Gary Cross
Engineering Manager at Oikos Storage Limited- Claim this Profile
Click to upgrade to our gold package
for the full feature experience.
Topline Score
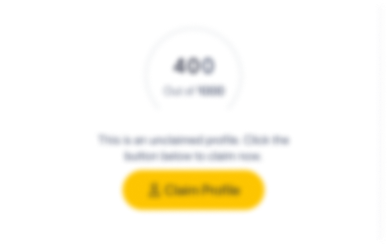
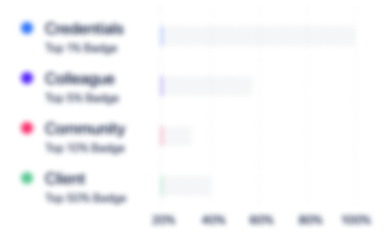
Bio
0
/5.0 / Based on 0 ratingsFilter reviews by:
Experience
-
Oikos Storage Limited
-
United Kingdom
-
Oil and Gas
-
1 - 100 Employee
-
Engineering Manager
-
Oct 2019 - Present
• Responsible for the day-to-day maintenance activities for all the equipment at the Terminal across all disciplines, including plant integrity and safety critical equipment.• Employed by Oikos to Benchmark the Maintenance Department and to introduce Best Practices such as KPI measurements to increase reliability and reduce maintenance costs.• Responsible for turnkey Projects.• Manage a £1.1 million budget
-
-
Mechanical Engineer
-
Sep 2016 - Oct 2019
• Mechanical Engineer working on a sixty-eight-million-pound project during the design, construction and commissioning phase. • Equipment installed includes, deep-water jetty, marine loading arms, access gantry, piping, valves, rotating equipment, fire suppression systems, Nitrogen skid, 12 new tanks, pig diverter valve and intelligent mooring system. • Reviewed/updated OIKOS specifications, such as Piping Fabrication/Installation, Piping Materials, Painting etc.• Authorised all mechanical vender drawings, calculations, specifications, data sheets, piping ISO’s, layout/installation drawings.• Input into Hazop, Hazid, Area Classification and MOC review meetings.• Attended vender due-diligence assessments and completed bid evaluations.• Developed the commissioning/two-year operating spare requirements.• Attended all mechanical factory acceptance tests.• Developed P&ID’s.
-
-
-
bp
-
France
-
Business Consulting and Services
-
1 - 100 Employee
-
Maintenance Reliability Engineer
-
Sep 2014 - Sep 2016
• Developed/implemented maintenance/spares strategies including Maximo upload, across all disciplines North Sea Region Platform and FPSO Projects.• Developed the condition monitoring routes • Developed/implemented maintenance/spares strategies including Maximo upload, across all disciplines North Sea Region Platform and FPSO Projects.• Developed the condition monitoring routes
-
-
-
SNC-Lavalin
-
Canada
-
Civil Engineering
-
700 & Above Employee
-
Principal Mechanical Engineering (Rotating) & Lead Engineer
-
Oct 2012 - Dec 2013
• Completed a Platform Top Side Feed Project for the Venezuelan Government designing the Rotating Equipment and then becoming the Lead Engineer, across all disciplines • Completed a Platform Top Side Feed Project for the Venezuelan Government designing the Rotating Equipment and then becoming the Lead Engineer, across all disciplines
-
-
-
Petroplus
-
Belgium
-
Oil and Gas
-
100 - 200 Employee
-
Mechanical Engineering Team Leader
-
Feb 2009 - Oct 2012
• Led (Technical Authority) a team of professional Mechanical Engineers to optimise plant reliability, safety, cost and efficiency across the refinery.• Covered the Rotating equipment specialist role from April 2011.• Mechanical/Inspection lead for the 2009 refinery shutdown, managing works fronts, work scopes, work pack completion and technical queries.
-
-
Project Managed a Major Gas Turbine & Boiler Overhaul June 2008 - Feb 2009
-
Jun 2008 - Feb 2009
• Completed within the set schedule, within budget (£3million), meeting all the objectives and with an excellent safety record.
-
-
Machinery Team Leader
-
Jul 2007 - Jun 2008
• Managed the day-to-day rotating equipment maintenance activities with a team of twenty-three technicians, seven apprentices, four contractors and a planner.• Reduced backlog man-hours from 15,000 to 9,000hrs and made various reliability improvements. Coached technicians/apprentices with quality issues, promoted “get it right first-time culture”.
-
-
-
-
Reliability Engineer
-
Jul 2002 - Jul 2007
• Defined workscope for long/medium term reliability improvements and Projects.• Updated the Refineries Standards, Policies & Procedures, Piping Classes, Engineering Maintenance Strategies and Mechanical Reliability Forms.• Developed a new/replacement equipment tendering document.• Planned and executed two major machine overhauls, one of the machines being a Project improvement, during a planned plant shutdown.• Defined/executed work scopes for BP’s 2005 Refinery Shutdown (March 2004 – June 2005).• Defined work scopes for two Sulphur Plant shutdowns.• Became the SPA for our Sulphur plants, Gulftronic filtration, and seven reciprocating compressors.• Defined work scopes for BP’s 2006 Refinery Shutdown (June 2005 – June 2006).
