufacturing business. Responsibilities included conducting daily line walks and repairs as required, acting upon work requests and updating the CMMS system, assisting during shutdowns of production lines to preempt possible causes of machine failure. Working in an engineering department responsible for the preventative maintenance of equipment in a paint manufacturing business. Responsibilities included conducting daily line walks and repairs as required, acting upon work requests and updating the CMMS system, assisting during shutdowns of production lines to preempt possible causes of machine failure.
-
-
-
SLM - Everyone Active
-
United Kingdom
-
Wellness and Fitness Services
-
700 & Above Employee
-
Maintenance Technician
-
Jun 2015 - Oct 2015
Responsible for reactive and planned maintenance, contractor management, budget control. Continuous improvement of CMMS system to ensure customer satisfaction. Responsible for reactive and planned maintenance, contractor management, budget control. Continuous improvement of CMMS system to ensure customer satisfaction.
-
-
-
Muntons plc
-
United Kingdom
-
Food and Beverage Services
-
1 - 100 Employee
-
Engineering Manager
-
2003 - 2015
Team leader of engineers Principle contractor/ project manager Main contact for contractors Administrator for CMMS Team leader of engineers Principle contractor/ project manager Main contact for contractors Administrator for CMMS
-
-
Education
-
Stowupland High School
High School
Community
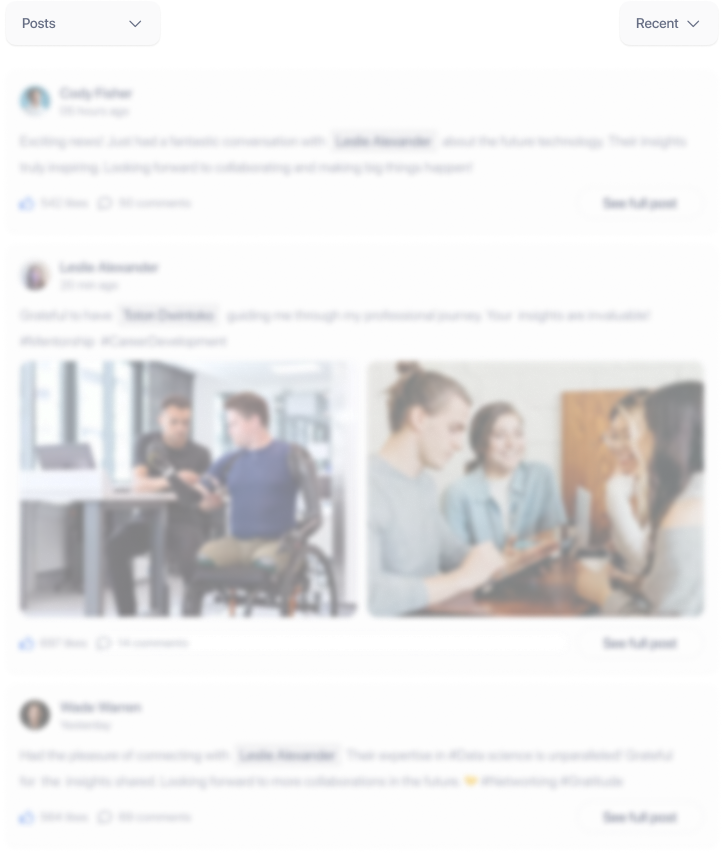