-
-
-
Cargill
-
United States
-
Food and Beverage Manufacturing
-
700 & Above Employee
-
Maintenance Supervisor/ Reliability Engineer
-
Jun 2000 - Jun 2002
• Responsible for the day-to-day maintenance activities including rotating/static equipment. With a team of twelve technicians, five shift technicians and various sub contractors.• Employed by Cargill to Benchmark the Maintenance Department and to introduce Best Practices such as KPI measurements to increase reliability and reduce maintenance costs. • Responsible for the day-to-day maintenance activities including rotating/static equipment. With a team of twelve technicians, five shift technicians and various sub contractors.• Employed by Cargill to Benchmark the Maintenance Department and to introduce Best Practices such as KPI measurements to increase reliability and reduce maintenance costs.
-
-
-
Shell
-
Oil and Gas
-
1 - 100 Employee
-
Senior Rotating Equipment Engineer
-
Apr 1998 - Dec 2000
• Technical adviser for all aspects of the refinery’s rotating equipment including investigations into equipment failures using Root Cause Analysis Techniques. Defining repair scopes, implementing reliability improvements generally from Reliability Centred Maintenance Studies, planning major overhauls, Project scope/implementation/commissioning, updating Engineering working instructions, developing maintenance systems and condition monitoring which includes vibration analysis and oil sampling.• Has impact on refinery maintenance budget of £3 million, 1998’s figures show the refinery came within budget due to excellent reliability and constant condition monitoring.• Focal point for rotating equipment spare parts, where in 1998 stock levels where finely tuned, resulting in a benefit to the business of about £500k. • Asset owner for Shell’s Frame 5 Gas turbine driving a 25MW generator combined with a waste heat boiler. Planned, managed, and executed the 1998 maintenance shutdown within budget and duration without any safety incidents.• Managed the refinery’s Key Performance Indicators which assess rotating equipment bad actors and mean time between pump failures, refinery average in 1997 was 80 months, which increased to 109.
-
-
Area Engineer (Manager) & Senior Rotating Equipment Engineer Apr 1999-May 2000
-
Apr 1999 - May 2000
• Managing all maintenance activities including budgets (£3.5 million), safety, contract performance and people. The Area covers the following plants, Tankage, Jetties, Crude Distiller, Boiler House, High Vacuum Unit, Bitumen Unit, Cooling Water, Flare Recovery Unit and LPG Facilities.• Managing a team comprising of a Support Engineer, two supervisors, a planner, a work force labour pool of thirty-two and fourteen mechanical technicians.
-
-
Mechanical Engineer (Rotating Equipment) and Workshop Manager
-
Jan 1997 - Apr 1998
• Planning and costing the maintenance works for rotating equipment as per operation requirements, ensuring deadlines, safety and quality were kept.• Organising services, materials, subcontracts for a team of twelve mechanical technicians.• Controlling an annual budget for contracts, materials, tools, and overheads of £1.4 million.• Planned and executed major rotating equipment overhauls during the maintenance shutdown in October 1997. • As the Workshop Manager I controlled the everyday activity within the four sections of the workshop, fabrication, machining, rotating equipment overhauls and relief valve overhauls.
-
-
Mechanical Engineer (Rotating/Static Equipment) and Workshop Manager Jan 1997 - Apr 1998
-
Jun 1995 - Jan 1997
-
-
Rotating Equipment Shutdown Engineer
-
Nov 1993 - Jun 1995
Rotating Equipment Shutdown Engineer/Rotating Equipment Engineer for Shell’s 1995 Major Shutdown
-
-
Mechanical Technician
-
Sep 1986 - Nov 1993
-
-
Apprentice Fitter/Turner
-
Sep 1982 - Sep 1986
-
-
Education
-
London South Bank University
B.Eng, Mechanical Engineering
Community
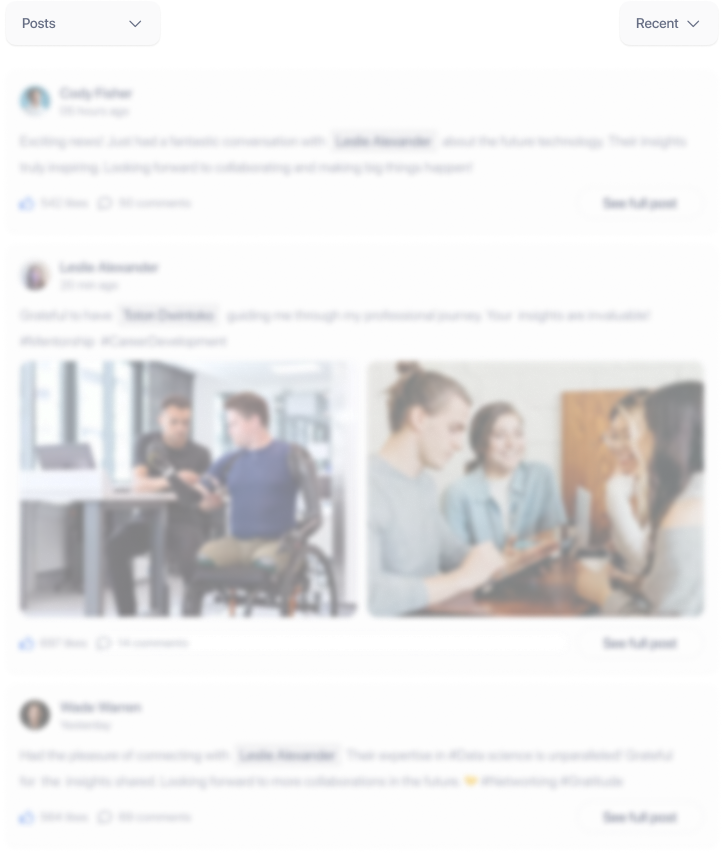